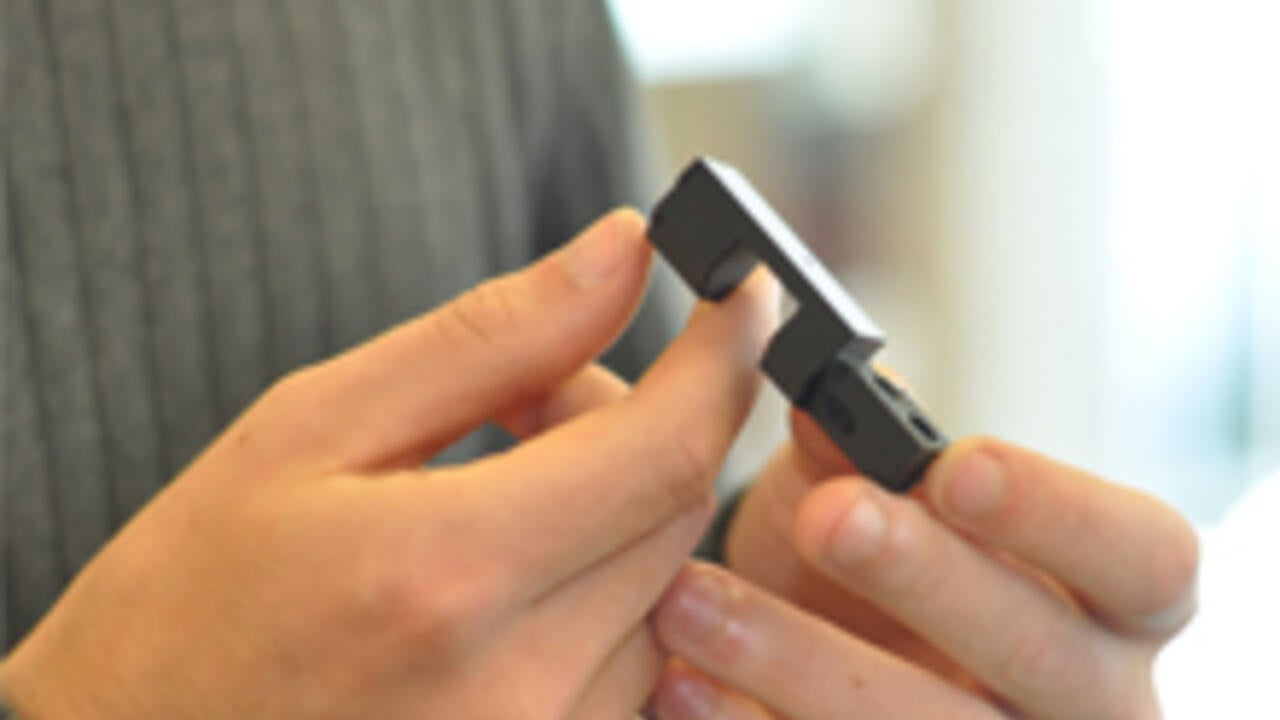
Waterloo students make car parts with 3D printer
3D printer is an “innovation machine” for Waterloo students who want a quick and affordable way to create prototypes
3D printer is an “innovation machine” for Waterloo students who want a quick and affordable way to create prototypes
By Christian Aagaard Communications and Public AffairsThe coolest things in Engineering 5 are usually found in the ground-level service bays, home to student teams intent on turning transportation on its head.
But the buzz lately has shifted to the second floor where the University of Waterloo's Student Design Centre (SDC) runs a 3D Print Centre, featuring a Fortus 360mc three-dimensional printer.
For those who use it, it's an innovation machine.
"We want to keep the focus on undergraduate students,'' says Peter Teertstra, SDC's director. "We want take their entrepreneurial spirit and vision to really show it off. Here, they can afford to ‘print’ their designs."
In 3D printing, printers read rich design files and make objects out of plastics or powdered metals applied in extremely thin layers.
Motor mounts, an exhaust manifold and an adjustable wrench with a functioning worm screw make up the list of items the centre's printer has produced from plastic since it began operating last fall.
With support from two partners in the 3D printing business, Cimetrix Solutions and Stratasys Ltd., the centre installed the unit for $100,000 - the amount it received as a grant from the Denso Foundation. The Hyphen division of Christie Digital Solutions Canada Inc. is also a partner.
Today, with the printer running 24/7, the centre has access to another one operating in the Mechatronic Vehicle Systems lab. For undergraduate students, the centre charges for work based only on the volume of material used, a policy in place since its inception in January 2013.
Last year, mechanical engineering student Stefanie Bruinsma was the first co-op placement to run the machine. Among other things, she "printed" a piston.
For cash-poor, time-strapped students, the printer offers a quick and affordable means of creating "iterations," which are trial-and-error prototypes. This is proving to be a significant resource for the Engineering student teams designing Mars lunar rovers, clean-running snowmobiles, rockets and other vehicles.
"With 3D printing, our student teams can now add additional design enhancements, have more invested in their vehicles, and present significant modifications with what they take to competition," says Ross McKenzie, WatCAR's managing director.
Teertstra says students in any faculty can use the printer. It might make masks for a drama, or a model of a molecule. Students pay for the service via UWaterloo media.doc on campus.
Previously, for the student teams, getting a proper prototype meant numerous trips to the machine shop and several days of effort. "Here, you can press a button and it's done," Teertstra says.
Read more
Special issue of Waterloo Magazine celebrates women who lead, and explores equity in education and the workplace
Read more
New building will have some of the best research facilities in the world and support students as they design, build and test their ideas
Read more
With AI, manufacturing and green tech-focused companies, Waterloo-linked innovators are scaling businesses for global impact
The University of Waterloo acknowledges that much of our work takes place on the traditional territory of the Neutral, Anishinaabeg, and Haudenosaunee peoples. Our main campus is situated on the Haldimand Tract, the land granted to the Six Nations that includes six miles on each side of the Grand River. Our active work toward reconciliation takes place across our campuses through research, learning, teaching, and community building, and is co-ordinated within the Office of Indigenous Relations.