Understanding of the performance of a specific component in a given application or the response of the material to a specific forming process can greatly benefit the design of the component or the manufacturing process respectively. Robust predictive modeling can help understand and predict the performance, but these models that capture the fundamental physics and that can represent a real world application are computationally expensive.
Multi-scale modeling across different length scales allows for passing of relevant data from one scale to the next, permitting more flexibility and better predictability of component performance at the desired length scale. At CMRG, we are developing approaches that can utilize knowledge generated at one length scale, using the relevant physics and that scale, and can be passed to models working at another length scale. The ultimate goal is to develop models that also incorporate a feedback to the other length scale.
Our research areas for multiscale modeling
- Advanced phenomenological plasticity models coupled with crystal plasticity models
- Phenomenological finite element models coupled with crystal plasticity models
- Crystal plasticity models coupled with machine learning techniques
Select publications
- Kohar, C.P., Bassani, J.L., Brahme, A., Muhammad, W., Mishra, R.K. and Inal, K., 2017. A new multi-scale framework to incorporate microstructure evolution in phenomenological plasticity: Theory, explicit finite element formulation, implementation and validation. International Journal of Plasticity.
- Muhammad, W., Ali, U., Brahme, A., Kang, J., Mishra, R.K., and Inal K., 2017. Experimental Analyses and Numerical Modeling of Texture Evolution and the Development of Surface Roughness during Bending of an Extruded Aluminum alloy using a Multiscale Modeling Framework. International Journal of Plasticity
- Ali, U., Odoh, D., Muhammad, W., Brahme, A., Mishra, R.K., Wells, M. and Inal, K., 2017. Experimental Investigation and Through Process Crystal Plasticity–Static Recrystallization, Modelling of Temperature and Strain Rate Effects During Hot Compression of AA6063. Materials Science and Engineering: A.
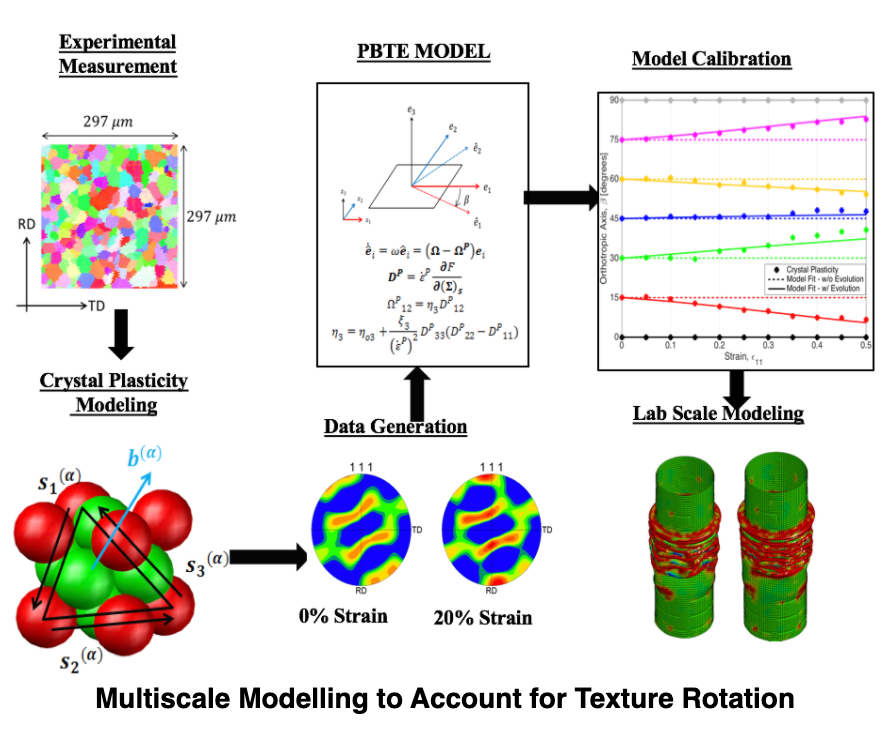
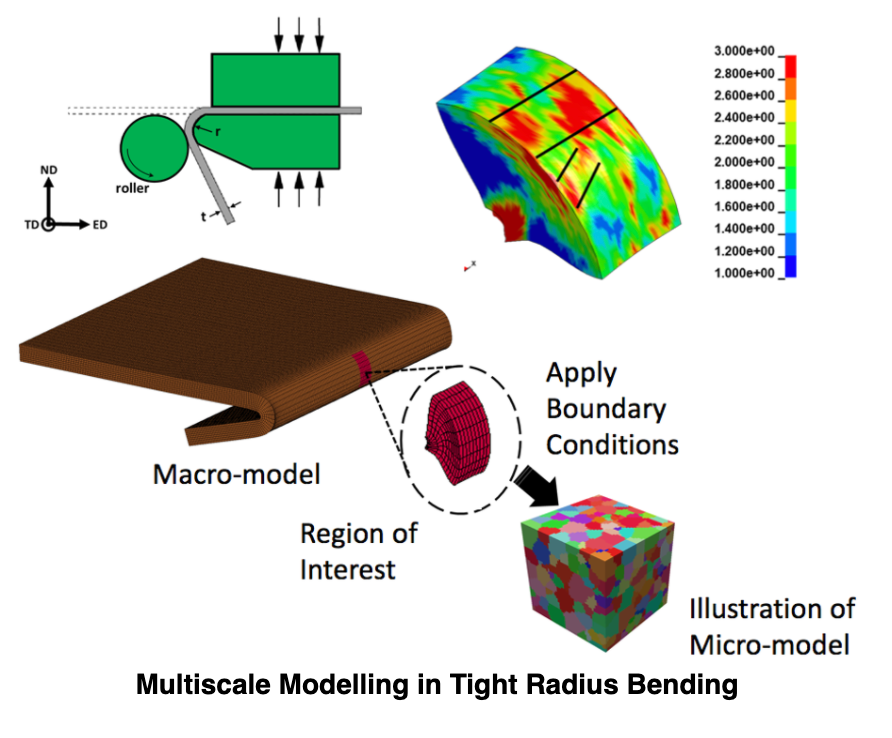