Even though robotic manipulators are relatively new to industry, they have contributed greatly in the development of the manufacturing industry.
Companies are always seeking faster robots to increase their productivity, and parallel manipulators are capable of offering the speed that companies are looking for with a relatively low cost.
In classic serial manipulators, actuators are embedded in joints and they contribute to the total inertia of the robot, which limits its operation speed. On the other hand, parallel manipulators place all actuators at a stationary base, and the position of the end-effector is driven by a closed kinematic chain. This reduces the effective inertia of the manipulator, allowing faster motion.
The manipulators developed in this project use cables in place of rigid links in parts of the mechanism to further reduce inertia and increase speed. Additional consideration is required to guarantee that cables always have enough tensile force to keep the entire mechanism rigid and reduce structure vibration.
In conclusion, the three primary objectives in this research are:
- Develop a new cable-based parallel mechanism with low moving inertia. Explore novel design procedures to optimize design factors such as size of the workspace and link geometry.
- Develop new controllers or improve current motion control techniques for the robot. Current commercial motion control techniques are for rigid body motions and are not capable of producing satisfactory results for systems susceptible to vibrations.
- Develop computer programs for the ultra high-speed robot with enhanced graphical user interfaces for path planning, design and simulation.
Industrial applications - warehousing robotics
The attributes of cable-based robots provide an advantage over conventional robots in industrial applications. The reduction in inertia allows the cable-based robot to pick and place of objects inside factories or similar exterior large workspaces more effectively. However, the properties of cables create challenges including mobile platform collapsing and unacceptable oscillations during operation. To address these problems, the design and control of fully constrained cable-based robots with parallel manipulator are studied. For this type of robot, the motion and force generation of the mobile platform is accomplished by controlling both the cable lengths and the positive cable tensions. They are also dependent on actuator redundancy, which is proved beneficial to expand the workspace, remove some types of singularities, increase the overall stiffness, and support high payloads in several proposed cable-based robot designs. The goal of this research is to investigate fully constrained cable-based parallel manipulator and to gain insight into large-scale high-speed warehousing applications.
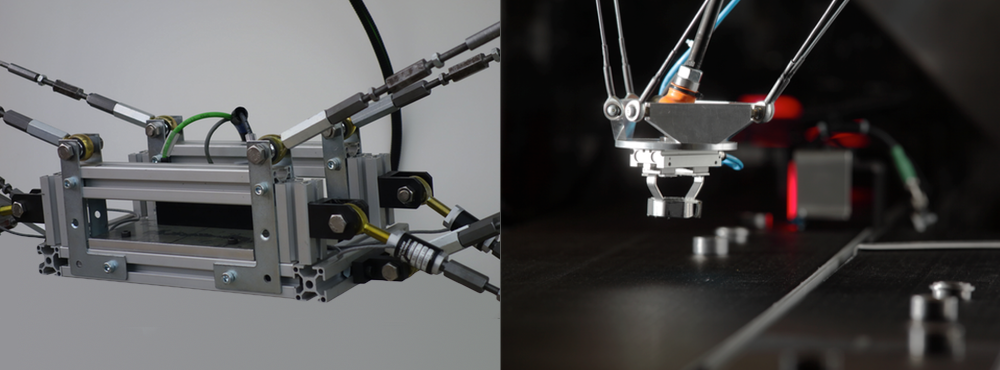
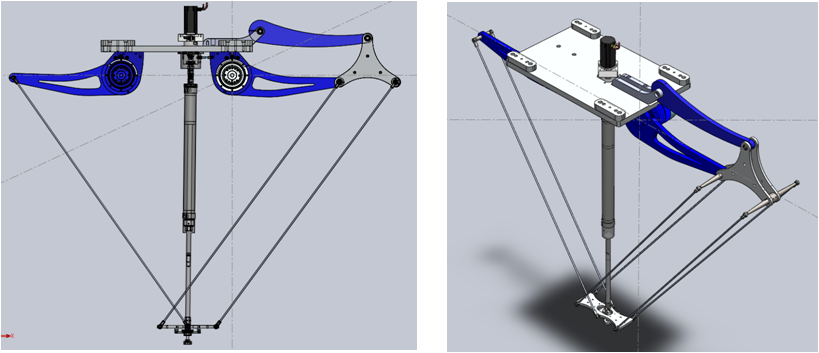
Parallel manipulator with all actuators at stationary base
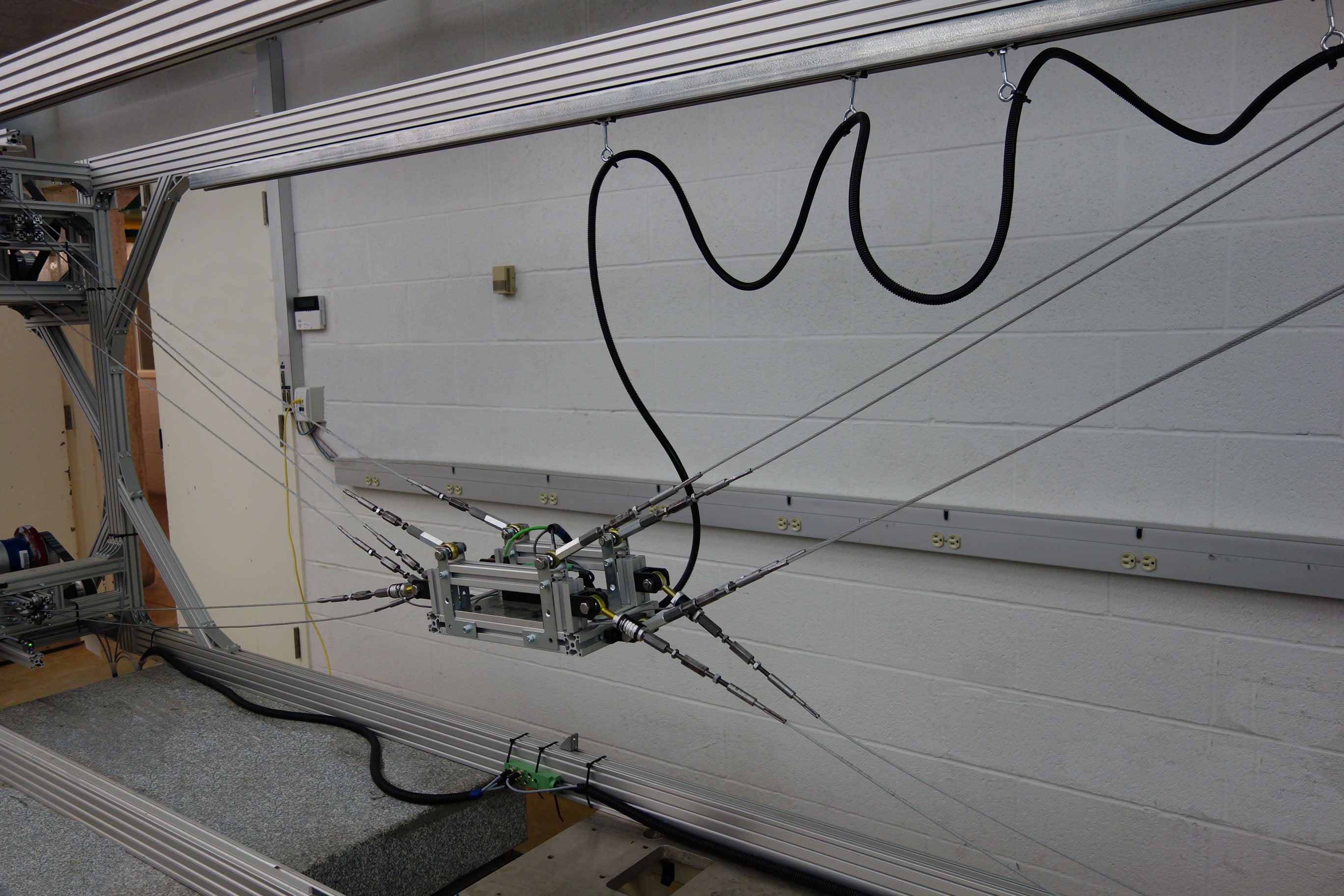
Warehousing robot prototype
Commercial applications - AEMK systems
High-speed robotics has the potential to improve automation, assembly, and packaging processes in a wide range of industries. The AEMK Systems DeltaBot uses a patented cable actuated design to produce leading edge speed, accuracy, and reliability. The high-speed robot is also easy to assemble and integrate into industrial systems due to its flexible control system. The DeltaBot is also available with integrated vision systems that can be used in parts inspection, feature detection, component identification, and sorting. For more information on the DeltaBot and its specifications, please visit the AEMK Systems website.