Non-destructive testing (NDT)
Non-destructive testing (NDT) is an examination technique to evaluate the integrity of a material, a mechanical component or other parts without causing physical damage. Among many types of NDT methods, ultrasonic NDT uses high frequency sound waves for the detection of flaws inside the structure. After World War II, the ultrasonic method proposed by Sokolovin in 1935 and later applied by Firestone in 1940 was soon developed to be a viable option for material testing. Over the years, the technology has been applied extensively across diverse areas. Many products have been commercialized worldwide, but most of them are based on the similar operating principle to the one illustrated below.
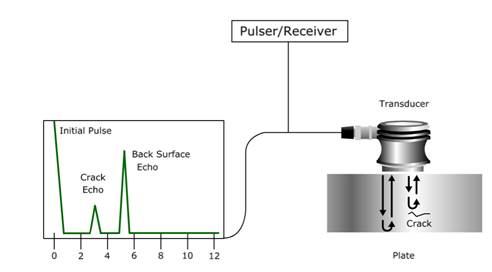
The transducer converts high frequency electrical signals provided by the pulser into the mechanical pulse waves. The waves propagate through the tested material until they meet a defect within the material or the other end and are reflected back. The reflected wave will then be picked up again by the transducer as an electric signal which is then sent to a receiver circuit. The depth of the crack within the material can be calculated based on the sound speed of the material and the time delay between the incident pulse and the echo pulse. Albeit the neat and straightforward principle of the method, one major obstacle it is facing is that the performance of the testing relies heavily on the training level of the operator, which means the human factor has a great impact. Therefore, in order to improve the quality of the measurement and also expand the applications of the method, our lab is seeking a way to automate the ultrasonic NDT technique and the goal is to integrate this technology into the conceptual “smart factory” in the future.
Currently, our lab is developing our own NDT system, which is now built with a DPR300 Pulser/Receiver (JSR Ultrasonics, USA) and a digital oscilloscope (Tenma, UK) show below which can communicate with a personal computer. Single channel contact probe and immersed probe are used to take measurements on the workpieces. Using this setup, we are able to investigate the suitable control mechanism to manipulate the sensor so that the measurement can be fully automated.
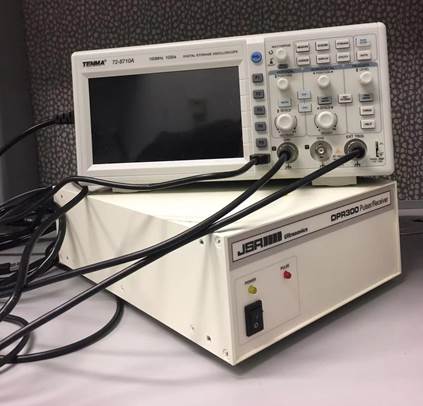