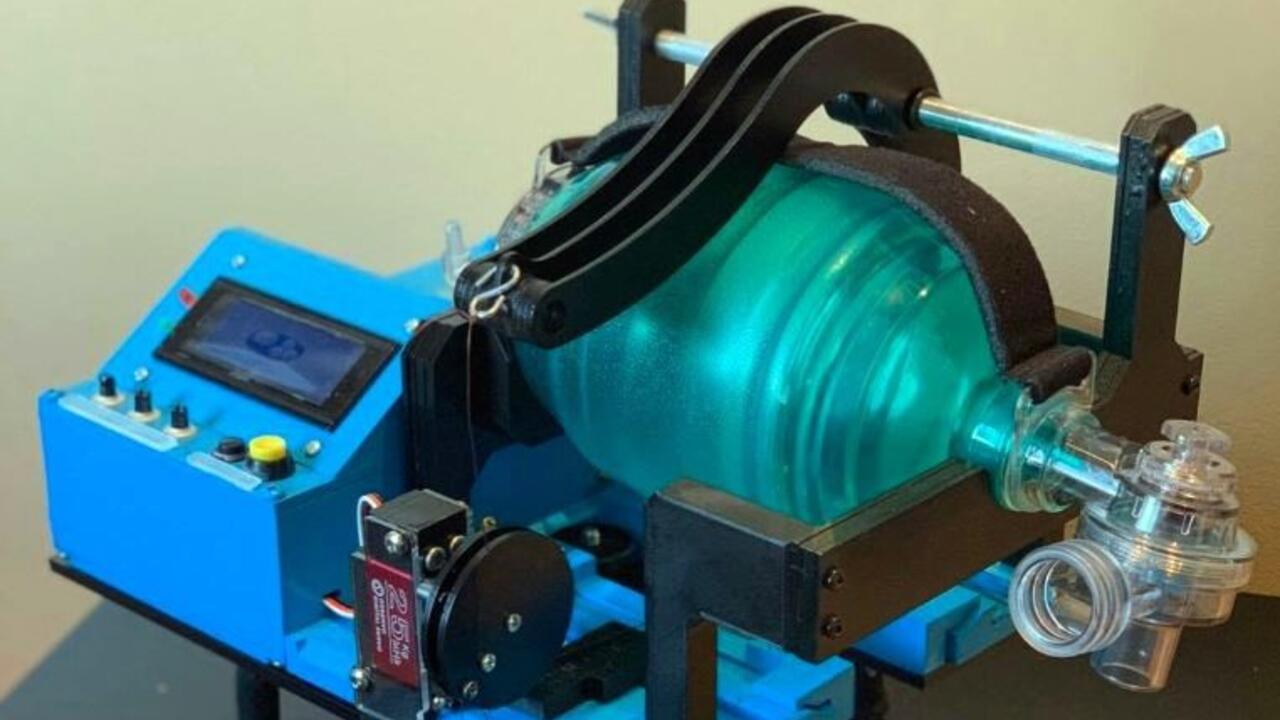
Students build ventilator that could be used for COVID-19 response
Engineering students are looking for help from academics and industry to refine and produce their low-cost, portable ventilator
Engineering students are looking for help from academics and industry to refine and produce their low-cost, portable ventilator
By Brian Caldwell Faculty of EngineeringIt began as a few words on a sticky note while a team of engineering students at the University of Waterloo brainstormed ideas for their fourth-year design project.
Now, little more than six months later, the students have a working prototype of a portable, low-cost ventilator they hope could soon help save lives on the front lines of the COVID-19 crisis.
“It’s a total fluke, but our project couldn’t be any more relevant than it is today,” says Connor Simmons, one of four team members from the mechatronics and mechanical engineering programs.
The device they designed and built for just over $200 - dubbed AIR for Automated Inhalation Resuscitator- was intended to replace breathing equipment now manually operated by paramedics at emergencies.
Team members (from l-r): Brian Mao, Connor Simmons, Aditya Matam and Sam Raisbeck
But as the coronavirus pandemic gathered steam, eventually forcing the cancellation of their Capstone Design symposium last month, the students realized they had something with even more potential.
“We were obviously very disappointed because we didn’t get to show off our product,” says Simmons, who is working with Sam Raisbeck, Brian Mao and Aditya Matam.
“Then we started seeing stories about hospitals getting overwhelmed and people running out of ventilators. That’s when it dawned on us that our product is actually an inexpensive ventilator.”
Operated by a small motor, AIR uses special arms to automatically squeeze a self-inflating bag to send air through a mask, or an intubation tube, and into a patient’s lungs.
Controls allow the breathing rate, air volume and air pressure to be adjusted, and the device is designed for use on adults, children and infants.
Team members believe its low cost and simplicity make it best suited for emergency use in the developed world, or as a stand-in for full-scale ventilators in areas of the developing world with limited access to them.
In an effort to get them into the hands of medical professionals quickly, the team has made design information freely available online and is asking for help from academics and potential industry partners to test, refine and produce them.
“We think the cost of our product and the speed with which it could be manufactured are huge advantages,” Simmons says.
“A lot of people are now scrambling to design cheap ventilators because of the shortage, but by sheer coincidence we already have more time invested in ours than any other design we’ve seen.”
The project was inspired by a close friend and paramedic who told Simmons that manually helping patients breathe using a bag valve mask is a lot harder than it looks in the movies.
It has already benefited from testing at a laboratory at Conestoga College in Kitchener, where there is a respiratory therapy program, and input from health-care workers at the Hospital for Sick Children in Toronto.
“Our hope is that our device can make a difference as soon as possible, but we definitely need help to get it out there,” says Simmons.
Read more
Waterloo’s MSAM Lab is increasing capacity for research, training and partnerships to meet growing demands in the field of advanced manufacturing
Read more
Experts from the Waterloo Institute for Sustainable Aeronautics want solar panels to power airports safely
Read more
How transmission electron microscopy is now pushing the frontiers of research at the University of Waterloo
The University of Waterloo acknowledges that much of our work takes place on the traditional territory of the Neutral, Anishinaabeg, and Haudenosaunee peoples. Our main campus is situated on the Haldimand Tract, the land granted to the Six Nations that includes six miles on each side of the Grand River. Our active work toward reconciliation takes place across our campuses through research, learning, teaching, and community building, and is co-ordinated within the Office of Indigenous Relations.