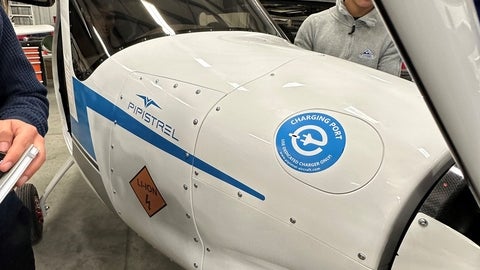
Circuit training in an e-plane: does an hour of charging give you an hour of flight time?
Landing and taking off are two of the most important skills for pilots to learn and perfect. As electric planes target the flight school training market, one important question is, how well do e-planes (and their batteries) support this type of training?
The Pipistrel Velis Electro is the world’s first type certified e-plane (2020 in Europe) and is being flown at the Region of Waterloo International Airport (CYKF). A team of Waterloo Wellington Flight Centre (WWFC) instructors and Waterloo Institute for Sustainable Aeronautics (WISA) researchers record and analyze data produced by the Velis Electro’s onboard data logger. A series of flights totaling 10 hours were made to see how the aircraft performed doing the takeoff, circuit and landing phases.
The pilots completed a total of 65 circuits, consisting of five to seven circuits per flight, in eleven flights. Average flight time was 54 minutes, and average air time was 40 minutes, followed by an average charge time of an hour for an average cycle time of a little over two hours per flight (pre-flight inspection and briefings included). The battery started at 100% state of charge (SOC) and each flight was planned to have at least 30% SOC remaining as a safety reserve when they landed for the last time.
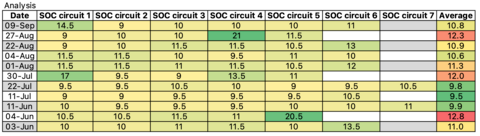
Table 1. Battery Discharge per Circuit
Flight time is recorded as Hobbs time, which starts when the Battery Engage switch is turned on and ends when the switch is turned off at the end of each flight. Air time starts when the wheels leave the ground at the beginning of the flight, and ends with touchdown. Both numbers are important as flight schools typically charge by flight time, while air time determines what flying exercises can be completed, as well as maintenance intervals. On average, the first take-off occurred at the 14-minute mark, after the pilot completed cockpit checks and thepower check (which is the Velis substitute for an engine run-up in traditional planes), and taxied to the launch point.
Looking more closely at the data, we can see that the battery starts with 100% SOC and drops only 2% SOC after 14 minutes of checks and taxiing. This is because the electric motor only needs power when you want to move. When holding in position, the motor is off, and no power is being drawn from the battery. The propeller often stops spinning completely. Similarly, very little power is required to maintain ground taxiing speed. In contrast, SOC drops quickly during the take-off and climb stage with high power settings. A complete circuit typically takes six to seven minutes and reduces SOC by 9-11% (Table 1). In a few cases, circuits were modified to accommodate other traffic, such as commercial jets taking off, and the extended circuit used up to 21% SOC.
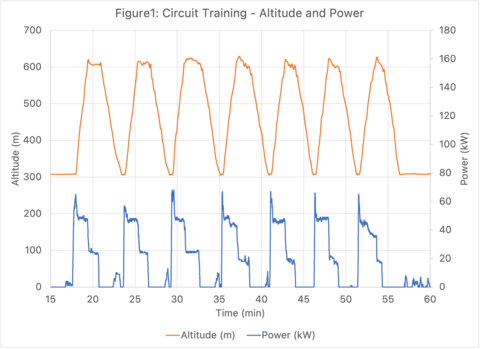
Figure 1. Circuit Training - Altitude and Power
The power settings used at each stage of the circuit are illustrated in Figure 1. The maximum power setting of 64kW is typically used for take-off and the first 90 seconds to climb to 100 meters (300 feet) above the airport, at which point the power is set to 48kW (climb power) for the remaining climb to an altitude of 300 meters (1000 feet) above the airport. This altitude is maintained with a power setting of 18 to 28 kW until the plane reaches the point to start descent, when power is reduced to near zero. Short bursts of power may be added to maintain the proper slope on final approach. After landing, the sequence is repeated: full power for takeoff, climb power for climb, cruise power for level flight, and idle or zero power for descent to land. The transition between landing and takeoff for these flights is called a ‘touch-and-go’ as multiple takeoffs and landings are achieved in the single lesson, and the plane never stops moving to save time. With each touch-and-go, the pilot develops familiarity with each stage of the circuit.
Back on the ground, the charger cable is plugged into the Velis (same as an electric car) and the battery is recharged. Each cycle begins with the SOC rapidly rising to 91% (Figure 2), at which point it slows down to protect the battery with a slower charge for the last 9%. However, charge rate is temperature dependent; the initial charging rate was slower on the cooler morning of August 31, ramping up more slowly to the usual charge rate of 20 kW once the battery reached 19°C. Looking more closely at the top of the graph (Figure 3), you can see that the charging rate slows down once again when above 97% SOC. On average, it took 22 minutes to charge from 91 to 100% SOC. The final 1% (from 99 to 100% SOC) took six minutes on average, but this ranged from three to eight minutes depending on battery temperature and other factors. On average, it took 60 minutes to charge from 35% to 100% SOC. Starting at 30%, an hour’s charging reached 99% SOC.
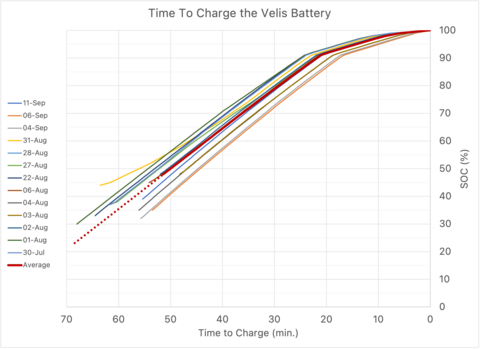
Figure 2. Time to Charge the Velis Battery
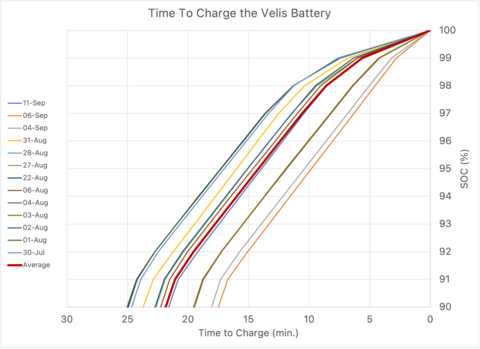
Figure 3. Time to Charge the Velis Battery - 90-100%
So, do you get an hour of flight time for an hour of charging? An hour of charging is likely to get you to 99% SOC, if you start around 30% SOC. That should give you six circuits and 54 minutes of flight time on average. However, if you added one more circuit, it would probably take seven minutes (61 minutes in total) and reduce the SOC from 30% to 20% (still above the 15% threshold where no more circuits are allowed). This would give you the hour of flight time, so yes, it is possible to fly for an hour after charging for an hour. However, the SOC is lower than when you started (20% instead of 30%) so the better answer is, “not quite.” The next incremental improvement in battery or related technology is expected to easily change the answer to “yes.”
The Velis Electro performed the 65 circuits reviewed above with a simplicity and consistency that should fit normal circuit training at flight schools. Future exercises will consider the impact of temperature on battery performance as the flights documented above were summer morning flights and we want to examine fall and winter operations as well.