Introduction
These design guidelines and rules were determined during the process development stage and several microfabrication runs carried out at CIRFE cleanroom facility. The rules identify the physical and geometrical limitations of individual process steps. The herein presented guidelines are extremely important and must be considered at the design stage. If the guidelines are not followed closely by UW-MEMS users, the fabricated devices will not meet the specifications and will probably fail or malfunction.
In general, there are two types of rules. The first type of rules specifies the minimum feature sizes and minimum feature separation distances within a single layout layer, i.e. intra-layer design rules. The minimum feature size refers to the minimum side length of a trace that is feasible using UW-MEMS. In other words, if this rule is violated there is no guarantee that the feature will be produced on the wafer. Similarly, the minimum separation distance between adjacent features must comply with the design rules in order to be feasible. Failure to follow the minimum spacing design rule results in a merged feature.
The second type of design rules specifies the inter-level crossovers (overlaps) and separation distances. This is mainly imposed by the inevitable relative misalignment of the different layout layers throughout fabrication, and it will be shortly detailed. Both types of design rules are considered mandatory and should be followed closely by the designer.
Design Rules: General Outlines
The layout design rules for the UW-MEMS process are explained in the following tables and illustrated in schematic format following the tables. First, Table 1 outlines the different layer names, corresponding material thicknesses as well as layer numbers and description.
Table 1: Layer Names, Material Thicknesses, Layers Order, Layer Description and Comments
Layer Name | Material Thickness | Layer Order | Layer Description | Comments |
---|---|---|---|---|
“TiW” | 50nm | 1 | Resistive Voltage Biasing | Resistive Layer |
“D1” & “D1HOLE” | 0.7µm | 2 & 3 | Dielectric | 0.7µm SiO2 to cover the bias lines |
“G1” | 1µm | 4 | Conductive Layer | 40nm evaporated Cr + 70nm evaporated Au + 0.9µm electroplated Au |
“D2” | 0.7µm | 5 | Dielectric | 50nm TiW + 0.7µm SiO2 |
“A” & “D” | 2.5µm | 6 & 7 | Sacrificial Layer | 2.5µm Anchor and 1µm Dimple openings |
“G2” & “G2R” | 2µm | 8 & 9 | Conductive Layer | 70nm sputtered Au + 1.9µm electroplated Au |
Table 2 outlines the layers that are used during the microfabrication process. Please note that for the case of “Light Filed”, you draw the features that you want to be remained on the wafer. For example, for TiW layer patterning, you draw the features or traces such as bias lines. For the “Dark Field”, you draw the parts you want to be removed from the corresponding layer such as release holes or openings for anchors and dimples. Please pay special attention to this concept. Failure to do so will result in a reverse polarity devices.
In other words, for D1HOLE and G2R, you draw only the location of dielectric openings and release holes in gold, respectively. These layers will be subtracted from the D1 and G2 layers by CIRFE personnel prior to printing the second and seventh lithographic masks.
Table 2: Layer Names, Layer Polarity Type and Comments
Layer Names | Polarity | Comments |
---|---|---|
“TiW” | Light Field | Patterning TiW |
“D1” | Light Field | Patterning D1 without openings |
“D1HOLE” | Dark Field | Additional layer for openings on the D1 layer |
“G1” | Light Field | Patterning G1 |
“D2” | Light Field | Patterning D2 |
“A” | Dark Field | Opening anchors between G1 and G2 |
“D” | Dark Field | Dimples of G2 for contacts of the switches as well as preventing the stiction of large plates |
“G2” | Light Field | Patterning G2 |
“G2R” | Dark Field | Additional layer for release holes of the G2 layer. |
Table 3 presents the lithographic mask numbers with the respective GDSII indices of their constituting layout layers. GDSII is the only format that UW-MEMS accept from all users. Please use the GDSII numbers that are specified in the table for each layout layer to avoid confusion. Layers D1HOLE and G2R are just employed to create the openings in the D1 layer and the release holes in G2 layer, respectively. No lithographic masks are printed specifically for these layers. Please note that the dimples are meant for small features. Nominal surface area is 10µm by 10µm. However, they can be used for long lines, but it is recommended that the width of the lines be 10µm.
Table 3: UW-MEMS Masks and GDSII Layer Indices
Lithographic Mask | Layer Name(s) | GDSII Index |
---|---|---|
Mask #1 | TiW | 101 |
Mask #2 | D1 – D1HOLE | 102 - 110 |
Mask #3 | G1 | 103 |
Mask #4 | D2 | 104 |
Mask #5 | A | 105 |
Mask #6 | D | 106 |
Mask #7 | G2 – G2R | 107 - 109 |
Design
Rules:
Overlaps
&
Enclosures
Generally, the following guidelines should be considered:
- For overlaps and enclosures of the layers, up to 10mm of misalignment between the layers is assumed. This is due to the limitations of our photolithography system. This is an advisory design rule.
- TiW lines are designated for the DC bias lines with no current flow. This layer is very thin, and it is not intended for power transfer.
The following outlines the specific layout design rules to which close attention must be paid. It is worth emphasizing that the minimum feature size and minimum spacing between features are limits to which the designers should strictly adhere. Ideally, adding a 10mm additional safety margin to these numbers may increase the yield of fabrication. Users can have round, orthogonal or any arbitrary shape in your layout. The release holes must be 10mm x 10mm squares with edge to edge distances not exceeding 20µm. Please do not use this layer to define geometries. The features are embedded to provide access to underneath the structural layer during the release purposes.
1. “TiW” resistive DC bias lines:
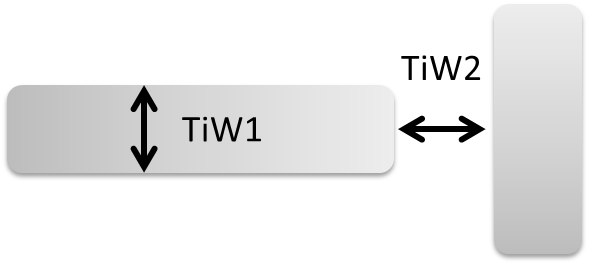
Description |
Rule
Label
|
Value
(µm)
|
---|---|---|
Width/Length of TiW | TiW1 | ≥ 10 |
Spacing of TiW | TiW2 | ≥ 10 |
2. First Dielectric “D1” stacked with “TiW” and Gold “G1”:
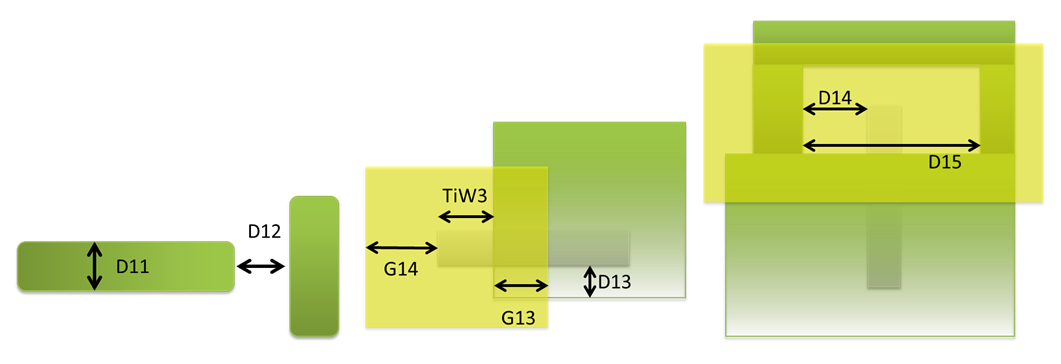
Description |
Rule
Label
|
Value
(µm)
|
---|---|---|
Extension of TiW from D1 | TiW3 | ≥ 20 |
Width/Length of D1 | D11 | ≥ 15 |
Spacing of D1 | D12 | ≥ 15 |
Overlap of D1 with TiW | D13 | ≥ 5 |
Extension of D1HOLE from TiW | D14 | ≥ 10 |
Width/Length of D1HOLE | D15 | ≥ 35 |
Overlap of G1 pad with TiW or D1 | G13 | ≥ 15 |
Overlap of G1 pad with TiW | G14 | ≥ 10 |
Note: TiW lines MUST be always covered with D1, G1, or both.
3. First Gold “G1”:
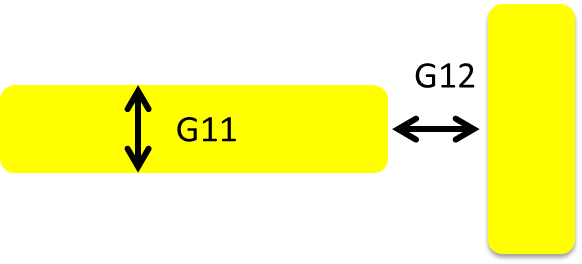
Description | Rule Label | Value (µm) |
---|---|---|
Width/Length of G1 | G11 | ≥ 10 |
Spacing of G1 | G12 | ≥ 10 |
4. Second Dielectric “D2” on top of TiW adhesion layer:
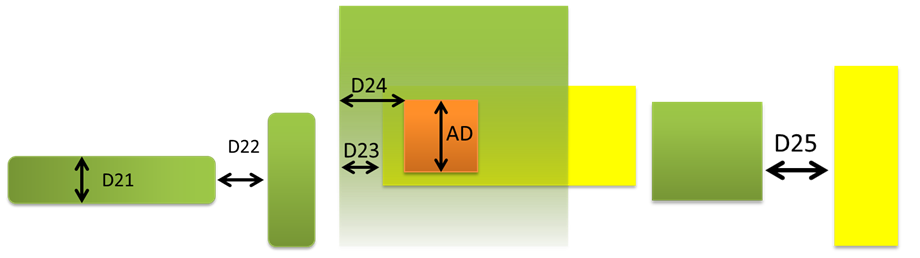
Description | Rule Label | Value (µm) |
---|---|---|
Width/Length of D2 | D21 | ≥ 15 |
Spacing of D2 | D22 | ≥ 15 |
Overlap of D2 with G1 | D23 | ≥ 10 |
Overlap of D2 with A | D24 | ≥ 15 |
Spacing of D2 from G1 | D25 | ≥ 15 |
Feature size of A over D2 | AD | ≤ 200 |
Note: D2 over 2 separated trances MUST be separated.
Note: Anchor on top of D2 cannot be used as mechanical support but can be used for Metal-Insulator-Metal (MIM) capacitor.
5. Anchor “A” Openings:
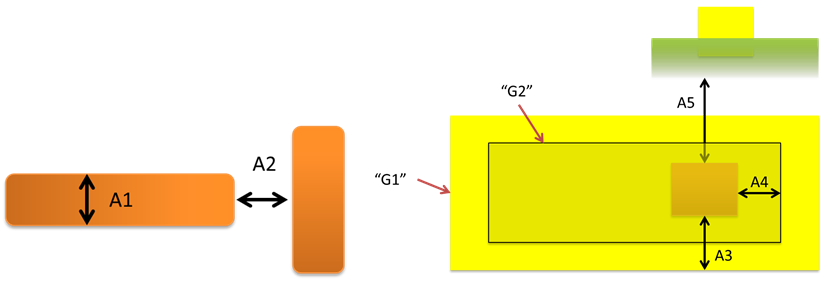
Description | Rule Label | Value (µm) |
---|---|---|
Width/Length of A | A1 | ≥ 10 |
Spacing of A | A2 | ≥ 10 |
Overlap of G1 with A (A MUST be covered with G1) | A3 | ≥10 |
Overlap of G2 with A (A MUST be covered with G2) | A4 | ≥ 5 |
Spacing of D2 from A | A5 | ≥ 10 |
6.
Dimple
“D”
Openings:
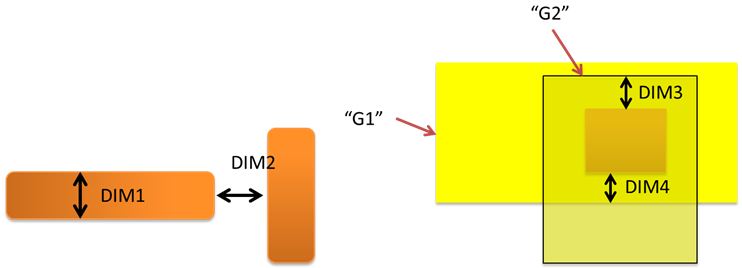
Description | Rule Label | Value (µm) |
---|---|---|
Width/Length of D | DIM1 | ≥ 10 |
Spacing of D | DIM2 | ≥ 10 |
Overlap of G2 with D | DIM3 | ≥ 5 |
Overlap of G1 with D | DIM4 | ≥ 5 |
7. Second Gold “G2”:
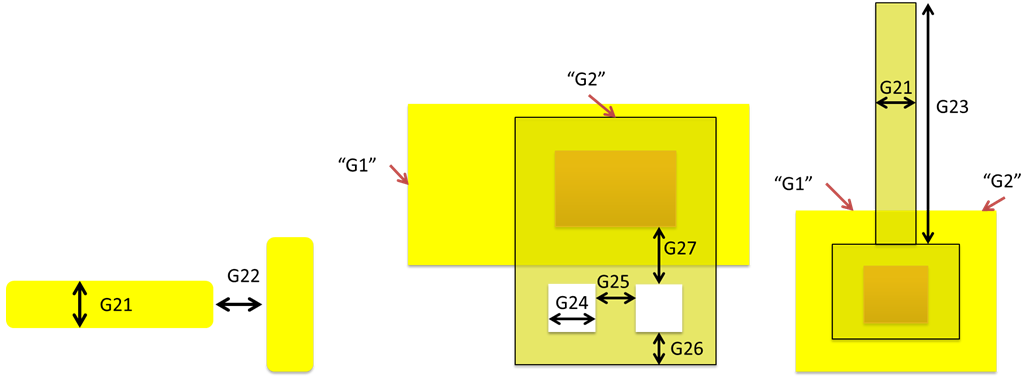
Description | Rule Label | Value (µm) |
---|---|---|
Width/Length of G2 | G21 | ≥ 10 |
Spacing of G2 | G22 | ≥ 10 |
Ratio of G23/G21 when G2 is not anchored to G1 | G23/G21 | ≤ 30 |
Non-anchored length of G2 | G23 | ≤ 1200 |
Width/Length of G2R | G24 | ≥ 10 |
Spacing of G2R (edge-to-edge) | G25 | ≥ 20 |
Spacing of G2R from G2 edge | G26 | ≥ 10 |
Spacing of G2R from A | G27 | ≥ 10 & ≤ 30 |
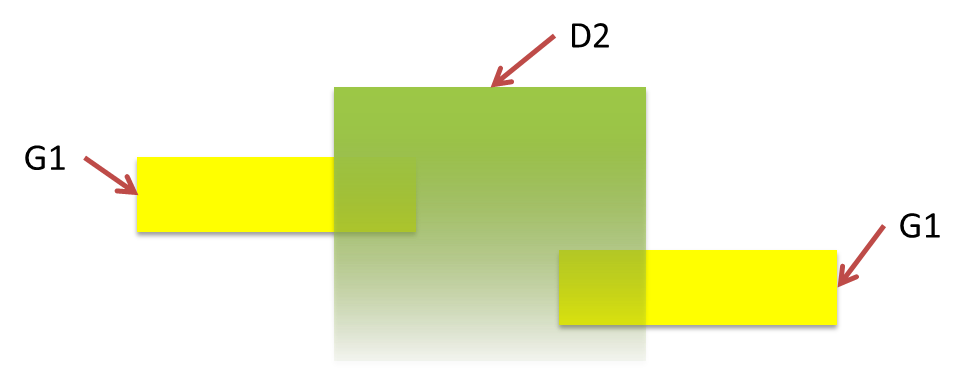
Note: This configuration results in short-circuit between the two G1 traces due to the conductive TiW thin layer underneath the D2 layer.
9. Caution 2:
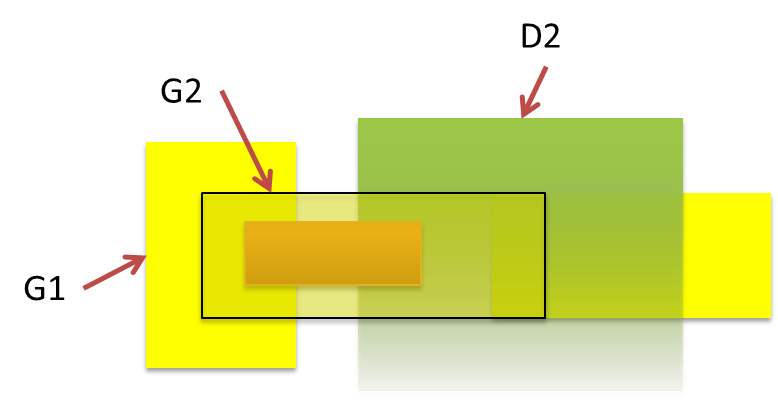
Note: This configuration may result in short-circuit between the G1 and G2 traces through D2 layer.
Material Properties
Table 4 reports some of the mechanical and electrical properties of the UW-MEMS process. The data is based on the measurements performed on earlier UW-MEMS processes and agree well with the nominal known values in the literature. Designers can use the existing values in the literature for the other material properties.
Table 4: Physical properties of UW-MEMS materials
Material |
Residual
Stress (MPa) |
Conductivity (Ω-1/m) |
Sheet
Resistance (Ω/□) | Relative Permittivity |
---|---|---|---|---|
TiW of Resistive Bias Lines | ------ | ------ | 20* | ------ |
SiO2 of D1 and D2 | ------ | ------ | ------ | 4 |
Au of G1 and G2 |
190 +/- 30% Tensile | 3.6х107 | ------ | ------ |
*Higher resistivity (500Ω/□) will be optionally available.