Introduction
Description of tarping methods and required forces
Manual tarping
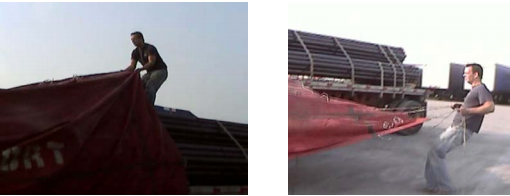
Figure 1a and 1b
Tarping and untarping using a rack-and-tarp kit
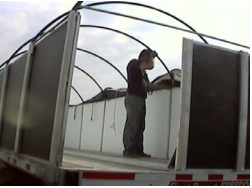
Figure 2
Tarping and untarping using sliders
A sliders tarping system consists of a tarp attached to a frame and rail system that is dedicated to that flatbed trailer. When a load is either picked up or delivered, the sliders system must be untarped and then retarped. This system is operated from the ground. To untarp the sliders system, a driver disconnects the buckles connecting the flaps at the back of the trailer, opens up the back flaps, and pulls apart the Velcro at the bottom of the back flap. Then the driver obtains a long handle crank from the slots under the trailer, connects it into the bottom of the back flap, and then uses it to roll up the back flap until it is over the top of the slider trailer. Once the back flap is rolled over the top, the handle end of the long crank is attached with the corner flap. A small handle crank is then used to disengage the rear inner braces. The driver then pushes the slider open towards the headboard. The main forces for the sliders method was pushing or pulling the tarp system open or closed and these forces ranged from 107 – 235 N. Typically one hand is used to push or pull the slider system at a vertical hand height of approximately 140 cm. The forces in the upper range exceed the strength capabilities for one- handed maximum horizontal pull force with dominant hand, 147 N for males and 98 N for females [4] as well as the one-handed horizontal female pull strength capabilities of 61 N [10]. If the slider tarp gets jammed in the rails, due to a poorly maintained system or due to ice and snow, the driver may have to go back and forth to both sides of the trailer to push the slider from both sides of the trailer. Next a winch bar is obtained and used to unwind the ratchet locking mechanisms at each of the front corners. Then the front slats are disengaged and the slider is pushed towards the rear of the trailer. To retarp a slider tarping system, the untarping sequence is retraced (Figure 3). Overall this system prevents the driver from having to climb on the trailer and reduces tarping and untarping time to approximately 10 minutes (if no difficulties are encountered).
Although the slider method initially appeared easier, it also resulted in high peak back loads and peak muscle activity. This is mainly due to the asymmetrical high forces required to pull or push the slider. Participants were required to pull or push the unit with one hand and as a result this torque increased spinal compression and low back activity. This method, however, required less time and resulted in lower cumulative exposure.
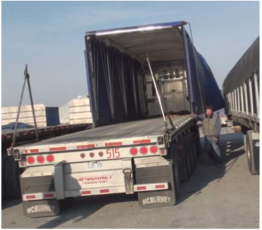
Figure 3
Comparison of tarping methods
Strength capabilities
All three tarping methods had job elements which exceed published strength capabilities and force guidelines. Some tarping tasks may limit the number of workers who are able to perform the job and may increase risk of injury. Overall, the forces during manual tarping and untarping were the highest and exceeded strength capabilities much more than rack and tarp and sliders. Feedback from the company indicated that they are trying to widen their pool of drivers but their current hiring is limited by the high strength demands of the tasks.
Risk of musculoskeletal disorder
Manual tarping and untarping results in the greatest back exposure based on the greater amount of time with high back loads, greater duration of time in severe back flexion, greater cumulative back loads, and higher back muscle activity. This greater amount of back flexion is expected for this method as the vertical working range for tarping a load on a flatbed trailer is from ground level to approximately 160 cm, depending on the load size and techniques used, whereas the other two methods do not typically require work below 100 cm. Overall, the manual tarping method has the greatest risk of back injury due to higher forces, the peak and cumulative loading, and the time in awkward back postures. In addition, there was also high loading on the upper extremity during manual tarping and untarping.
The rack and tarp kit method involved more overheard work as represented by the time in severe shoulder flexion for right and left shoulders. This greater shoulder flexion was consistent with the greater trapezius activation during this tarping method. Thus, the rack and tarp method results in greater risk of shoulder injury.
Even though the slider method had peak loads which were not significantly lower than the other tarping methods, this method required less time and resulted in lower cumulative exposure, including less time exertingforces, less time in awkward shoulder and back postures, and lower cumulative back and shoulder loads. Thus, the sliders method results in the lowest risk of injury.
Workload (heart rate)
Based on the heart rate values, all three tarping methods are demanding jobs. The average heart rate of all three tarping methods was in the “high workload” category. In addition, the heart rates during the tarping methods ranged from 81.3% to 95.8% (average 93%) percent of the participants’ age-predicted maximum heart rate. Based on the heart rate results, the sliders method is preferred because it resulted in a lower average heart rate, lower percentage of maximum predicted heart rate and less time in the high workload or greater.
Working at heights
Tarping a load using a standard tarp and rack and tarp kit requires drivers to climb on the trailer and load, whereas the sliders tarping method minimizes or eliminates the need to climb on the load and flatbed trailer. Working from the trailer or on top of the load, poses inherent safety risks as there is risk of falls from elevation which is increased due to slippery, uneven surfaces and trip hazards.
Injuries from falls from trailers and getting on and off the trailer is a prominent concern in the transportation sector [11, 12] as a standard flatbed trailer is 122 – 137 cm off the ground [13] and the load can be up to 4 meters high. A study that analyzed injury claims of the fall from trucks as recorded in the database of the Ontario Workplace Safety and Insurance Board (WSIB) for the year 1997 identified 352 claims which involved a fall that occurred from a truck, trailer or the cargo, and the costs associated with the 352 claims were over 5 million dollars [12]. Of these cases, 50 percent were falls from the back or side of the trailer. In Ontario, the industrial regulations, O. Reg. 851 s. 85 requires fall protection for any worker working at heights three meters or greater. In the United States, Occupational Safety and Health Administration (OSHA) regulations require fall protection for workers over 1.83 meters. Flatbed truck drivers who tarp loads are frequently required to climb on the trailer and load. Drivers often climb on the load without adequate fall protection as the site or customer often does not have a fall arrest system provided for tarping or the different trailer and load geometry do not permit it [14]. Additionally, workers are very susceptible to environmental conditions while completing these tasks because weather, such as wind, rain, cold and snow, plays a huge role in increasing the difficulty of the job.
Getting onto a standard flatbed trailer is difficult, and it poses a hazard because the trailer has few, if any, handholds, inadequate steps, and slippery surfaces. Although the use of three-point contact during climbing is advocated in the transportation industry training, it is often not possible when climbing on flatbed trailers or loads due to lack of adequate handholds and steps. Getting onto the flatbed trailer is often done by climbing on the Interstate Commerce Commission (ICC) bar, which is not an adequate step as it was designed to prevent vehicles from going under the trailer in a rear-end collision [13], or from around the headboard, or over a tire. Similarly, getting onto the load is also difficult and has inherent hazards since the load typically does not have any handholds or steps and may be uneven and slippery.
Whereas, getting off the load and trailer is often achieved by drivers jumping down because it is the quickest means to get down and there is no method incorporated to safely get off using three-point contact. In this tarping study, the participants jumped off the trailer to the ground 58% of the time and jumped off the load down to the trailer 75% of the time. This concern is also apparent for exiting truck cabs as drivers tend to jump from the first or second of step of the tractor [15, 16]. Jumping from elevated surfaces creates high impact forces which transfer high loads to the joints and also increases the potential of slips and falls immediately after landing. Jumping from the cab seat level has been reported to produce impact forces averaging 6 times the subject’s body weight, and as high as 12 times [16]. These high forces create risk of injury to the bones and joints, and this risk of injury increases as people age, become deconditioned, and lose muscle mass, strength, flexibility, and bone density [15]. A study that examined injury reports from a voluntary incident reporting system spanning over two dozen U.S. trucking companies reported that 27% of the 3053 cases reported were due to slips and falls and 9% of those cases were from entering or exiting vehicle beds of trucks, trailers or semi-trailers [11].
Summary
Based on this study, manual tarping results in greater physical demands and safety risks than the other alternate systems and thus the two alternate tarping methods are to be preferred where feasible. Perhaps surprisingly, the peak and average loads did not differ much between methods; most benefits were seen in the time that forces were exerted. Rack and tarp kit method was preferred over manual tarp because it has lower loading compared to manual tarping except for duration time in severe shoulder flexion. The slider method was preferred overall as it minimizes or eliminates the need to climb on the load thus reducing fall hazard exposure, demands with climbing on the load and loading from jumping is eliminated. It also has lower physiological workload with lower average heart rate, lower percent of maximum heart rate, less time in high workload, takes less time to complete, less time exerting forces, less back and shoulder loads, less time in severe back flexion and bilateral shoulder flexion and is impacted less by windy and inclement weather. Thus, the slider method was found to minimize demands, heart rate and safety concerns and was preferred by drivers.
These findings were consistent with the drivers’ feedback. All participants preferred the two alternative tarping methods over manual tarping. Three quarters of the drivers preferred sliders and the rest preferred rack and tarp kit. Some drivers stated that manual tarping should be eliminated. Others had feedback to improve the job by making lighter and more durable tarps. The drivers reported that the sliders were easier, less time consuming, less physically demanding and had less risk of injury.
The alternate methods offer a wide range of benefits including reduced physical demands, reduced exposure to fall hazards as well as improved productivity due to the shorter times, but with the disadvantage of being less versatile.
References
-
Liberty Mutual Group. (2006). Ergonomic considerations for tarping in the trucking industry. Loss Prevention Reference Note, LP 5363 July.
-
Van Dyne, P. and Christiansen, T. (2006). The lowdown on safe tarp handling. Occupational Health and Safety, 75(6), 128-131.
-
Eastman Kodak Company. (2004) Kodak’s Ergonomic Design for People at Work (2nd Edition) (S. N. Chengalur, S. H. Rodgers, and T. E.Bernard, Eds.) John Wiley and Sons, Inc., New Jersey.
-
Mital, A., Nicholson, A. S. and Ayoub, M. M. (1997). A Guide to Manual Material Handling, 2nd Ed. Taylor and Francis Ltd.
-
Waters, T. R., Putz-Anderson, V., Garg, A., and Fine, L. J. (1993). Revised NIOSH equation for the design and evaluation of manual lifting tasks. Ergonomics 36 (7), 749-776.
-
Norman, R., Wells, R., Neumann, P., Frank, J., Shannon, H., Kerr, M., and the Ontario University Back Pain Study (OUBPS) Group. (1998). A comparison of peak vs cumulative physical work exposure risk factors for the reporting of low-back pain in the automotive industry. Clinical Biomechanics 13(8), 561-573.
-
Neumann, W. P., Wells, R. P., Norman, R. W., Frank, J., Shannon, H., Kerr, M. S., and the OUVPS Working Group. (2001). A posture and load sampling approach to determining low-back pain risk in occupational settings. International Journal of Industrial Ergonomics. 27, 65-77.
-
Punnett, L., Fine, L. J., Keryserling, W. M., Herrin, G. D., Chaffin, D. B. (1991). Back Disorders and non-neutral trunk postures of automobile assembly workers. Scandinavian Journal of Work and Environmental Health 17, 337-346.
-
Haslegrave, C. M., Tracy, M. F. and Corlett, E. N. (1997). Force exertion in awkward working postures - strength capability whiletwisting or working overhead. Ergonomics, 40(12), 1335-1362.
-
Chow, A. Y., and Dickerson, C. R. (2009). Shoulder strength of females while sitting and standing as a function of hand location and force direction. Applied Ergonomics, 40, 303–308.
-
Lin, L-J, and Cohen, H.H. (1997). Accidents in the trucking industry. International Journal of Industrial Ergonomics, 20, 287-300.
-
Jones, D. and Switzer-McIntyre, S. (2003). Falls from trucks: A descriptive study based on a worker’s compensation database. Work, 20, 179-184.
-
McClay, R. E. (2008). Truck fall: Examining the nature of the problem. Professional Safety. 53(5), 26-35.
-
Lan, A., Daigle, R., and Lafrance, L. (2000). Safe tarping systems for wood chip trucks. Journal of Safety Research, 31(2), 81-91.
-
Montante, W. M. (2008) Don’t jump: The potential effects of jumping form heights. Professional Safety. July, 32-35.
-
Fathallah, F.A. and Cotnam, J.P. (2000). Maximum forces sustained during various methods of exiting commercial tractors, trailers, and trucks. Applied Ergonomics 31, 25-33.