Background
Boundary conditions are extremely important for simulating/optimizing fluid flow and heat transfer in heat exchanger designs. Improving performance of heat exchangers requires greater freedom in the design process, which is computationally demanding and imposes manufacturing challenges.
Conventional optimization methods, that keep the heat exchanger boundaries distinguishable, are based on pixel or voxel optimization which require high CPU time due to the complexity of multidimensionality. Additionally, as the conventional methods/software packages start from limited pre-defined heat sink fin geometries, the final design/output may face manufacturing challenges and/or optimality issues (i.e. may be a local optimum but not an absolute optimum).
Description of the invention
Researchers at the University of Waterloo have invented a fast and non-restrictive method for optimizing the shape of heat exchanger fins that reduces the dimension of the optimization problem without sacrificing manufacturability or freedom to change the heat exchanger design.
The methodology uniquely utilizes Deep Reinforcement Learning (Deep RL) and Boundary Representation (BREP) algorithms and automatically designs/simulates heat exchanger fins and layouts based on the “physics” of each use-case. The designer is only required to input/define the “design space”, i.e. the boundaries of heat exchanger’s solid components, and thermodynamic parameters, i.e. temperatures and heat flux. The system then optimizes the shape of heat exchanger fins for maximum heat transfer and minimum fluid pressure drop.
Advantages
- Easy to use (convenient) and fast (is not computation intensive).
- Provides customized optimal designs (is not a “one size fits all”).
- 30% improved heat transfer and 60% reduction in pressure drop
- Manufacturable designs
- Seamless interaction with CAD software
Potential applications
The invention can potentially be used for designing/simulating any heat exchanger system, including for:
- Consumer electronics
- Data centers
- HVAC systems
- Electric Vehicles

Deep RL workflow with parallel Computational Fluid Dynamics environment
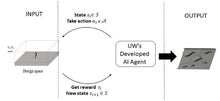
Schematics for heat exchanger generative design
Reference
10209
Patent status
Patent Pending
Stage of development
Lab prototype and
Ongoing research
Contact
Scott Inwood
Director of Commercialization
Waterloo Commercialization Office
519-888-4567, ext. 43728
sinwood@uwaterloo.ca
uwaterloo.ca/research