
Estimating external corrosion rates for buried piping
The integrity of buried piping is a significant concern in many industrial facilities, including nuclear power plants, where failure or leakage can have significant economic, environmental, and safety consequences.
Unlike aboveground piping, assessing the degradation of buried piping is very difficult due to access restrictions. The most common failure mechanism is external corrosion, which depends on
- Physical and electrochemical (and microbial) processes
- Piping and soil characteristics
- Inspection and preventive maintenance methods
Most buried pipe is constructed of carbon steel, although many other materials have also been used.
The main objective of this study was to analyze the available data from the industry and estimate representative external corrosion rates for carbon steel piping under different soil conditions. The resulting rates can then be used to predict the corrosion allowance over a given evaluation period for the fitness-for-service (FFS) assessment of buried and underground piping.
Data analysis
One of the earliest, and still the most comprehensive longterm publicly available study of underground corrosion is by the National Bureau of Standards (NBS) between 1922 to 1952. The extensive NBS field program involved more than 36 500 individual specimens, representing 333 varieties of materials, buried at 128 different test sites throughout the United States. The samples or specimens were retrieved over several years from each test site and measured for mass loss (i.e., general corrosion) and maximum corrosion penetration depth (i.e., localized corrosion or pitting).
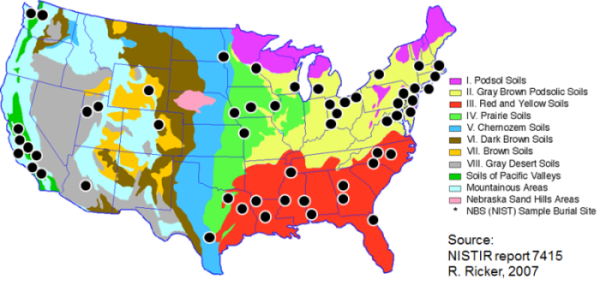
Methodology
The long-term observations from previous studies indicate that the corrosion process exhibits erratic variations in the early stages, e.g., less than 5 years. After this, the corrosion growth appears to reach a so-called steady state. In other words, the corrosion rate becomes approximately linear after a period of accelerated growth.
It is not possible to predict the life of an underground steel structure from measurement of depths of pits made after some short period of exposure, such as 1 or 2 years (M. Romanoff, 1952).
As a result, the steady-state concept was also adopted in this work, with the corrosion rates estimated for each test site using the following logarithmic regression model
where Y(t) denotes the corrosion penetration at time t, and a and n represent site specific constants.
The (nonlinear) logarithmic regression model of corrosion was fitted to the maximum penetration and weight loss data over time for varieties of carbon steel included in the NBS dataset. The steady-state rate for a given soil site was defined as the slope of the chord joining the model predicted corrosion penetration depths (or uniform thickness loss) at t = 5 years and t = 15 years. Example results for test site 19 (Des Moines, IA – silt loam) are shown below.
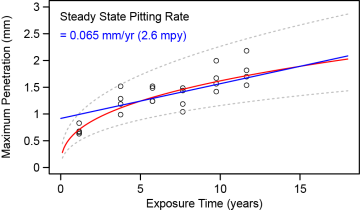
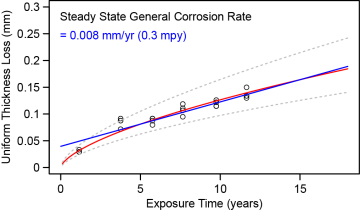
Classification based on soil texture
Many studies have investigated the correlation of corrosion rates with parameters related to soil and the environment, including soil resistivity, moisture, pH, acidity, soil chemistry, etc. However, given the high spatial and temporal variability of the parameters at the local scale adjacent to the buried specimens, the results have generally been quite poor. Similar to other studies, no meaningful differences or correlations were found in our study.
Soil texture represents a more broad classification of soils, based on the relative proportions of sand, silt, and clay present in the material. As a result, the soil test sites and the estimated steady-state corrosion rates were grouped by soil texture and then fitted by probability distributions, shown below. These results can then be used to estimate a representative corrosion rate (e.g., 80th percentile value) for piping buried in a given type of soil.
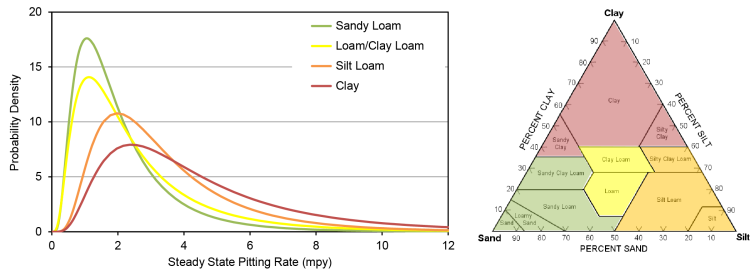
Benefits
The direct benefit and main application of the study results is the FFS assessment of buried piping. The estimated distributions of a steady-state corrosion rate can be readily used to predict the remaining component lifetime and (or) the time until the next inspection. The results help to satisfy both leakage and structural integrity requirements by determining the future corrosion allowance in terms of the localized (i.e., pitting) corrosion and the uniform (i.e., general) corrosion rates.