Power Production and Flow visualization Experiments in a Controlled Environment
Abstract
Performance Characterization and detailed aerodynamic analysis of a three bladed 4m diameter wind turbine has been completed. This turbine was custom designed and built to be used within a large scale indoor University of Waterloo operated wind facility. Laser based imaging techniques were used to determine the flow over the blades for a range of tip speed ratios typical of commericial turbines.
Power production tests covered a range of mean wind speeds to 11m/s and rotational rates to 220 rpm. This allowed the power production to be determined as a function of wind speed, as traditionally found in power curves for commercial turbines, and the Cp as a function of the tip speed ratio. Peak power curves for commercial turbines, and the Cp as a function of the tip speed ratio. Peak power was found to be 3080 W with a Cp of 0.4.
Laser based imaging was used to produce velocity maps of the chord-wise air flow over an area near the tip of a blade. This testing is unique as it presents large scale flow results in an unbounded external flow on a rotating turbine.
PIV Method
In order to get an instantaneous measurement of the velocity around the airfoil a noninvasive technique called Particle Imaging Velocimetry(PIV) was utilized. This process captures two images very close together, typically on the order of micro-seconds. In order to visualize the flow water-based small particles were added to the flow. Since this technique does not require a probe the flow remained undisturbed as the measurements were taken.
The velocity field was then calculated by using a correlation techinique to determine on average, the direction the smoke particles are travelling and their speed.
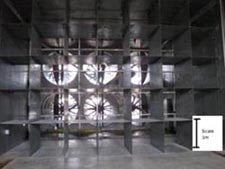
Experimental Setup
Wind Facility
- 8.0 m wide by 5.9 m tall outlet (shown in Figure 1).
- Six 100 hp variable frequency drives used to drive airflow.
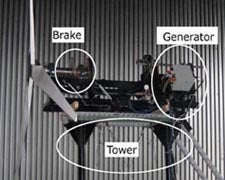
Turbine Apparatus(shown in Figure 2)
- 4 m diameter rotor
- 3 m tall tower structure
- DC Motor/Generator
- Resistor load bank
Results
The results for this experiments are divided into two areas of study: power generation and blade flow characterization.
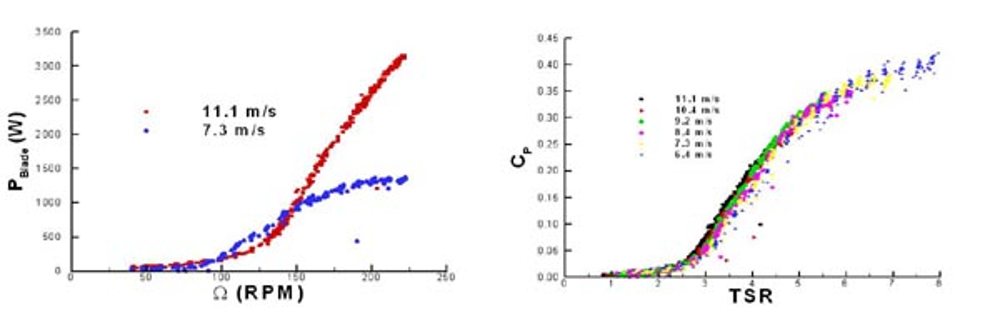
The coefficient of power could then be calculated over the range of TSRs covered during each test. The raw results, shown in figure 4, for the range of wind speeds between 6.4m/s and 11.1m/s and rotational rates between 40 rpm and 220 rpm collapse down onto one curve as expected. These raw results represent the individual data points collected during the tests, not the meanm and have only had five outliers removed, out of approximately 2400 total data points.
Based on the PIV process, raw image(Figure 5) are converted into velocity plots which are translated into a frame of refernce relative to the blade.
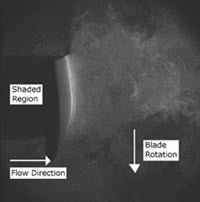
Conclusions
Power Generation:
- Unique ability to vary both incoming wind speed and the rotational rate to test over range of TSRs
- Raw power output peaked at 3080 W at a wind speed of 11.1m/s
- Cp approaching 0.4
PIV concept used successfully to produce velocity flow field around rotting blade.