Laser additive manufacturing has emerged as an interdisciplinary technology utilizing the advantageous features of additive manufacturing techniques, laser technology, and computer aided design and manufacturing (CAD-CAM).
Considering the nature of the laser additive manufacturing process, this technique has shown remarkable potential for a wide range of applications from hard facing process and repair of high-value components to rapid manufacturing. Owing to the advances in laser technology, powder metallurgy, sensors, robotics and control, high-speed computers and other related fields, many research groups have been focused to develop this emerging manufacturing technique to its full potential in the last decade.
The special characteristics of the laser additive manufacturing process, namely strong metallurgical bonding with minimal dilution, small heat affected zone and manufacturing process planning step reduction, have offered solutions to the limitations of its comparable conventional techniques such as welding and thermal spraying. Investigations on the mechanical and metallurgical properties of noble additive materials are also being pursued by different research groups parallel to the studies concerned with process developments. In addition, fabrication of components with complex geometry and unconventional structures such as heterogeneous and porous structures that cannot be produced conveniently by traditional techniques are other priorities of research in this field.
Within last ten years, the laser additive manufacturing laboratory at the University of Waterloo has been involved in many research projects in the field of laser additive manufacturing. Laser additive manufacture research areas include modeling and control, coating of hard materials, and applications of the laser additive manufacturing process.
Equipment and facilities
The equipment required for the laser additive manufacturing process are split into the following two setups:
Setup #1
- 1.1 kW fiber laser (IPG)
- Five-axis CNC table (Fadal)
- Powder feeder (Sulzer Metco: TWIN-10-C)
Setup #2
- 1 kW Solid State Nd:YAG laser (LASAG)
- Four-axis CNC table
- Powder feeder (Sulzer Metco: 9MP-CL)
A wide range of facilities for metallography as well as material characterization are also available in conjunction with the material laboratories. See the complete list of available facilities.
Modeling and control
Laser additive manufacturing is a complex process which determines the final properties of deposited materials by several multidisciplinary physical phenomena occurring in the course of melting, solidification and solid-state transformations during the heating and cooling process. For optimizing a large number of operating parameters and designing an efficient control plan to achieve reproducible results with constant properties, understanding these phenomena and their effects is of critical importance. Considering the complexity of laser additive manufacturing, this is not convenient to optimize exclusively by means of the experimental analyses. Hence, numerical simulation of the process beside the experimental analysis is an efficient approach for this purpose. Along with this necessity, one of our main focuses is modeling and control of this process. Our research projects on simulation of the laser additive manufacturing process have resulted in a few unique three dimensional (3D) time-dependent modeling approaches by which the geometry of the additive material deposited on the planar and non-planar surfaces along with the temperature and thermal stresses can be predicted. In addition, several vision-based control systems have successfully been developed and implemented for clad geometry and height control using different methods such as a variable structure controller, feedforward proportional-integral-derivative (PID) controller or the adaptive sliding mode technique.
Coating of Hard Materials
In laser additive manufacturing, high cooling rates can create fine microstructures and consequently produces outcomes with superior mechanical and metallurgical properties. This characteristic of laser additive manufacturing has comprehensively been investigated through its application of hardfacing processes where a wear-resistant surface is required to cover a bulk/base material. In addition, due to the additive nature of laser additive manufacturing, this process has shown a great potential for deposition of Metal Matrix Composites (MMCs) which have demonstrated outstanding performances in high temperature applications. Within the last few years, several hardfacing alloys such as Stellite 1, Ti-45Nb, FeAl, and Ti-C-Fe have been successfully deposited and characterized in our laser additive manufacturing lab.
Applications of the laser additive manufacturing process
Several projects have been conducted on other applications of laser additive manufacturing and its process development/improvement such as characterizations of tungsten carbide laser cladding, repair of cemented tungsten-carbide tools, and investigation on the effect of the preheating process on the deposition of Satellite 1 as a crack-sensitive hardfacing alloy. A complete list of ongoing and past projects and their details is available at the Automated Laser Fabrication Lab website. More information about the commercial applications of laser additive manufacturing is found at Smart Fabrication's website.
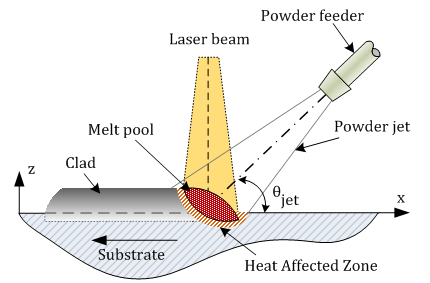
Schematic of the laser additive manufacturing process
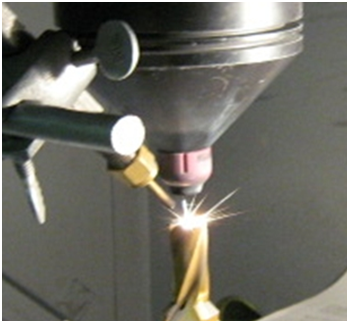
Repair of a drill bit tip using laser additive manufacturing process
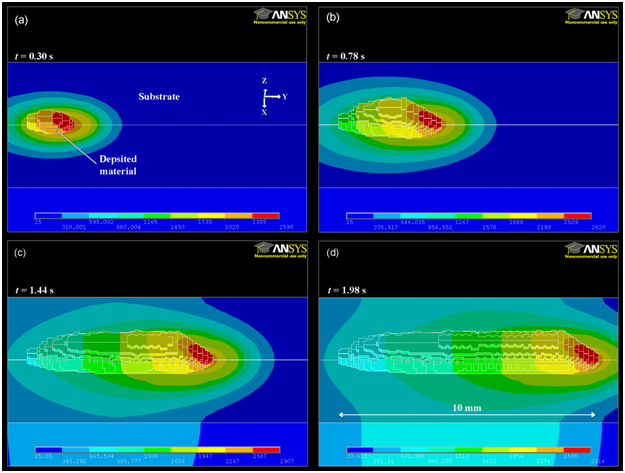
(a to d) Simulation results of a single-track deposition of Ti45Nb on Ti-6Al-4V at 5 mm/s laser scan velocity: dynamic geometrical prediction of the additive material and temporal temperature distribution (°C)
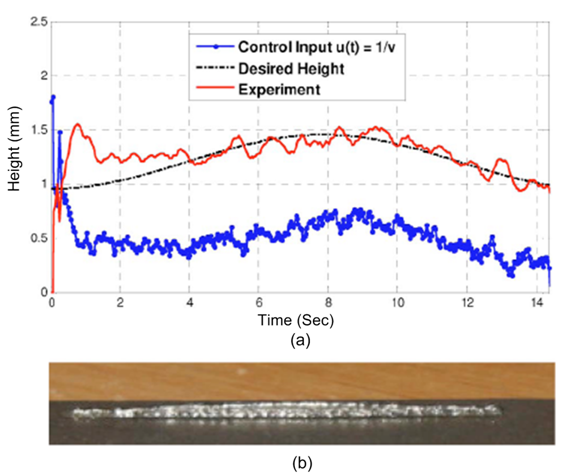
Height control using adaptive sliding mode technique: (a) Control system performance in tracking sinusoidal reference input, (b) A sinusoidal deposited clad - The result of the research is published in Journal of Manufacturing Science and Engineering, v. 132 (4), 2010.
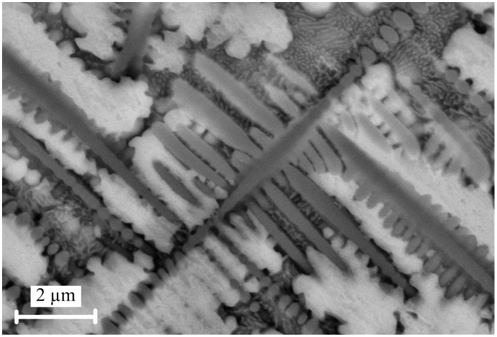
Deposition of Ti45Nb deposited on Mild Steel: Backscatter SEM image of the very fine dendrite structure of Ti45Nb - The result of the research is published in Surface and Coatings Technology, v. 204 (15), 2010.