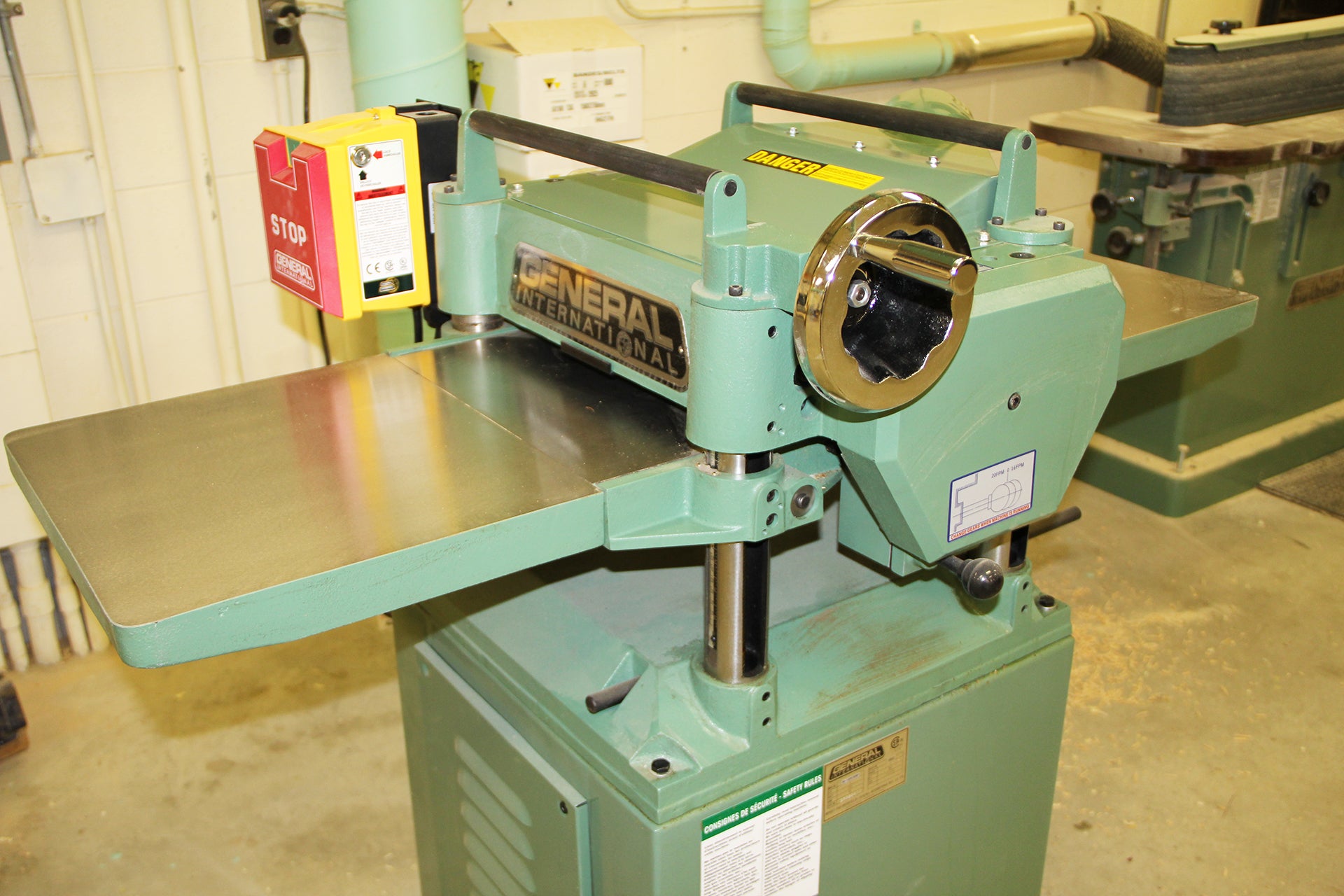
Description and uses
The planer (also called a surfacer) is a single purpose machine that planes wood to uniform thickness. It mills the surfaces of lumber, creating faces or planes that are parallel. The tool is invaluable for customizing standard stock thickness and making material flat. More than one pass through the machine is required if the thickness of your material has to be reduced by more than the max. cut depth of 1/8” (3mm). Hardwoods may require max. cut depths of no more than 1/16” (1.5mm) and multiple passes. The planer is equipped with a special helical cutter head with 4 rows of carbide inserts for a total of 42 inserts. The planer has a 2-speed gearbox and the outfeed rate corresponds to the selected cutter head speed. Raise or lower the cutter using the hand wheel at the side of the machine to set desired thickness. Ensure that the machine will cut your wood with the grain to reduce splintering and chipping of the surface. Turn the machine on and feed your work piece into the cutter head until the feed roll automatically controls the rate of cutting. Keep your hands away from the chute. Pick up the material as it feeds out the back of the chute. Work should be at least 8” (20cm) long and no thinner than 3/8” (10mm). Never try to feed wood into the back of the chute.
Further considerations
- Wood must be fed with the grain and never across the grain since the pressure of the feed roll and the cutter head may shatter the wood and cause damage to the machine.
- Verify location of on off switch and/or emergency power disconnect.
- Do not look into the chute. Stand slightly to the side of the machine when feeding in stock.
- Do not plane wood that has loose knots or serious defects.
- Make sure that the work piece is free of nails or foreign objects that could cause personal injury or damage to the machine.
- Twisted stock will remain twisted when planed; the machine is only capable of making two surfaces parallel.
Tip: Several pieces of same thickness and length can be fed through the machine at the same time. This action not only saves time; it also places less strain on the machine and the cutting blades.