Designs of current horizontal axis wind turbine (HAWT) blade tips vary depending on the scale but are for the most part simple shapes within the blade plane. The conventional shapes are popular due to their proven track records and ease of manufacture. Simple alterations to the standard tip have been found to produce desirable results in relation to bending load elevation, whereas out of plane shapes, such as the endplate and winglet, can apparently augment the power output. It has also been suggested that alternative tip shapes can reduce aerodynamic blade noise. With the facilities available at the University of Waterloo, it was decided to pursue research that explored the effect of various blade tip designs on the performance of a wind turbine.
Design and Fabrication of a Interchangeable Tip Wind Turbine Blade
A wind turbine blade is defined by a blended distribution of cross-sectional blade stations. Each station has a shape known as the airfoil, a size defined by the chord length, and an orientaion defined by the twist.The airfoils selected were the S83X series, which were designed specifically for wind turbines of 1 to 3 m blade length.
The blade geometry (chord and twist distributions) was optimized using the National Renewable Energy Laboratory(NREL) PROPID design code and codes developed in-house. This code is widely used in wind turbine blade design.
The specifications of the wind generation facility and test rig dictated the remaining design parameters. Due to these specifications, the blade length is 1.6m, the design wind speed is 6.5 m/s, and the operational rotor speed is 200 rpm.
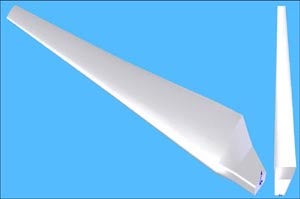
A solid model of the resulting optimized blade can be seen in Figure 1.
The final phase of the design was the exchangeable tip. To accomplish this a three pin cam lock system was chosen (Figure 2). This allows the outer 10% of the blade to be exchanged.
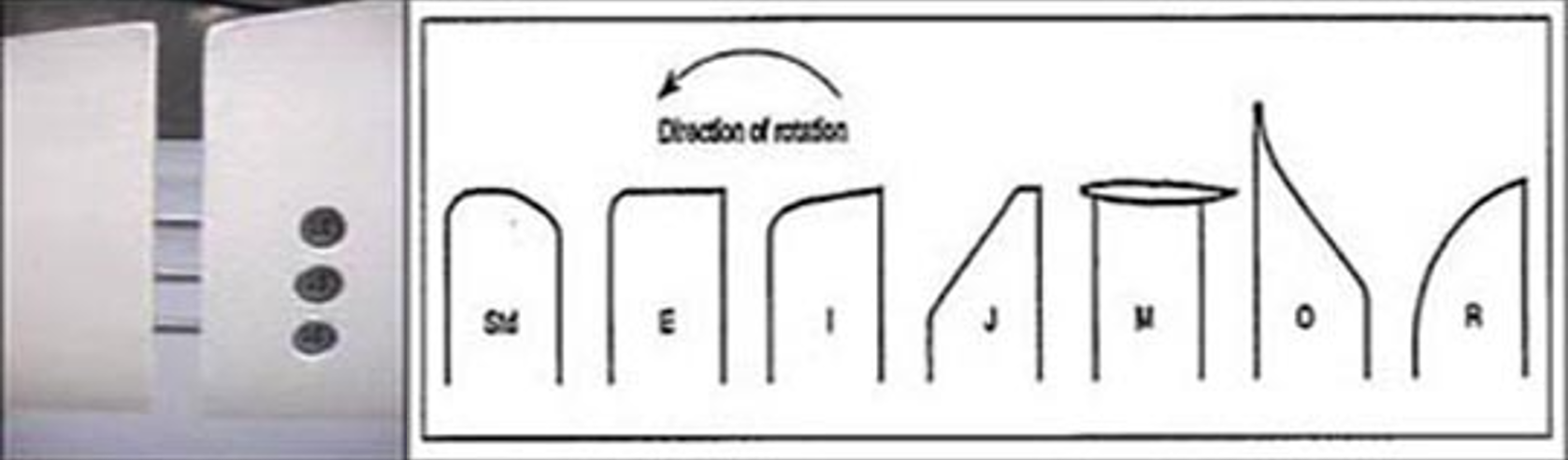
Different tips (Figure 3) are machined out of maple using a CNC mill, after which they are painted to achieve the same surface finish as the blade.
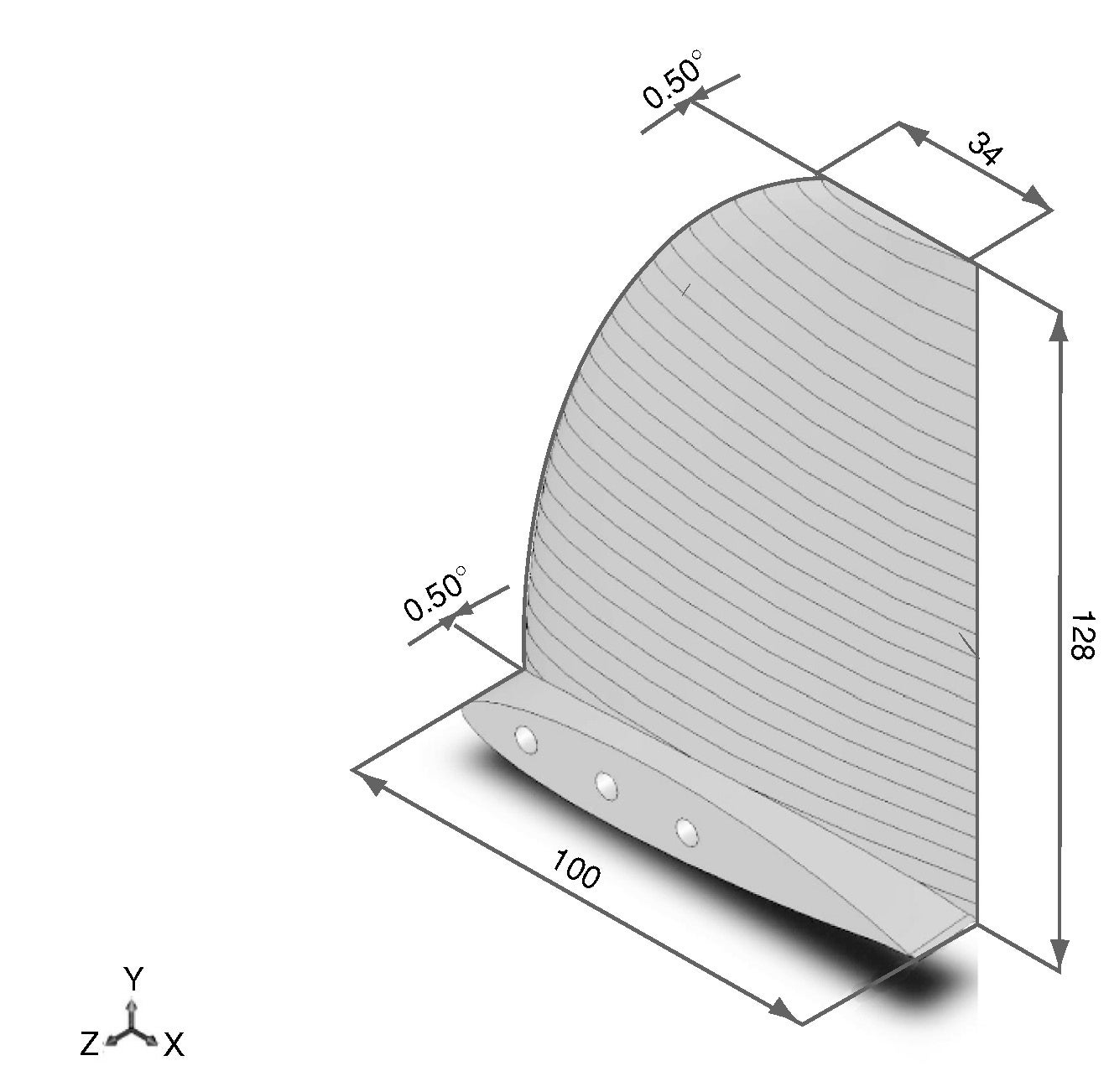
A sample of the winglet design used in this study.
Results
The effects of two different winglets were quantified by repeating the test that was executed with the standard tip for each winglet. Both winglets were found to have a bell-shaped power augmentation profile, with a broad peak between 6.5 m/s and 9.5 m/s where power was increased by 5% to 7%. These power augmentation figures matched closely with the findings in the literature that suggested increases of 2% to 8% are possible. It was noted based on flow visualization, power augmentation values and previous studies, however, that these designs are certainly not optimal and it is possible that an optimized winglet design could be attained through further modeling and testing. See research publications for more information. New winglet designs have been evaluate to determine effects of design parameters such as angle settings.
Future Work
More in depth research will be conducted to explore the effect of winglet designs on rotor performance.