Design Team Members: Alfred Tsang, Mehran Malek
Supervisor: Professor Fieguth
Background
Steel lamination defects are surface inconsistencies that compromise the function of steel parts. Steel laminations, also referred to as slivers or scales, are surface inconsistencies that occur in the manufacturing process of steel sheets and rolls. Due to the stampings process, however, some laminations are more exaggerated on the final formed part than the original sheet metal. A result of this is the need to examine for defects on the final formed part. The part that this system is being developed for is used in the rack and pinion steering system of the popular Chrysler minivans and is shown to the right. The project is being completed for Woodstock Stampings which is a manufacturer of steel stamped parts for the North American automotive industry.
Project description
The purpose of this project is to design and develop a machine vision system for the detection of steel lamination defects.
Design methodology
Qualitative and quantitative analysis was performed in order to model the lamination. Features were identified and measured through various methods of image processing techniques. Research thus far has included image manipulation, filtering, edge detection techniques and image subtraction. Also, image processing techniques such as frequency transforms, wavelets, Hough transform and Gabor filter have also been investigated.
Factors like camera angle, image resolution, colour, illumination, shadows, and noise were required to be analysed. The concave and convex natures of the objects' sides further complicate the system..
When suitable techniques have been identified, feature selection will be required, followed by feature classification.
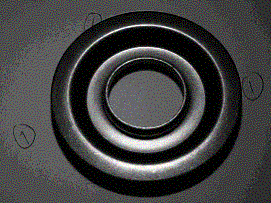
Figure 1. Original Image
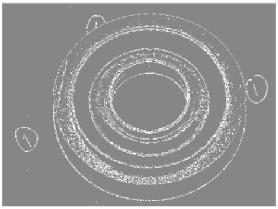
Figure 2. Edges of image.
A lamination can be seen on the left hand side.