Variable-structure cable-driven parallel robots (VSCR)
One way that CDPRs can be made variable-structure is by allowing for collisions between cables and fixed rigid objects intentionally placed in the work area: any time a collision occurs along the length of a cable, the effective anchor points of the cable will change, leading to a corresponding change in the dynamic structure of the mechanism.
One of the major advantages of VSCRs is their ability to cover non-convex work areas: a significant relaxation on the constraints of traditional CDPRs. The ability to cover non-convex workspaces is one that greatly enhances the design freedom and the range of applications for which CDPRs can be applied.
One area where this ability is especially useful is for extending the usable workspace in cluttered environments and as a collision avoidance strategy: cables can be made to avoid regions where cable inference would be unsafe by colliding with and bending around a set of permissible objects instead.
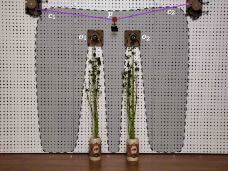
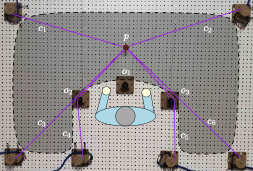