The Quantum-Nano Fabrication and Characterization Facility (QNFCF) is pleased to offer user training and support for mechanical sample preparation for transmission electron microscopy analysis. This service is available to anyone accessing our new JEOL F200 TEM system and is intended to complement existing sample preparation capabilities of the Zeiss FIB/SEM.
Detailed procedures have been tested and documented using the suite of tools available in the TEM Sample Preparation Laboratory located in QNC B703, which include:
- Precision grinding and polishing tools (Allied Multiprep 8’’ and Southbay 900)
- Ultrasonic disc cutter (Gatan Tuned Piezo Cutter)
- Diamond saws (Southbay 650 and Leica EMTXP)
- Dimpler (Southbay D500i)
- Low angle dual beam ion milling with LN2 cooling option (Leica EM RES102)
- Inspection microscope (Zeiss AxioScope, 5-150 X)
- Wet and dry fumehoods, analytical scale, hotplate, ultrasonic bath, micro-pipettes etc.
Any questions about these new capabilities or their access should be directed to Sandra Gibson.
The sections below will summarize two newly documented workflows for mechanical sample preparation each applied to one example sample. These sections summarize the processes for dimple grinding with ion milling, and wedge polishing.
Technique #1: Dimple grinding with ion milling
Samples can be cut into the standard size 3 mm discs required for TEM using the Gatan Tuned Piezo Cutter. It uses a slurry of boron carbide and an ultrasonically oscillating cutting tool to gently grind away samples into disc, cylinder or rectangle shapes. The method is especially well suited to cut brittle materials without undesired cleavage or chipping.
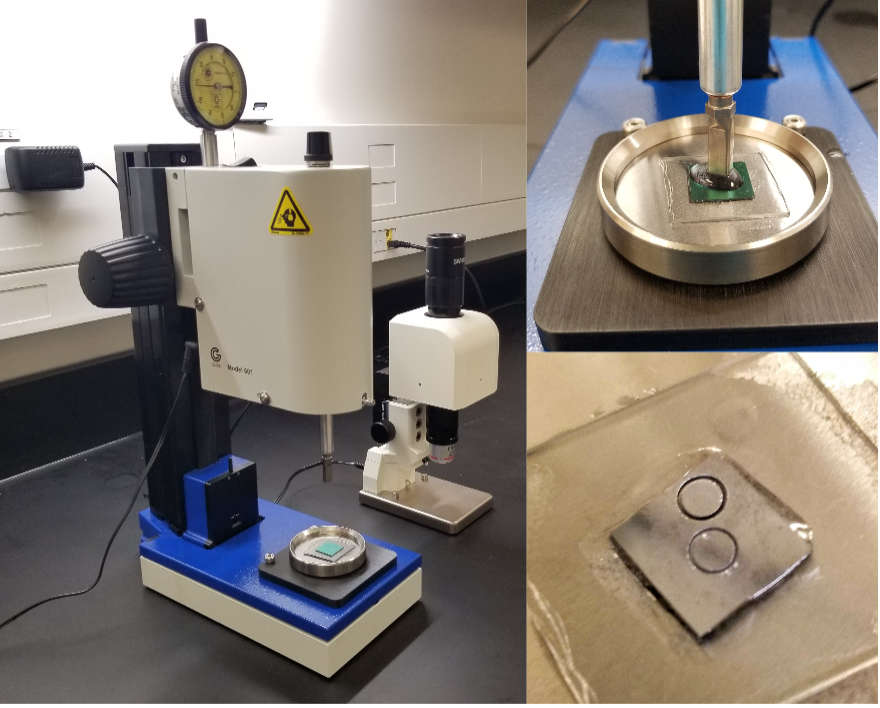
The disc is then thinned and polished using precision diamond lapping on the Allied Multiprep 8’’.
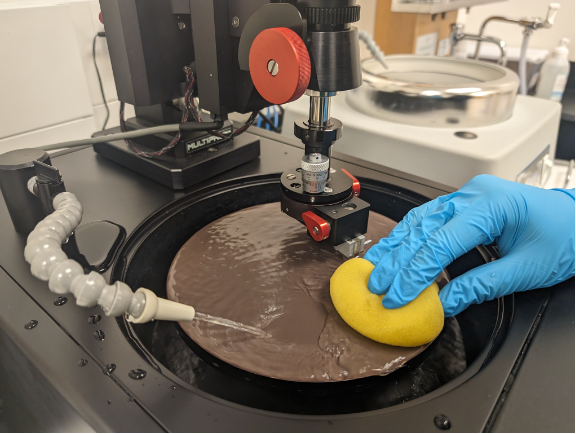
The Southbay D500i tool uses a perpendicularly rotating polishing tool and sapphire sample platen charged with an abrasive polycrystalline diamond paste. Dimpling grinds a ‘bowl’ shape out of the sample having a large thin central area surrounded by a robust outer rim. This efficiently pre-thins the sample center to only a few microns thickness, while also eliminating special handling techniques for fragile specimens.
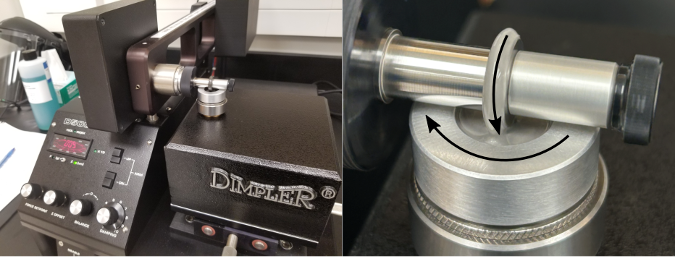
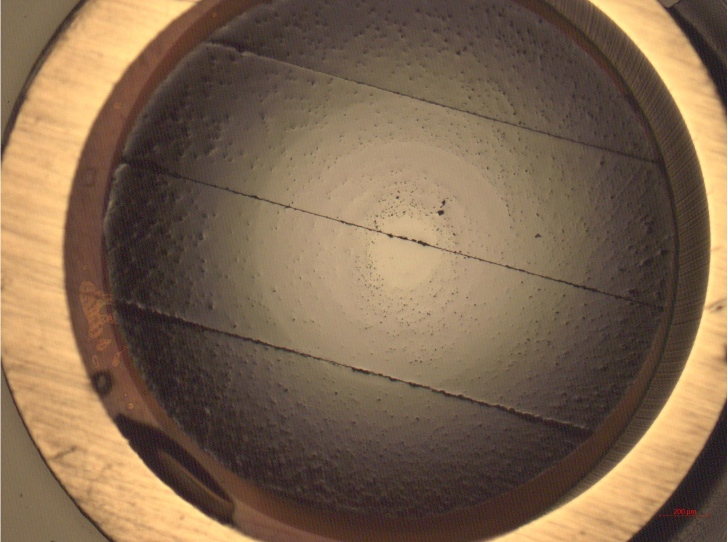
Dimpled samples are subsequently ion milled, which gently sputters away material until the centre region is thinned down until a hole is formed. The EM RES 102 has two inert (Ar+) ion guns which can be used at low angles (e.g. 6˚-2˚) and low accelerating voltages (e.g. 8 kV-2 kV) for a gentle final polishing which does not alter the sample structure or introduce artifacts.
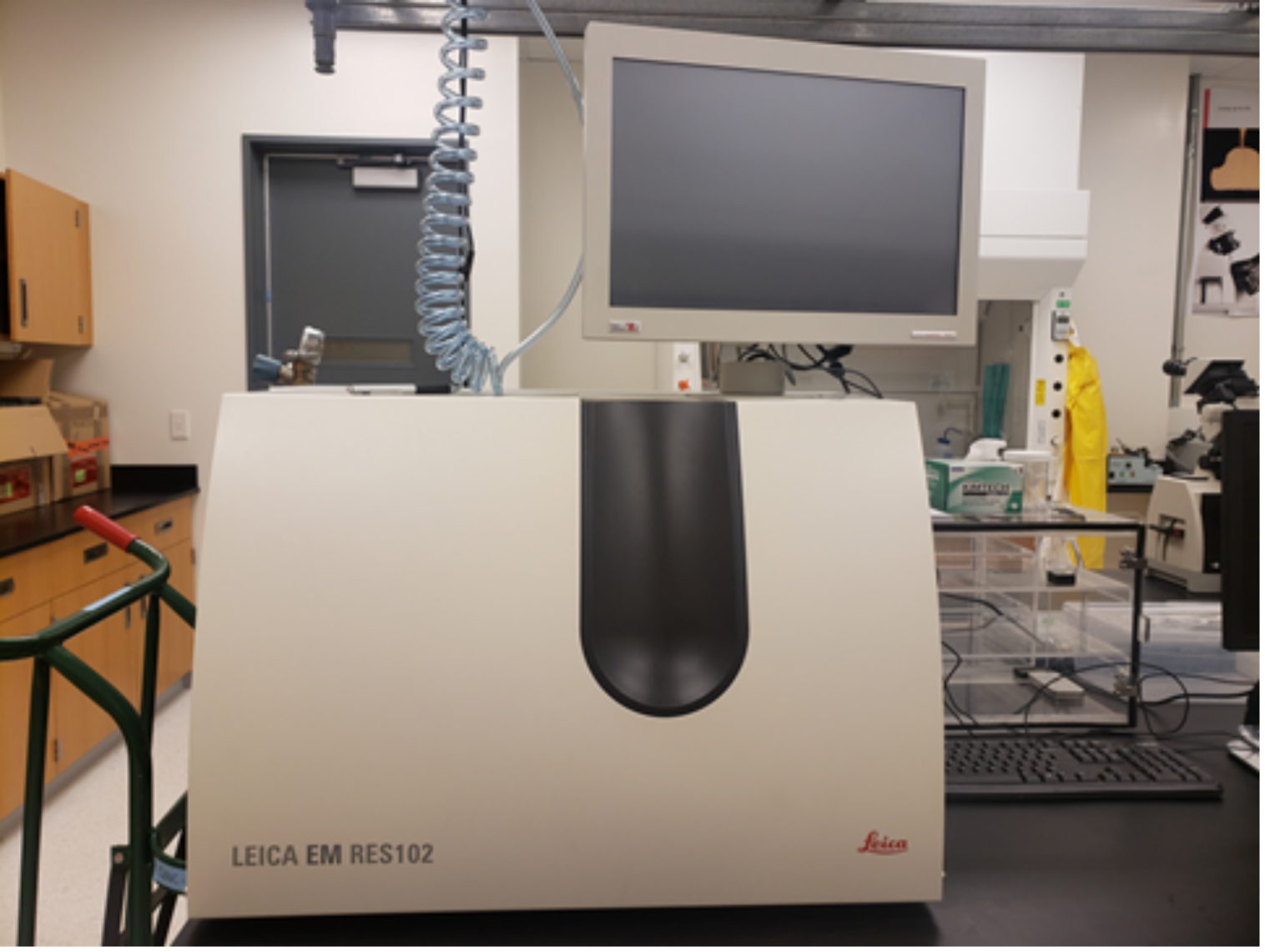
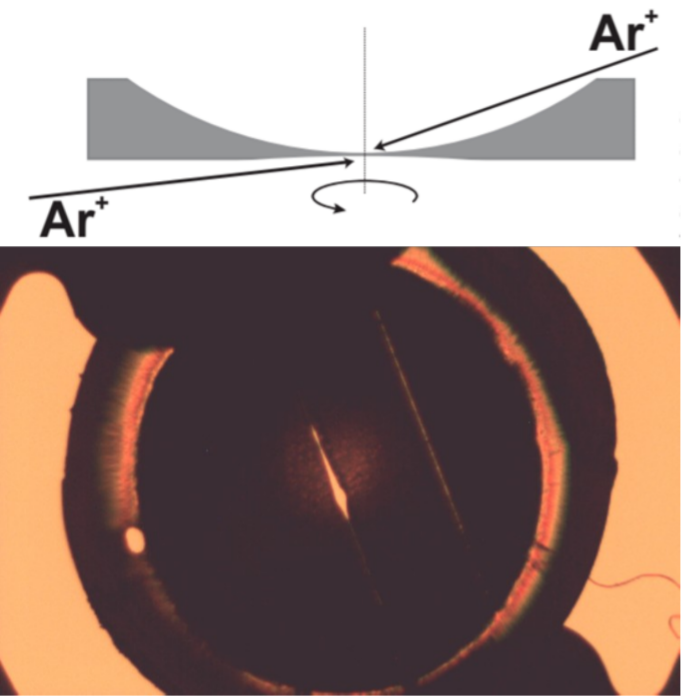
Figure 6: (Top) Two Ar ion guns gently mill the sample until a hole (bottom) is created in the centre.
This technique was applied to an aluminium 'scalmalloy' sample provided by Ali Rezaei from the Multi-Scale Additive Manufacturing Lab. LPBF (laser powder bed fusion) is an additive manufacturing technique where lasers are used to melt metal powders; this process can lead to the formation of melt pools that have a so-called 'fish-scale' microstructure. A 3 mm 'self-supported' disc was processed using the dimpling and ion-milling procedure. This process yielded several large electron transparent regions suitable for analysis, near the centre hole visible in figure 7.
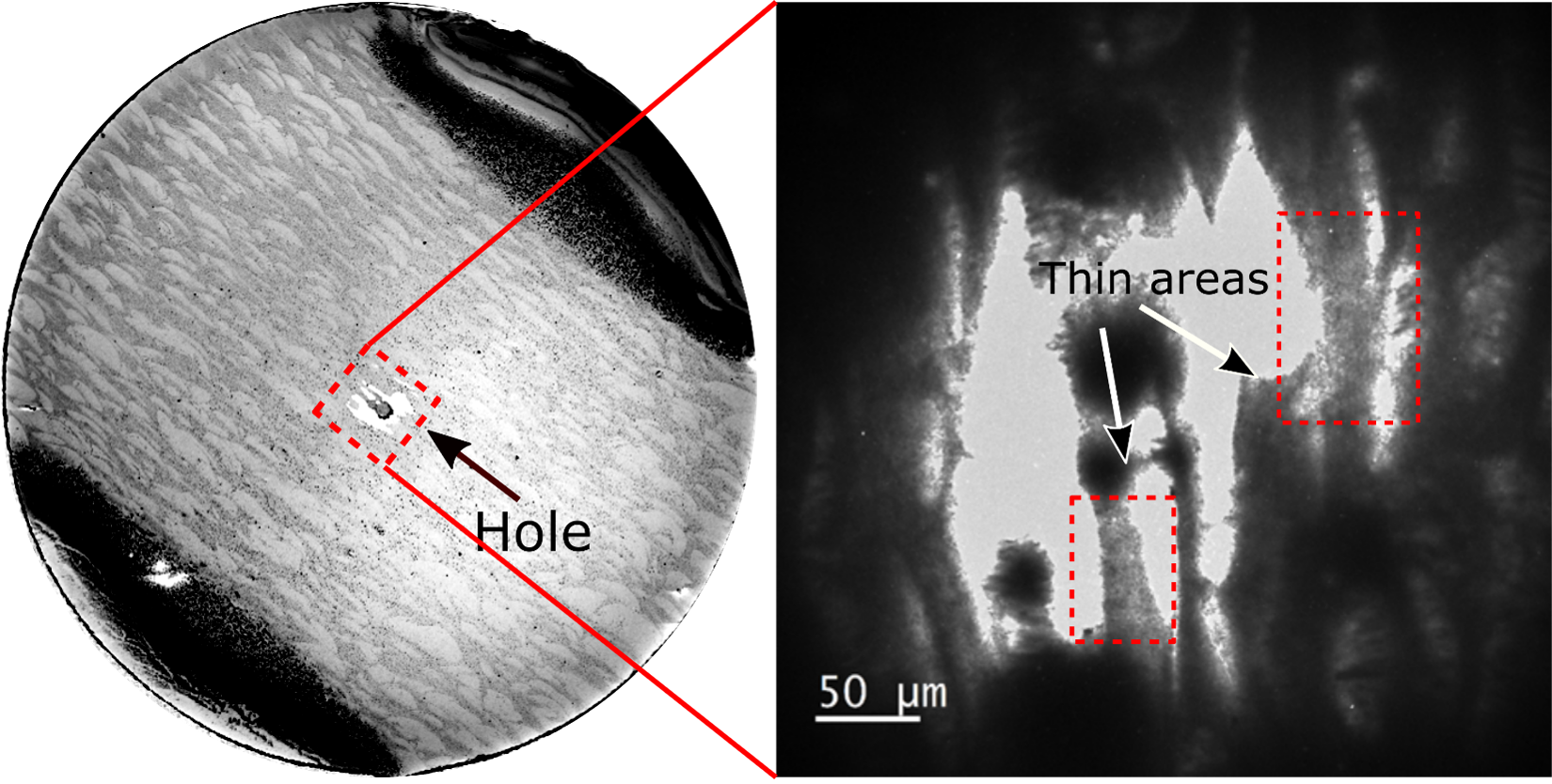
Using electron energy loss spectroscopy in the TEM, Al2(Sc, Mg) nano-precipitates were identified in the melt-pool boundaries.
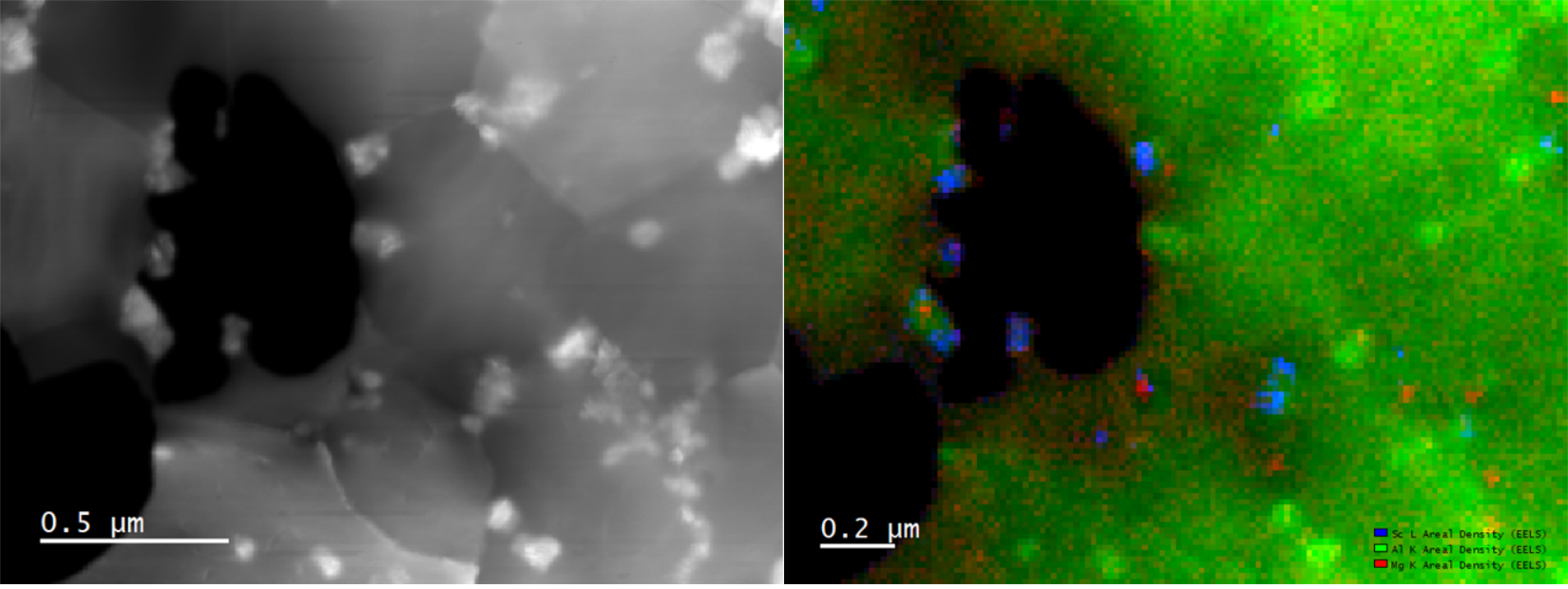
Technique #2: Wedge polishing
This is an alternative technique (to dimple grinding with ion milling) which uses only precision polishing to prepare TEM samples.
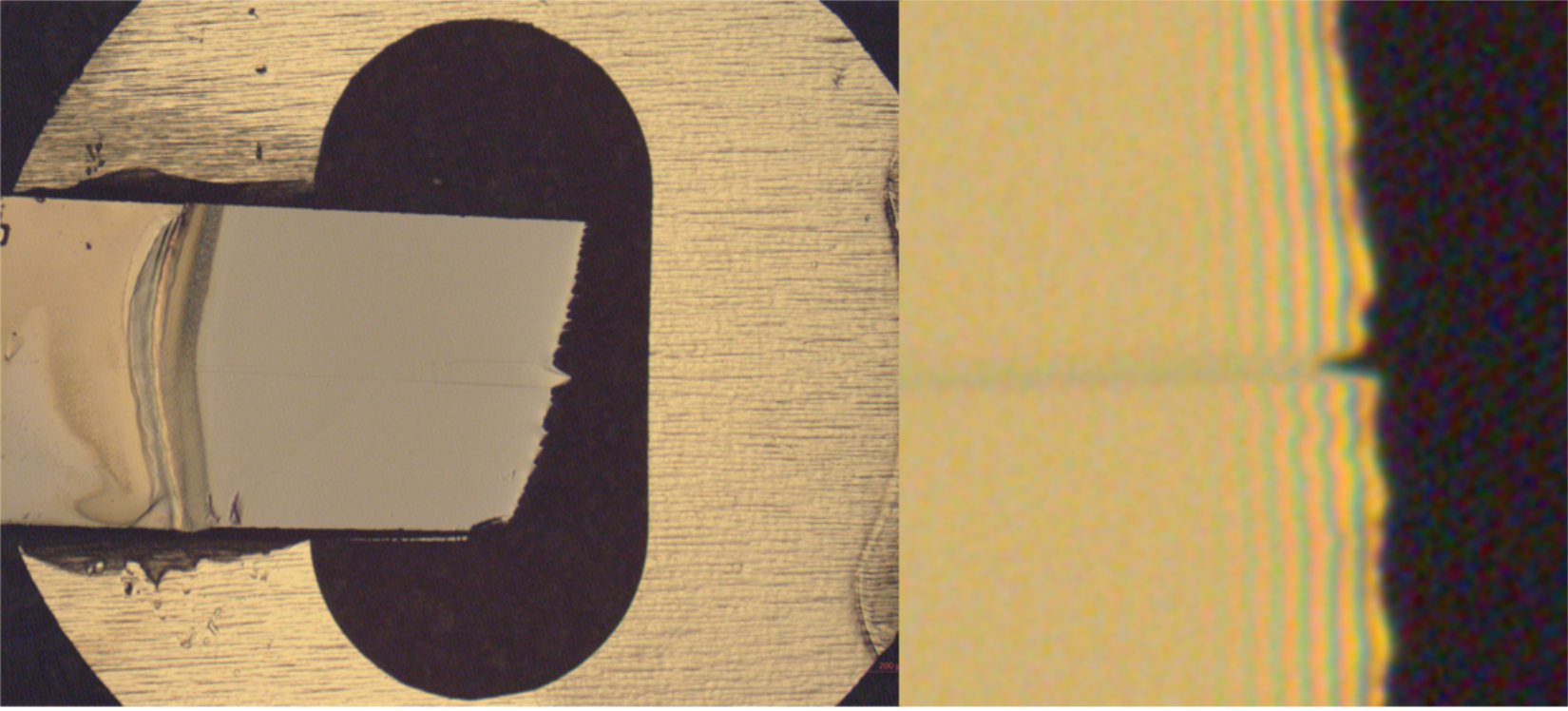
For a cross-sectional sample two pieces are glued together face-to-face under pressure using PFP 353ND epoxy. The 'sandwich' is then cut into 1 mm x 2 mm slices. The slices are thinned and polished on both sides using diamond lapping film. In the final step a 2˚ angle is introduced so that one edge becomes exceptionally thin. Interference fringes and sometimes a change in colour can be observed as the sample approaches a suitably thin state. The wedge sample is then mounted onto a 3 mm slotted TEM grid as shown in Figure 6. On either side of the glue line an area which is 100 nm thick or less can be imaged at the atomic scale in the TEM.
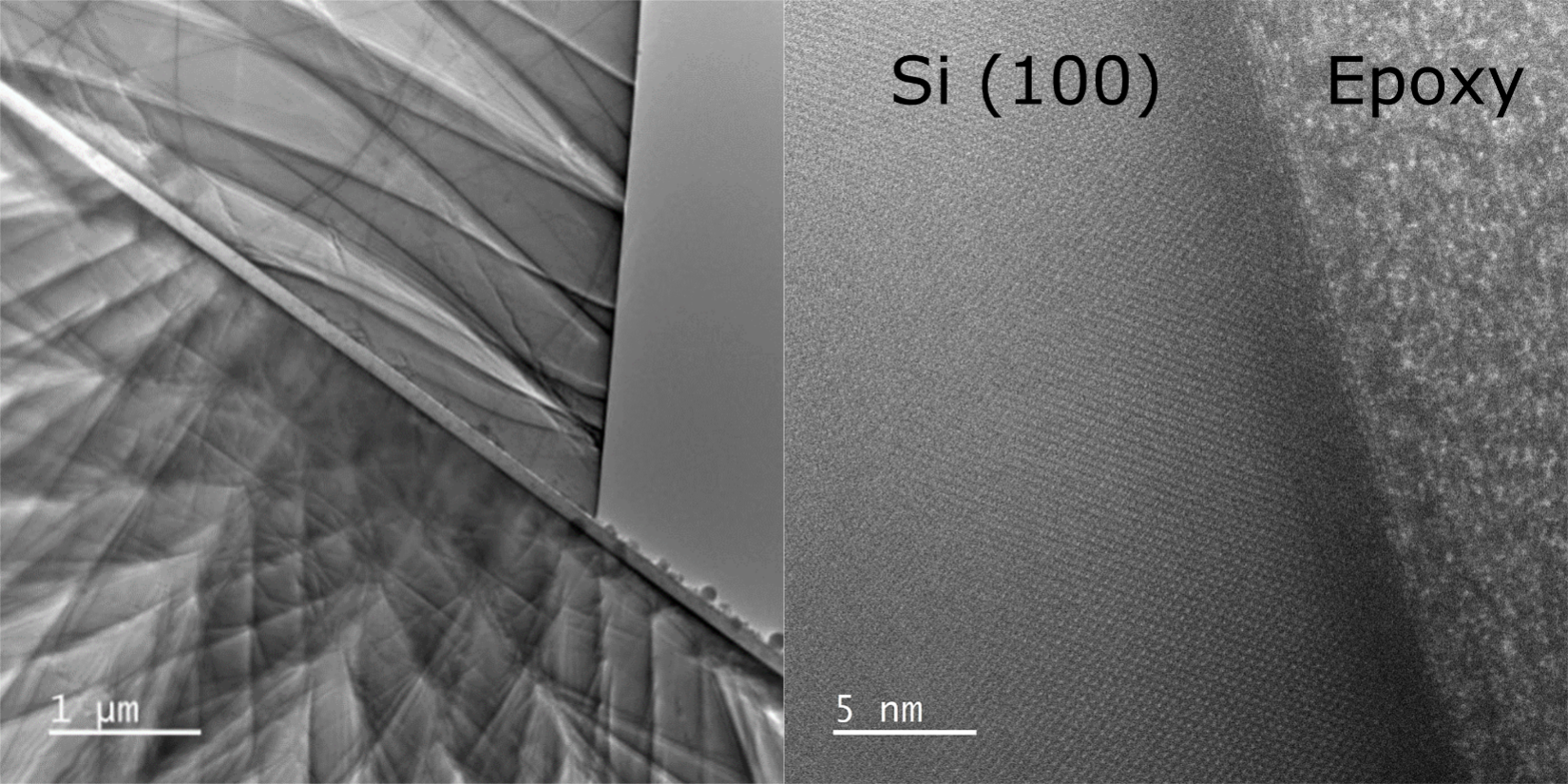
In a second test of this technique five nominally 10 nm thick layers of different metals (Ti, Au, Al, Pt Cu) were deposited by electron-beam PVD onto a silicon substrate. Wedge polishing yields a thin (<50nm), clean and defect free region where elemental mapping can be performed.
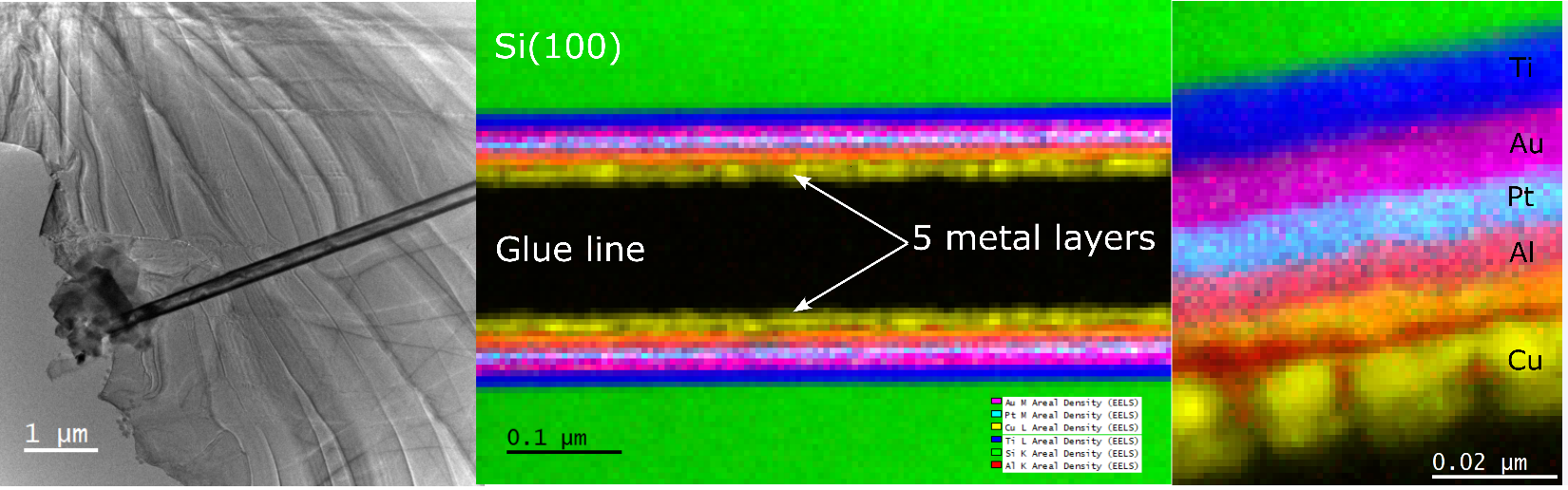
Other Techniques:
This toolset can also be used to cut and polish samples for various other purposes. For projects involving feature aligned chip cross-sectioning, backside polishing, parallel delayering or substrate thinning and polishing, contact Sandra to discuss.
Special thanks for the excellent work of co-op student Daphene Wen who completed all the hands-on testing and written documentation for this project. We gratefully acknowledge the Transformative Quantum Technologies program for their financial support which enabled the development of these capabilities.