Concern details
Task description:
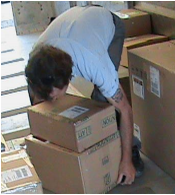
Figure 1a: worker unloading freight with automated conveyer
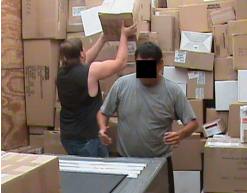
Figure 1b: worker loading freight into semi trailer with automated conveyer
Evaluation:
- Some of the population may not be able to perform because it exceeds tabulated strength capabilities.
- High back loads that that increase risk of injury.
- The weights exceed value outlined by Snook thus resulting in increased risk of injury.
- The packages are outside the recommended lifting zones.
- The high lifting frequency may induce fatigue.
-
Some of the population may not be able to perform because it exceeds strength capabilities.
Based on the biomechanical assessment of this job, less than 90 percent of the population has sufficient strength to lose load the trailers due the awkward postures and heavy loads. The workforce has strength limitations at the shoulder and elbows for lifts over 18 kg at vertical heights over 95 cm and back strength limitations when lifting 35 kg packages [1]. When forces exceed strength capabilities, it hinders an individual’s ability to perform the task, and the higher the portion of the population not capable of performing a task, the greater the risk of overexertion injury.
-
High back loads that exceed acceptable levels of which risk of injury increases.
The biomechanical human model revealed concern with high spinal loading for workers performing this job [1]. Retrieving or placing packages from the trailer results in high spine loads that increase the risk of injury for some of the population, specifically when lifting all package weights (1-35 kg) from off the floor as the shear force exceeds the Maximal Permissible Limit (MPL) as well as when lifting packages over 26 kg at a vertical height of 50 cm and 35 kg packages at a vertical height of 50 cm as the back compression exceeds the Action Limit (AL). The combined low back pain reporting index score for (un)loading the trailer indicates 56% of workers have increased chance of reporting low back pain from this job.
-
The weights exceed maximum acceptable weight limits.
According to well accepted manual handling guide (Liberty Mutual Tables, i.e. Snook Tables) [2], the package weights exceed the Maximum Acceptable Weight of Lift (MAWL). Due to the high frequency and awkward postures, the maximum acceptable weight of lift for this job is 5 kg for packages over shoulder height, 6 kg for packages between knuckle and shoulder height, and 7 kg for packages below knuckle height. Workers are three times more susceptible to injury if the job exceeds the MAWL.
-
The packages are outside the accepted lifting zones.
This job results in poor lifting conditions which are cause for concern as the location of the packages are outside the preferred lifting zone of 75 cm to 110 cm vertical height and horizontal reach of 40 cm (5th percentile female reach distance with elbow at side of body) [3].
-
The high lifting frequency may induce fatigue.
Furthermore, high frequency lifting tasks (≥ 15 lifts/min) result in fatigue if there is inadequate recovery time between lifts or lifting bouts [4, 5] as well as repetitive, awkward shoulder and back postures which are cause for concern [6]. Using a method proposed by the National Institute of Occupational Safety and Health in the USA to create a composite lifting index, unloading or loading the packages from the trailer at a frequency of 18 lifts per minutes results in a frequency multiplier of 0, which results in a composite lifting index score of infinity. A score of infinity suggests the work demands of the job exceeds physiological demands, and puts most of the workforce at increased risk of fatigue increasing the risk of injury. Note that at a lifting frequency of 11.7 lifts a minute, which is 65% of the actual frequency, the CLI is 6.5. A score above 1.0 indicates the job poses risk of injury for some of the workforce, and a score over 3.0 indicates high risk of injury to the majority of the population [7].
Countermeasures
In addition to improving the vertical heights of the packages, the lifting frequency is unacceptable and needs to be reduced to a quarter of the current frequency by slowing the conveyor and adding additional workers. Slowing the conveyor belt speed will reduce the speed at which the packages can be loaded onto it and thus not as many additional workers would be required. If the conveyor speed is not altered, four additional workers are required.
Even with the above modifications, the package weights still exceed the maximum acceptable weight of 9 kg at a frequency and improved vertical heights [2]. Since the majority of the packages exceed that weight, the use of a hoist or team lifting boxes over 9 kg is required to reduce the risk of injury. However, if the above countermeasures are not implemented, a hoist or team lift would be required for packages over 6 kg.
Risk factors | Countermeasures |
---|---|
Lifting packages are outside the accepted lifting zones | Eliminating the loose loading is required. This would involve loading the packages into crates/bins on lift tables (see illustrations). The full crates would be moved with forklifts and would be stacked in the trailer to optimise truck capacity. |
High lifting frequency | Reduce conveyor speed by half and add additional workers. |
Heavy loads | Vacuum hoist or team lifting boxes over 9 kg |
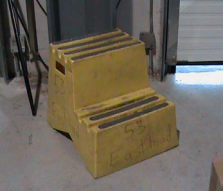
Figure 2: Step
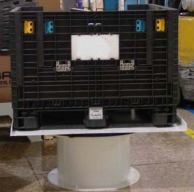
>Figure 3b: Bin raised on a rotate stand
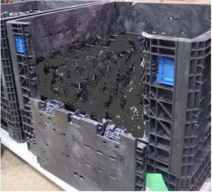
Figure 3a: Bin
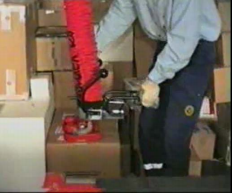
Figure 4: Vacuum hoist
References
- Norman, Wells, R., Neumann, P., Frank, J., Shannon, H., Kerr, M. (1998). A comparison of peak vs cumulative physical work exposure risk factors for the reporting of low back pain in the automotive industry. Clinical Biomechanics, 13(8):561-573.
- Snook, S.H. and Cirello, V.M. (1991). “The design of manual handling tasks: Revised tables for maximum acceptable weights and forces.” Ergonomics 34(9): 1197-1213.
- Pheasant, S. And Haslegrave, C. (2006). Bodyspace: Anthropometry, ergonomics, and the design of work, Taylor and Francis Group.
- Petrofsky, J., and Lind, A.R.(1978). “Metabolic, cardiovascular, and respiratory factors in the development of fatigue in lifting tasks.” Journal of Applied Physiology, 45: 64-68.
- Rodgers, S.H., (1997). “Chapter II-10: Work physiology – Fatigue and recovery.” In G. Salvendy (ed.), Handbook of Human Factors and Ergonomics (2nd Edition). New York: John Wiley and Sons, P. 268-297.
- Kilbom, A. (1994). Repetitive work of the upper extremity: Part II: The scientific basis for the guide. International Journal of Industrial Ergonomics, 14:59-86.
- Waters, T.R., Putz-Anderson, V., Garg, A., and Fine, L. J. (1994). “Revised NIOSH equation for the design and evaluation of manual lifting tasks.” Ergonomics 36: 749-776.