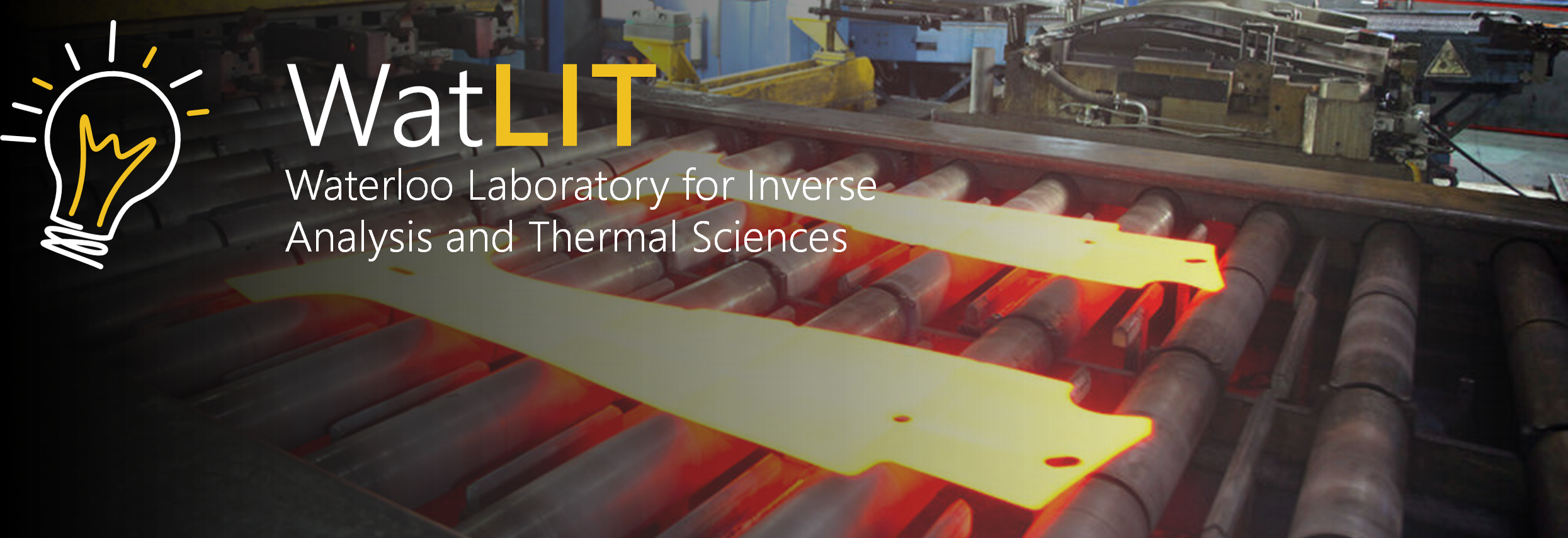
Why is this important?
In hot forming die quenching (HFDQ) or hot stamping, ultra-high strength steel sheets called “blanks” are first austenitized in a long, roller-hearth furnace and then transferred to a cooled die, where they are simultaneously formed and quenched into fully-martensitic parts. Both the number and variety of hot-stamped parts have grown dramatically since its inception in 1987, reaching 360 million parts per year in 2016.
Most hot stamping is done on Al-Si coated steel, which prevent the blanks from oxidizing and decarborizing within the furnace. The Al-Si coating melts in the furnace and reacts with iron from the substrate steel to form a permanent Al-Si-Fe intermetallic layer that provides some long-term corrosion protection.
In order to remain internationally-competitive, automotive parts manufacturers must maximize production rates (minimize cycle time, which is time between two successive parts) while ensuring that the part is fully austenitized as it leaves the furnace.
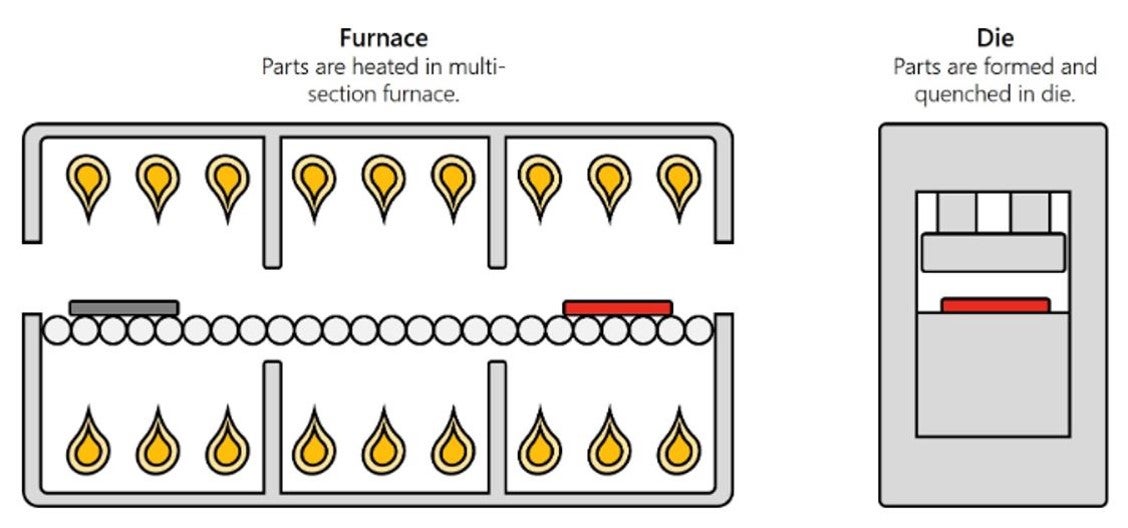
WatLIT research into hot stamping focuses on understanding the coating transformation, modeling roller hearth furnaces, direct contact heating, and characterizing the heat transfer coefficient.
In-situ spectroscopy and coating evolution
The Al-Si coating melts at 577°C, yielding a brief liquid layer before it reacts with iron from the base steel to form a solid, intermetallic Al-Fe-Si layer. The molten Al-Si can seep into the furnace rollers, leading to their premature degradation and failure. The radiative properties of the blank change dramatically with coating transformation, which affects how quickly the steel is heated within the furnace.
The WatLIT team is using in-situ and ex-situ optical diagnostics to understand coating transformation, and how it changes with process parameters (e.g. heating rate.) For example, laser reflectance measurements can pinpoint exactly when the coating melts and when it re-solidifies, while analysis of the corresponding speckle pattern in the reflected laser light shows the evolving surface roughness. Current research is focused on FTIR and in-situ Raman microscopy images, which indicate oxide layer growth and the formation and dissolution of intermetallic phases.
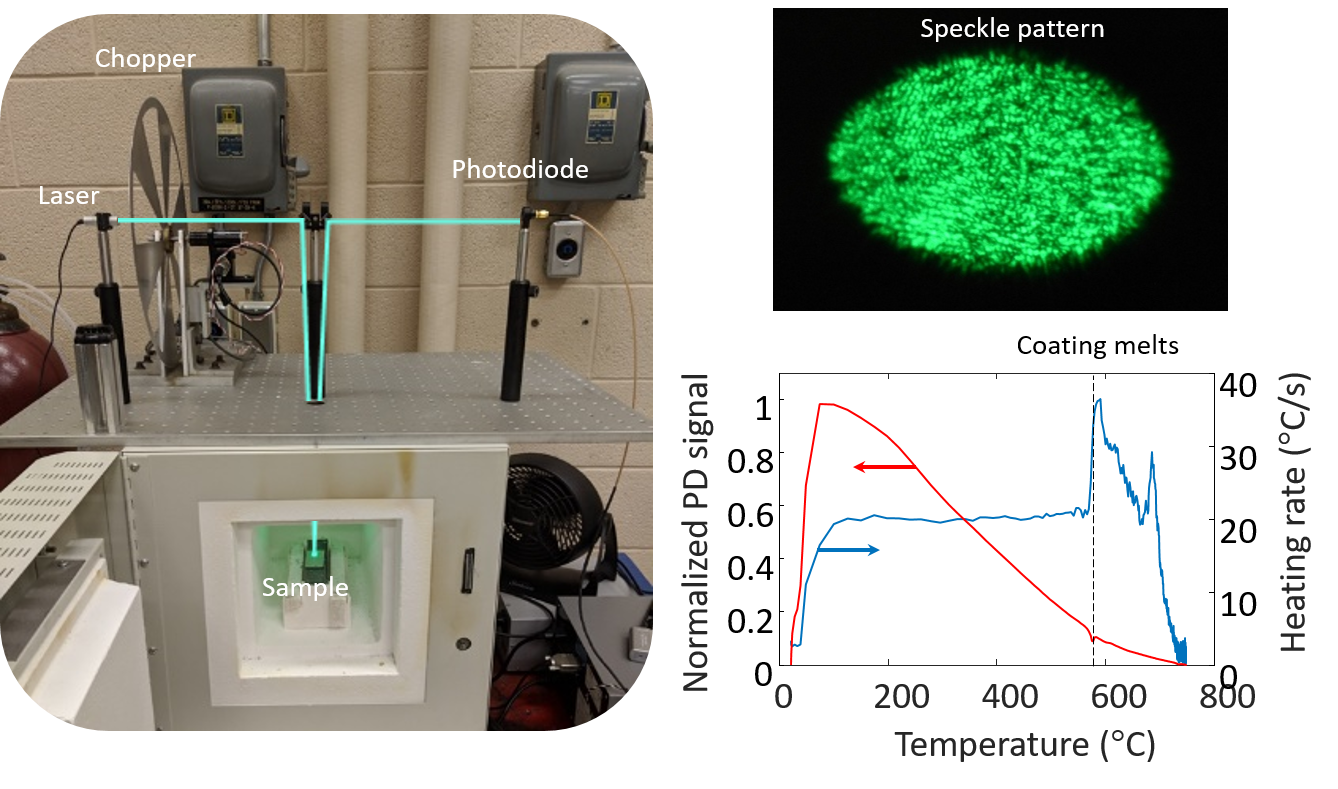
Roller hearth furnace modeling
Manufacturers must adjust the roller hearth furnace parameters (zone temperatures, roller speeds, and batch spacing) to minimize cycle time while ensuring that the blanks are completely austenitized prior to quenching/forming. To this end, the WatLIT team has developed a thermo-metallurgical model of blank heating. The model consists of two coupled sub-models: a heat transfer model that predicts how the blank temperature changes as it traverses through furnace zones, and a metallurgical sub-model that calculates the transformation of the blank microstructure from as-received ferrite/pearlite into austenite.
This model has been coupled to a genetic algorithm to determine the furnace parameters that minimize cycle time. Current work is focused on improving the accuracy of the metallurgical sub-model and modeling the coating transformation.
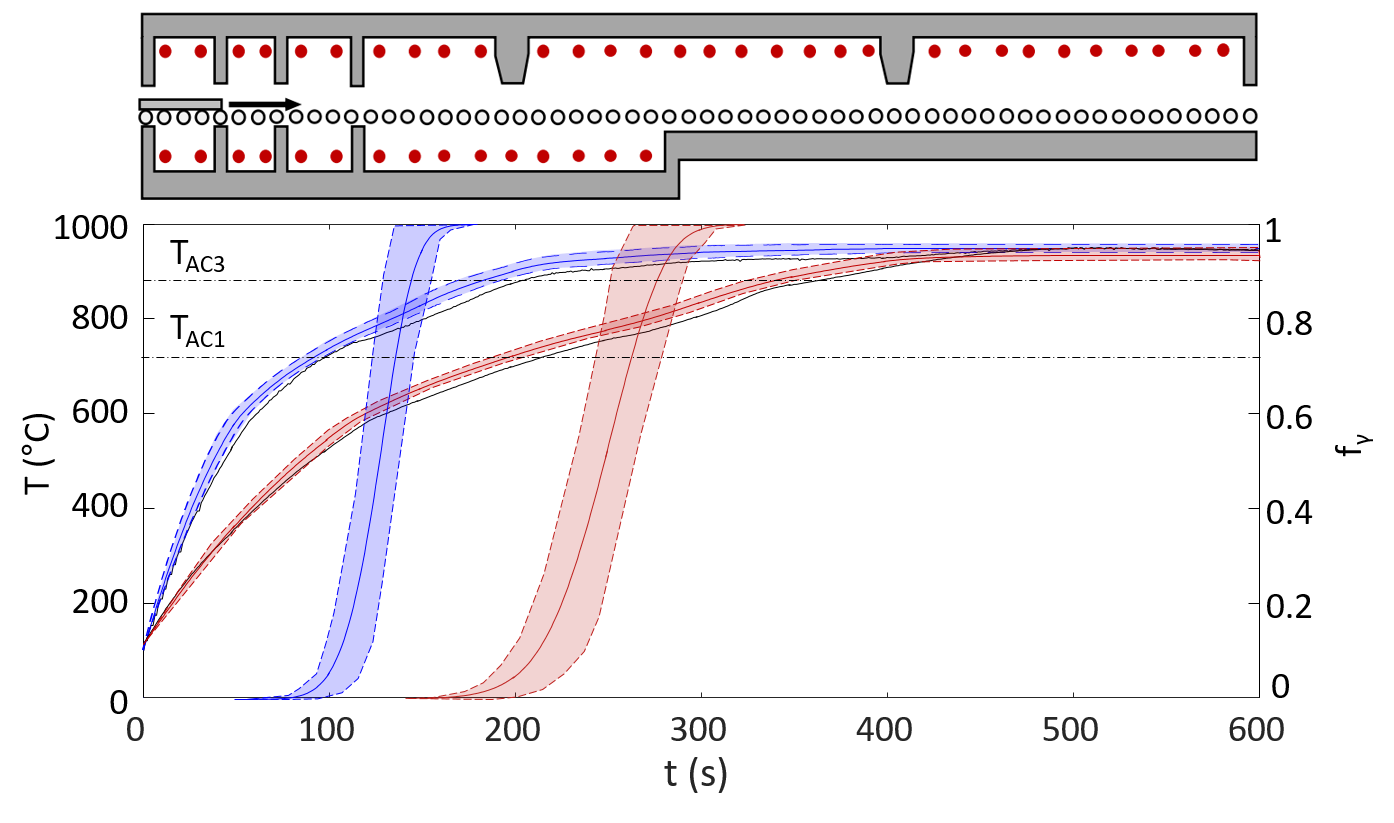
Direct contact heating
Austenitizing a blank within a furnace takes 5-8 minutes, so furnaces must be very long (typ. ~30-40 m) to maintain a reasonable cycle time. Because of their large size, roller hearth furnaces are also very energy-intensive and costly to operate. These drawbacks motivate development of non-furnace based austenitization schemes.
In direct contact heating, blanks are heated within two heated platens mounted in a hydraulic press. The platens are made of a high-temperature nickel steel alloy, and may be heated by magnetic induction or using embedded silicon carbide heaters. This process requires only 30 s to austenitize a blank, and heating and forming dies can be mounted within a single hydraulic press, which simplifies blank transfer.
Direct contact heating can also be used to produce parts having tailored microstructures for improved crash performance. In this approach, the metal platen contains ceramic inserts that align with the soft region of the blank. Even though the platen is isothermal, less heat is transferred from the ceramic regions because of the lower thermal effusivity of the ceramic. (This is the same reason why the buckle of a seat belt feels hotter than the strap on a summer’s day even though they reach the same temperatures.) Portions of the blank that abut the ceramic inserts are not completely austenitized, and transform into a mixture of ferrite and martensite when quenched, which is more ductile than a fully-martensitic microstructure.
Characterizing the heat transfer coefficient during forming
Transforming the austenitized blank into a martensitic part during forming-quenching is predicted on maintaining a cooling rate of at least 30 K/s. The cooling rate, q”, depends on the blank temperature, the die temperature, and the heat transfer coefficient (HTC) between the blank and the die,
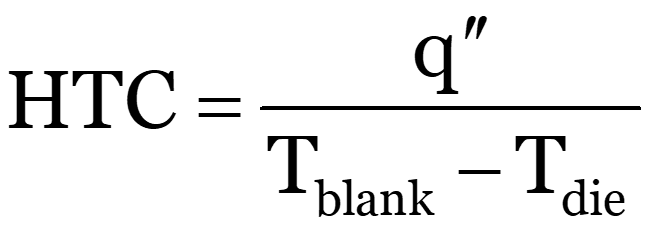
The HTC depends on the contact area between the blank and the die due to micro-asperities which flatten with increasing pressure. If the HTC is too small, the cooling rate may not be sufficient to form martensite, resulting in undesirable “soft” spots on the formed part. This is a particular problem for complex part geometries, where the interface pressure is non-uniform. The intermetallic coating also impacts the HTC, in a way that is not fully understood. Automotive parts manufacturers must understand the relationship between interface pressure and the HTC in order to design dies and understand the limitations to part geometries posed by the HTC, and how coating weight affects the HTC.
WatLIT research is focused on characterizing the HTC during hot stamping using flat dies instrumented with sub-surface thermocouples. Blank temperature is measured using thermocouples and a pyrometer mounted within the die. The instantaneous die surface temperature and heat flux are found through inverse heat conduction analysis.
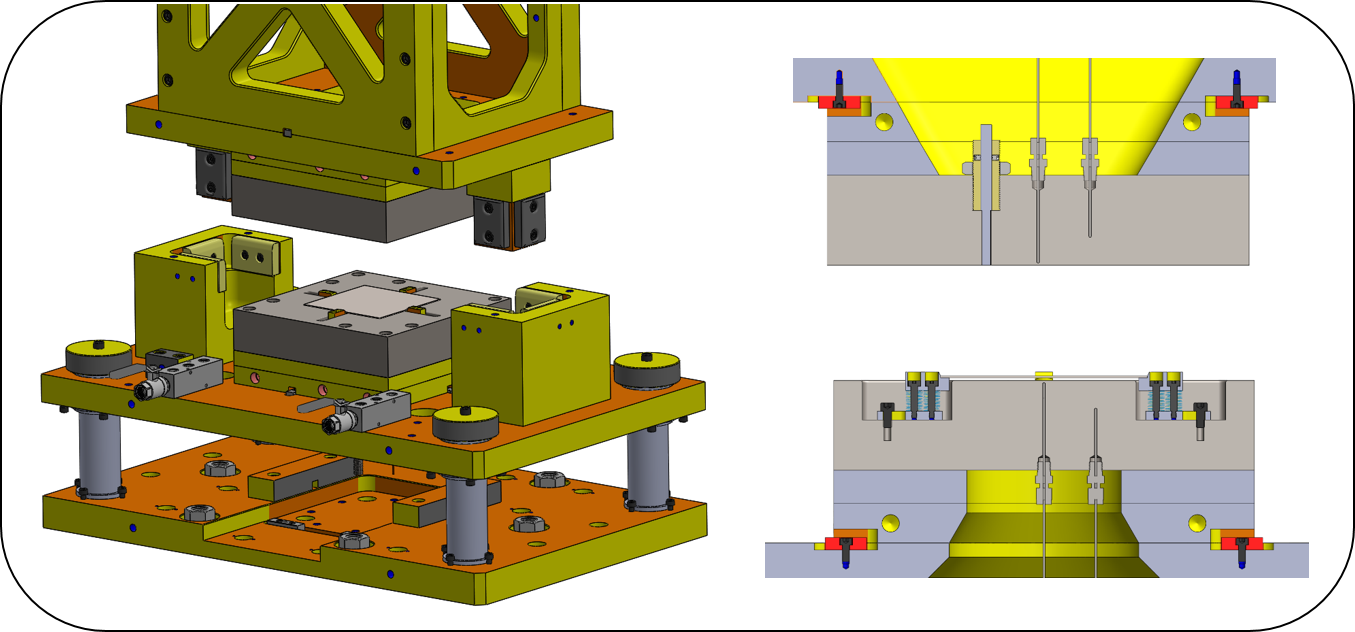
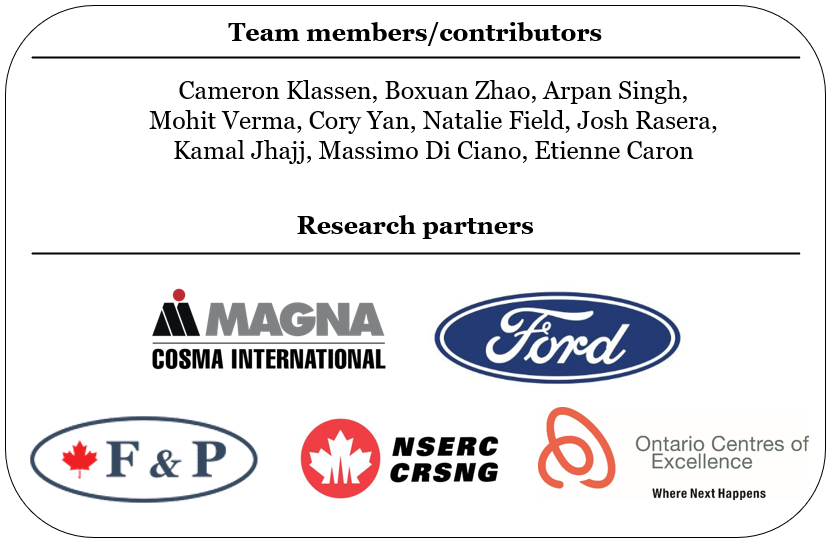