Background information
Joining of magnesium alloys is an enabling technology for the increased use of these materials in structural automotive applications; however, there are many technology gaps that need to be addressed to realize this potential. Joining of wrought and cast components must be considered in materials selection and the design process as it is intrinsically linked to crash performance, fatigue life, corrosion resistance, and noise transmission of the auto body. Development of efficient processes to produce high quality joints with magnesium in similar and dissimilar combinations, such as steel and aluminum, is critical for widespread integration of magnesium in automotive applications. Several joining technologies have been identified for potential in joining of magnesium, including: resistance spot welding, laser welding, electromagnetic welding, friction stir welding (FSW), mechanical fastening, self‐piercing rivets, and others. Significant work is required to optimize these processes and determine which technologies are best suited for specific applications.
Objectives
Electromagnetic welding
- Establish the feasibility of electromagnetic welding of magnesium to magnesium, magnesium to steel and magnesium to aluminum sheets.
Resistance spot welding
- Investigate the influence of surface conditions on the weldability of AZ31 magnesium alloy in terms of weld nugget growth, surface expulsion, joint strength, and electrode tip face stability.
- Studies on weldability for RSW of AZ31 alloys.
- Establish the relationship between microstructure and mechanical properties of the resistance spot welding (RSW) AZ31 magnesium alloy.
Laser welding
- Evaluate and optimize autogenous laser welding processes in similar material combinations.
- Determine the effects of process parameters on weld quality.
- Evaluate the weldability of current and future magnesium alloys, and determine the influence of material characteristics such as inclusion density, pore density, and surface oxide conditions on weldability.
Equipment
- Pulsar-25 kJ electromagnetic machine
- NUVONYX ISL-4000L diode laser
- Single phase spot welder
- Median frequency direct current spot welder
Results/findings
Electromagnetic welding
- Feasibility of electromagnetic welding of magnesium to aluminum sheets has been established.
Resistance spot welding
- Acid cleaning produced much more uniform surfaces with lower contact resistance, which resulted in higher shear strength with the same weld size because of lower percentage of internal nugget porosity.
- Process windows for AZ31-A and AZ31-B alloys have been established.
- The AZ31-A and AZ31-B alloys welds consist of five microstructurally distinct regions across welding zones, i.e. base metal (BM), heat affect zone (HAZ), transition zone (TZ) for AZ31-A or columnar zone (CZ) for AZ31-B, fine dendrite zone (FDZ), and equiaxed dendrite zone (EDZ).
Laser welding
- Diode laser welds are hindered by solidification cracking.
- CO2 welds require increased shielding to limit the hydrogen porosity that may enter the weld when the violent mixing and boiling of the weld pool occur.
- Cleaning of the oxide layer is required for sound welding as during welding, the oxide does not remelt and leads to cracking and stress concentrations in the finished weld.
Pictures/figures
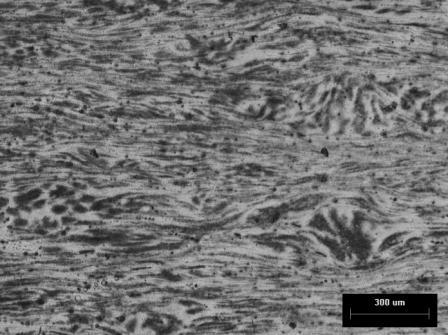
Figure 1) Etching reveals the microstructure of the magnesium alloy
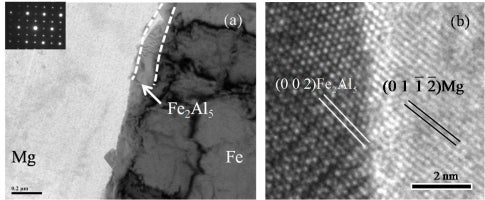
Figure 2) TEM observation and diffraction pattern of the magnesium/steel spot welded interface: (a) interface of bonded magnesium (Mg) and iron (Fe) with a Mg/Fe2Al5/Fe structure; (b) HRTEM of the low energy Fe2Al5/Mg heterophase interface
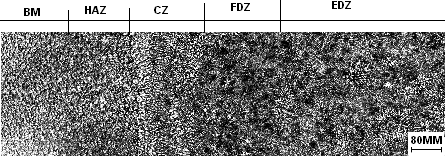
Figure 3) AZ31 alloy weld consists of five microstructurally distinct regions