General Use Policy
The CNC machines in the Architectural Engineering Maker Space (AEMS) shop are intended to be used primarily by the Architectural Engineering (AE) program for academic projects. If no AE students need the machines, they are open for use by other members of the University community for academic or work purposes.
The following guide is meant to give the reader an overview of the key concepts and process of CNC work in AEMS. CNC (Computer Numeric Control) processes can take many forms, and while some of the principles in this manual will universally apply to all CNC machining, most of the specifics are for the type of machining that we perform in AEMS. The nature of CNC is that every project is unique and presents its own challenges. For this reason, the operation of the machine is restricted to AEMS staff only.
Equipment Specs
AEMS has two CNC milling machines:
The first is a 3-axis AXYZ mill with a bed size of 60” x 48” (1500mm x 1200mm) and vertical clearance of 12” (300mm). It is equipped with a 7-position tool changer and vacuum table. It is capable of machining through parts up to 8” (200mm) thick and is able to machine foam, wood and some plastics.
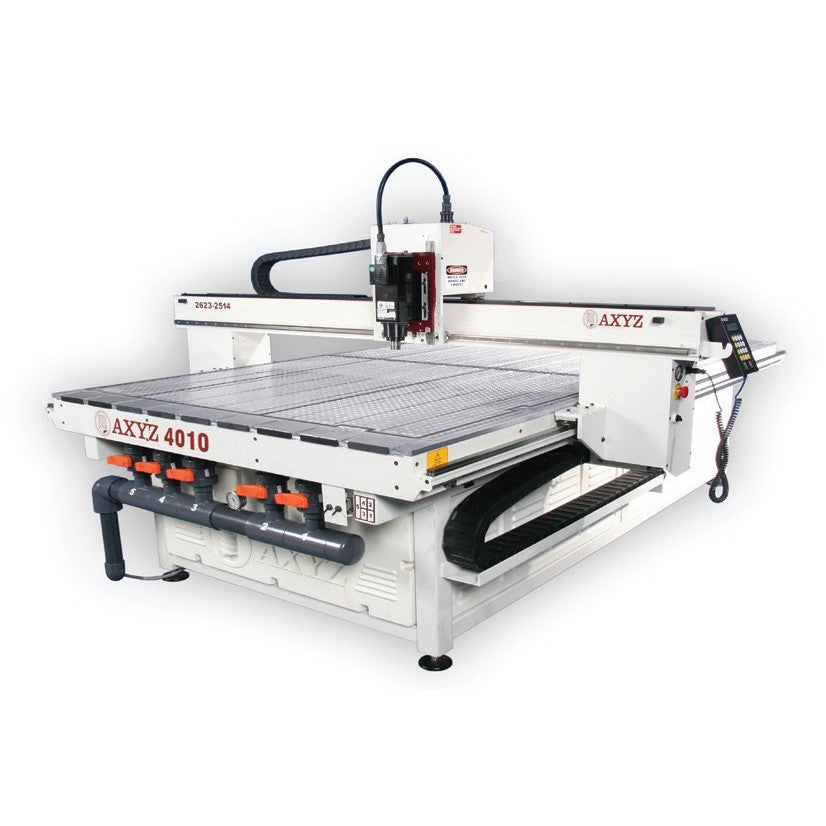
AEMS also has an AXISWORKS 5-axis CNC for performing light duty work that the 3-axis machine cannot reach. Its working area is a cubic 24” (600mm). This machine is meant for lightweight materials only, this primarily means foam.
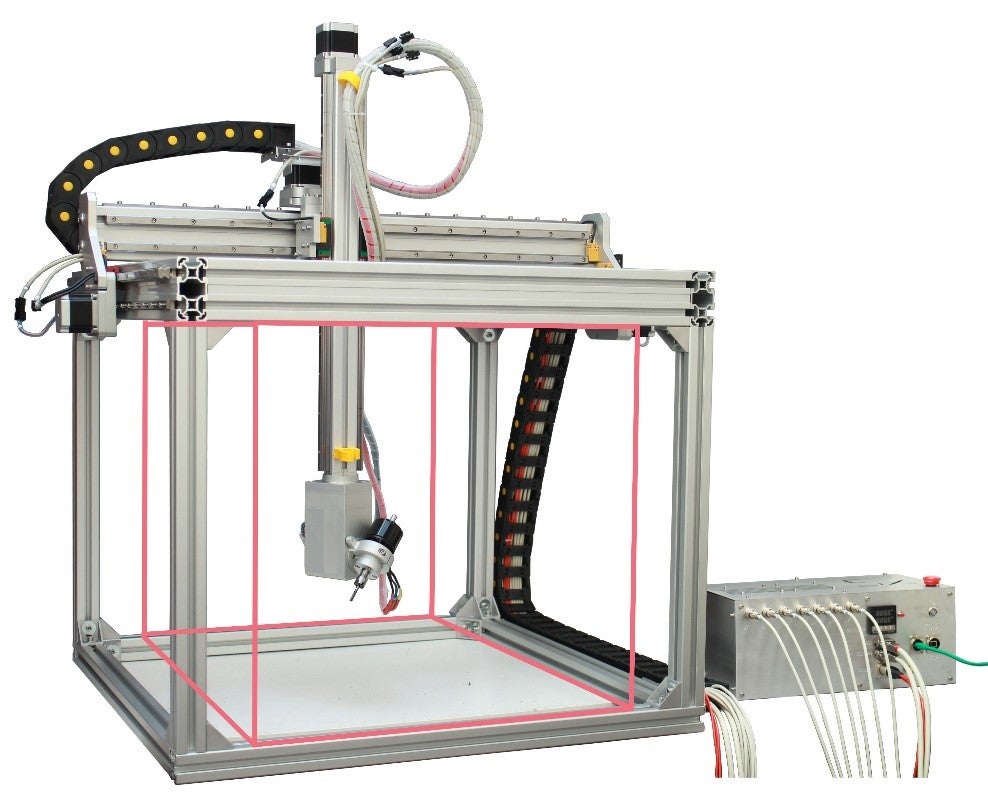
Safety Hazards
There are several hazards present with CNC machining. The student operator must read the Standard Operating Procedure for CNC. They need to be aware of all hazards and follow the instruction of AEMS staff when supervising any CNC machine. Disregard for the established safety rules will result in a loss of AEMS access privileges. If you are unclear about your responsibilities while using the machine, please do not hesitate to ask AEMS staff, they are there to help and answer questions.
Standard Operating Procedure Manual
Scheduling
CNC bookings are made by contacting AEMS staff who maintain a calendar of all fabrication activities in the AEMS. CNC bookings cannot be made until an AEMS technologist programs your part(s) to determine how much time is needed including setup and cleanup. All parts will be charged a 1 hour minimum. Normal bookings are from 9:00am until 4:00pm excluding the lunch hour (12:00pm-1:00pm) Monday through Friday. Bookings are expected to be paid upon completion. Parts will not be released until payment is made.
Rates
Waterloo Engineering Students | $10.00/hr |
Other Waterloo Students | $20.00/hr |
Research | $30.00/hr |
External Departments | $30.00/hr |
Payment Policy
Payment can be made by accessing the University’s E-Commerce site. There is a single listing for CNC work, please enter a quantity that equals the final cost given by AEMS staff. Save your receipt and show it to AEMS staff to claim your finished parts.
Invoices can be created for research or external entities providing a standard 10-digit account code, however the final cost must exceed $100. Parts costing less cannot be invoiced and must be paid on the E-Commerce site.
File Preparation
CAD files for AEMS CNC work can be either 2D or 3D. These can be generated by several programs, including Rhino, AutoCAD, Fusion 360, and Solidworks. Files must be scaled correctly (units must be mm or inch) and include the block of material that is being machined from, otherwise known as the “stock” or “stock block”. Please ensure that the stock block measurements are as close as possible to the real block of material. Do not assume that the labelled dimension of off-the-shelf products are the real dimensions. For example, 4” thick polystyrene foam will range from 3 7/8” to 4 1/8”, quarter inch (6.35mm) plywood can be as thin as 5mm. Not including real, measured dimensions can seriously impact the finished product.
Examples of proper file setup:
This site was generated with the available material in mind. It is 100mm at its thickest point and 600m x 600mm overall. The model is also a solid polysurface. While this isn’t strictly necessary for CNC work, it is good modelling practice.
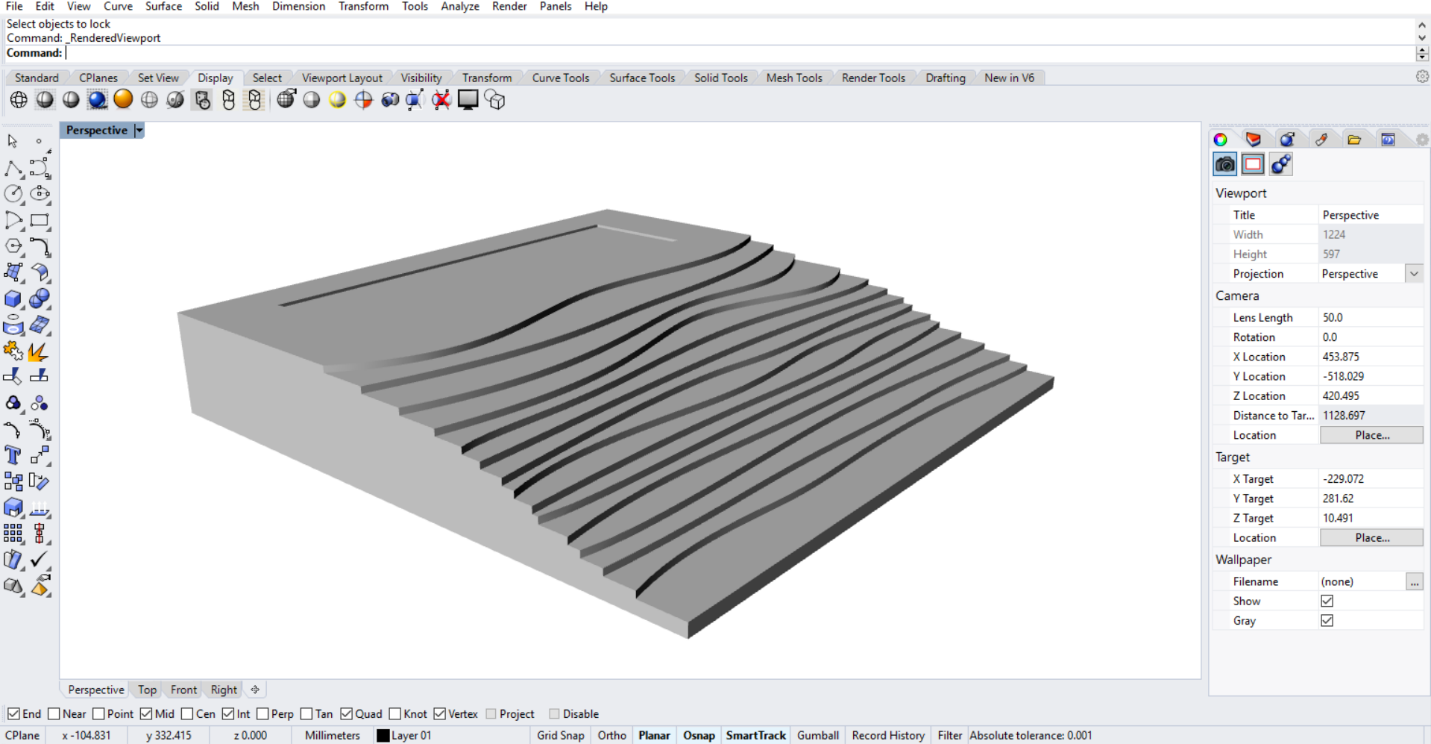
If you have multiple parts being machined from a single block of material, please arrange them on the stock block prior to submitting your file. Parts must have a minimum of ½” (12mm) clearance around them and to the edge of the stock. If you have multiple stock blocks, please export them separately.
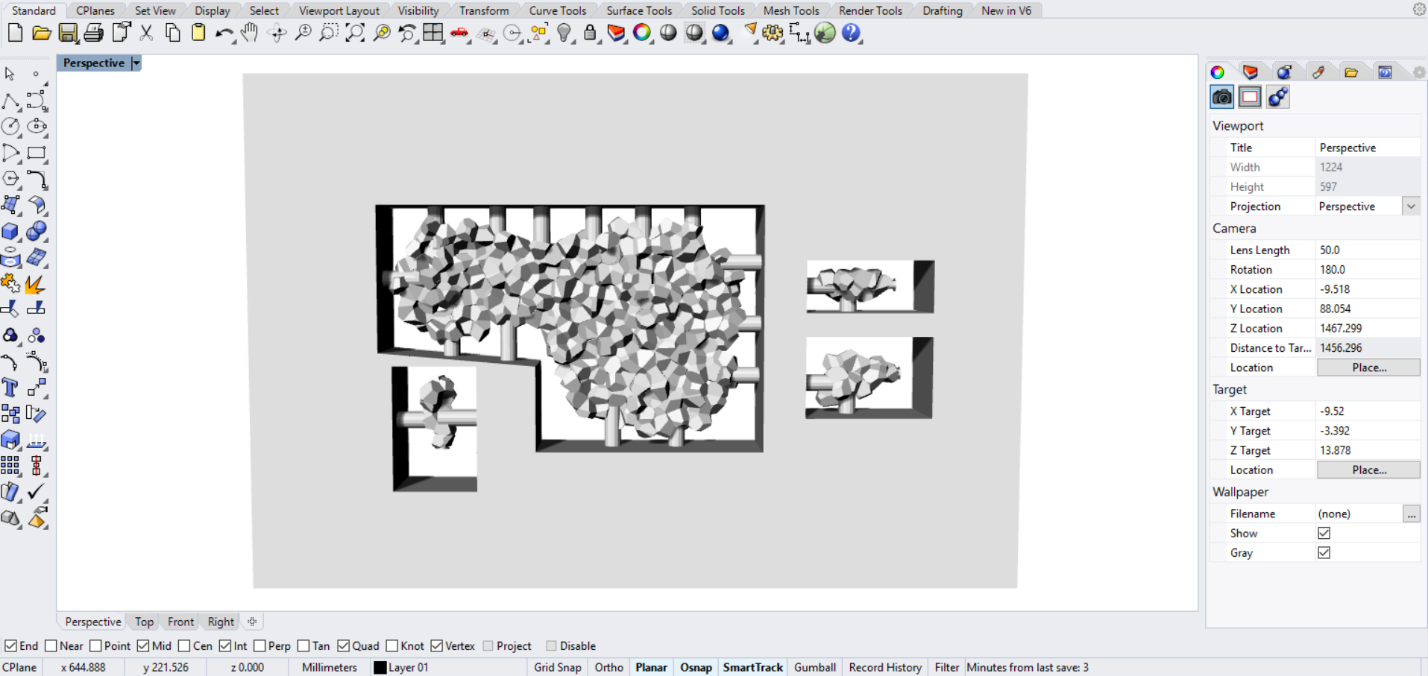
Materials
CNC machining in AEMS is limited to a few types of materials. This is due to the capabilities of the machine and that AEMS will only stock cutting tools for these common materials.
- Wood and wood products including plywood and particle board. MDF can be machined in 2D only due to the large amount of dust it produces.
- Polystyrene (XPS) and polyurethane foams (most densities). EPS or expanded polystyrene is not recommended as it does not hold detail well and is messy to work with.
- Some plastic products in 2D only. Please consult AEMS staff before purchasing material to make sure it is suitable for CNC work.
Programming
Once files have been submitted, AEMS staff will program the toolpaths using CAM software. AEMS uses Fusion 360 for this task. CNC programming is a complex operation and unlike other machinery in AEMS, students are not required to be knowledgeable in this area and are not expected to learn the process, unless they are interested. However, there is some basic terminology that will help students make some decisions about the outcome of their project.
Stock (block) | The piece of material that is being machined away from. |
Tooling | This refers to the cutting instrument. These can vary greatly in size, shape, and purpose. AEMS keeps an inventory of common sizes used for wood and foam. |
Toolpath | Literally the path that the cutting tool travels while cutting. CAM software generates toolpaths as a visual reference only, G-code is what the CNC reads. |
Roughing | The process of removing excess material. This is typically done as quickly as the material and tooling will allow. The greater the difference in volume between the stock and finished part is, the longer this process will take. Generally used in 3+ axis machining. |
Finishing | A broad term for a toolpath that travels along the surface of the part to add definition. There are many types of finishing toolpaths, the most commonly used in AEMS is a Parallel Finishing pass. Generally used in 3+ axis machining. |
Stepover | Distance between passes of a tool expressed as a measurement or as a percentage of the tool’s own diameter. For example, a 25% stepover with a ½” (12.7mm) tool would be 1/8” (3.175mm.) |
Profiling | A toolpath that follows a line either on center or off. Typically a 2-axis operation for cutting out shapes. |
Pocketing | A toolpath that cuts a relief to a certain depth inside of a closed shape. Typically a 2-axis operation. |
Speed vs. Quality
One of the biggest decisions a student will have to make about their part is whether they want it to finish quickly or with a high level of quality, it is rare to be able to accomplish both. The diagrams below illustrate why.
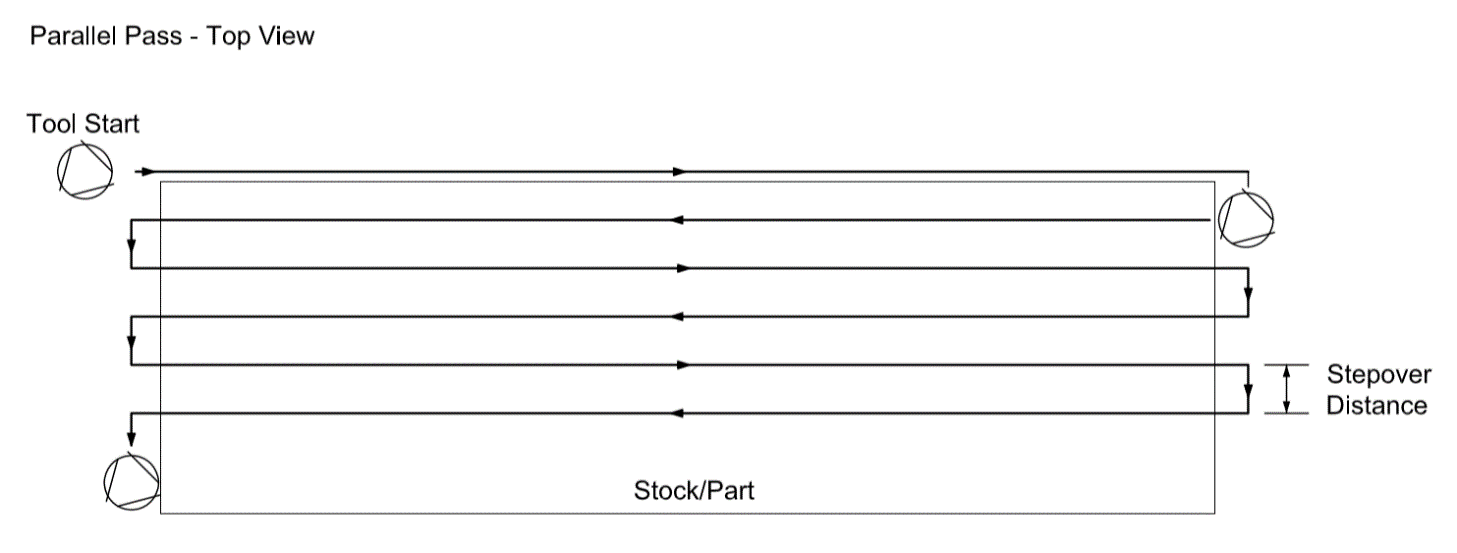
Above - In a Parallel Finishing pass the tool begins travelling along the edge of the part. When it reaches the end of the edge, it moves over by the programmed Stepover distance and then moves back along the part. It will continue this back and forth pattern until it machines the desired area.
Below - The surface of a parallel machined part will be scalloped when a ball-nosed tool is used. When using a high Stepover of 50%, the scallops will be more pronounced resulting in a rougher surface than if a lower Stepover of 25% is used. In contrast, the higher Stepover is faster as it requires half as many moves to machine the same area.
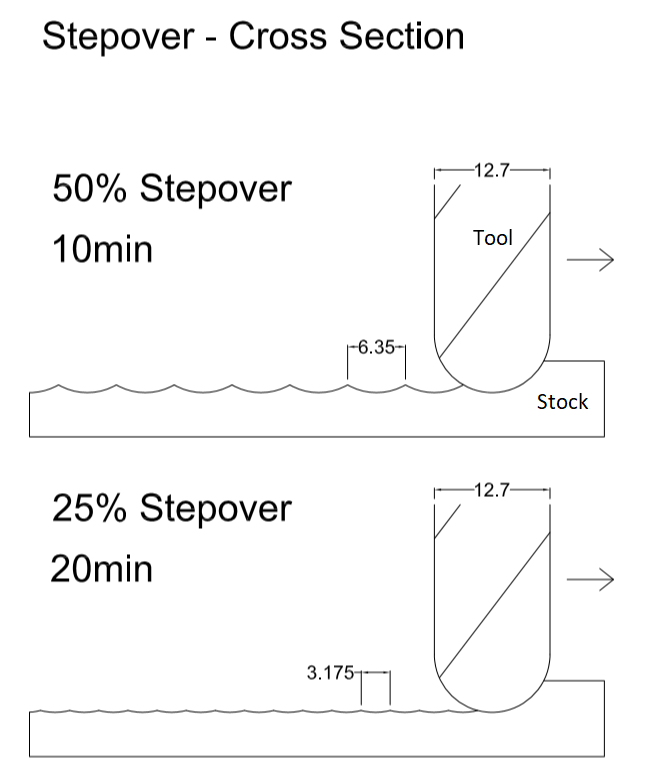
Most parts will require that the student decide on a Stepover value. Example parts of different Stepovers will be provided, and files can be programmed with various values so that time estimates can be obtained. A small Stepover will yield a higher quality part, but at the cost of time. AEMS staff will help by suggesting recommended values.
Tool Selection
There is a wide variety of tooling available for CNC milling. AEMS staff will suggest tooling based on your material and the scale of detail required on your part. AEMS will have common sizes in stock for machining wood and foam. If for some reason a specialized tool is required it will be the student’s responsibility to purchase it with guidance from AEMS staff.
The tooling used in AEMS generally falls into two categories:
Flat (End) mill — This type of tooling features a square profile and is used primarily for 3d parts with an abundance of flat areas, 2d profiling, or roughing passes. Extra large sizes are used for operations called “fly cutting” where a thin layer is skimmed off a surface to ensure flatness or to achieve a certain dimension.
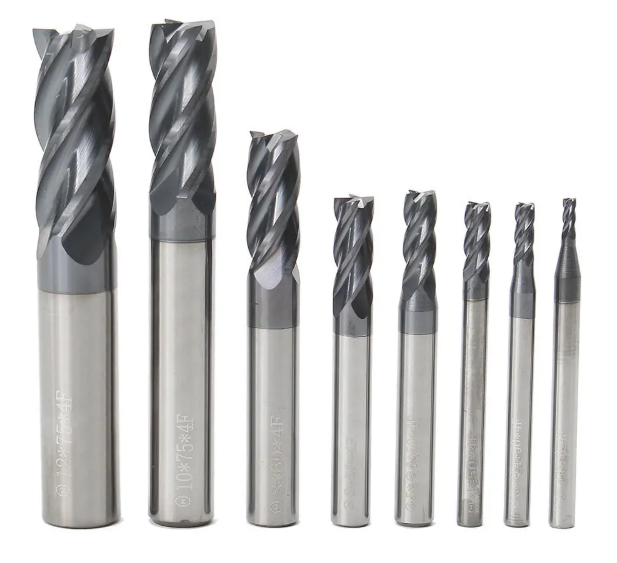
Ball mill — These tools feature a semi-spherical profile and are used primarily for finishing passes on parts with angled faces or 3d curves such as topography. The CAM software will calculate the toolpath so that the surface of the part is always at a tangent to the spherical end.
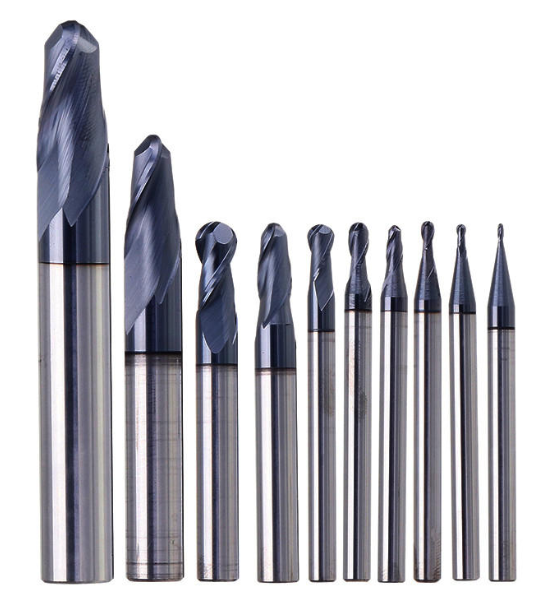
Machine Setup
Before machining can begin, the stock must be fixed to the machining table. This can happen a few different ways depending on the situation:
Vacuum Table | The 3-axis CNC mill is equipped with a vacuum table that allows a part to be held firmly in place using vacuum pressure alone. This is the ideal method as it allows a part to be held securely without any clamps, negating the risk of a tool collision. Only works with parts that have a large and flat surface area. |
Double Sided Tape | This method again reduces the likelihood of a tool collision with any clamps but is generally weaker than using the vacuum table. Tape may sometimes be used for parts that do are not suitable for vacuum holding due to irregular or small surfaces. |
Screws/clamps | These can be used to hold a part in place, but the operator must be careful with the location of these in relation to the area being machined. CNC tooling is sharp, but also brittle. Contact with clamps (even if the tool is not spinning) can shatter tooling. |
Origin (Zeros)
Once the machine is turned on, it will go through a process of “zeroing” itself. Finding the machine zero allows the controller to know where the tool is in within it’s 3d envelope. Caution should be exercised when initializing the zeroing process, make sure no one (including the operator) is near the machine as it will perform automatic movements once the process begins.
The next step is to locate the part “origin.” During programming AEMS will have decided on a feature of the stock to use as the origin. This can be any identifiable point such as centers, protrusions or measured marks, but most commonly is a corner of the material. A tool is loaded and manually moved so that the very center of tool’s tip is aligned with the predetermined point. This tells the machine where the part is in space, all of the machining will be done using this reference point.
Machining Process
Once the parts have been secured and the origin located, machining can begin. The G-code is exported to the CNC controller which pre-processes the file to check for errors. The machine will then start by selecting the first programmed tool and beginning to cut. The operator must not leave the machine running unattended for any reason. CNC machining is not a perfect process and accidents and errors can and do occur. The operator must be present to pause/stop the machine as quickly as possible. The operator is also responsible for ensuring no bystanders wander too close to the machine or try and touch the machine or part during machining.
Warning Signs
While the process is running, the operator must watch and listen for these key indicators that something is wrong:
- The stock moves, shifts, or lifts off the machine table.
- The sound changes significantly.
- Smoke or the smell of smoke.
- The tool is broken or missing.
- The machine is cutting in mid-air, not contacting the part.
Should any of these occur, pause the machine immediately and notify AEMS staff.
Cleanup
Once the machining is complete, AEMS staff will move the CNC to a safe position to allow access for cleaning and part removal. The student is responsible for leaving the machine and surrounding area in the same condition as when they began. All debris must be cleaned from every surface of the machine, paying special attention to the table and the surrounding floor. AEMS is equipped with a dust collection system, several shop vacs, and brushes/brooms for this purpose.
Once cleanup is completed, proof of payment must be shown to AEMS staff. Only then is the completed part released to the student.