Using Our Prusa Printers
Our desktop printers are the perfect way to turn your ideas into reality. They currently print with PLA, PETG, and TPU/FLEX. Our materials are priced as $0.06/g for PLA, $0.07/g for PETG, and $0.08/g for TPU/FLEX material.
To use the desktop printers, come in to the RPC during open hours, slice your parts, find an avaliable printer, and start your print. Our staff are available to help you set up your print and to recommend ways to make sure your print is a success.
Using Prusa's own slicer you have complete control over your print and confidence knowing the software was designed specifically for the printer. You can use the slicer on our PC here or download it for yourself on from the Prusa website. Below we will walk you through some important features in the slicer.
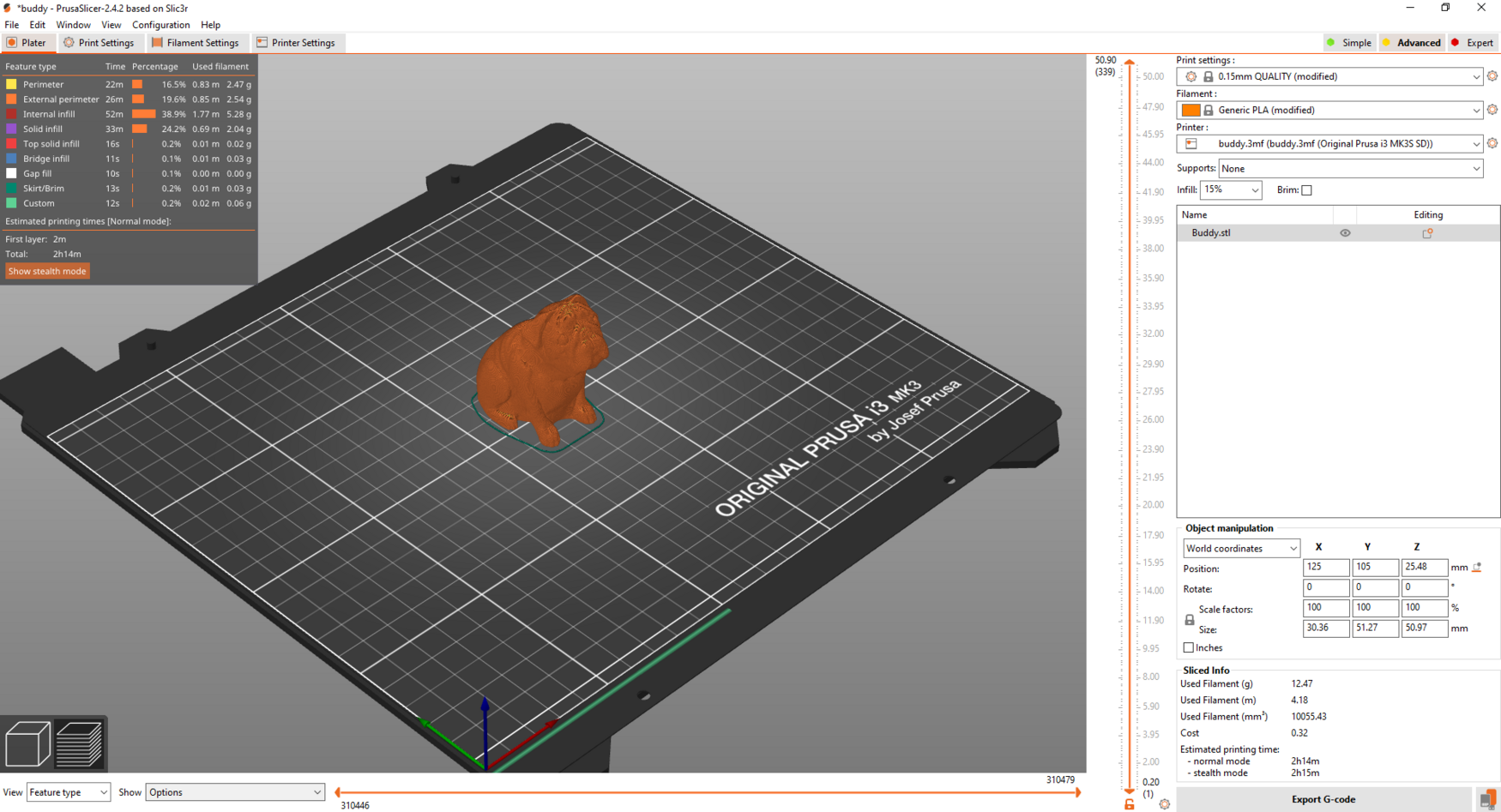
Once a design is sliced you get infomration about the time to print, the amount of material used, and a break down of how much time and material the different features are using
Intro To The Slicer
First, you will need to save your CAD file as an .3mf, .stl, .obj or .step (in order of preference).
Once you have your file open it in the Prusa slicer. Ensure the size is correct with the information on the right hand side. You can move, rotate, scale, and snap a side of your print to the baseplate using the various controls on the left. To reduce the required support, snap the largest flat side of your print to the baseplate.
Next, you select the resolution under Layer height between 0.05mm to 0.3mm(0.15mm to 0.2mm is standard), your filament type (typically Generic PLA), your Infill density (keep it to 30% or below), and your Printer (either i3 MK3S+ or MINI+).
Finally click Slice now (bottom right), then Export g-code (same place) and save to a USB drive for a MINI+ printer or an SD card for a MK3S+.
Above the Basics
Auto generating supports is typically the only setting you need to select, however if you have more experience 3D printing, or you're just feeling a bit adventurous, you can customize many different aspects of your print.
By switching through simple, advanced, and expert modes (top right) you will gain access to more and more settings in the print, filament, and printer settings (top left).
Print settings is the main one you will be accessing, it deals with things like infill, supports, layers, and nozzle speed. Filament settings is used for temperature, and retraction tuning. Printer settings should remain untouched.
Information on some of these settings can be found below.
Infill
- Infill can be modified to change the density (as a percent of volume), the infill pattern/styles, and the top and bottom fill patterns (with these being the visible surfaces on the top and baseplate). Decreasing the infill will make your part lighter and also shorten printing time, 15% infill is suitable for most prints. If your part needs to support a greater load, increasing the wall thickness/shells with have a greater impact on the overall strength than increasing the infill.
- Ironing as the name implies uses the hot nozzle to smooth or iron out the specified part of of the print, however, it adds a lot of time to the print. Can be good for aesthetic purposes when a very smooth layer is desired (you cannot iron the layer on the baseplate)
- Reducing Print Time has two interesting options. Combining infill of multiple layers, since it is not visibile it can be a little messier looking and only infill where needed, essentially making internal supports.Both are great ways to cut down print time and/or material without sacrificing print quality
Speed, Temperature, and More
Selecting the appropriate material in the slicer under filament will slice for the recommended temperature and speed settings. However, if you'd like to adjust these settings this chart contains the recommended settings for all the thermoplastics you might use here:
Material | Print/Nozzle Temp (°C) | Print Bed Temp (°C) | Print/Nozzle Speed (mm/s) |
---|---|---|---|
PLA | 190-220 | 55-70 | 40-100 |
PETG | 230-250 | 80-90 | 30-50 |
TPU / Flex | 210-240 | 25-60 | 20-40 |
- When setting your own nozzle speeds keep first layer, bridges, and all perimeters (especially small & external) very low as these require more precision than the other layers. (ex. PLA can be anywhere from 20-45mm/s for these )
- Infill and Solid infill can have a fairly high speed as they are less important visually
Support material
- Support Material has the option to turn support material on/off, set it to auto generate (they can be manually painted on), the threshold angle for supports to be used, and the first layer density. Activating the checkbox for Generate support material and making sure supports are generated everywhere is usually adequate for most prints and ensures all necessary features are supported
- Raft allows you to create a support base your print will float on (like a raft) to give it extra support and allow for removal from the baseplate without fear of breaking
- Options for Support Material and Raft gives you multiple modifiers to really hone in your support material to ensure it's exactly what you want. However, the auto generated supports usually work well for most prints.
Layers and Perimeters
- Layers are how a slicer gets it's name. It slices your design into hundreds or thousands of very small layers it is going to make out of the filament. You can modify layer height to increase quality/resolution of print, however, this also takes more time. The first layer height is often slightly larger when using a very fine layer height just to ensure good bed adhesion.
- Shells determine your print's solid wall thickness at the top, bottom and sides. This can be very important if you know your print will be load bearing, as the wall thickness has the greatest impact on structural strength of the part.
- Quality and Advanced generally are good for all prints unless you have a reason to modify one. Ex) very long overhang/bridge so you turn on thick bridges.
- Fuzzy Skin is a fun experimental feature that gives prints a textured (almost fuzzy) appearance as the print is less smoothed so individual layer create the fuzz appearance.
Skirt & Brim
- Skirt is a default ring that gets printed around your design, it doesn't really have any real uses except for you know the nozzle is working and as a draft shield, so we recommend to turn this setting off by setting loops to zero.
- Brim if enabled creates a supporting base that funnels upward to create a stable first layer, good for prints with small or unstable first layers, or large flat prints to help with layer adhesion and prevent warping. It can be put outside, inside, or both and the width/offset of the brim can be modified