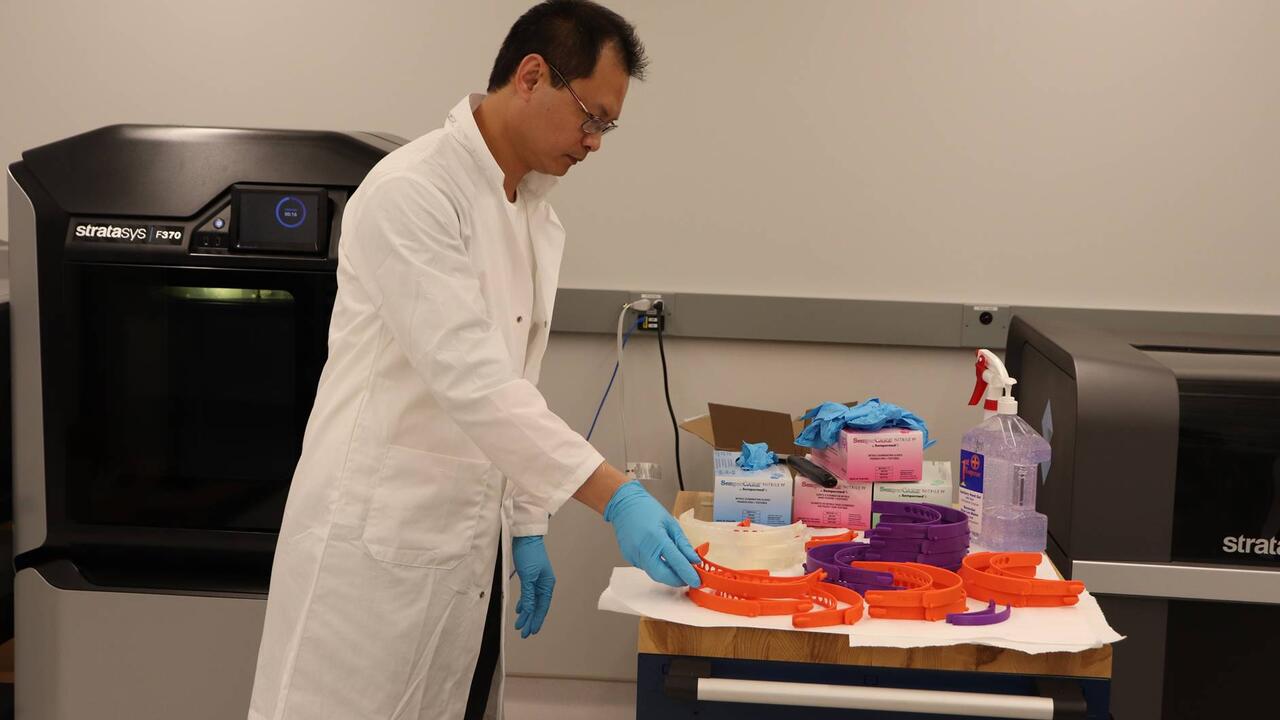
3D printers used in battle against COVID-19
Production focus pivots to 3D-printed parts for face shields worn by health-care professionals
Production focus pivots to 3D-printed parts for face shields worn by health-care professionals
By Carol Truemner Faculty of EngineeringUniversity of Waterloo facilities have shifted their production focus to 3D-printed parts for face shields used by health-care workers battling COVID-19.
3D printers in the Multi-Scale Additive Manufacturing (MSAM) Laboratory and in the Print and Retail Solutions Department at the University are being used to build certified pieces of the protective equipment from a special material currently in short supply throughout the local medical community.
Two weeks ago, Health Canada reached out to companies and institutions across the country to determine the number of 3D printers capable of creating required medical equipment, including parts required for the shields, worn over top of surgical masks for additional protection.
“Our lab quickly volunteered to help and we’re now part of a community group of companies and institutions that have banded together to provide free medical support and supplies,” says Ehsan Toyserkani, a mechanical and mechatronics engineering professor and research director of the MSAM lab.
Jerry Ratthapakdee, an MSAM lab technician, takes a completed headband out of a 3D printer in the University of Waterloo’s Multi-Scale Additive Manufacturing (MSAM) Laboratory.
With materials supplied by Cimetrix Solutions Inc. located in Oshawa, Waterloo’s printers are currently producing 50 to 60 engineered polymeric headbands and bottom reinforcements a day.
The parts are shipped to InkSmith, which has provided the digital data for the printers to read. The company assembles the laser-cut shield films and printed parts and then distributes them to local hospitals and medical centres.
Toyserkani said the MSAM lab will also be producing N95 respirator masks if the designs developed by international 3D printing companies such as Copper3D are approved by Health Canada. An N95 mask filters out 95 per cent of particles, including bacteria and viruses.
“We’re looking into the possibility of customizing the design and molding the mask to the face,” says Toyserkani. “One of the main benefits of our lab is that we can fully appreciate 3D technologies and how they can be deployed to develop, design and produce medical components.”
Mihaela Vlasea (BASc '08, PhD '14, mechanical engineering), a mechanical and mechatronics engineering professor and associate director of MSAM, points out that a lot of the prep work for 3D printing can be completed remotely to ensure safe social distancing.
“The technicians just need to go in, hit the print button and monitor for the first few minutes," she says. "Then they can essentially go home and come back when the parts are ready.”
Sanjay Singh, an electrical and computer lab instructor and software specialist, has also been making parts for face shields, but on his personal 3D printer rather than in a lab.
“I am working from home, marking student work and the 3D printer is in the next room, which is a sort of workshop,” he says. “When the print job ends, I can start printing again in a minute or so.”
For Singh, the greatest source of innovation right now is the individual person rather than large companies.
“It's amazing how fast solutions came when there was an environment receptive to such things,” he says. “It speaks to the power of collaboration such as those seen in open-source projects of various kinds.”
A team comprised of MSAM lab members is part of a global innovation challenge launched last week by the Montreal General Hospital Foundation in collaboration with the Research Institute of the McGill University Health Centre to design a simple, low-cost ventilator that can meet the needs of COVID-19 patients.
Vlasea says that after entering the challenge a week ago, team members are well on their way to developing a viable solution.
Read more
Researchers altered bacteria found in wastewater treatment, where microplastics can enter environment
Read more
The stuff that gives cards, ornaments and decorations a holiday lustre does more than just gets everywhere
Read more
Funding supports a range of projects from sustainable 3D printed materials to 6G network innovations and improving the electric automotive industry
The University of Waterloo acknowledges that much of our work takes place on the traditional territory of the Neutral, Anishinaabeg, and Haudenosaunee peoples. Our main campus is situated on the Haldimand Tract, the land granted to the Six Nations that includes six miles on each side of the Grand River. Our active work toward reconciliation takes place across our campuses through research, learning, teaching, and community building, and is co-ordinated within the Office of Indigenous Relations.