Flows over cylindrical geometries are encountered in many engineering applications, e.g., civil structures, underwater installations, and heat exchangers. In our laboratory, combined experimental and numerical studies are conducted to improve understanding of wake development and structural loading on cylindrical bodies, which govern heat transfer, vibrations, and noise generation in relevant applications.
Experiments are carried out in both our water flume and recirculating wind tunnel facility and are complemented by numerical simulations at low to moderate Reynolds numbers. Figure 4 shows Direct Numerical Simulation (DNS) results for cross-flow over a uniform circular cylinder for a range of Reynolds numbers. For each case, vortices are shed alternately into the wake, forming a von Kármán vortex street.
The vortices are two-dimensional and laminar for the Reynolds number (Re) of 100, develop three-dimensional instabilities for Re=220 and 300, develop finer scales and distortions in the wake for Re=800, and turbulent transition occurs in the separated shear layer for Re=1575.
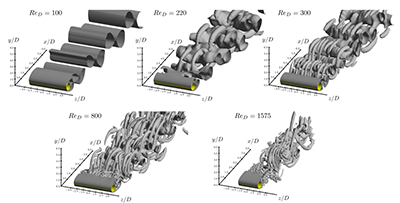
Figure 1. DNS results for a cylinder in cross flow showing different topological regimes for ReD = 100-1575. Vortices are visualized using the λ2-criterion (λ2=0.01).
Complex cylindrical bluff bodies are also studied. Figure 5a shows an experimental flow visualization image of vortex shedding in the wake of a cylinder with a step change in diameter. The discontinuity in diameter (at Z/D=0) results in cellular vortex shedding pattern in the wake. Three distinct vortex shedding cells can be identified in figure 5, one in the wake of the small cylinder and two in the wake of the large cylinder.
Each vortex cell has a distinct shedding frequency, which results in complex vortex interactions at cell boundaries. Figure 5b and c show numerical results, which reproduce the vortex dynamics observed experimentally and illustrate the complexity of turbulent vortex shedding in the wake of a step cylinder.
5a.
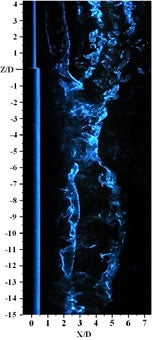
5b.
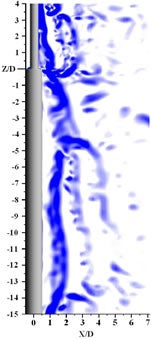
5c.
Figure 5. Flow over a step cylinder at Re=1050: a) experimental flow visualization b) numerical results showing vorticity at the same plane c) numerical visualization of turbulent vortex shedding in the wake of a step cylinder at Re=1050. Note, the cylinder is oriented along z axis, and flow is from left to right.
Figure 6a-c shows Particle Image Velocimetry (PIV) measurements in the wake of finned cylinders with varying fin densities. With decreasing fin spacing c/D (i.e., increasing the density of fins), the wake region grows significantly and vortex formation is displaced into the wake (e.g., Fig. 6c).
The change in flow development has profound effects on the fluctuating lift forces, while the mean drag trends are described well by models of additive viscous drag on the fin surfaces. A definition for an effective cylinder diameter was developed incorporating flow blockage from boundary layer growth on the fin surfaces. The resulting length scale universally collapses shedding frequency data for finned cylinders (Fig. 6d).
6c.
6d.
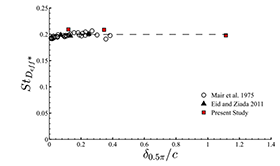
Figure 6. Spanwise vorticity in the wake of finned cylinders at ReD= 1040 for varying fin density (a) c/D = 8, a uniform cylinder, (b) c/D = 0.361, and (c) c/D = 0.111. A Strouhal scaling (StDeff*) for the shedding frequency is shown in (d).