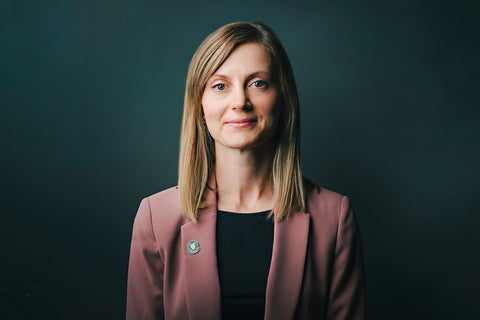
Dr. Mihaela Vlasea is helping build a new aviation industry, one airplane part at a time. A Waterloo Faculty of Engineering professor as well as an associate director of the Waterloo Institute for Sustainable Aeronautics, she’s a recognized expert in metal additive manufacturing — popularly known as 3D printing — and uses its wide ranging-technologies to fuse materials together to produce a vast array of new products for the aviation industry and beyond.
But just as what she creates in Waterloo’s Multi-Scale Additive Manufacturing (MSAM) Lab are complex pieces in a far larger puzzle being assembled by many hands, she’s one person, one part of a university-wide initiative laying the groundwork for an aviation sector that is truly sustainable — environmentally, economically, and socially. Indeed, as she explained in a recent interview, her vision for WISA and the industry itself can only be realized through this kind of co-operative, collegial venture.
“The ingredients for delivering solutions in sustainability often require multidisciplinary approaches,” she explains. “WISA plays an important role in bringing researchers together across multiple faculties to discover synergies in tackling problems under the aeronautics sustainability umbrella.”
As an example of how this works on the ground, Vlasea points to Waterloo’s newest ‘Research-for-Impact’ program. Its funding, she says, “invigorated projects across six faculties under social, environmental and economic sustainability pillars.”
Vlasea’s passionate about her work and the positive contribution the institute is making. She’s uniquely qualified for the associate director’s job, too. Between graduating from Waterloo with a Bachelor of Applied Science in Mechanical and Mechatronics Engineering in 2008 and a Doctorate in the same field in 2014, she made what turned out to be a highly appropriate move and received a Diploma in the Space Studies Program at International Space University, class of 2011 (Austria).
Although the MSAM lab, with more than $25-million worth of research infrastructure, is a separate entity from WISA, it’s partnering with the institute on several major initiatives. One project, for instance, deploys high-strength aluminum alloy powders that are produced by means of an inexpensive, environmentally-friendly micro-milling process to create light-weight, high-performance aerospace parts by using laser powder-bed infusion. Another project is working to produce aerospace components using a new class of titanium alloys that have been created in a low-cost process that generates no direct greenhouse gas emissions. Yet another initiative is developing sensors for assessing temperatures and strains in turbine-blade applications for the aviation sector.
“I am continuously impressed by the research portfolio that WISA had been able to engage with,” Vlasea says. “My research, focused on additive manufacturing, enables solutions that consider creative freedom in design topologies and architectural materials to enable products with superior performance. These capabilities are quite aligned with the aviation/aerospace sector and continue to be disruptive in this field.
“For instance, as part of the ‘Research-for-Impact,’ my research looks to contribute towards 3D printing of high-strength aluminum alloys and low-cost, high-performance titanium alloys to address the need for robust part production. Additionally, in collaboration with another faculty member leading the work, Dr. Armaghan Salehian, the research will reveal how to dampen noise and vibration using additively manufactured latticed architectures.”
It’s clear that this kind of advanced research will advance WISA’s stated goals of reducing, even eliminating, the harmful environmental impacts of aeronautics while supporting supply-chain resilience, cost efficiency and long-term economic growth. Even better, the parts Vlasea is making through metal additive manufacturing could end up outperforming what’s currently produced by more conventional methods. And as always, the work in her lab stands out as a highly visible part of WISA’s interdisciplinary approach that promotes diverse, equitable and inclusive workforces.
“The WISA team now has deep transparency into many different areas of research across campus and can create amazing networking opportunities among researchers and beyond towards industry partnerships, particularly through the Sustainable Aeronautics Summit,” she says. They’ve “brought to light numerous cross-collaborative research threads that will continue to be explored beyond the scope of the ‘Research-for-Impact’ pilot.
In talking to Vlasea, it’s obvious she’s just getting started with WISA. “I am excited to be part of this dynamic research environment,” she says, “and engage in promoting collaborative opportunities in the aviation sector, as well as to continue to understand the impact of my research field — additive manufacturing — towards sustainability.”