As a classic fluid-structure interaction (FSI) phenomenon, vortex-induced vibration (VIV) refers to the motion on the structure induced by the periodic irregularities on the interacting external flow. In certain conditions, a fluid flow past a bluff body (e.g. a circular cylinder) could lead to alternate shedding of swirling vortices in the downstream, i.e. Karman vortex street. Consequently, this repeating pattern of wake vortices generates periodic fluid forces on the body, which could cause the elastically supported body to continuously vibrate as long as vortices are shed at a frequency close to the system natural frequency (“lock-in”). VIV is also a multi- and inter-discipline research problem, incorporating fluid mechanics, structural mechanics, vibration, experimental and computational fluid dynamics, acoustics, etc.
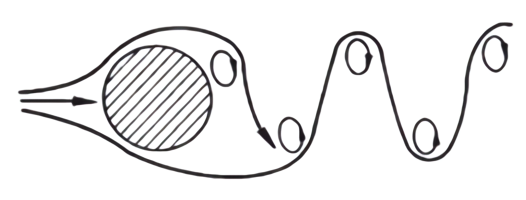
VIV is responsible for fatigue damage and structural failure in most engineering scenarios, like bridges, power transmission lines, ocean structures, oil drilling platforms, marine risers, and other applications. Therefore, different methods are taken to prevent or reduce vibration, including strakes, shroud, axial slats, fairings, splitter plate and ribboned cable. The suppression principle of these devices is to prevent the formation of vortex street by disturbing the correlation between vortex shedding and vibration.
Apart from the negative effects, VIV also contains enormous energy that hasn't been fully exploited and well used by now. The most recent interest in VIV ensues from the low-speed fluid energy extraction based on the FSI mechanism. The elastic structure undergoing VIV captures the energy of fluid flow (wind and/or water) as the energy of vibration, which can then be transduced into more convenient form of energy, such as the electricity through a piezoelectric transducer or other transmission structures connected to the generator. The cross-sectional shape of bluff body has a decisive influence on the energy generation performance by inducing different vortex vibration phenomena. For example, the circular cylinder extracts fluid energy by VIV, while the rectangular cylinder, D-section and cylinder-appendage system (e.g. cylinder with splitter plate) by a combination of multiple vibration responses, such as VIV, galloping and flutter. In addition, the common hydrodynamic quantities that influence vortex vibration, including mass, structural damping and Reynolds number, also have negligible effect on the energy harvesting efficiency.
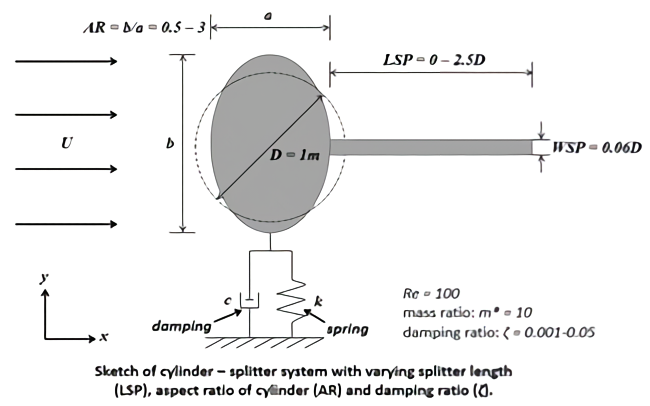
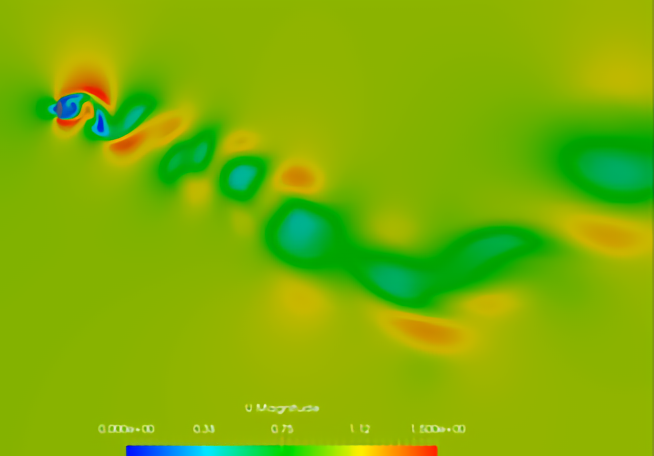
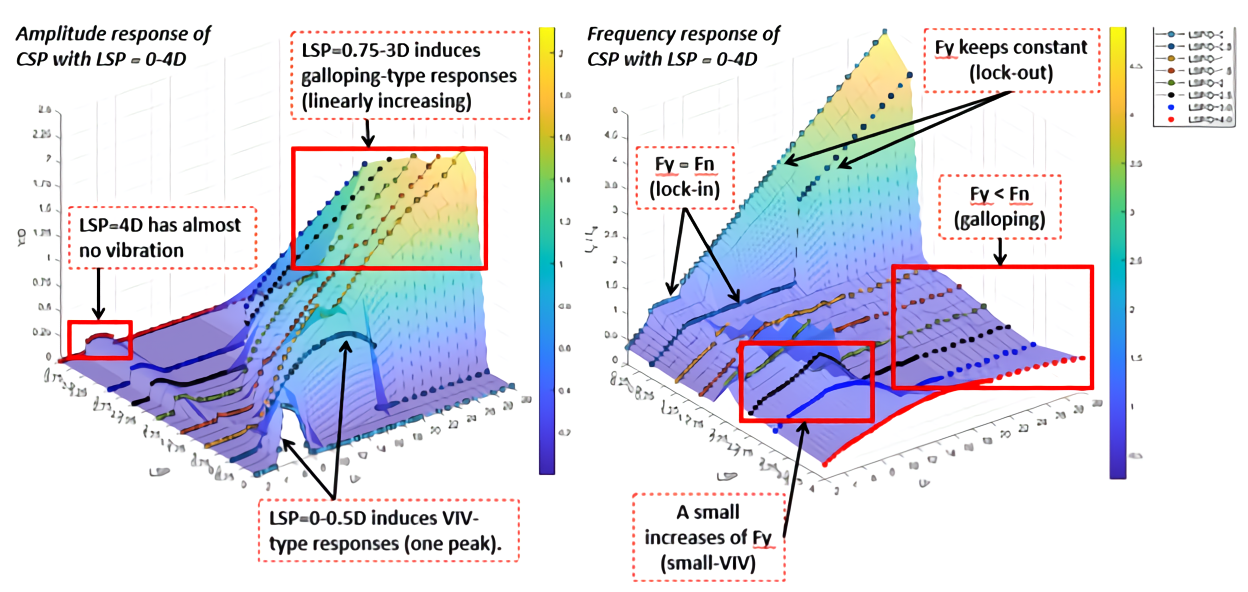
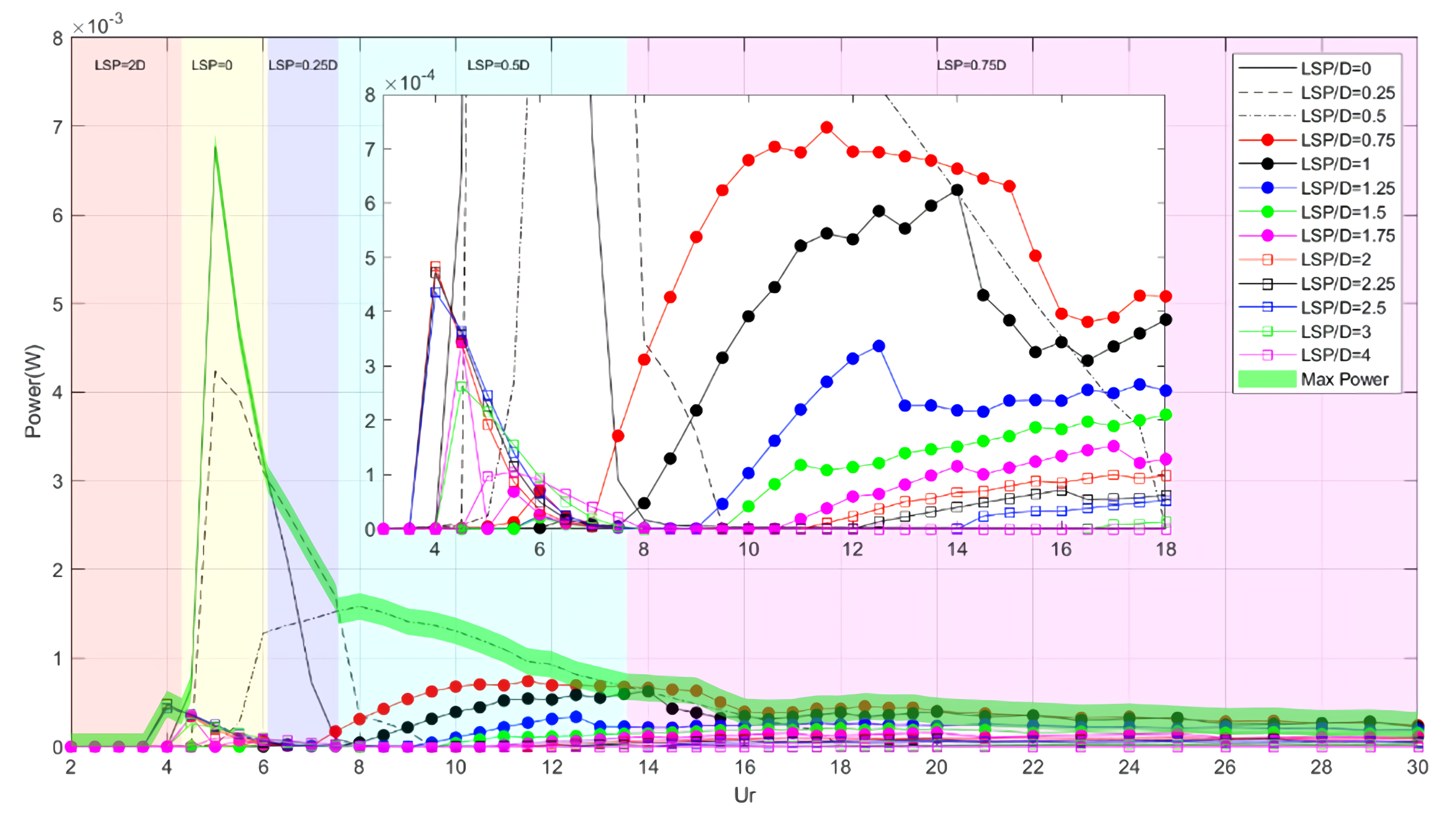
A deep understanding of VIV mechanism is essential in any engineering applications, whether suppression or utilization. Therefore, a variety of research methods has been developed over the past a few decades. Experiment is obviously the most important mean to obtain the real rules of VIV. Computational fluid dynamics (CFD), especially fully-order model (FOM), has become another powerful tool benefited from the rapid development of computer technology in recent years. Some mathematical models based on the physical meaning or empirical parameters are also proposed to analyze VIV at a more theoretical level.
Linear stability analysis (LSA) is one method of studying flow-induced vibration (FIV), which is based on the reduced-order model (ROM) of fluid dynamics. On the one hand, it could help researchers figure out the underlying mechanism behind the phenomenon. On the other hand, compared to traditional CFD calculation methods with FOM, it has significantly higher efficiency in identifying unstable intervals for structural oscillation. Furthermore, the ROM can be combined with potential control modes, which has great advantages in engineering applications. The combination could suppress structural vibration to reduce structural damage such as fatigue in civil and marine engineering, and it could also expand the instability range of the device in the field of energy utilization to improve energy harnessing efficiency.
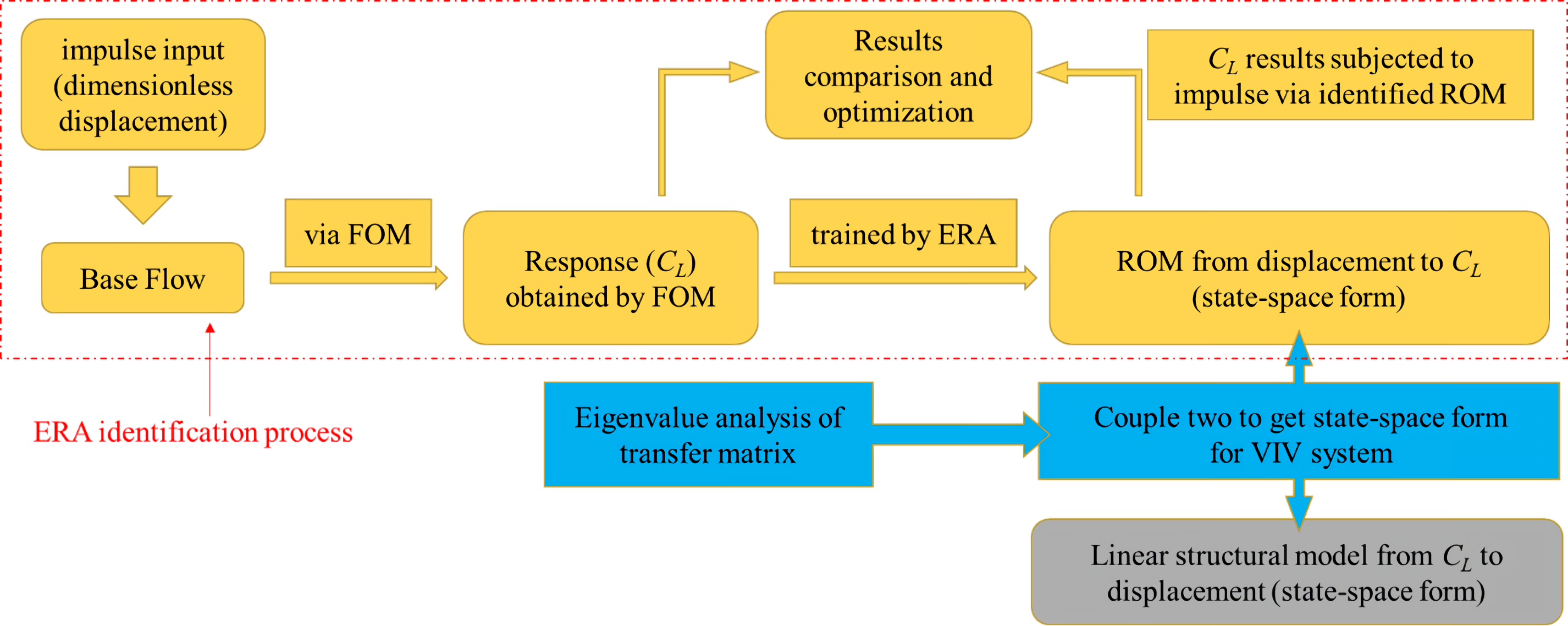
- Process diagram for Reduced order model of VIV based on ERA
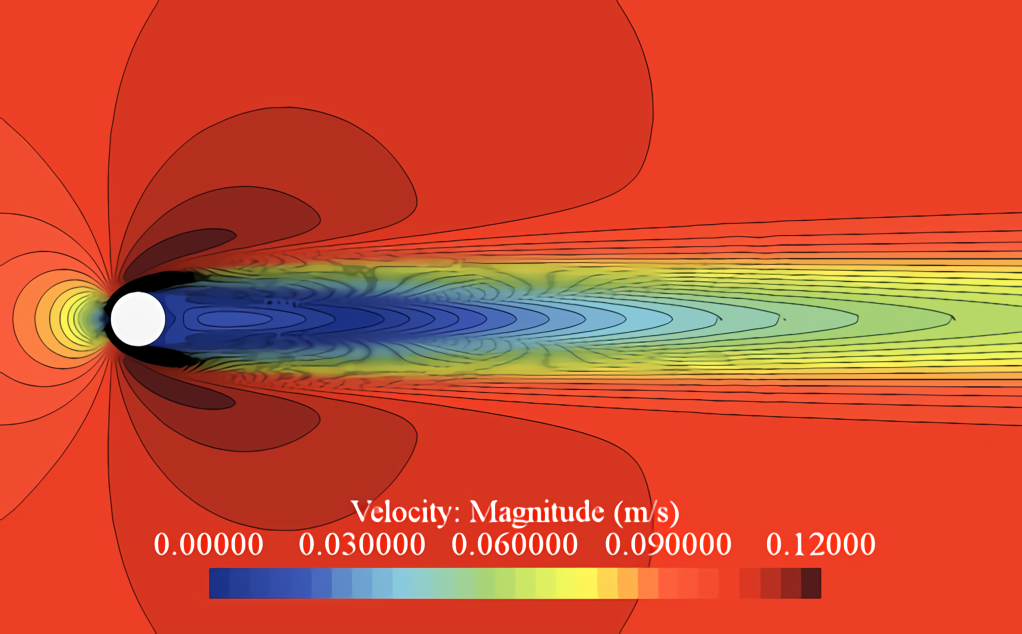
- Base flow at Re = 60, flow from left to right. (Non vortex street and periodic dynamic coefficient)
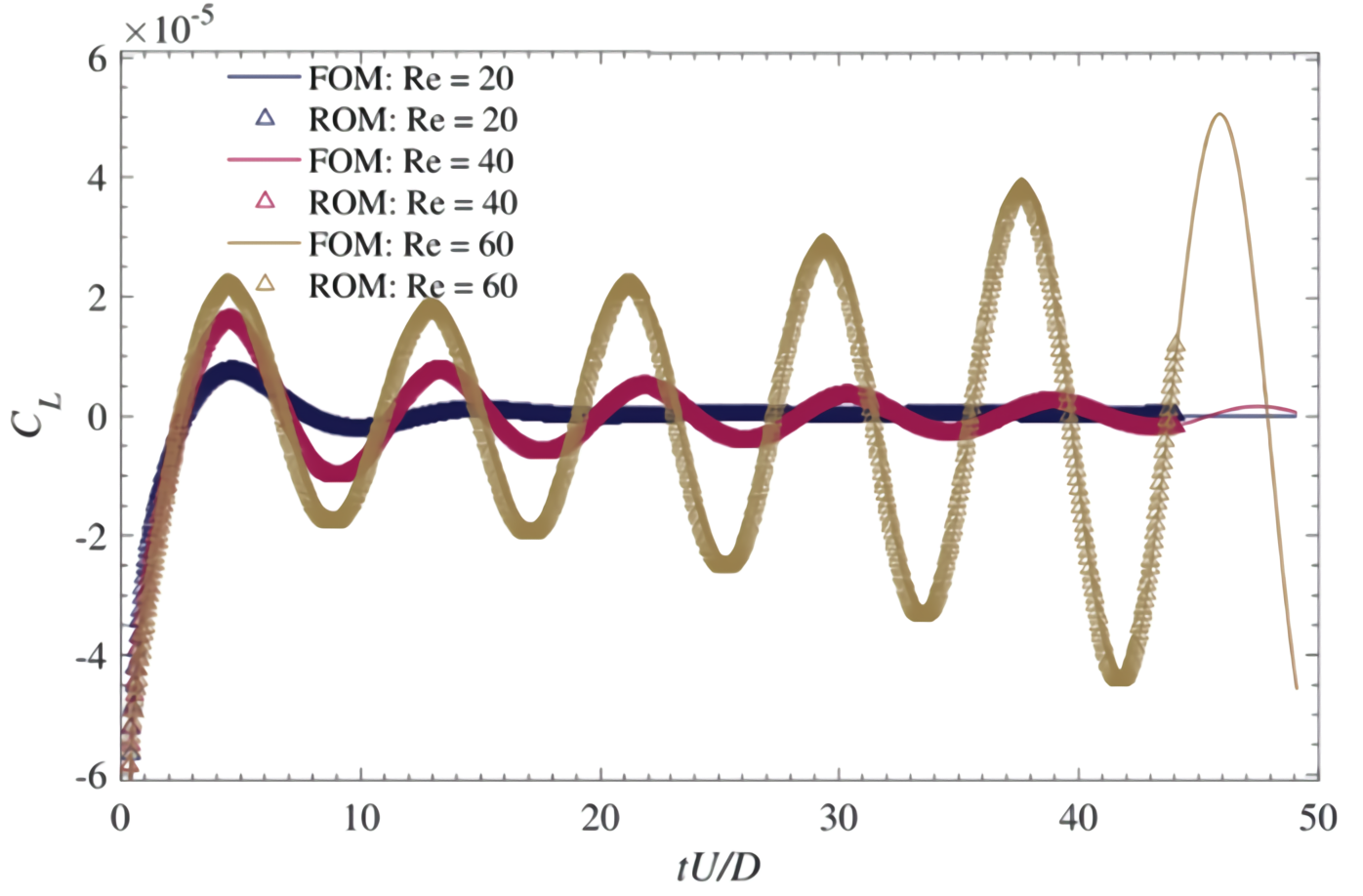
- Designed impulse input: 10−3 D.
- CL response history of the FOM, and corresponding identified CL of ROM.
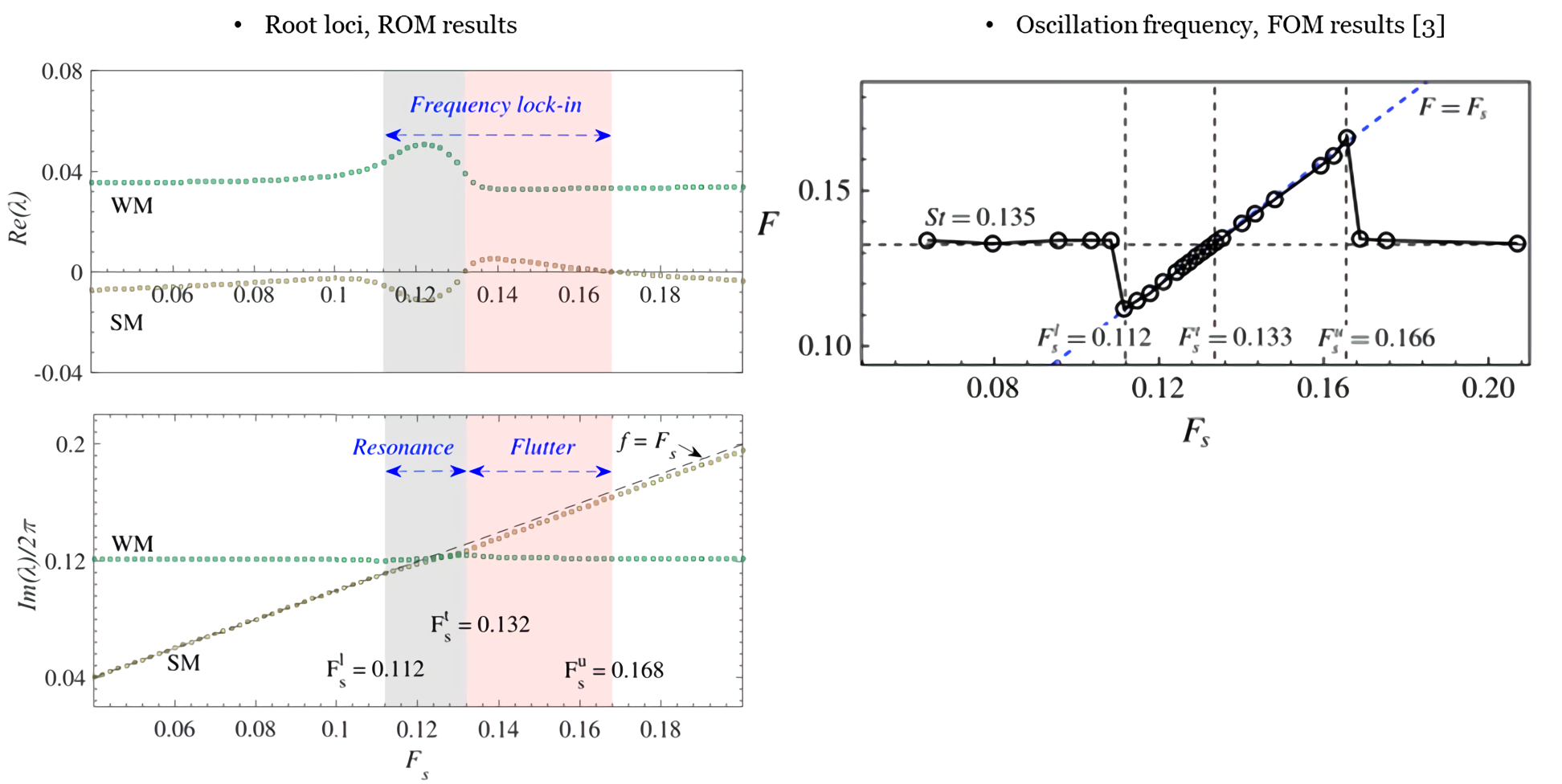
- The eigenvalue branches distribution and oscillation frequency varying with reduced natural frequency Fs with (Re, m*) = (60, 50).