QMS Webinar Series: Failure Mode Effective Analysis
Speaker: Abdul Khalfan CQE, SSGB
Principal, Quality Assurance & Reliability Engineering Consulting Services
Failure Mode Effective Analysis
Failure Mode Effective Analysis better known as FMEA. It is an effective tool to provide decision making information to a Team of design, manufacturing, industrial, test, service, quality, and sustaining engineers, supply chain, maintenance personnel, program managers, management, and stakeholders at large to make value-added and pragmatic decisions to address chronic issues and ideas of improvements regarding their products/devices and services based upon objectiveness and not subjectiveness.
The concept of designing FMEA as a tool to address chronic and safety issues initiated in the 1960’s by the Aerospace industry during the Apollo missions, in the 1970’s by US Navy and Automotive industries.
There are four types of FMEA: i) System FMEA, ii) Design FMEA, iii) Process FMEA, and iv) Service FMEA.
The output of FMEA is based upon a ‘Risk Priority Number’ whose acronym is ‘RPN’. ‘RPN’ is calculated by taking into consideration the problem / issue at hand of its Severity multiplied by Occurrence multiplied by Detection or mathematically RPN = Severity X Occurrence X Detection. Typically, higher the ‘RPN’ number, higher the priority to address the issue at hand. However, this may or may not be applicable in each and every case as business decisions need to taken into account also.
The salient feature of FMEA is that it can be put into effect or practiced at any given point in time within the Product Life Cycle (PLC). It is or can be used to address problems/issues and improvement ideas for reliability, availability, serviceability, installability, and cost improvement.
About Abdul Khalfan:
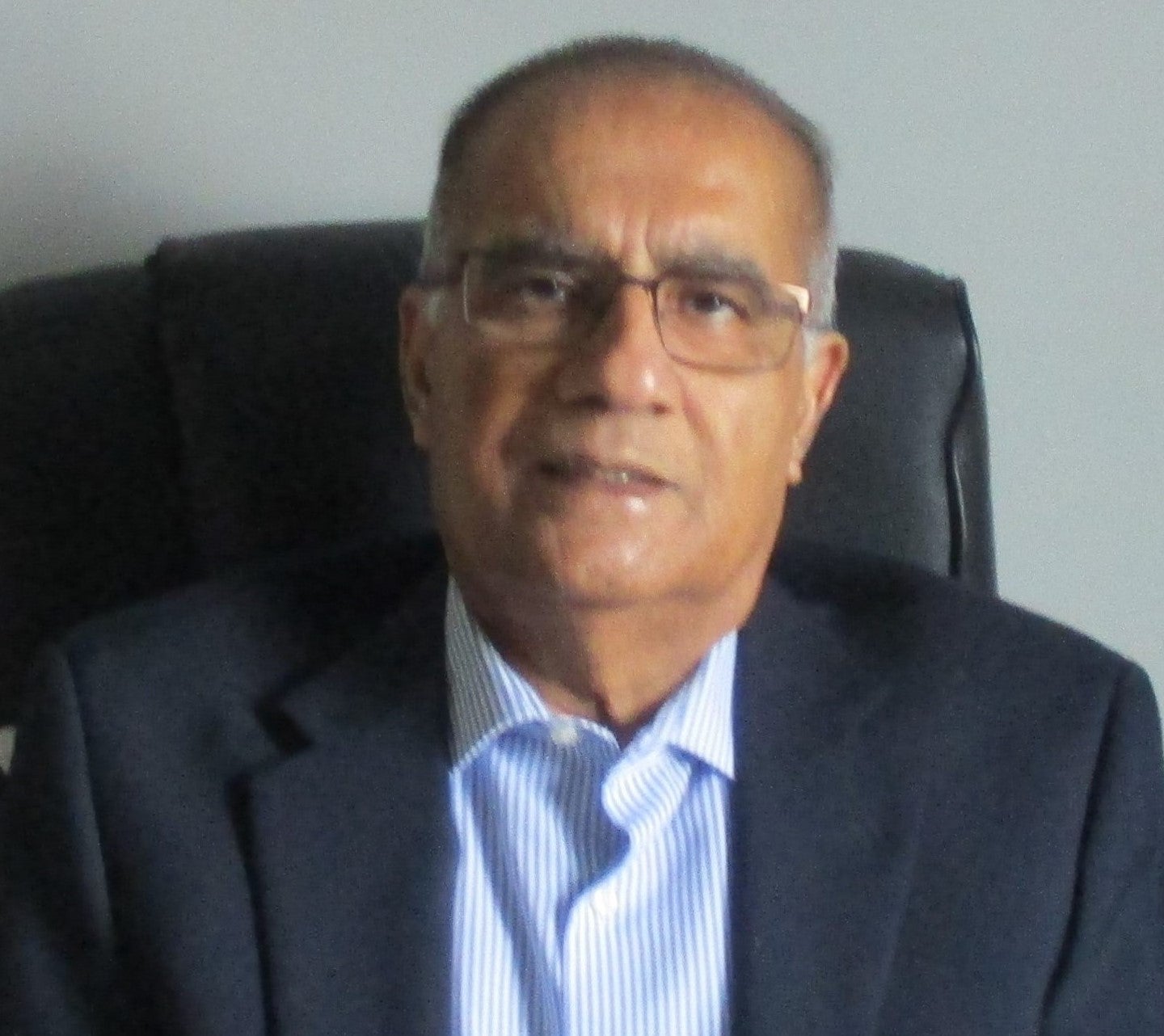
Abdul
Khalfan
is
a
Quality
Management
Systems
Professional
(QMS)
with
extensive
experience
in
the
high-tech
industry.
His
hands-on
style
and
practical
approach
to
business
management
makes
him
a
natural
catalyst
for
improvement
initiatives.
His
unique
career
path
and
ground
up
experience
has
provided
him
with
business
and
process
insights
leading
to
greater
profitability,
value-add,
and
efficacy
for
small,
medium,
and
large
companies
and
organizations
such
as
NCR
Corporation,
Flextronics,
Ingenico,
Com
Dev,
Teledyne-Dalsa,
ITT,
Bell-Howell,
KA
Imaging,
Curriato
Inc.,
Schock
Metal
America
Inc.,
Durose
Steel,
Honda
Automotive,
Kaparel,
to
name
a
few.
Currently,
he
is
providing
Consulting
Services
for
ISO
9001:2015
and
ISO
13485:2016
Standards
to
Medical
Device
and
non-medical
companies
in
Kitchener-Waterloo
area.
Abdul
Khalfan
consistently
focused
upon
underperforming
processes
and
products
to
higher
levels
of
excellence
and
profitability.
Using
careful
statistical
analysis
and
a
keen
eye
for
value-add
and
process
improvements
he
has
been
able
to
transform
unproductive,
wasteful
practices
into
effective
and
value
added
process
improvements.
Additionally,
Abdul
Khalfan,
has
established
from
ground
zero
the
entire
infra
structure
of
QMS
resulting
in
ISO
9001
Certification
in
the
first
audit;
managed
continuous
improvement
projects
which
in
one
case
improved
the
‘Early
Life
Performance’
of
products
by
47%
resulting
in
savings
of
millions
of
dollars,
significantly
reduced
the
number
of
process
steps
and
data
consolidating
North
American
data
in
one
database
saving
10
man
days
of
work
and
savings
of
US$
100,000
annually.
Similarly,
significantly
streamlined
and
formalized
haphazard
and
broken
Engineering
Change
Request
and
Engineering
Change
Notice
processes
in
a
formal
consolidated
and
automated
process,
thereby
realizing
its
effectiveness,
efficiency,
reduced
number
of
errors,
timely
execution,
and
cost
savings.
Abdul Khalfan is an ASQ Certified Quality Engineer (CQE), SSGB, an Exemplar Global Certified Lead Auditor for ISO 9001:2015 and ISO 13485:2016 Standards, Certified Process Management and Improvement Trainer, holds Advanced Quality Assurance Diploma with an Electrical Engineering background.
He has been a frequent guest speaker at ASQ Meetings on Quality and Reliability subjects, part time instructor at Conestoga College on the subject of Total Quality Management (TQM), and is currently delivering Quality and Reliability workshops for UW CBB (Centre for Bio-Engineering and Biotechnology).
Abdul’s Consulting Services website address: www.qareconsulting.com.
Please contact cbb@uwaterloo.ca for the meeting link