Layout Generation
This chapter presents a basic example of MEMS relay to illustrate the UW-MEMS layout generation step-by-step for designers. Experienced designers typically use tools such as L-EDIT and Cadence to generate the layouts for the various layers. However, any tool that can generate layouts in GDSII formats can be used to submit designs to UW-MEMS. This example is given to provide beginners in the field with layout illustrations to help them understand the guidelines given in chapter 2.
Consider the MEMS relay shown in Figure 3.1. The relay consists of a cantilever beam anchored to an input signal line. The cantilever can be pulled down using electrostatic actuation so that its tip makes contact with the output signal line and hence closes the relay. The actuation is performed using a pad covered by SiO2 (i.e. dielectric). The two DC bias pads are connected to the actuation pad and the input signal line using high resistivity TiW traces. A dimple is added to the cantilever tip to ensure contact with the output signal line. Below is a description of the seven masks used for production of a MEMS relay based on the nine layout layers detailed in chapters 1 and 2.
- Fig. 3.2a shows the layout of Mask #1 (produced from “TiW” layer). This mask shows the two high resistivity traces that connect the DC bias pads to the actuation pad and the input signal line. The mask is “Light Field”. Note that the TiW traces must be made at least 20 µm longer on each side in order to overlap the gold (see Design Rules: Overlaps & Enclosures).
- Fig. 3.2b shows the layout of Mask #2 (produced from “D1” and “D1HOLE” layers). This mask shows the insulation layer that covers the bias lines. The mask is “Light Field”.
- Fig. 3.2c shows the layout of Mask #3 (produced from “G1” layer). This mask shows the input/output signal lines, actuation electrode and the two bias pads. The mask is “Light Field”.
- Fig. 3.2d shows the layout of Mask #4 (produced from “D2” layer). This mask shows the insulation layer that covers the actuation electrode. The mask is “Light Field”.
- Fig. 3.2e shows the layout of Mask #5 (produced from “A” layer). This mask defines the anchor location for connection of G2 and G1 metals. The mask is “Dark Field”.
- Fig. 3.2f shows the layout of Mask #6 (produced from “D” layer). This mask defines the dimple location which is connected to the tip of the cantilever. The mask is “Dark Field”.
- Fig. 3.2g shows the layout of Layer #8 (“G2”). This layer shows the cantilever. The layer is “Light Field”. Besides, Fig. 3.2h shows the layout of Layer #9 (“G2R”) that is “Dark Field”. This layer will be subtracted from “G2” layer mask by CIRFE personnel to generate the Mask #7.
Note:
The
cantilever
length
needs
to
be
extended
at
the
anchor
location
in
order
to
make
sure
that
“G1”
and
“G2”
enclose
“A”
(see
Design
Rules:
Overlaps
&
Enclosures).
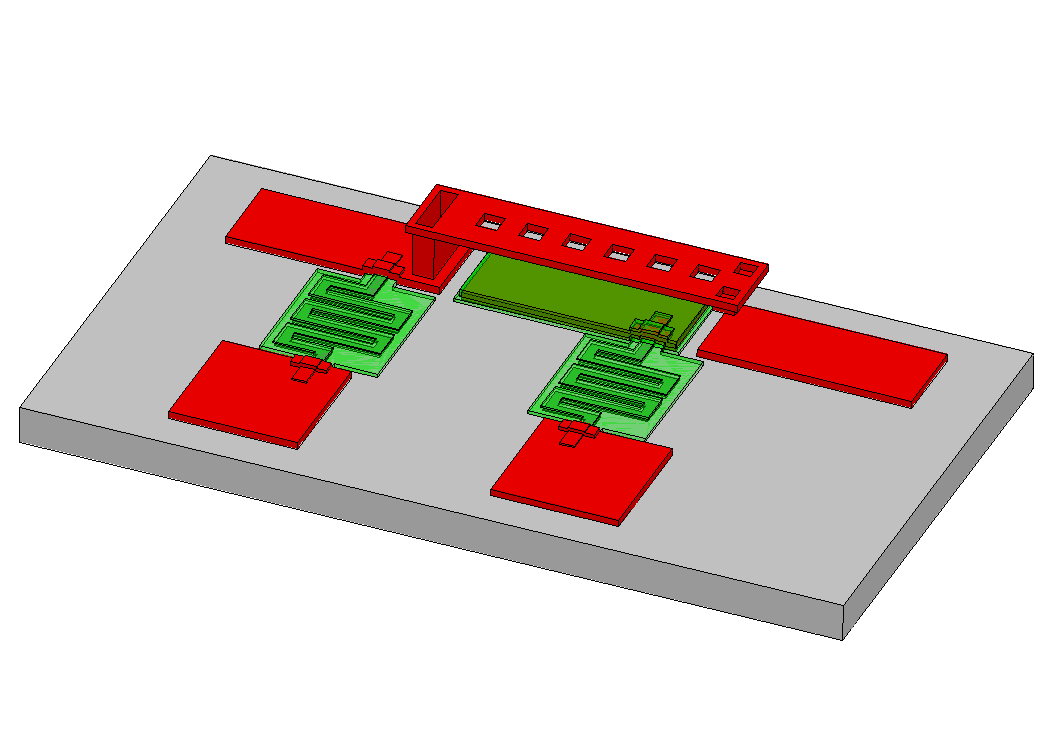
Figure 3.1: A MEMS Relay
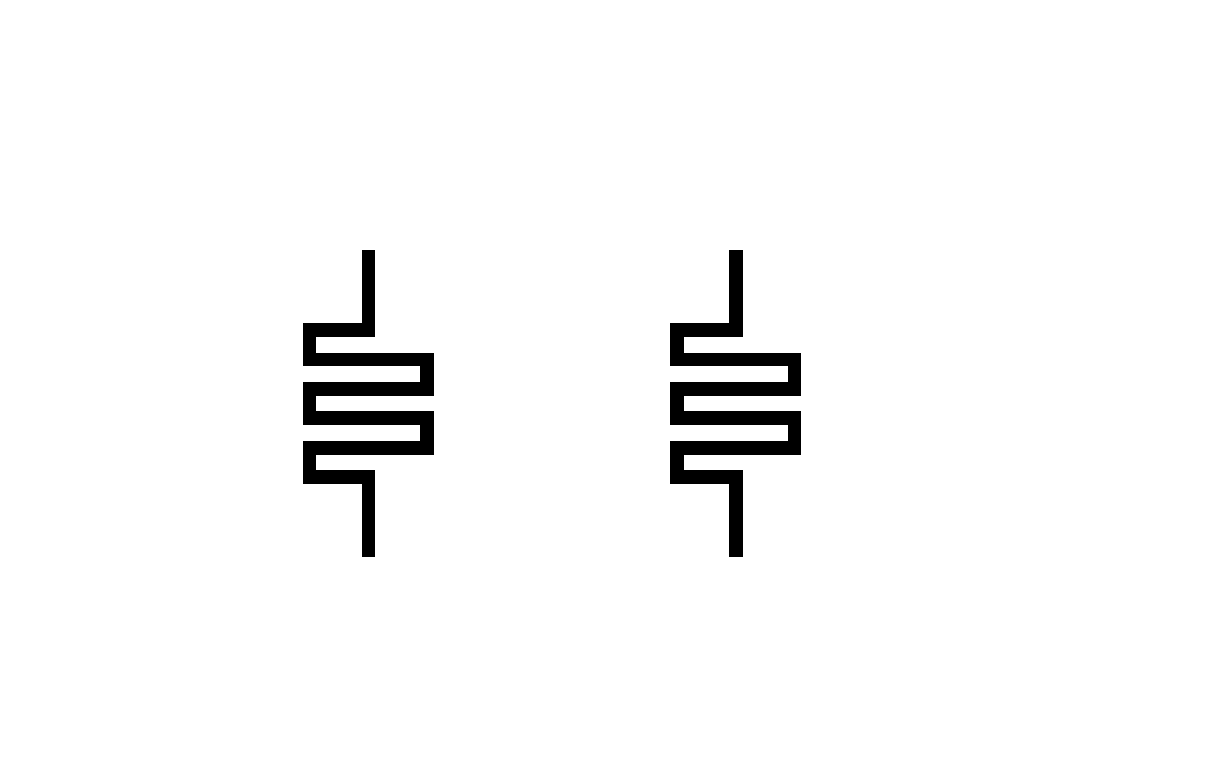
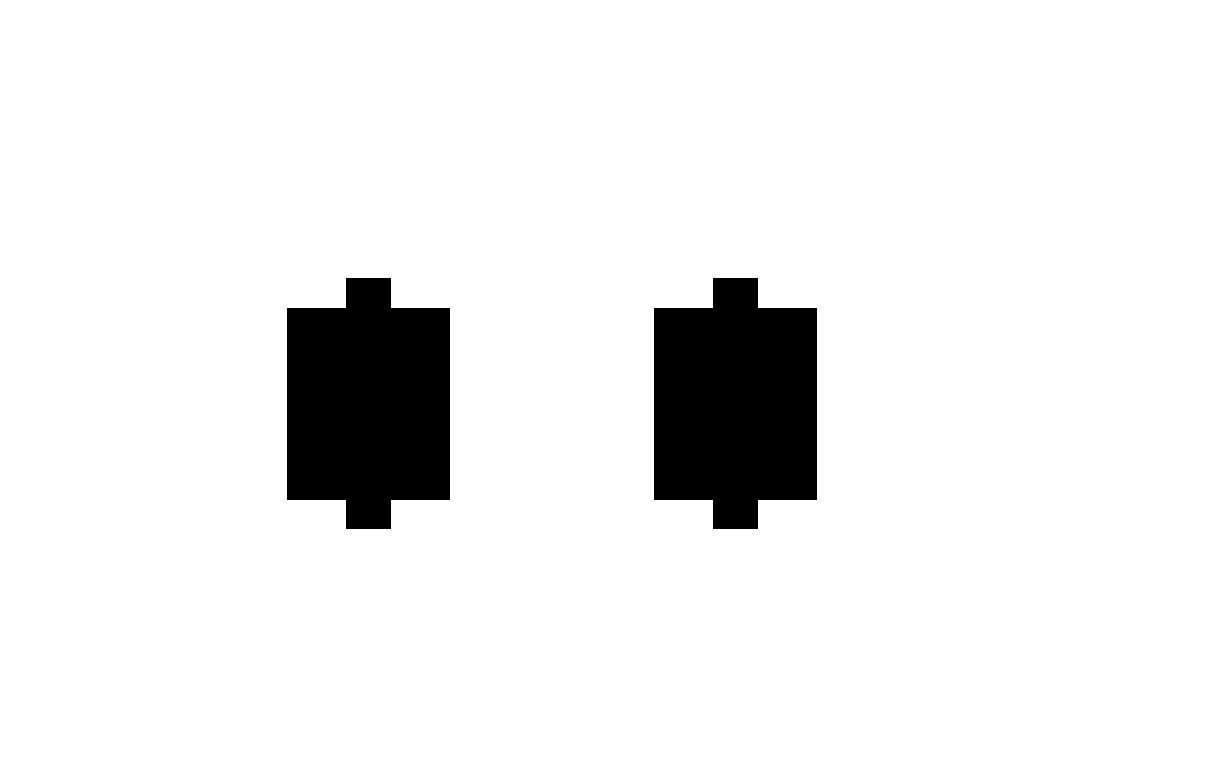
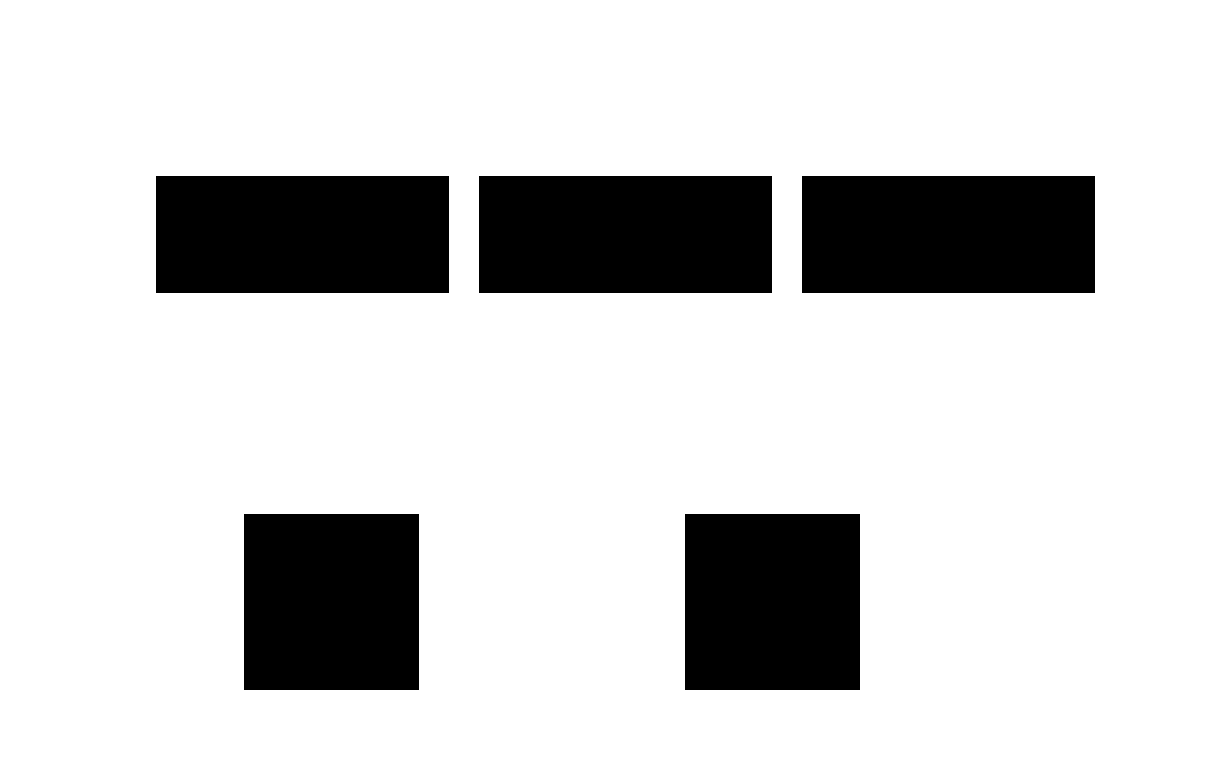
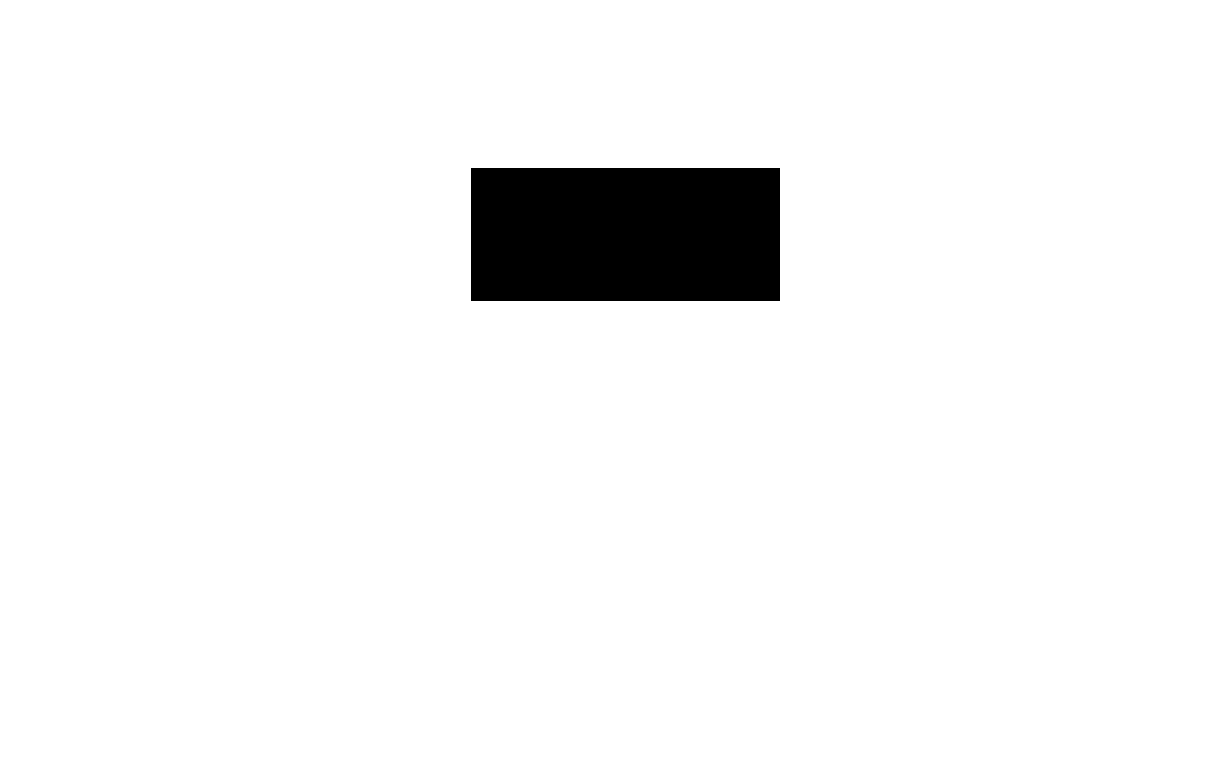
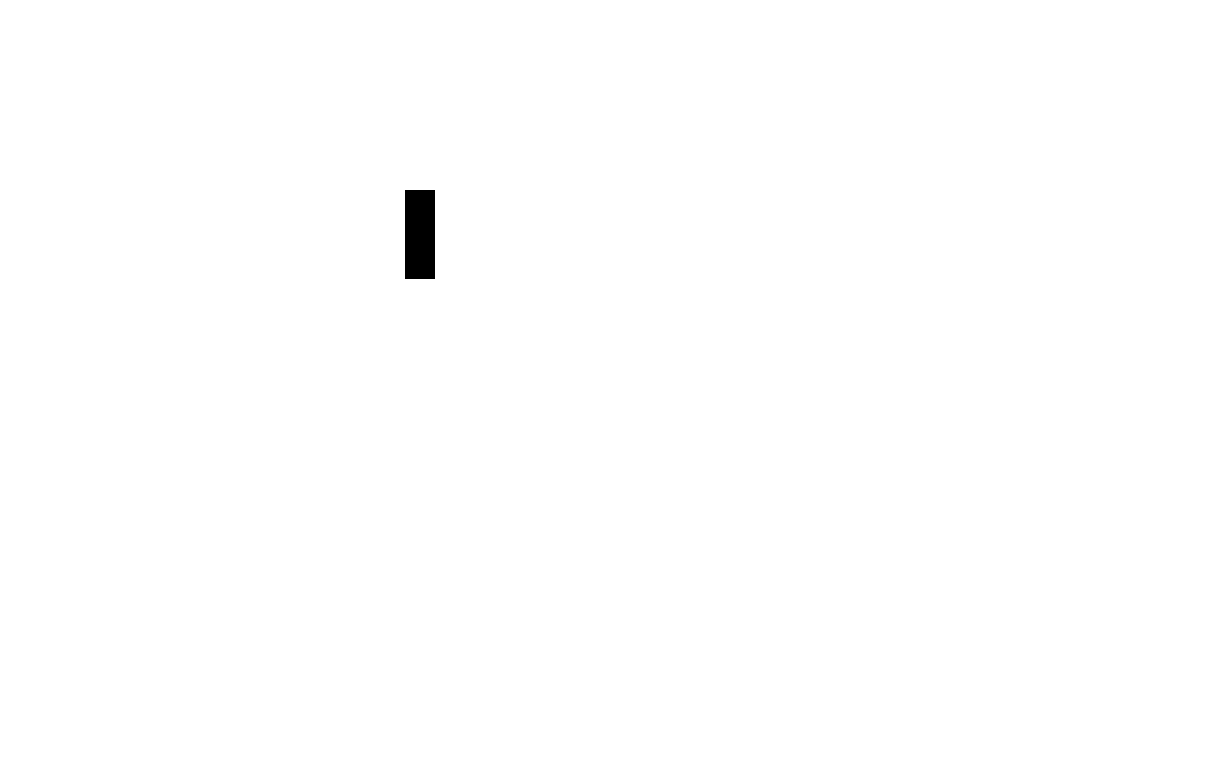
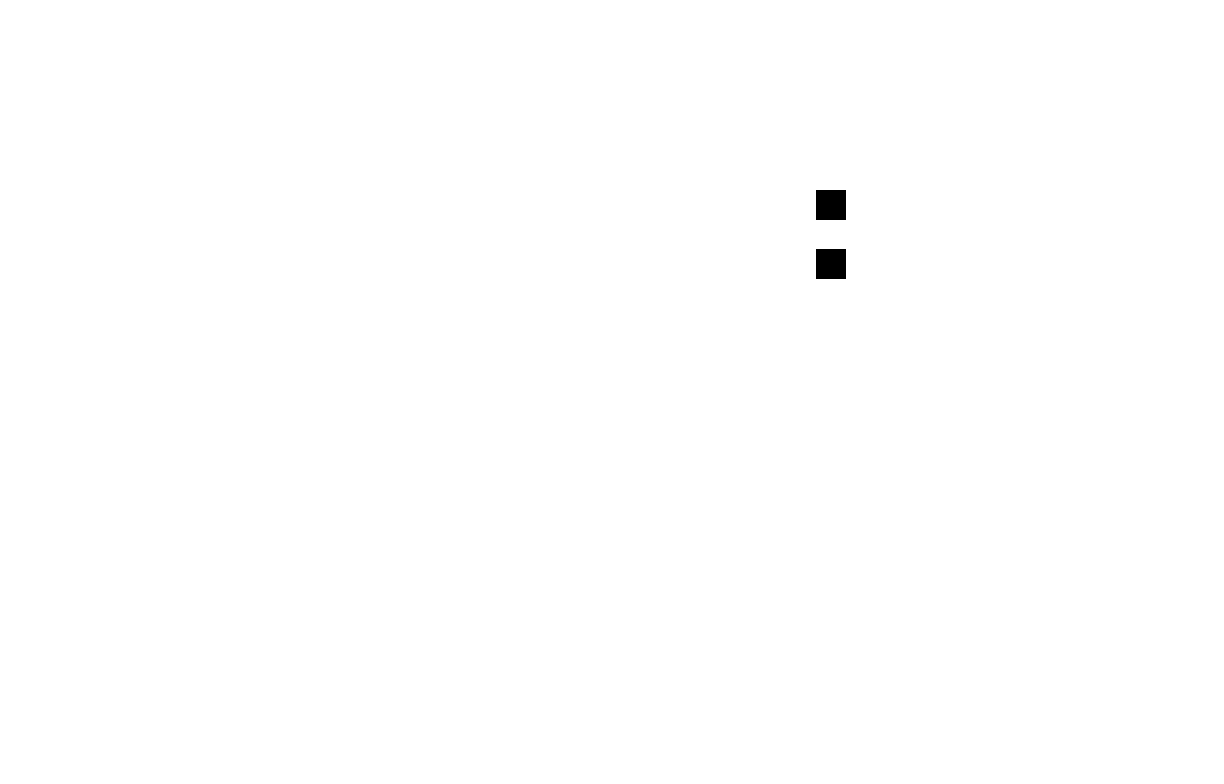
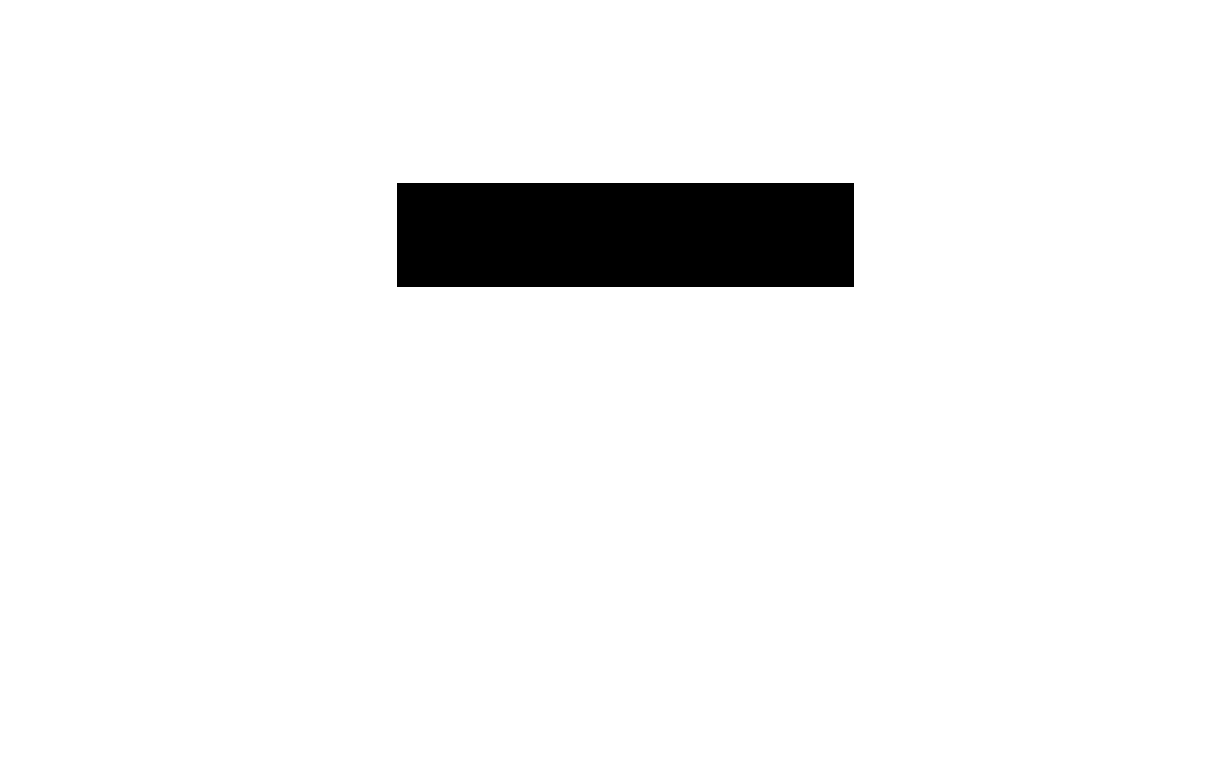
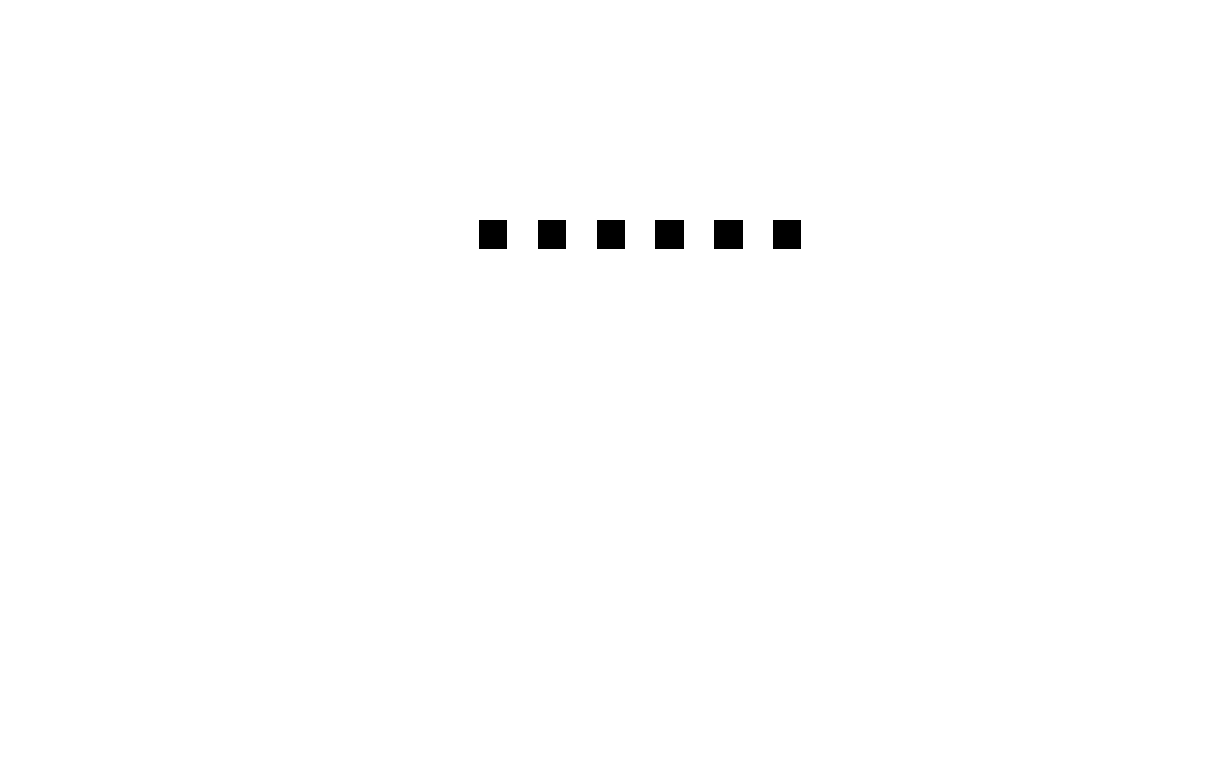