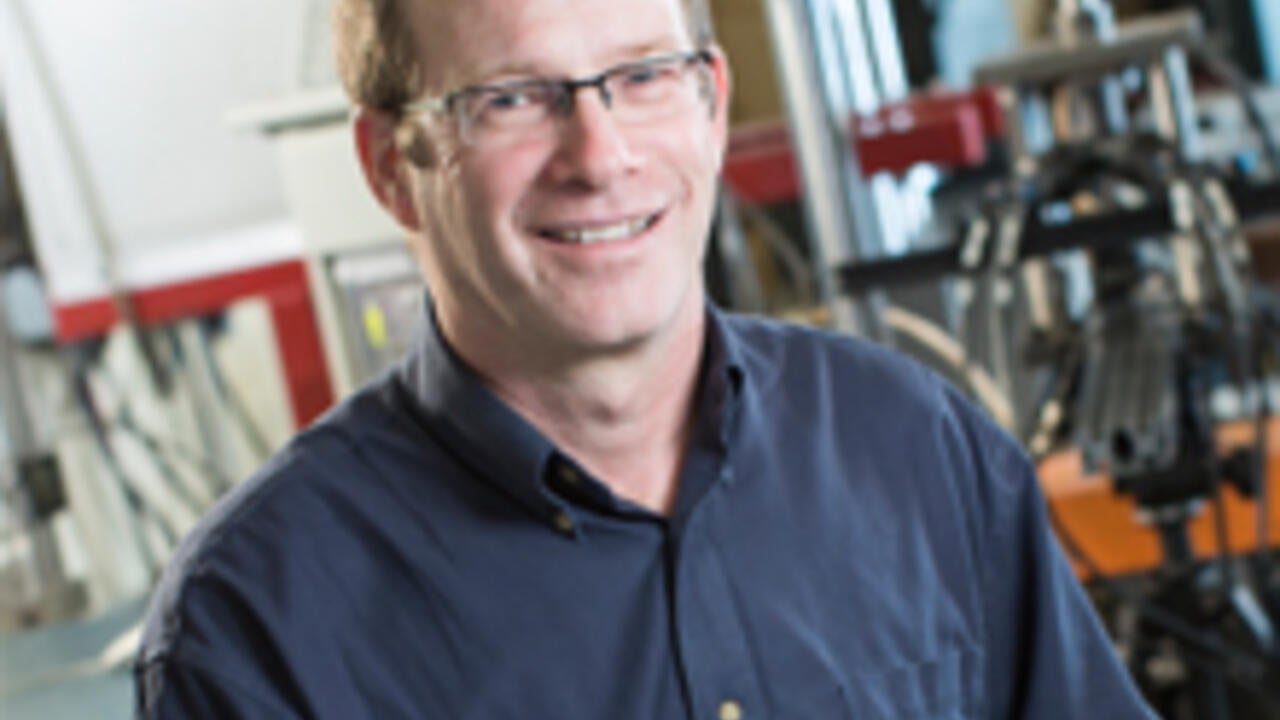
Crunch time: Team's research puts auto industry on weight-loss plan
In Michael Worswick’s automotive research lab, metal and other materials are put to the test, to measure how much stress, tension, pressure and strain they can take.
In Michael Worswick’s automotive research lab, metal and other materials are put to the test, to measure how much stress, tension, pressure and strain they can take.
In Michael Worswick’s automotive research lab, metal and other materials are put to the test, to measure how much stress, tension, pressure and strain they can take.
A professor and Canada Research Chair in the University of Waterloo’s Department of Mechanical and Mechatronics Engineering, Worswick leads a research team that punishes metal and other materials en route to a lighter, safer automobile.
“We deal with the issues that arise when light-weight materials are introduced into car bodies and structures,” says Worswick, who heads the Forming and Impact Mechanics ResearchTeam.
The team welcomes two new and hefty members in October — a 1,400-kilogram payload crash sled and a 75,000-kilo, two-storey forming press. Last March, Automotive Partnership Canada and the Ontario Research Fund awarded $4.1 million to help pay for the equipment and support the research of 18 researchers for three years. An additional $2.6 million from the Canada Foundation for Innovation and Ontario Research Fund will fund the press and lab expansion.
A sled, but no sleigh bells
Mounted on a rail, the sled will plow into full-sized components made by the press — the side framing of a car, for example — and provide the team with information about the crash-worthiness of materials.
Crash-worthy, when it comes to keeping people safe, refers to the ability of a component to absorb crash energy and dissipate it away from the occupants. A Transport Canada study based on 2004 statistics estimated the social cost of a fatality in a traffic crash in Ontario was $13.6 million.
High-strength steel, magnesium and aluminum make up the team’s primary materials. With auto-industry partners, researchers collaborating across a wide spectrum of disciplines experiment with new methods of forming metals into lightweight components while minimizing the loss in strength.
Samples are pounded or stretched, cooled or heated, sometimes under the eye of cameras shooting at 100,000 frames per second.
Government policy, meanwhile, urges the research along. U.S automakers must meet a 35.5 mpg (15.1 kms/litre) fuel efficiency standard by 2016; 54.5 mpg (23 kms/litre) by 2025. Canadian standards are expected to match.
But it’s not all about saving gas. Research by the impact mechanics team is just as important to advances in electric and hybrid vehicles.
Whether it’s fuel cells or batteries, weight reduction is a key enabler,’’ Worswick says.
Read more
3D printing technology is perfect fit with new Waterloo Institute for Sustainable Aeronautics
Read more
Waterloo lab helps fill industry demand for additive manufacturing skills
Read more
Combining machine learning techniques with real-world scenarios to combat forest fires
The University of Waterloo acknowledges that much of our work takes place on the traditional territory of the Neutral, Anishinaabeg, and Haudenosaunee peoples. Our main campus is situated on the Haldimand Tract, the land granted to the Six Nations that includes six miles on each side of the Grand River. Our active work toward reconciliation takes place across our campuses through research, learning, teaching, and community building, and is co-ordinated within the Office of Indigenous Relations.