Although magnetic levitation is mostly popular with its macro applications such as maglev trains, recently it is being used in the micro world, as well.
Magnetic levitation completely eliminates friction and adhesion that are two big hurdles to be overcome in microscale systems. Our studies focus on magnetic levitation of Micro Electro-Mechanical Systems (MEMS) in an extended air-gap within a large working envelope. Combined with the unique advantage of dust-free operation of magnetic levitation, our systems can be used in micromanipulation in hazardous environments and microassembly of hybrid microsystems.
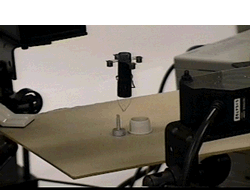
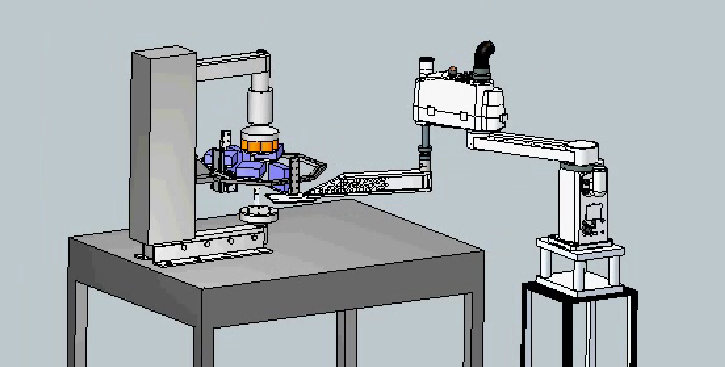
Collaborative micromanipulation: Magnetically navigated microrobots and motorized micromanipulator
This project proposes a novel manipulation system (MM) to perform the compliant and dexterity manipulation of small objects in a confined space. The system consists of a magnetically navigated microrobot (MNM) and a non-ferromagnetic tip held by a motorized micromanipulator (MM) working together to manipulate a tiny object. Both manipulators have three-degrees-of-freedom motion. The MNM is levitated in a 28mm airgap with 10um accuracy. In a manipulation task, the MNM is force controlled with a position-based impedance controller to regulate the holding force on the manipulated object. A magnetic flux measurement-based off-board force determination mechanism was developed to provide feedback force to the impedance controller. The proposed automatic pick-and-place system has a potential application in the field of microinjection as the size of the MNM is downscaled to micrometres. The MNM can be used as the holding equipment, while the motorized micromanipulator can be implemented as the holder of the injector.

Drug delivery and microsurgery in the human body using magnetically driven capsule robots
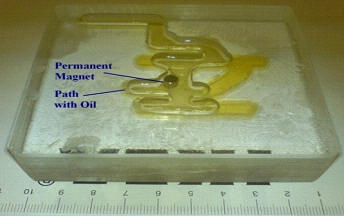
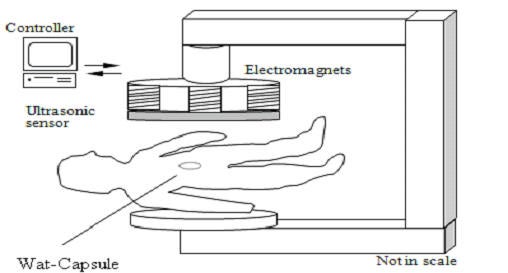
Remote-controlled disposable microrobot to implement toxicity-type laboratory experiments
This research aims at developing a novel technology to remotely manipulate biohazardous materials and specimens during implementation of a laboratory experiment using wireless microrobots.