MEMS structure floating robots are designed and fabricated to perform various tasks remotely.
The increasing understanding of researchers about micro systems and micro mechanisms led to a wide interest about micromanipulation. Currently, there is a high demand for systems which can position micro objects with high precision. Such systems find many applications such as microassembly of mechanical components and manipulation of biological samples. These applications require high positioning accuracy, gentle handling, high working range and high manoeuvrability.
There are numerous microrobotic stations reported in literature for micromanipulation applications. These systems are generally composed of a motion stage that is controlled through a controller and an end-effector tool designed for the specific application. The end-effector tool is connected to a massive controller system through arms which limits the working environment. In addition, the end-effector tool is usually in micro size, therefore care should be taken when the end-effector tool is integrated with the controller system. The dominant forces in the micro scale such as friction and adhesion are very complex to formulate which further complicates the controller design for such systems.
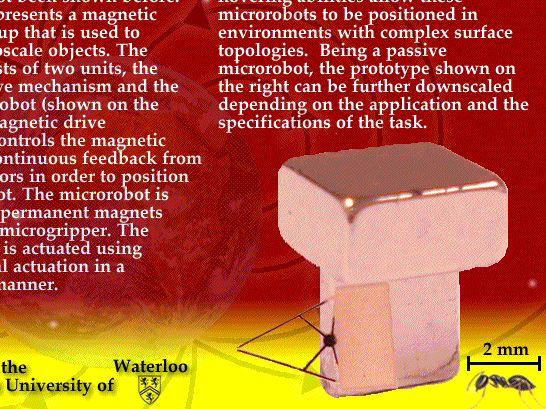
Magnetic levitation is a promising technology that can be used for micromanipulation. Although magnetic levitation has been discussed in manipulation in large scale, its application in micromanipulation as a microrobotic system has not been shown before. This project presents a magnetic levitation setup that is used to levitate microscale objects. The system consists of two units, the magnetic drive mechanism and the flying microrobot. The magnetic drive mechanism controls the magnetic field using continuous feedback from position sensors in order to position the microrobot. The microrobot is composed of permanent magnets attached to a microgripper. The microgripper is actuated using photo-thermal actuation in a non-contact manner.
It has been demonstrated that the system has a positioning accuracy of 13.2 µm in a volume of 3 x 3 x 2 cm3. Micromanipulation of 100 µm diameter objects is demonstrated. Dust-free operation, high manoeuvrability and operability in closed environments are the most important traits of the system.
Flying microrobots have many advantages over crawling, swimming, or walking robots. Advanced hovering abilities allow these microrobots to be positioned in environments with complex surface topologies. Being a passive microrobot, the prototype shown on the right can be further downscaled depending on the application and the specifications of the task.
C. Elbuke, M.B. Khamesee, and M. Yavuz are with the Department of Mechanical and Mechatronics Engineering at University of Waterloo.