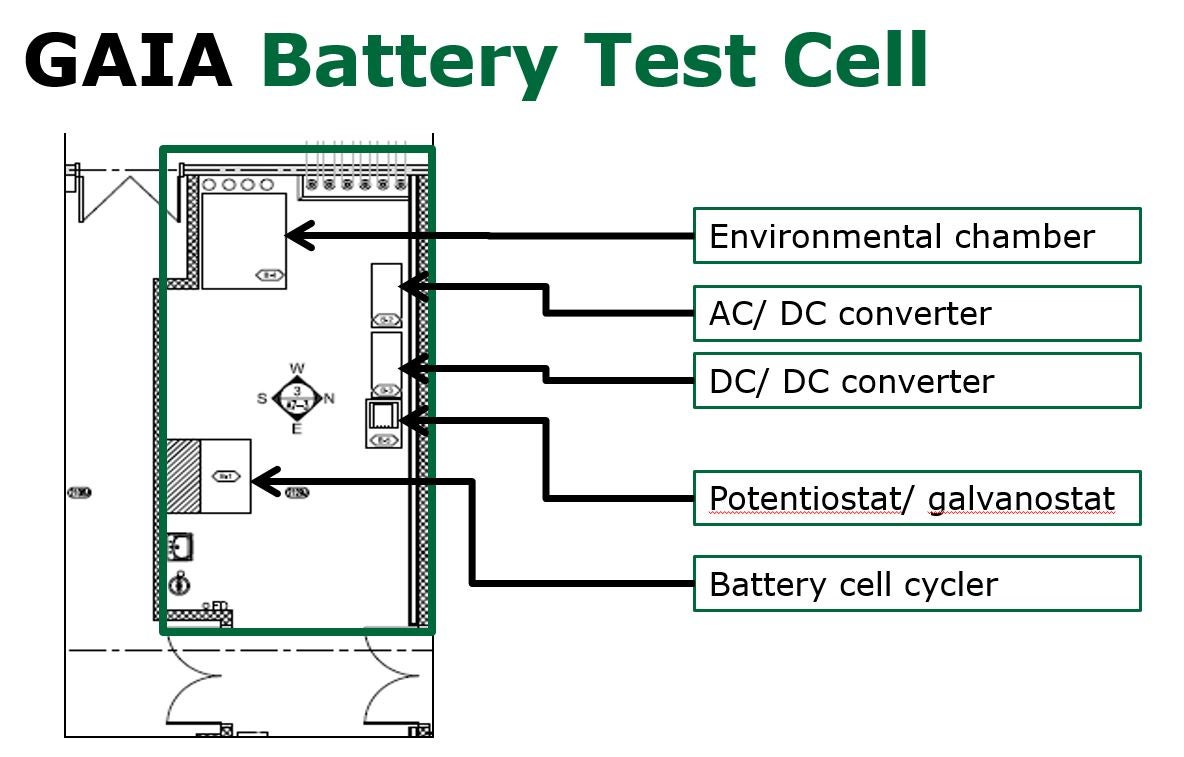
With concerns about the impact gas fueled vehicles have on the environment, the automotive industry is looking to increase production of electric and hybrid vehicles. With this increase, there is an exploding demand for reliable batteries to power these vehicles.
Battery testing is an important aspect within the Green and Intelligent Automotive (GAIA) facility, to assure quality and sustained problem-free operation. The quality of battery components are of critical concern, especially as requirements for battery standards in vehicles are strict. Sooner or later, the loss of capacity in batteries will become an issue, thus manufactures have a desire to reduce this in their vehicles.
As the automotive industry has a standard that calls for batteries to maintain a storage capacity of 80% or more after 10,000 charging cycles, suppliers must ensure leak tightness down to the smallest battery component. Electrolytes must not leak from the battery cell and moisture should not be able to enter. This means that each cell must be gas-tight, because if it is not, that will cause power reduction over the long term and improperly enclosed battery cells could lead to being destroyed by the penetration of atmospheric humidity, with catastrophic results.
GAIA uses various testing mechanisms to ensure the safety and longevity of the battery cycle. Testing helps to determine how big the battery pack is needed to be to store for the advertised amount of energy throughout the life of the vehicle. Accurately measuring the efficiency of batteries storage and delivery of an electrical charge helps to determine the cycle life of a battery.
To learn more about the various testing mechanisms, click on one of GAIA’s testing links to the right of the page.