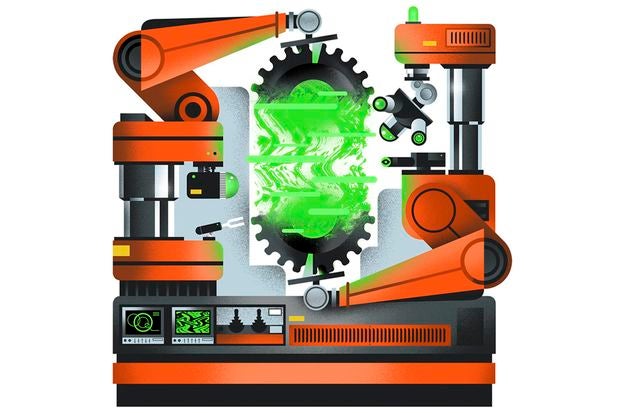
Your car has yet to reach its first birthday when the transmission seizes up unexpectedly. A mechanic informs you the culprit is a hairline crack on a gear deep inside the engine block. You haven’t been in any collisions, so how did a faulty part end up in your new vehicle?
To avoid irate customers and costly repairs of cars under warranty, auto makers like Nissan and parts manufacturers such as Germany’s ZF Group are turning to Acerta Analytics Solutions, a Kitchener, Ont., start-up that employs data analytics to identify components at risk of failure. Using sensors, the company’s system scans a transmission component, for example, for patterns of vibration or material irregularities and compares them to previous defect reports. A match indicates a part is potentially faulty, so it’s yanked off the line before it can be installed, explains founder Greta Cutulenco. And this all happens remotely: Acerta clients simply subscribe to the system, which analyzes a continual flow of data transmitted from factory floors.
The 20-employee company is but a tiny cog in a vast machine of connected technologies collectively dubbed Industry 4.0. Following transformations ushered in by just-in-time delivery, automation and supply chain integration, this next revolution in manufacturing will be driven by data analytics, artificial intelligence and wireless connectivity. The aim is to harness all the retrievable but mostly ignored data that factories generate – such as patterns in equipment breakdowns or past supplier records to project delivery lead times – and use it to improve productivity both in the plant and throughout the supply network. Researchers put global spending on these technologies at more than $200 billion (U.S.) in the next five years, with automotive, aerospace, and food- and beverage-processing companies expected to spearhead its adoption in Canada.