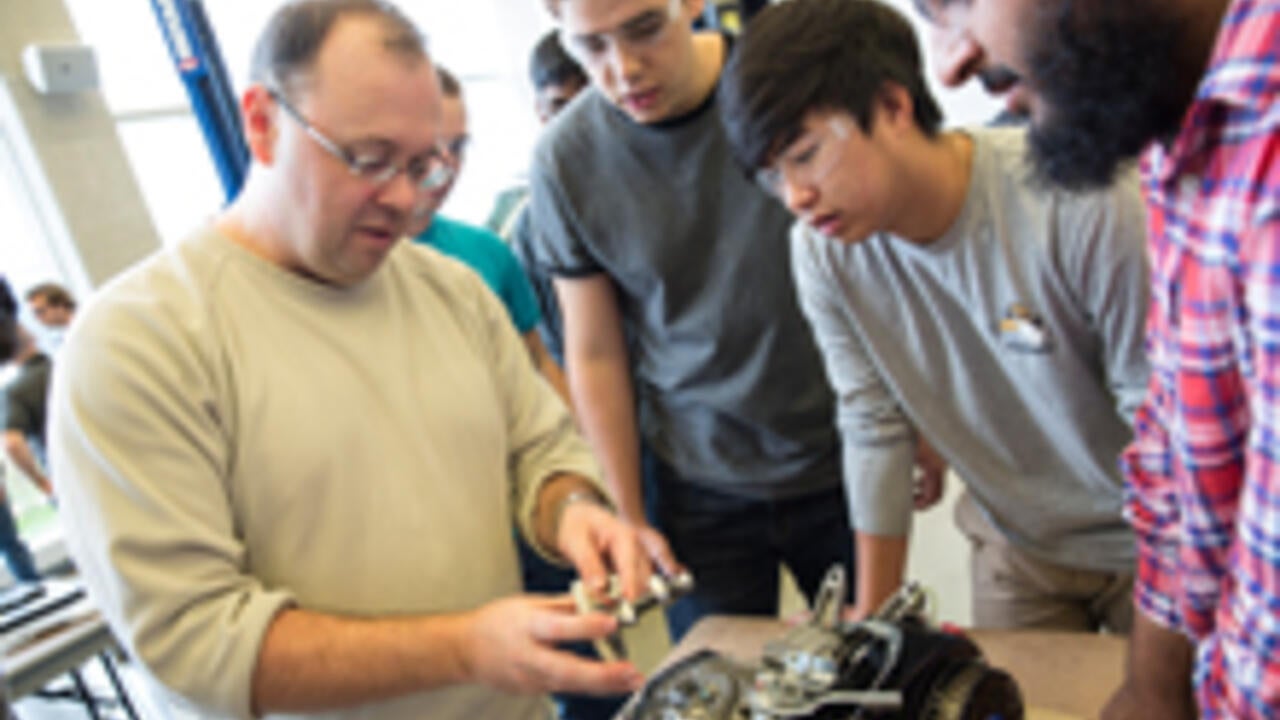
Hands-on learning in Waterloo’s engine dissection lab
Waterloo engineering students get their hands dirty while they learn about design and function in the engine dissection lab.
Waterloo engineering students get their hands dirty while they learn about design and function in the engine dissection lab.
By Christian Aagaard Marketing and Strategic CommunicationsThe room smells of motor oil. Parts lie scattered on tables and students exchange uncertain glances.
This is the engine dissection lab for first-year engineering students — dirt-under-your-nails, experiential learning at the University of Waterloo. The specimens are snow blower engines.
“They strip them down, then they put them back together and the engine has to start,” says Michael Collins, the associate professor minding the lab on the ground floor of Engineering 5.
The program has nothing to do with getting the campus ready for winter, and everything to do with turning out better engineers. Most of the students in the course are taking their first steps toward careers in mechanical or mechatronics engineering.
How can they design, Collins asks, if they don’t understand mechanical function, or speak the language of machinists and technicians?
So they wiggle off parts, take measurements, scribble notes and sketch. Some students took shop class in high school; some have worked on farm machinery.
“A lot of them come in with almost no experience working with hand tools,” says Collins. “They might wonder why the ratchet wrench works in one direction, but not the other.’’
Professor Sanjeev Bedi introduced the lab to mechatronics students a few years ago. Collins and Professor Roydon Fraser have applied it to mechanical engineering.
A week after stripping and re-assembling their engines, the students test them out — first in a dry run hooked up to a computer, then outside, with fuel.
Two years later, the students see those engines again. In Mechanical Engineering (ME) 321, the components have much to teach about the forces and dynamics at work during internal combustion.
In ME 340, professors Mary Wells and David Weckman call on the students to think about the design and manufacture of the parts. They set up a crisis for a Canadian engine-builder — the threat posed by a cheaper, off-shore knock off.
“We look at the product in the context of our manufacturing-processes course,” Weckman says. “How are the parts made, out of what materials? And the challenge is, how can we do it more cost-effectively, and be more competitive?”
It is both an engineering challenge and a real-world business problem.
“They learn hands-on skills, teamwork skills and they’re studying open-ended problems under constraints,” Wells says. “That’s really moving them to become professional engineers.”
An industrial metallurgy course, ME 435, uses full-size auto engines to teach about metals and alloys.
"It’s the best kind of learning when you’re having fun,” Collins says.
Read more
Waterloo team creates vision of a transformed world for architecture biennale
Read more
Waterloo celebrates its connection to the latest group of up-and-coming entrepreneurs
Read more
New building will house research on machine intelligence, mobile robotics, autonomous vehicles and wearable biomedical devices
The University of Waterloo acknowledges that much of our work takes place on the traditional territory of the Neutral, Anishinaabeg, and Haudenosaunee peoples. Our main campus is situated on the Haldimand Tract, the land granted to the Six Nations that includes six miles on each side of the Grand River. Our active work toward reconciliation takes place across our campuses through research, learning, teaching, and community building, and is co-ordinated within the Office of Indigenous Relations.