Vertical axis wind turbines, or VAWTs, differ from traditional horizontal axis wind turbines (HAWTs) in the orientation of the rotor and blades. While this technology is long-established and offers flexibility for small-scale installations, it has received less attention in research due to its inherently lower efficiency compared to HAWTs. At the Computational Fluid Dynamics and Turbulence Modeling Laboratory, one of the major focuses is on intelligent VAWT design and fabrication in order to increase the feasibility and value of this technology. Recently, a novel blade pitch control system has been developed here for a straight-bladed (H-type) VAWT. 2D CFD studies have been done using ANSYS Fluent to investigate the aerodynamic and power behaviors of VAWTs at different blade pitch angles. These insights are incorporated in a system using PID (conventional controller) in combination with a Multi-Layer Perceptron Artificial Neutral Networks (MLP-ANN) approach to develop a model for actively controlling blade pitch angle according to wind conditions.
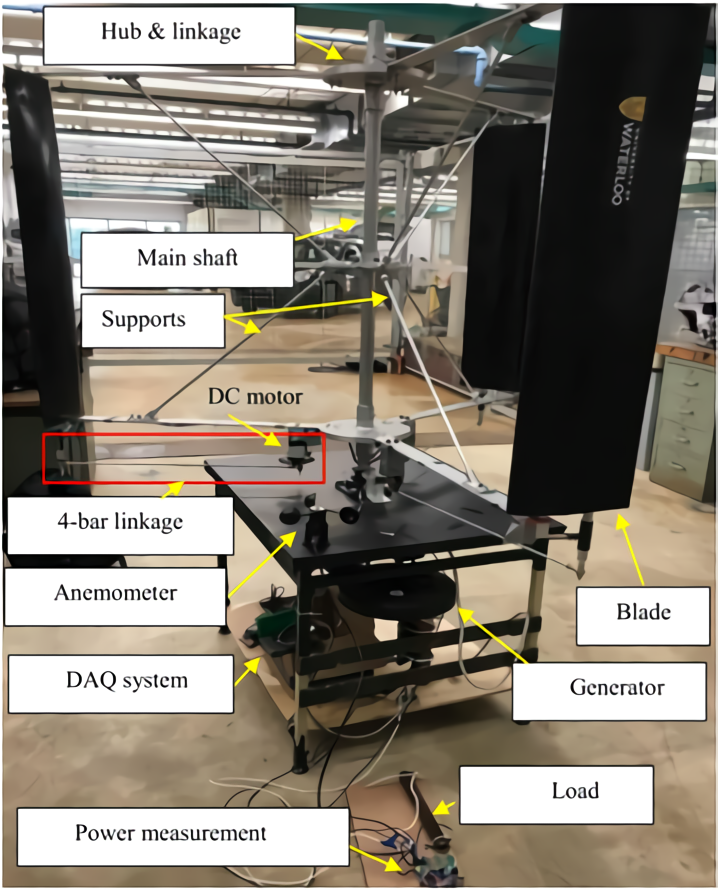
To validate this control system, an experimental prototype of a smart VAWT has been constructed. Each blade is shaped to the NACA 0018 airfoil profile and can be pitched individually using a four-bar linkage mechanism, actuated by a DC motor. During operation, the anemometer sensor passes wind speed data into the PID + MLP-ANN controller, which then outputs the motor actuation signals to adjust the blade pitch so the turbine can more effectively harvest energy from the flow. It has been experimentally determined that this intelligent control design increases the turbine’s power output by around 22% compared to a VAWT with invariant blade pitch.
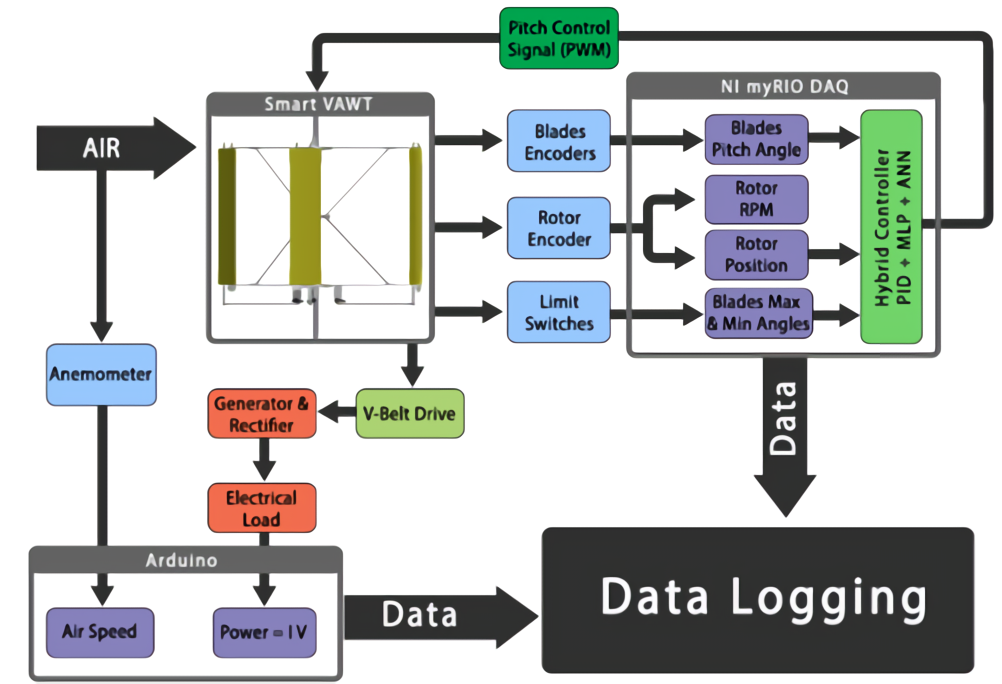
Another main objective of intelligent VAWT design is the study of turbine array configuration and its implications on power output. With HAWT farms, it is well-known that each turbine produces a massive downstream wake (a region characterized by velocity deficit). Since the available wind resource to extract from is lowered in turbine wakes, it is highly desirable to place turbines sufficiently apart so as to not detriment the power output of surrounding turbines. However, recent research has shown that VAWT turbines can exhibit higher power output when placed in close proximity with each other, for some array/cluster arrangements. It is hypothesized that this power “synergy” effect is due to VAWT blades accelerating the local flow just outside the wake regions and then taking advantage of the sped-up flow fields to generate more power.
Therefore, the laboratory aims to develop a fast-simulation system for predicting power synergy in VAWT arrays. While these synergy effects could be captured using conventional blade-resolved, unsteady RANS CFD, computations using this approach are highly expensive and time-consuming. Therefore, a more tenable and scalable method is required for simulating large quantities of VAWTs. Ongoing research is focused on using the Actuator-Line Model (ALM) to simplify and significantly speed up CFD. ALM uses the blade element momentum theory in conjunction with airfoil performance lookup tables to model the effect of blades on the flow without meshing their physical presence. It is of importance to study whether power synergy effects can be adequately captured using this ALM technique. In the future, this work will be extended to develop a framework for optimizing VAWT placement for an arbitrary array.