Air hybrid

Simulation of an air hybrid engine with two storage tanks
The overall objective of air hybrid research is to improve fuel efficiency of combustion engines through air hybrid engine and variable valve train system development. In air hybrid engines, the internal combustion engine is used as a compressor to capture the vehicle's kinetic energy while braking. The compressed air is stored in an air tank and used in the same engine to propel the vehicle via an air motor. This pneumatic hybridization significantly improves the engine’s efficiency and hence reduces emissions. We have achieved significant progress in addressing one of the most important barriers in bringing air-gas engines to the market: the size of the air tank. A novel air hybrid engine has been developed where the size of the air tank can be reduced using the new compression process performed at a much higher pressure, along with the development of a less complex variable valve timing system.
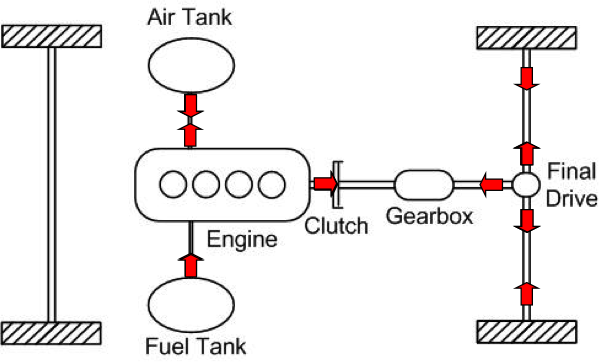
Air hybrid powertrain operation.
A novel compression strategy for air hybrid engines has been developed, designed and tested utilizing two storage tanks: one low pressure (LP) and one high pressure (HP) tank, which increases the efficiency of air hybrid vehicle regenerative braking significantly by increasing the stored air mass and consequently, storing pressure in the tank. In this method air is stored selectively in two tanks instead of a single tank in one revolution of the crank shaft. An experimental setup has also been designed and tested to evaluate the double-tank compression strategy in practice. Our research is currently focused on implementing the technology on a diesel engine.
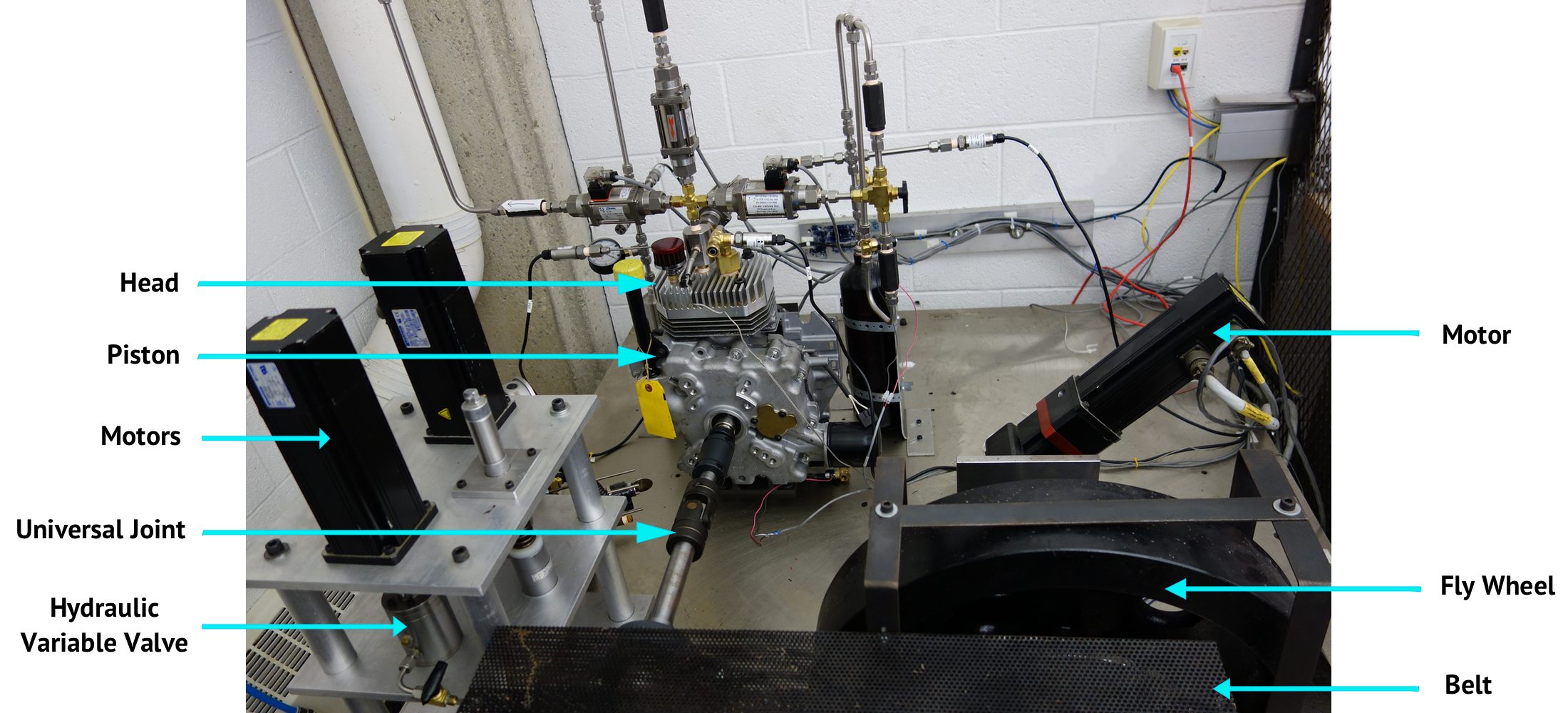
Air hybrid engine prototype
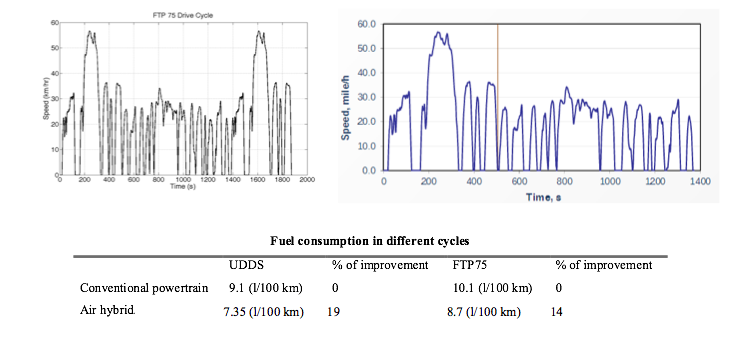
Air hybrid engine drive cycle efficiency results
Variable valve timing (VVT) systems
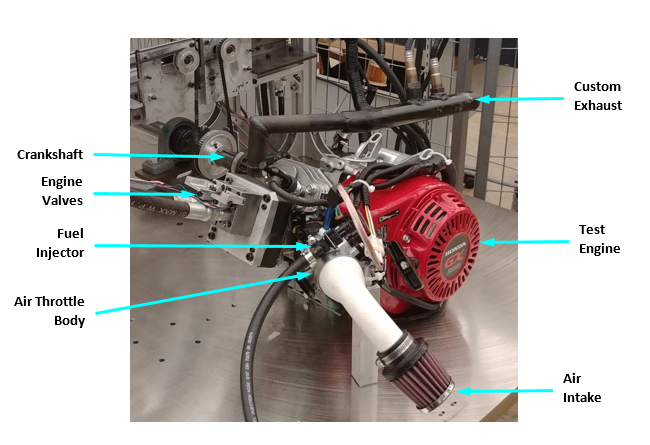
The current model of the VVT system
Engine valve systems have mainly been designed to accurately control the admission and rejection of intake and exhaust gases to the cylinder within each cycle. Throughout decades of engine development, conventional cam-follower mechanisms have been the primary means of controlling valve actuation and timing. In fixed valve systems, the engine valves open and close with fixed maximum lift and timings. Although this design provides reliable and accurate valve operation during various speed ranges, the engine cannot be operated at its most efficient manner over a broad range of speeds and load. In fact, because the dynamic behaviour of gas flow in a cylinder and through a valve varies significantly over different operating conditions, fixed valve timing is a compromised setting for a given design goal and, as a result, some desirable performance characteristics such as minimum emission or fuel consumption are sacrificed for other requirements like maximum power.
Variable valve timing (VVT) systems allows valve timing to be adjusted and optimized based on the engine’s current state. With a VVT system installed, an engine can be tuned to maximize fuel economy at partial load operation with no compromise of power at full load. Common VVT strategies include shifting the valve timings to achieve internal exhaust gas recirculation (IEGR) and using the Atkinson cycle by employing late intake valve closing.
Our team has developed a new hydraulic variable valve actuation (HVVA) system, eliminating the cams, camshaft, and rockers of a traditional internal combustion engine. This system uses a rotary hydraulic spool valves for each engine valve. The spool valves rotate with the crankshaft but can be phased relative to the crankshaft to change the valve timing. The valve lift height can be controlled by adjusting the hydraulic pressure in the system. This system offers fully flexible valve timing and valve lift height.
A more compact version of the HVVA system is in development, with the large engine market in mind. However, this technology has the capacity to provide a large reduction in fuel consumption anywhere the internal combustion engine is currently in use.
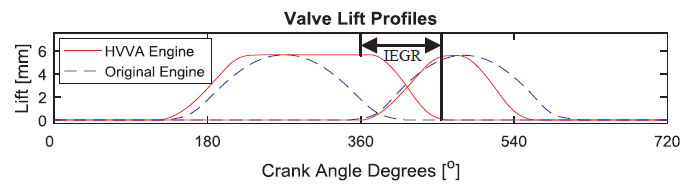
Figure 1 - Engine Valve Lift profiles, the exhaust valve was closed early to retain exhaust gas in the cylinder. This exhaust gas recirculation reduces total air intake and results in lower pumping losses.
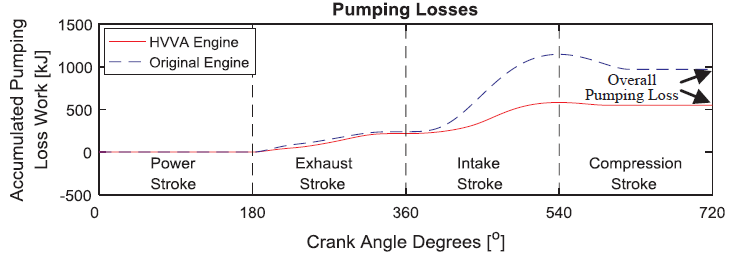
Figure 2 - Reduction in pumping loses when using VVT strategies on a test engine at the MVSL.
This VVT system was recently featured on ASME.org