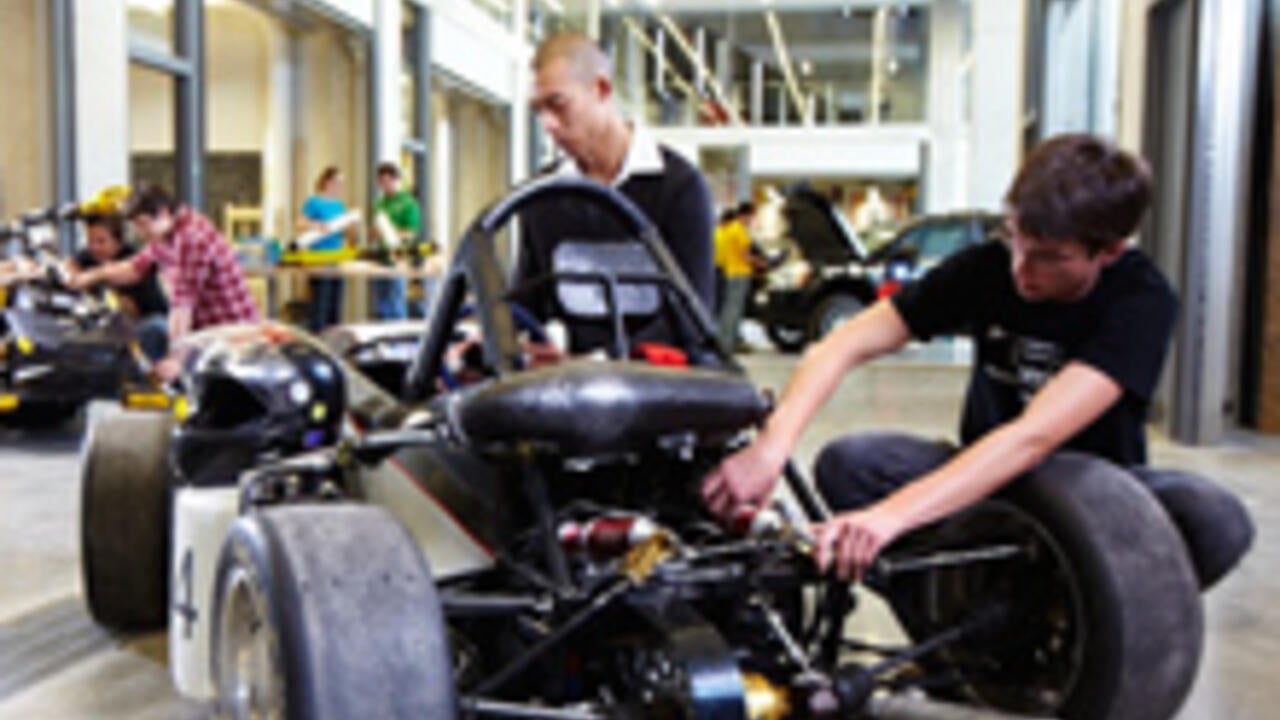
Waterloo research driving automotive innovation
In laboratories across the University of Waterloo campus, research into new fuels, smarter vehicles and lighter, safer materials is advancing the way we drive and what we drive.
In laboratories across the University of Waterloo campus, research into new fuels, smarter vehicles and lighter, safer materials is advancing the way we drive and what we drive.
By Christian Aagaard Communications & Public AffairsFor all its newness, the two-year-old Engineering 5 building on the University of Waterloo campus bears the whiff of old tech — the rubber and oil smell of an auto shop.
But here, and in the laboratories of the Engineering 2 and 3 buildings across the road, researchers advance the way we drive, and what we drive. The scope of their work includes electric cars, cars running on different fuels, cars containing new material, safer cars and cars that do some of the thinking for drivers.
That takes co-ordination, a role filled by WatCAR, the Waterloo Centre for Automotive Research.
“There is more automotive research done on this campus than at any other school in the country,” says managing director Ross McKenzie. “Ultimately WatCAR’s mandate is to profile and promote our competencies to industry and encourage them to engage in collaborative research.’’
What started out 10 years ago as informal group of mechanical engineering professors individually doing some automotive research has grown into WatCAR, the umbrella organization for 125 researchers collaborating across all six university Faculties. Eight automotive student teams with service bays in Engineering 5 apply what they learn to experimental vehicles ranging from hybrid cars to robot rovers.
Take some straw….
Today, WatCAR has research and co-op education relationships with parts companies and all five automakers in Ontario — Ford, Chrysler, General Motors, Honda and Toyota.
A stalk of wheat straw helps tell the story about the connections that occur under WatCAR.
Leonardo Simon worked with A. Schulman, a U.S.-based resin-and-plastics compounder to solve a problem with blending straw and plastic to make lighter, stronger auto parts. An associate professor in Waterloo’s Department of Chemical Engineering, Simon developed pellets of the size and consistency needed to meet the moulding standards A. Schulman set.
They took the results to Ford. Eighteen months later, owners of new cars were using armrest storage bins of wheat straw plastic made with Waterloo innovation.
McKenzie says that’s a fast turn-around, aided by a university culture in which researchers are encouraged to be entrepreneurial and own their discoveries.
“One of our big advantages under WatCAR is that we can work to rapid automotive industry timelines,” McKenzie said. “We are able to be nimble because of our unique (intellectual property) policy.’’
Read more
3D printing technology is perfect fit with new Waterloo Institute for Sustainable Aeronautics
Read more
Waterloo lab helps fill industry demand for additive manufacturing skills
Read more
Combining machine learning techniques with real-world scenarios to combat forest fires
The University of Waterloo acknowledges that much of our work takes place on the traditional territory of the Neutral, Anishinaabeg, and Haudenosaunee peoples. Our main campus is situated on the Haldimand Tract, the land granted to the Six Nations that includes six miles on each side of the Grand River. Our active work toward reconciliation takes place across our campuses through research, learning, teaching, and community building, and is co-ordinated within the Office of Indigenous Relations.