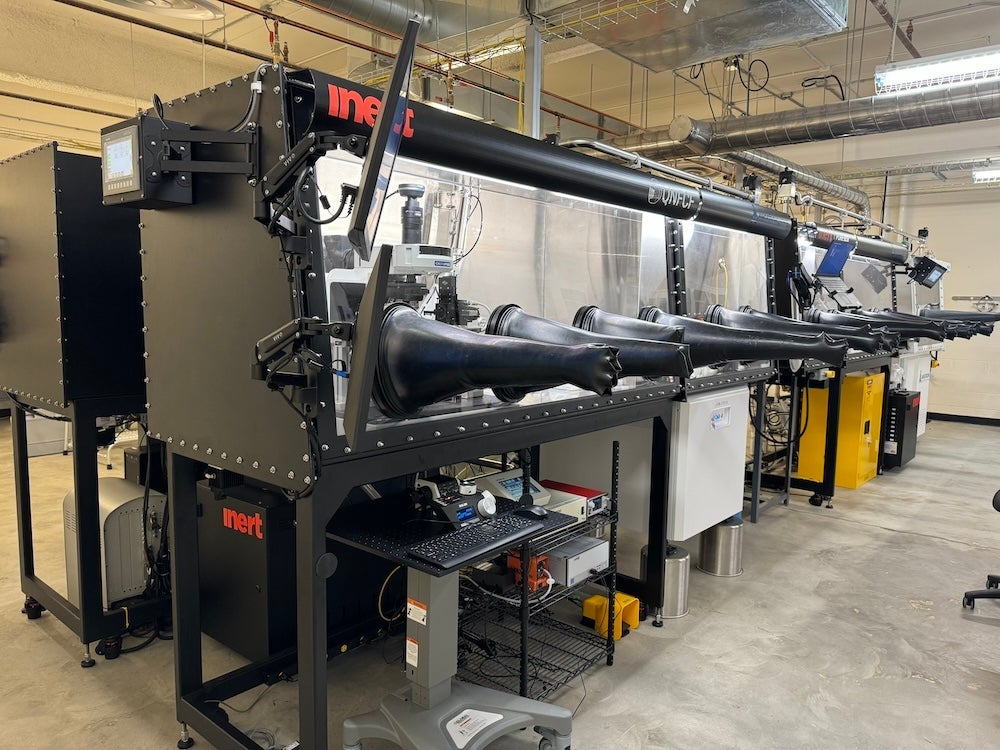
The Quantum Nano Fabrication and Characterization Facility (QNFCF) is announcing the commissioning of an inert atmosphere fabrication laboratory to enable development of 2D layered material devices. This unique capability was made possible through generous support from Transformative Quantum Technologies (TQT). The motivation for establishing this lab is the assembly 2D heterostructures and transferring these structures to custom fabricated contact chips to create complete devices. Many 2D materials such as chromium triiodide (CrI3) are prone to oxidation and must be assembled in an inert environment. This lab has been meticulously designed and assembled by the experts on the QNFCF team with technical support from Angstrom Engineering and JEOL USA. The combined goal is to serve the quantum community at the University of Waterloo, industry partners and the national research community through the Quantum Colaboratory initiative. The lab will be managed by QNFCF to the benefit stakeholders with open access and professional level maintenance of the infrastructure.
The Inert Atmosphere Fabrication Lab (IAFL) is a 1200 ft2 lab facility located in the David Johnston Research and Technology Park at the RAC building. This facility has a dedicated chemistry lab and a custom-built glovebox system containing a complete fabrication suite. This system comprises multiple glovebox stations, each dedicated to an individual fabrication step, linked together via antechambers. The entire system is under an inert nitrogen environment and maintains less than 0.1 PPM level of oxygen. Capabilities of each station are outlined below:
2DM Transfer station:
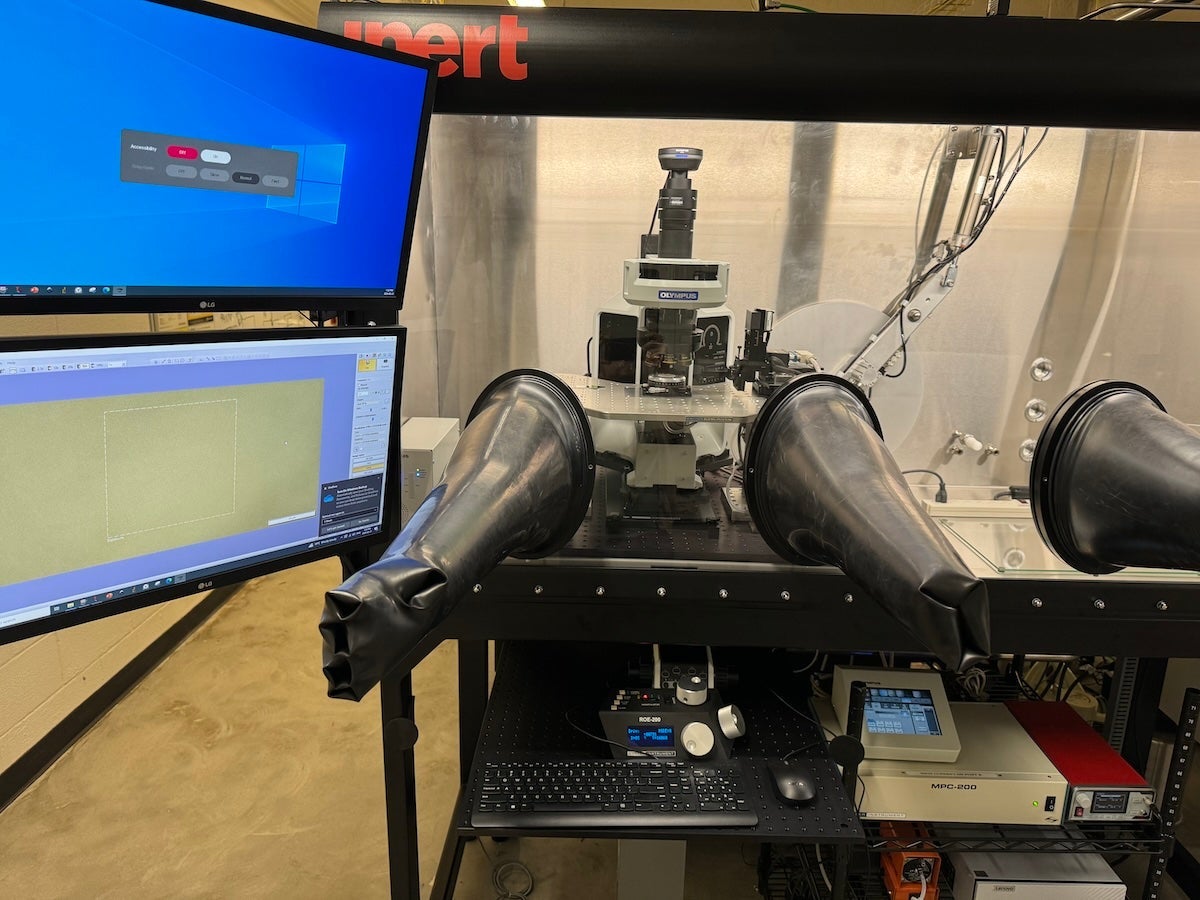
Researchers can visually survey samples loaded with 2D crystals and extract and stack the layers as required. The stacked 2D layers can then be controllably transferred to chips containing electrical contacts. The 2D materials transfer system is comprised of a fully automated Olympus BX63 microscope with a fixed stage, 200°C heated sample holder and a micromanipulator with 62.5 nm/step to enable researchers to assemble synthetic heterostructures and other 2D layered materials with speed and precision.
This station also contains a dedicated preparation work area for bulk crystal flake exfoliation. Here researchers can separate layers of material from bulk crystals using the scotch tape method and quickly transfer them to their heterostructure assembly using a glass slide and stamp method.
Wet Chemistry Station:
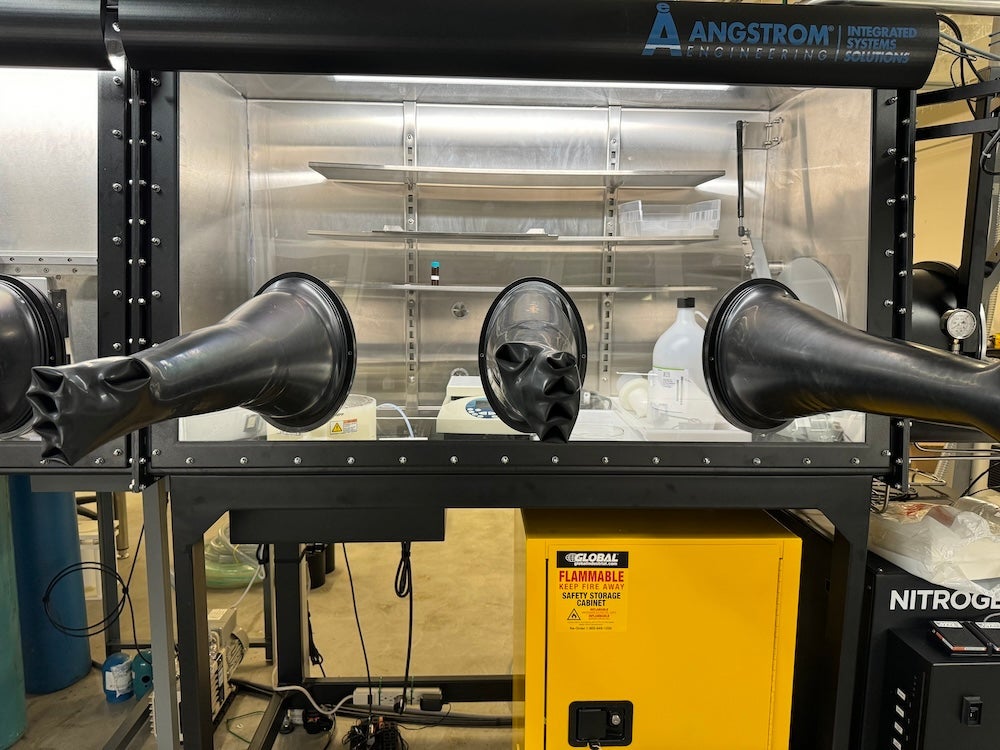
All organic solvent and resist spinning processes typically found in a fabrication cleanroom will occur in this glovebox. In this station you will find a Laurell spin coater, Torrey Pines Scientific hotplate, and a dedicated area for cleaning substrates and post metallization liftoff.
The chemicals used in cleaning, developing and lift-off are solvent based and generate fumes that must be contained to reduce atmospheric contamination. This station is equipped with a dedicated nitrogen purifier which can remove solvent fumes from the glovebox environment.
Reactive Ion Etching and Plasma Cleaning Station:
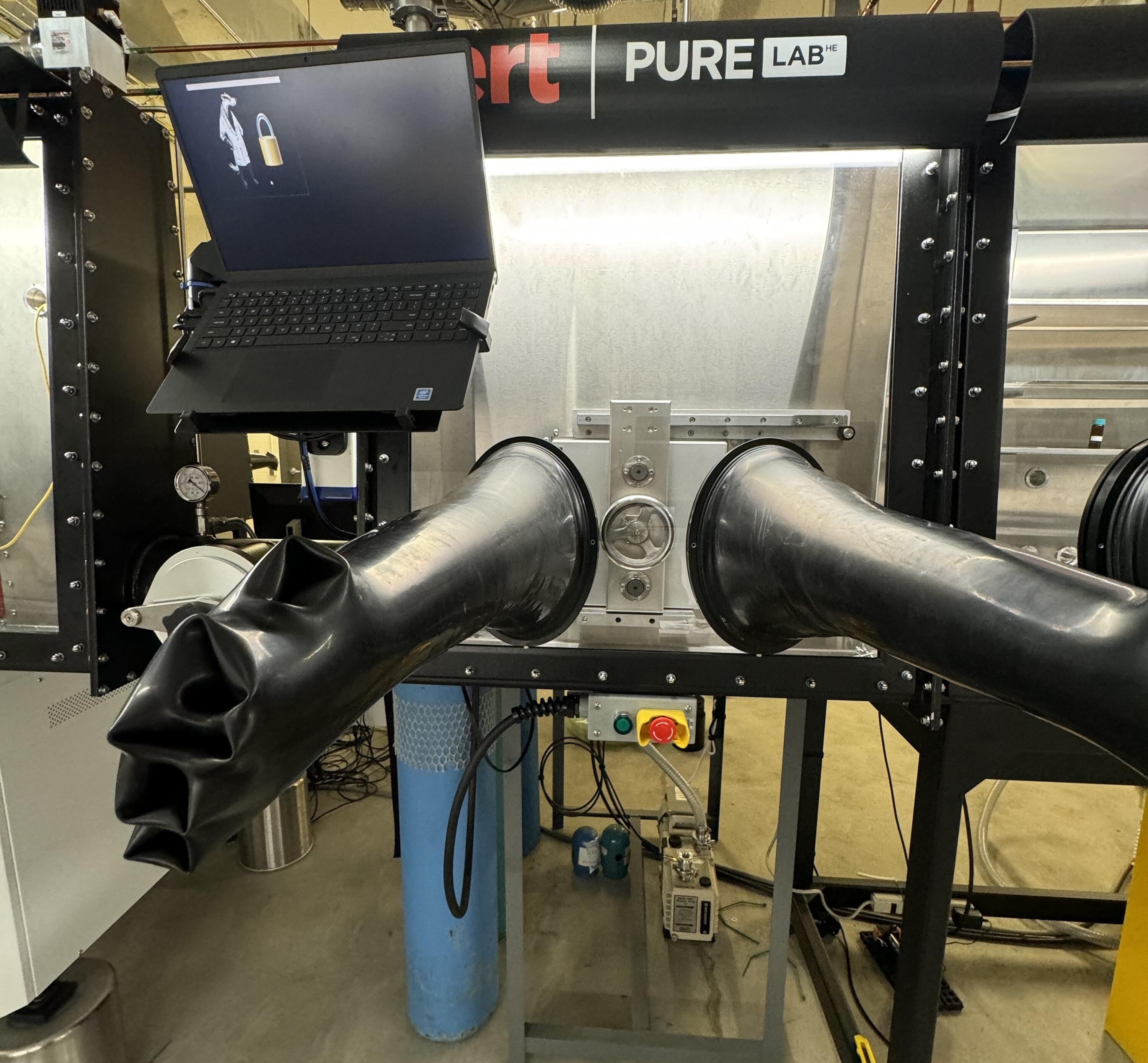
Plasma etching and cleaning plays an important role in many fabrication processes, particularly in 2D layered materials research. Many processes in 2D device fabrication such as removal of surface organics, surface activation of polymers, and reactive ion etching can be executed in this station. The PlasmaEtch system has a 300 W 13.56 MHz RF power supply with automatic matching unit and is setup for high-rate anisotropic etching. The gases available on this system are CHF3, O2 and Ar.
E-beam Patterning and Electron Microscopy Station:
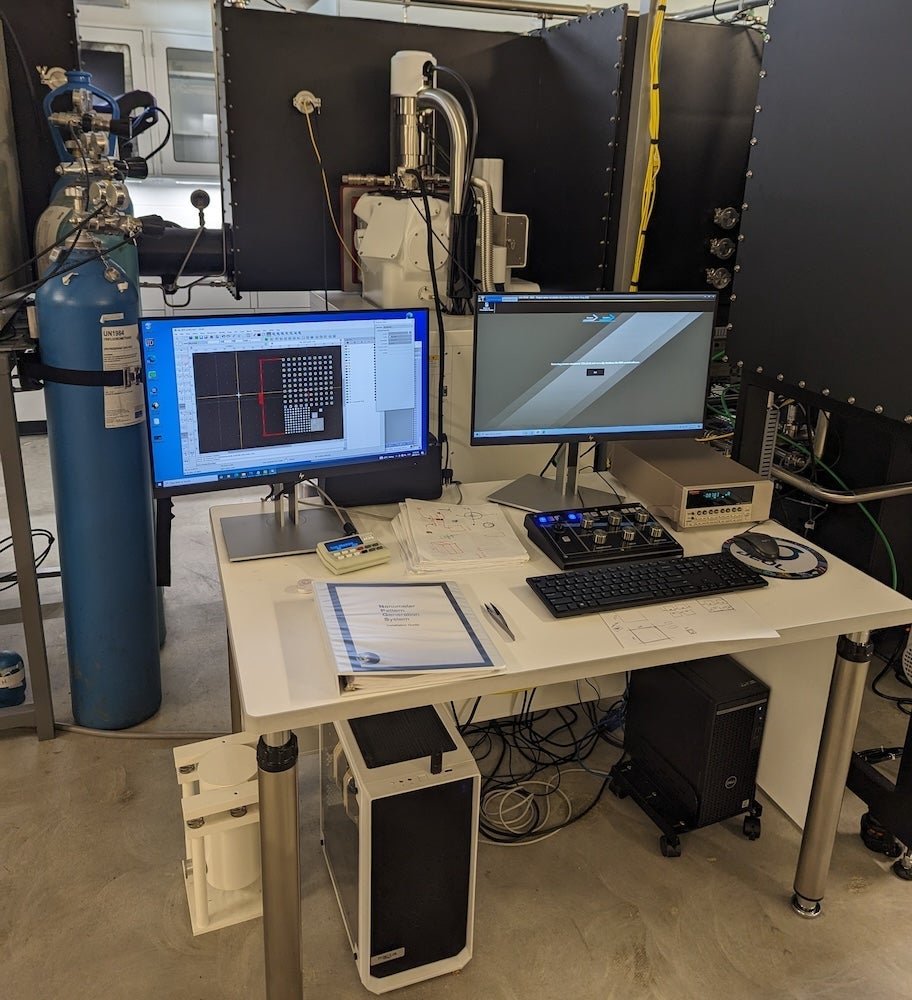
The E-beam patterning and electron microscopy station consists of a JEOL IT-510LV Scanning Electron Microscope (SEM), which has a 30kV electron column and a 5-axis stage. This system has been equipped with a beam blanker and a Nabity Nanometer Pattern Generation System (NPGS) to enable sub-micron patterning of electron sensitive polymer films.
The integration of the JEOL IT-510LV SEM into a glovebox was novel challenge as it required a custom engineered solution to isolate the electron microscope unit from vibrations transmitted through the glovebox. Vibrations were mitigated via the fabrication and integration of a custom designed microscope door which attaches to the glovebox via a flexible rubber membrane.
Metallization Station:
In this station a thin metal films can be grown by thermal evaporation. This can be used in tandem with pre-patterned polymers (from the E-beam patterning station) to fabricate electrical contacts for the 2D material device. The evaporator employed in this system is an Angstrom NexDep thermal evaporator featuring 4-thermal sources with an additional co-deposition capability. The system is charged with Au, Ti and can accommodate other materials as required. Samples can be loaded from the rear of the chamber (ambient lab environment) and through the front of the glovebox (inert atmosphere environment).
Characterization Station:
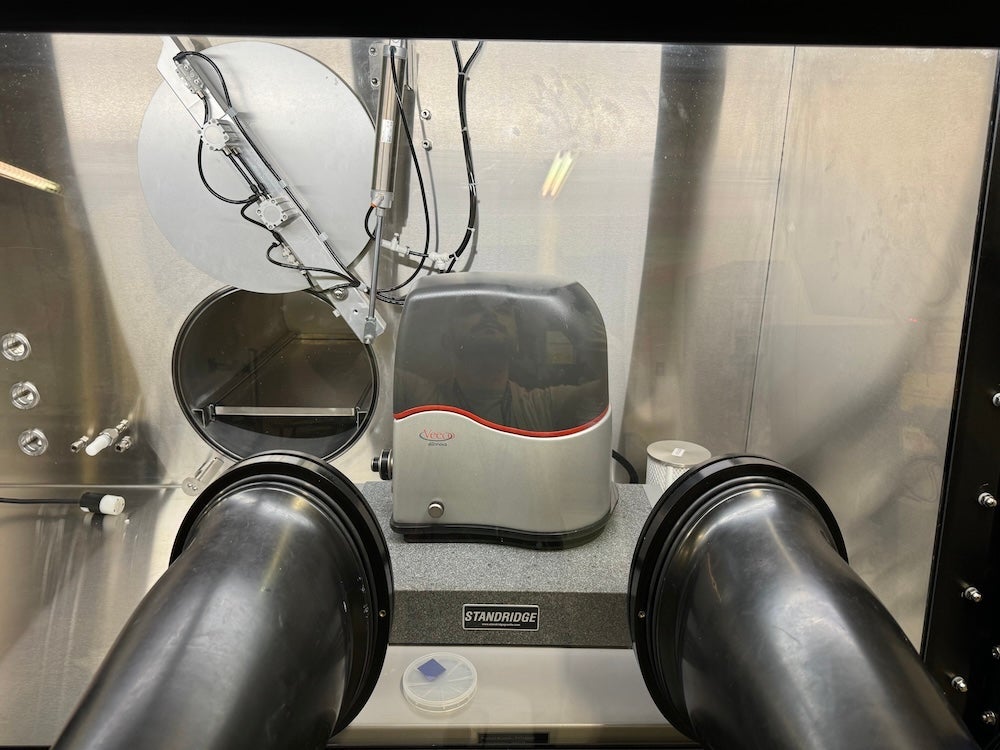
Atomic force microscopes (AFM) can measure the height of single atomic layers, which is required when characterizing assemblies of stacked 2D materials. The characterization station contains a Veeco Innova AFM with a 3-axis stage, installed in a glovebox which has been optimized to reduce vibrational noise.
Inquiries:
This new lab resource is available immediately for all members of the QNFCF community. TQT has also generously offered limited financial support to an initial cohort of members who agree to participate in improvement and advertisement of this resource.
Questions about capabilities, access, and support can be directed to Taso Alkiviades.