Background information
Friction-stir welding (FSW) is a solid-state joining process and is used for applications where the original metal characteristics must remain unchanged as much as possible. The process is applicable to aerospace, shipbuilding, aircraft and automotive industries. One of the key benefits of this new technology is that it allows welds to be made on alloys that cannot be easily arc welded.
More recently friction-stir processing (FSP) has been shown to alter the surface microstructure of a material via in-situ thermo mechanical processing. The FSP causes intense plastic deformation and material mixing at high strain rates, resulting in significant refinement, and redistribution of particles in the processed zone.
Objectives
- Friction stir welding of light weight alloys (Al and Mg)
- Dissimilar material welding (Al, Mg, to steel)
- Friction stir processing of nano-composites
Equipment
- 7.5 HP Jafo milling machine
- Micro hardness indenter
- Tensile test machine
- Optical microsocpy
- Scanning electron microscope
Pictures/figures
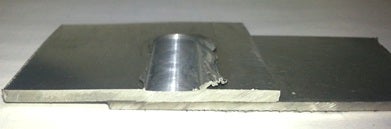
Figure 1) Al 5754 to DP600 dual phase steel lap weld
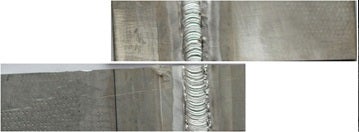
Figure 2) Optical micrograph showing the stir zone of a friction stir processed nanocomposite
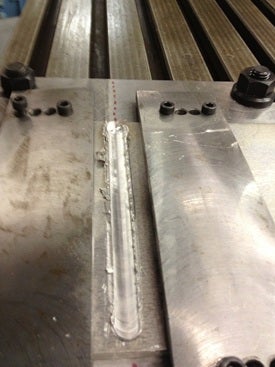
Figure 3) Al 6061 to AZ31 Mg alloy friction stir lap weld fracture surface which achieved fracture shear stress of 360 MPa
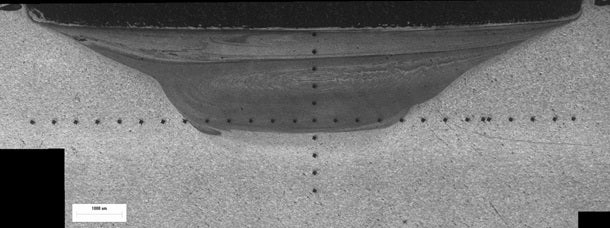
Figure 4) FSP nanocomposite sample after 3 passes
Figure 5) Reconstructed 3D model of dissimilar Al 2024 / Al 6061 dissimilar friction stir weld, compiled from serial sections