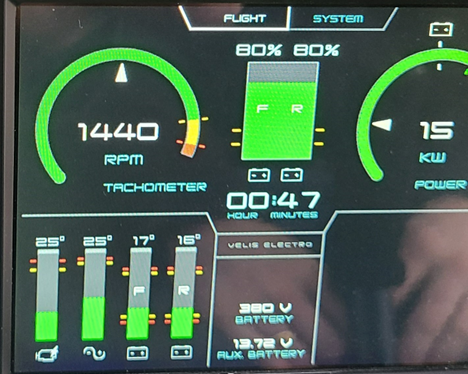
Image 1: Digital display shows four temperature graphs all in the green ‘normal’ zone.
Overheating and fire risk are two important concerns regarding electric aviation technology. Aircraft systems are designed with safety features and warning systems in mind to address these risks. So, what happens when you run charge/discharge cycles on a hot afternoon?
Temperatures on May 31st were forecast to soar above 30 °C, which offered the perfect opportunity to see how the e-plane and its cooling systems perform on a hot day. Lithium-ion batteries are sensitive to temperature, and over-heating has the potential to cause a fire, so we were especially interested to see how the Pipistrel systems handled hot conditions. The aircraft’s onboard data logger records many parameters including the temperatures of the batteries, inverter, and motor, and the outside air temperature (OAT) every 0.1 second. On May 31st, the OAT varied between 30-33 °C, near the maximum of 35 °C established in the Pilot Operating Handbook (POH). This would be a good contrast in temperature to our Day 2 ground runs, conducted on May 17th, a frosty morning with temperatures in the 6-9 °C range. We conducted our charge/discharge cycles on the black asphalt of the apron at the Waterloo-Wellington Flight Centre.
Day 3 of ground runs with the Pipistrel Velis Electro saw two additional University of Waterloo Aviation students join in. The new students were Anushka, a second year Geography and Aviation student, and Timothy, a first year Science and Aviation student. Each helped with the operations and practiced charging and discharging the battery in a simplified sequence of power settings.
The Velis Electro has two liquid cooling systems, one for the batteries and one for the motor and inverter. These cooling systems keep the motor, inverter and batteries within their respective operating temperature ranges. During charging, battery temperature is to remain between 0 and 45 °C. Temperatures were monitored during the charging phase (charger set to the maximum 20kW for fast charging on both days) and all temperatures remained well within limits (see graph 1).
Next, we wanted to see how the aircraft would perform during discharge. The aircraft was taxied to the run-up area and the motor run at a constant power to discharge the batteries. During discharge, the battery temperature must be kept between 0 and 58 °C. A warning message appears whenever any temperature enters the caution range (for the batteries, 51-57 °C). The graph of battery temperatures shows a consistent pattern of average battery temperature in the low 30s during the discharge sequence, closely matching the outside temperature. The battery temperature during the cooler May 17 ground runs was typically in the 15-18 °C range (see graph 2). In both cases, battery temperatures were slow to change even when sudden changes in power setting were made, an indication that the cooling systems were performing well. The clear message was that even with outside temperatures in the 30s, battery temperatures can be kept comfortably in the safe range, well below the 51 °C threshold for caution when the visual graph changes from green to orange.
The electric motor temperature is also measured so we compared its cycle on the hot day to that on the cool day. The motor temperature must be kept between -20 and 110 °C. In both cases, the temperature starts near the outside air temperature and then rises as the electric current powers the motor to spin the propeller. The higher the current, the steeper the rise in temperature as illustrated in the cool ground runs. As expected, the steepest rise in temperature was during the simulated climb with a power setting of 48 kW. When power levels returned to normal cruise settings, the motor temperature declined accordingly (see graph 3). Similarly, reducing the power to 15 kW resulted in a steeper decline in motor temperature. These cool day results were repeated during the hot day with a 30-kW cruise setting having a steeper temperature rise than the 25-kW power setting. During the 30-kW discharge, the motor temperature rose to 80 °C, but remained well below the caution threshold of 100 °C.
The inverter or power controller is the third major component of the powertrain. It converts the direct current (DC) from the batteries to the alternating current (AC) required by the motor. Its temperature is to stay between -20 and 70 °C. The temperature pattern during the cool day discharges was similar to that of the motor with a steeper increase observed during the high power setting of 48 kW, then a gradual decline when reduced to regular cruise power settings. Under these conditions, temperatures rose to over 40 °C, but remained well below the caution threshold of 65 °C. In contrast, on the hot day, the higher cruise power setting of 30 kW resulted in temperatures reaching the 65 °C threshold (see graph 4). Reducing the power setting from 30 kW to 20 kW caused a decline in inverter temperature away from the caution threshold. The illustration of warnings and caution messages in the POH (p. 237) depicts the scenario that was experienced during the hot afternoon ground run, with the gauges for battery and motor temperature remaining in their normal green ranges and the gauge for inverter/power controller temperature entering the caution range. The inverter temperature gauge also turns orange so that the pilot would notice and know to act.
The ground run trial demonstrated that the inverter caution temperature (65 °C) could be reached at a higher power setting (30 kW) on a hot afternoon (over 30 °C). The normal cruise power setting of 25 kW did not cause this threshold to be reached. This observation reinforces an important idea in electric aviation, higher current and power levels produce more heat so if you want to reduce temperatures, reduce the power setting. In addition, the ground run configuration meant that the cooling system did not benefit from the increased airflow that would have been going through the radiator if the plane were in flight, restricting its ability to cool the aircraft.
Overall, the ground run trials demonstrated that the cooling systems effectively keep the battery and motor temperatures within their normal ranges under hot conditions, even with suboptimal airflow.
The first component to reach its cautionary high temperature threshold was the inverter. This confirms the experience of pilots in hot locations such as California who report that the inverter is the first component to reach critical temperature thresholds. Equally important, the ground run trials also demonstrated that once a high temperature threshold is reached, a simple reduction in power will reduce the amount of heat being generated and bring temperatures back within normal operating ranges.
Pilots need to be alert and respond to cautions with appropriate action. In this case, reducing power (assuming that they can do so safely) is the best response when the digital temperature gauge goes from green to orange. Fly safe, use the information systems and take appropriate action.