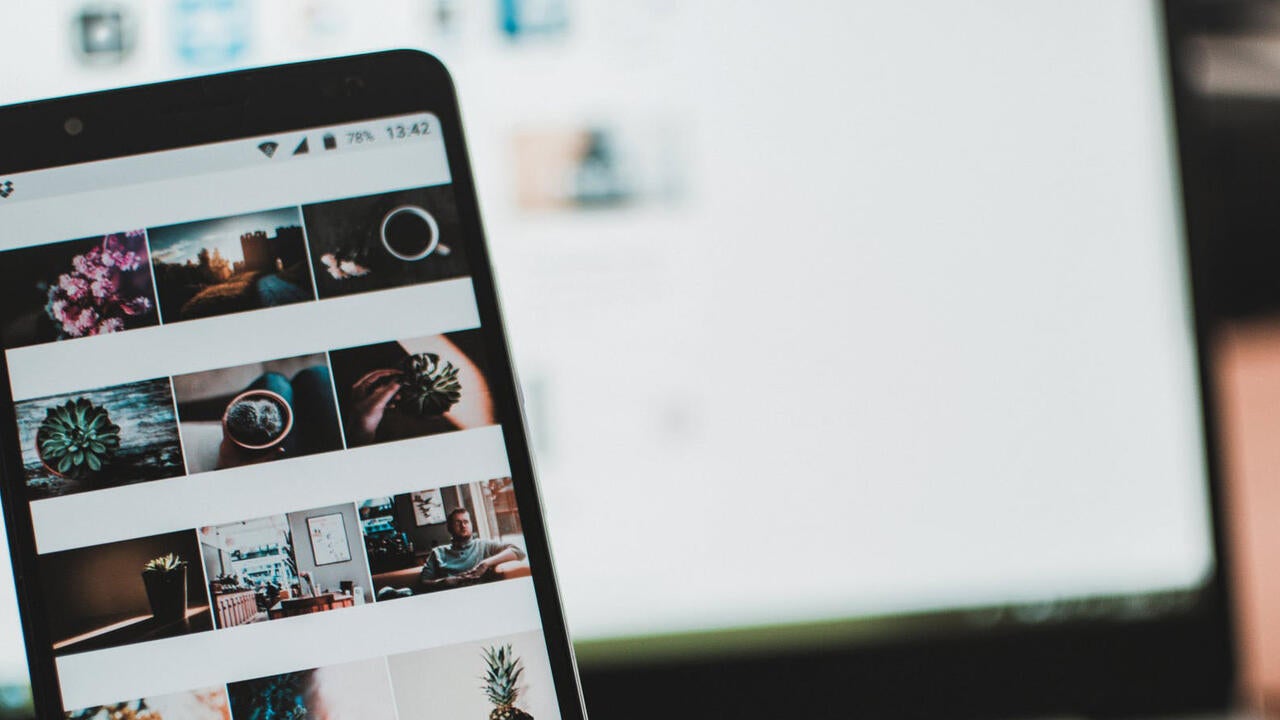
Flexible displays may finally be within reach
The next stage are electronic devices that act much more like paper and can be folded, rolled up or even crumpled up in a ball
The next stage are electronic devices that act much more like paper and can be folded, rolled up or even crumpled up in a ball
By Shane Schick Faculty of EngineeringFirst came the laptop, which we could close by folding down the screen. Then came smartphones and tablets, which fit into many pockets and bags. The next stage, according to Elahe Jabari, are electronic devices that act much more like paper and can be folded, rolled up or even crumpled up in a ball, potentially changing what we mean when we describe technology as “portable.”
Jabari, a Waterloo engineering Ph.D student who will complete her studies in the Fall 2015, has spent the last several years trying to develop the raw materials that would allow these malleable electronic components to be created. She’s combining a substance known as graphene with the next generation of manufacturing processes, 3D printing, to make it happen. The results could become the first step in delivering on the promise of flexible screens that have been discussed in the IT industry for at least a decade.
A form of two-dimensional hexagonal carbon, graphene was first discovered just over 10 years ago and has been considered for a variety of purposes, including biological engineering. Jabari, however, says its conductive and flexible properties make it an ideal candidate for a special kind of ink that would be used in a 3D printer to make flexible displays.
“I am so excited about this material,” she says. “At first we weren’t sure if we could print graphene with the aerosol-jet additive manufacturing system. Nobody else had done it before. We had to start from scratch.”
Developing highly concentrated graphene ink compatible with our additive manufacturing system took a year and a half, Jabari says. The ink has been successfully used to print the smallest ever printed graphene patterns that demonstrate the material’s and additive manufacturing systems’s potential. More recently, Jabari published a paper describing her research, ‘Micro-scale aerosol-jet printing of graphene interconnects,’ in the scientific journal Carbon, along with her instructor Dr. Ehsan Toyserkani in Mechanical Engineering.
Continuing in her engineering research, Jabari, has also developed a laser post processing protocol to locally treat printed graphene patterns, which is preferable for flexible electronics with low working temperature substrates. She is currently working on mechanical characterization of these printed electronics.
Having come to Canada after earning her B.A. and Masters degree in her native Iran, Jabari says one of the benefits of enrolling in the University of Waterloo’s Engineering program was the autonomy and resources to pursue a complex challenge.
“The best thing about my program is I felt so free to decide what I wanted to do,” she says, adding that the collaborative culture of her peers in the program has been a huge contributor to her success.
“I had access to many labs — in making this material, using just one lab wasn’t enough. There were many facilities required to do that,” she says. “I needed lots of equipment. My supervisor was also a great support throughout the research work.”
Following graduation, Jabari hopes to commercialize her work through the Multi-scale additive manufacturing lab site. Once that happens, we might see people interact with technology in entirely new ways. Just as the first generation of touch screens caused people to “pinch and zoom” to manipulate digital objects, flexible displays could become the basis for new wearable devices and much more.
“People are still carrying around large tablets, large cell phones or cracked cell phones — flexible displays could change all of that.”
Read more
Waterloo researchers develop techniques modelled on the human brain to improve how self-driving cars work
Read more
Waterloo welcomes emerging postdoctoral scholars to receive funding from Provost fellowship programs
Read more
Innovative device could power electronics with your body movements while you use them
Read
Engineering stories
Visit
Waterloo Engineering home
Contact
Waterloo Engineering
The University of Waterloo acknowledges that much of our work takes place on the traditional territory of the Neutral, Anishinaabeg, and Haudenosaunee peoples. Our main campus is situated on the Haldimand Tract, the land granted to the Six Nations that includes six miles on each side of the Grand River. Our active work toward reconciliation takes place across our campuses through research, learning, teaching, and community building, and is co-ordinated within the Office of Indigenous Relations.