There are several research facilities in the Fluid Mechanics Research Laboratory that are utilized for various experimental investigations. In particular, a variety of fluid mechanics problems can be studied for a wide range of Reynolds numbers in our closed-loop wind tunnel, adaptive-wall wind tunnel, water tunnel, and large scale wind generating facility.
By conducting complementary experiments in these facilities, we can take advantage of specific measurement and flow visualization techniques in order to perform an in-depth analysis of the flow field. Specific flow diagnostic methods include Time-Resolved Particle Image Velocimetry (TR-PIV), 3-component Laser Doppler Velocimetry (LDV), Hot-Wire Anemometry, time-resolved pressure transducers, microphones, and various flow visualization techniques.
Below is a list of anchor links to see specific facilities:
- Closed-loop wind tunnel
- Adaptive-wall wind tunnel
- Live fire wind tunnel
- Jet facility
- Water tunnel (flume)
Closed-loop wind tunnel
Modern laser-based fluid measurement techniques, such as LDV and PIV, require the flow to be seeded with tracer particles, for which our re-circulating wind tunnel was specifically designed. The tunnel can be operated at velocities between 2.5 and 32 m/s, with the free-stream turbulence intensity of less than 0.1%. The test-section is 2' x 2' x 8' and provides full optical access, thus making the facility ideally suited for laser-based flow diagnostic and flow visualization.
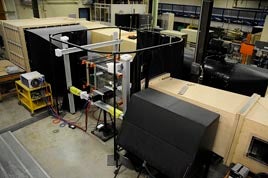
Figure 1. Closed-loop wind tunnel facility.
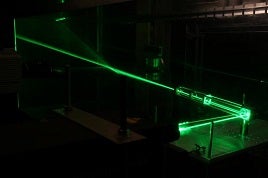
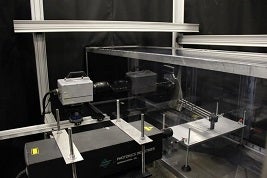
Figure 2. PIV setup in the closed-loop wind tunnel.
Adaptive-wall wind tunnel
The presence of solid boundaries is known to give rise to aerodynamic blockage effects in wind tunnels. Due to their detrimental influence on experimental data, such blockage effects must be quantified to allow for appropriate data correction. However, correcting wind tunnel data is difficult and, in many cases, impossible to implement. Our 2'x3' adaptive-wall wind tunnel (Fig. 1) offers a unique solution to this problem. In particular, blockage effects can be virtually eliminated by configuring the wind tunnel walls to imitate the shape of outer streamlines in an unbounded flow field. The free-stream velocity in the wind tunnel can be adjusted from 2.5 m/s to 40m/s, with the turbulent intensity of less than 0.3%. With such a wide operating velocity range, this facility is suitable for studying various fluid mechanics and aerodynamics problems.
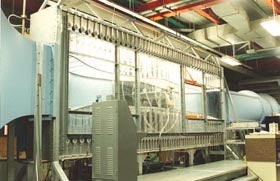
Figure 3. Adaptive-wall wind tunnel facility.
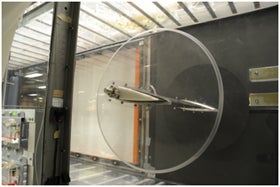
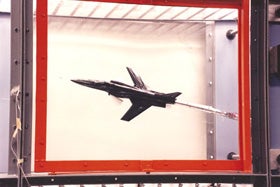
Figure 4. Airfoil and aircraft models installed in the test section of the adaptive-wall tunnel.
Live fire wind tunnel
Through our partnership with the Live Fire Research Laboratory, we have access to a large-scale wind tunnel facility to perform large scale experiments. This facility has a 20'x20' cross-section and is capable of producing wind speeds of up to 11.5 m/s.
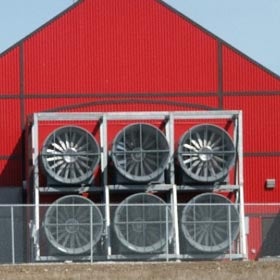
Figure 5. Six large-scale fans at the back of the facility produce wind speeds of up to 11.5 m/s
Jet Facility
The jet facility is a portable high aspect ratio slot jet (2D jet) that can be operated at speeds up to 35 m/s. It has been designed and built at University of Waterloo in order to study various types of jet flows, such as normally impinging flow, oblique impinging flow, wall jet flow, and free jet flow.
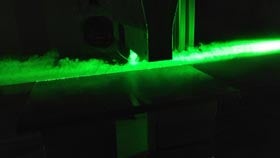
Figure 6. Flow visualization of an impinging jet using high speed cameras at the jet facility.
Water tunnel (flume)
Our water tunnel has a 1.2m x 0.5m cross section and a 2.4m long test section. This facility is used for investigating various fluid flow phenomena, including flows over complex cylindrical geometries and vortex induced vibrations. The water tunnel is ideally suited for LDV and PIV measurements and for conducting high-quality flow visualization.
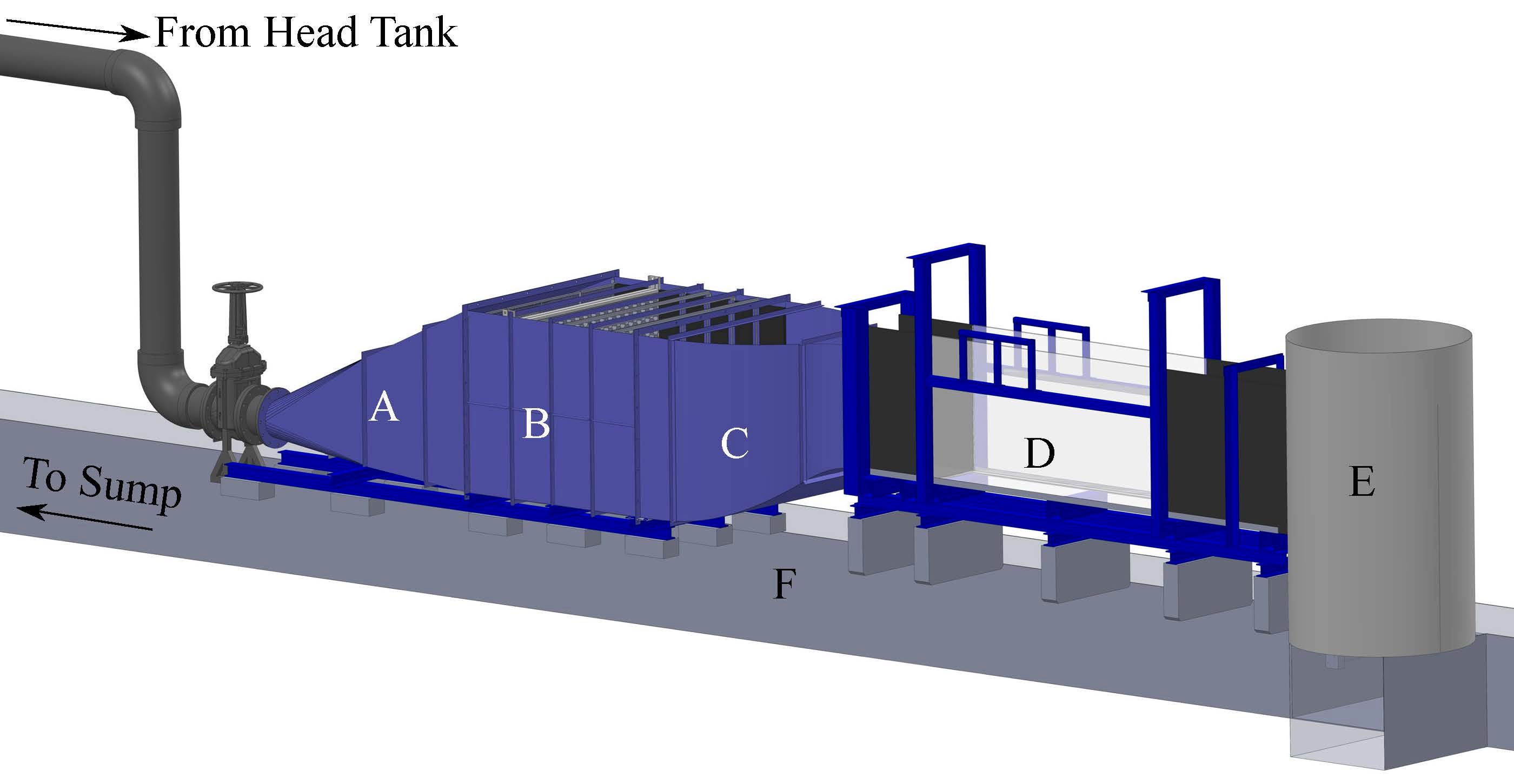
Figure 7. Water tunnel facility A: diffuser , B: settling chamber, C: contraction, D: glass test section, E: outlet tank, and F: return channel to the sump.