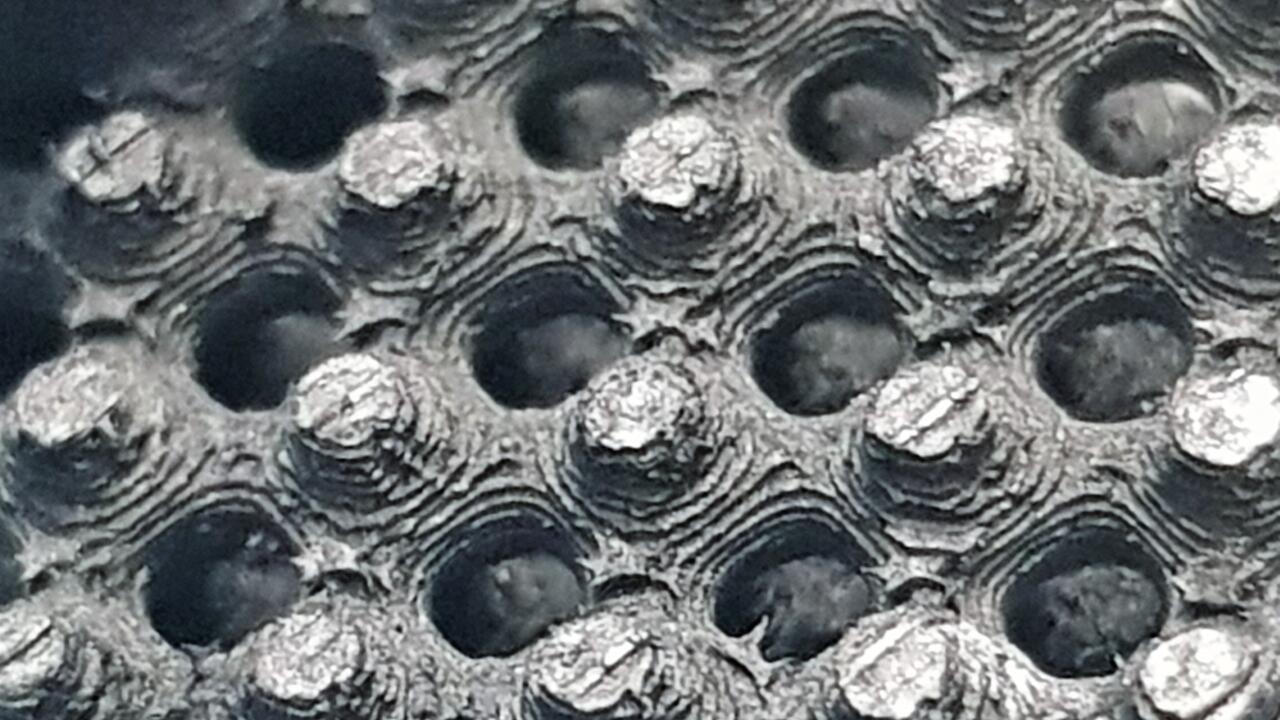
Sensing a breakthrough in wearable tech
Tough, flexible material created by researchers at Waterloo Engineering enables monitoring of everything from heart rate to athletic performance
Tough, flexible material created by researchers at Waterloo Engineering enables monitoring of everything from heart rate to athletic performance
By Brian Caldwell Faculty of EngineeringResearchers at Waterloo Engineering have utilized 3D printing and nanotechnology to create a durable, flexible sensor for wearable devices to monitor everything from vital signs to athletic performance.
The new technology combines silicone rubber with ultra-thin layers of graphene in a material ideal for making wristbands or insoles in running shoes.
PhD student Elham Davoodi led a project to develop a new sensing material using nanotechnology and 3D printing.
When that rubber material bends or moves, electrical signals are created by the highly conductive, nanoscale graphene embedded within its engineered honeycomb structure.
“Silicone gives us the flexibility and durability required for biomonitoring applications, and the added, embedded graphene makes it an effective sensor,” says Ehsan Toyserkani, research director at the Multi-Scale Additive Manufacturing (MSAM) Lab. “It’s all together in a single part.”
Fabricating a silicone rubber structure with such complex internal features is only possible using state-of-the-art 3D printing – also known as additive manufacturing - equipment and processes.
The rubber-graphene material is extremely flexible and durable in addition to highly conductive.
A close-up shows the honeycomb structure of a new sensing material invented by researchers.
“It can be used in the harshest environments, in extreme temperatures and humidity,” says Elham Davoodi, an engineering PhD student who led the project. “It could even withstand being washed with your laundry.”
The material and the 3D printing process enable custom-made devices to precisely fit the body shapes of users, while also improving comfort compared to existing wearable devices and reducing manufacturing costs due to simplicity.
Toyserkani, a professor of mechanical and mechatronics engineering, says the rubber-graphene sensor can be paired with electronic components to make wearable devices that record heart and breathing rates, register the forces exerted when athletes run, allow doctors to remotely monitor patients and numerous other potential applications.
Researchers from the University of California, Los Angeles and the University of British Columbia collaborated on the project.
The latest in a series of papers on the research, 3D-Printed Ultra-Robust Surface-Doped Porous Silicone Sensors for Wearable Biomonitoring, appears in the journal ACS Nano.
Read more
The stuff that gives cards, ornaments and decorations a holiday lustre does more than just gets everywhere
Read more
Funding supports a range of projects from sustainable 3D printed materials to 6G network innovations and improving the electric automotive industry
Read more
New AI-powered tech counts calorie and nutrient intake while people eat to help them live healthier, happier and longer lives
Read
Engineering stories
Visit
Waterloo Engineering home
Contact
Waterloo Engineering
The University of Waterloo acknowledges that much of our work takes place on the traditional territory of the Neutral, Anishinaabeg, and Haudenosaunee peoples. Our main campus is situated on the Haldimand Tract, the land granted to the Six Nations that includes six miles on each side of the Grand River. Our active work toward reconciliation takes place across our campuses through research, learning, teaching, and community building, and is co-ordinated within the Office of Indigenous Relations.