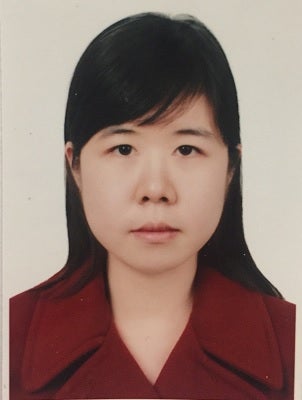
CLC decomposes fuel combustion reaction into several sub-reactions. Firstly, particles consisting of metal and support materials react with air in the oxidation reactor, converting metal into corresponding metal oxide. Oxidized particles are then transported into a reduction reactor where metal oxides react with fuel gas such as syngas and natural gas, releasing energy while generating a sequestration-ready CO2 stream. Particles containing reduced metal are recycled to the oxidation reactor to start the next cycle. In this process, the metal/metal oxide dual carries the oxygen from the air to the reduction reactor so direct contact between air and fuel is avoided.
The practicability and productivity of CLC strongly depends on the effective performance of oxygen carrier particles. The desired oxygen carrier particles should keep high reaction and conversion rates during long-term operation with hundreds of cycles. Therefore, it is critical to understand the causes of oxygen carrier deactivation. One speculation is that the particle structure changes due to sinter and/or attrition thus reducing the porosity. This may lead to a significant decrease of reaction surface. The goal in my research is to develop particle models that can explicitly account for interactions that occur in the particle and that are not explicitly considered in the current models, e.g. the effect of porosity. Through my work, new insight into the design and selection of desired oxygen carrier particles will be provided.
Thesis: A Multi-Scale Model for Nickel-Based Oxygen Carrier in Chemical-Looping Combustion