Introduction
The motivation toward vehicle weight reduction within the automotive sector has created a need for the replacement of mild steels with thinner gauge high strength steels and aluminum alloys. The vehicle components which can most benefit from these material substitutions are structural members that act as critical energy absorption components in the event of a vehicle crash. Crash structures are designed to absorb the crash impact energy while keeping the passenger compartment intact and the deceleration loads on the occupants minimal. The main challenge is to ensure that the crashworthiness of automobiles is not degraded as a result of structural weight reduction. This is the motivation behind the impact work at the University of Waterloo. Extensive research into the manufacturing processes and materials involved in fabricating light weight crash structures is the main focus of this work.
The two main types of crash structures that are studied at the University of Waterloo are the so-called s-rail and axial crush members shown below. Research is also conducted on ultra-high strength anti-intrusion components, such as B-pillars (Hot Stamping).
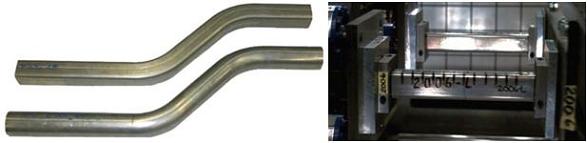
Pre-bent and hydroformed s-rails and axial crush members prior to an impact test
The key result of crash tests is the force and absorbed energy vs. time, which determines the structures crashworthiness and is a measure of its ability to reduce occupant injury. Impact tests are conducted at sponsors’ test facilities using a deceleration sled apparatus. S-rails and axial members have been manufactured from the following alloys:
- Dual Phase Steel (DP600, DP800)
- High Strength Low Alloy Steel (HSLA350)
- Drawn Quality Steel (DDQ)
- Aluminium (AA5754, EN-AW5018)
At the University of Waterloo, the research program focuses on the effect of the manufacturing process on the subsequent energy absorption potential of the s-rails and axial members. In addition to the manufacturing process, the effect of geometry and material properties are also studied. Extensive work has been done on the effect of the following parameters on the crashworthiness of the s-rails and axial members:
- Effect of alloy substitution
- Effect of circular (tubes) and square (hydroformed) cross-sections (s-rails/axial members)
- Effect of the high-pressure and low-pressure hydroforming process (axial members)
- Effect of corner radius of high-pressure and low-pressure hydroformed tubes (axial members)
- Effect of hydroforming end-feed in high-pressure hydroforming (axial members)
- Effect of pre-bending parameters such as bend severity and bending boost (s-rails)
- Effect of material properties (s-rails/axial members)
- Effect of material thickness (s-rails/axial members)
- Effect of tailor welded tubes (both hydroformed and non-hydroformed) of various materials and thickness
- Effect of crush initiators (s-rails/axial members)
In addition to the experimental program, complex finite element (FE) models have been developed at the University of Waterloo and validated against the experiments. These validated models are then used in the design process (by the car maker) to virtually manufacture and subsequently crash full scale FE vehicle models.
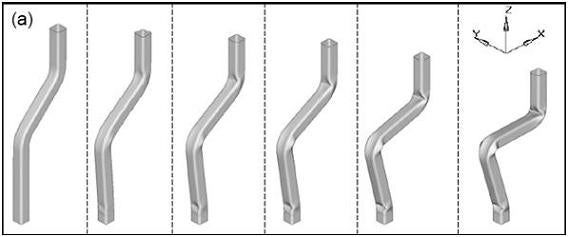
FE model of an s-rail undergoing an impact
S-Rails
The tube bending and hydroforming manufacturing processes are used to create the s-rail structures studied at the University of Waterloo. A more in-depth review of these processes can be found in the Tube Bending and Hydroforming research area. The first process required in the manufacture of an s-rail is the pre-bending operation. In this work, straight tubes are pre-bent by the mandrel rotary-draw tube bender at the University of Waterloo. The main variables that are varied during pre-bending are bend severity (R/D ratio) and bending boost. These variables affect the final crash response of the s-rail.
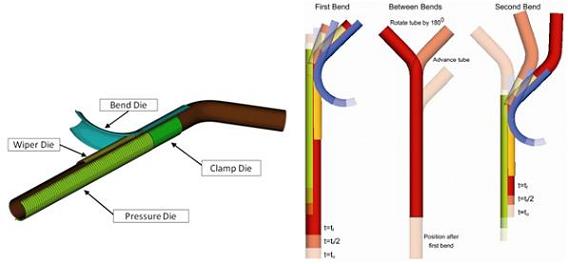
The tube bending FE mesh and the progression of the s-rail pre-bending FE model
As a part of this work, pre-bent s-rails (circular cross-section) are crash tested to assess their energy absorption potential. The energy absorbed by these s-rails is used as a baseline for comparison to the hydroformed s-rails that have a square cross-section. The low pressure hydroforming process is used to form the pre-bent s-rails into s-rails with square cross-sections. Shown below is the low pressure hydroforming die used to manufacture the s-rails. Die inserts are used to hydroform tubes that have been pre-bent with different bend severities (R/D ratios).

S-rail die photos: (a) isometric view of upper and lower dies (b) front view of lowerdie (c) isometric view of lower die (d) close-up view of die insert within lower die and (e) various die inserts
A considerable effort has gone into the development of complex FE models that are used to simulate the tube bending and subsequent hydroforming processes. These models have shown to accurately predict the complex strain paths that are involved in the two forming processes. Measured tube wall thickness and strain distributions (measured via circle grid analysis) have been accurately validated against the models. This forming history information is critical to the accuracy of the predicted energy absorption in the subsequent crash models. Shown below are the various contours of a pre-bent and hydroformed tube along with the comparison of the predicted and measured wall thickness and strain distributions for an aluminium AA5754 s-rail.
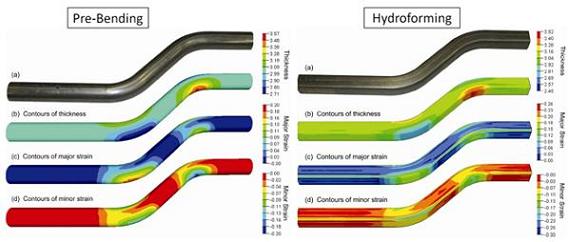
FE models of pre-bent and hydroformed AA5754 s-rails

The predicted and measured wall thickness and strain distributions around the circumference of a hydroformed aluminium AA5754 s-rail
The s-rail crash tests are conducted in a horizontal deceleration sled at the General Motors Technical Center. A schematic of the apparatus is shown below along with a picture of the test prior to and after an impact. During the impact test, the force versus crush distance is measured and then integrated to quantify the absorbed energy versus crush distance as shown below.
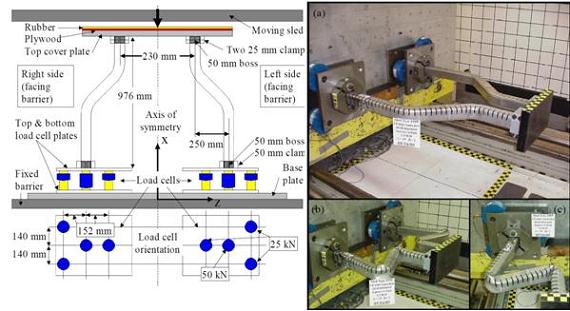
A schematic and picture of the deceleration sled crash test

Effect of hydroformed s-rail material (1.8mm wall thickness) on the crash response
FE models of the crash experiments have shown to accurately predict the crush loads and energy absorption. It has been shown that strain rate sensitive constitutive models (such as Johnson-Cook, Zerilli-Armstrong, Voce, etc.) are necessary to predict the high rate deformation that an s-rail undergoes during a crash test as shown below. The strain rate sensitive constitutive models used in this work are calibrated from high strain rate experiments which is explained in detail under the High Strain Rate Material Behaviour research area.
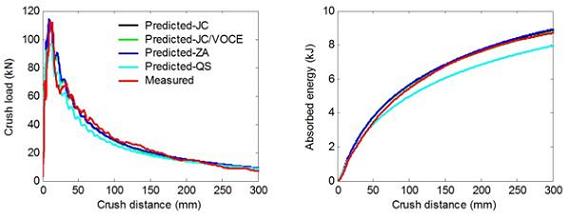
Crash results predicted using four different constitutive material models, and measured crash test results for hydroformed DP600 s-rails bent at an R/D ratio of 2.0 (JC = Johnson-Cook, JC/VOCE = Modified Johnson-Cook with Voce-type quasi-static term, ZA = Zerilli-Armstrong, QS = Quasi-static power law model)
In addition to predicting the energy absorption during impact, the geometry of the crushed s-rail must be predicted accurately, especially at the hinge points where the s-rail collapses. This is important because predicting the occupant compartment intrusion is critical to passenger safety. The below figure shows the accurate prediction of the crashed s-rails in the non-hydroformed (circular cross-section) and hydroformed (square cross-section) conditions.
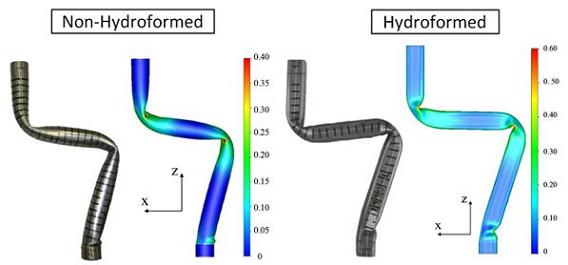
Actual and predicted s-rails in the non-hydroformed and hydroformed conditions (contours of effective plastic strain are shown)
Axial Members
Unlike an s-rail, which absorbs energy via bending deformation, axial members undergo a progressive folding type of collapse (see below) and are typically located at one end of the s-rail member. Once the energy absorption of the axial members is exhausted, the s-rail then absorbs the remaining energy of the impact. Axial structures isolate deformation to regions located at the front and rear of a vehicle.
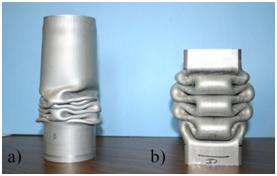
Folding behaviour for AA5754 alloy tubes: (a) round tube - diamond mode and (b) square high pressure hydroformed tube - symmetric mode
Similar to the s-rail work, straight sections of tube stock are hydroformed into axial members with a square cross-section. Both the low pressure and high pressure hydroforming process are used to form the axial members. In addition to varying the hydroforming process, the hydroformed corner radius (see figure below) and end-feed during high pressure hydroforming are also studied.
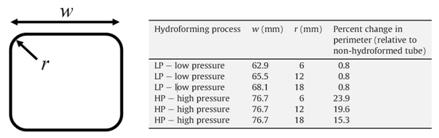
Variations in hydroforming process and corner radius for AA5754 aluminium alloy tubes
Axial members are quasi-statically crushed in a load frame at the University of Waterloo and dynamically crash tests in a horizontal deceleration sled at the General Motors Technical Center (see below). During the impact test, the force versus crush distance is measured and then integrated to quantify the absorbed energy versus crush distance.
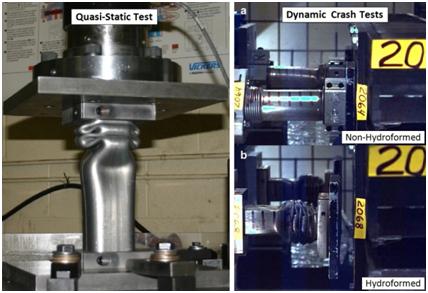
Quasi-static and dynamic crash tests of axial members
FE models of the impact tests accurately capture the energy absorption and folding behaviour as shown below. Also shown below is the importance of incorporating the full forming history (from hydroforming to impact) into the impact simulation, where not including the thickness change or work hardening predicts false energy absorption.
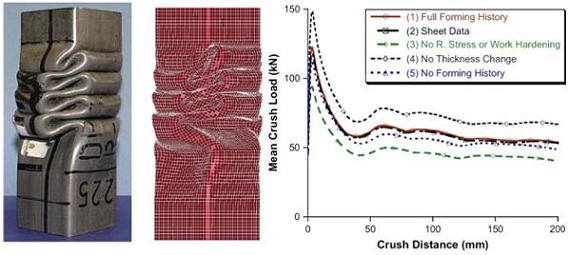
Actual and predicted axially crushed DP600 member and the effect of incorporating the forming history on the predicted impact loads of a HSLA350 tube
The development of advanced constitutive models to improve the prediction of axial (and s-rail) crash is also a focus of the work at the University of Waterloo. Some of the models that have been implemented are:
- von Mises Isotropic hardening model
- Non-linear isotropic-kinematic hardening model
- Johnson-Cook strain rate sensitive model
- Zerilli-Armstrong strain rate sensitive model
- Voce strain rate sensitive model
- Yld2000-2d anisotropic model
- Gurson-Tvergaard-Needleman constitutive model
- A combined kinematic hardening anisotropic and strain-rate sensitive model