ABSTRACT: Nano-structured and hierarchically structured materials play a vital role in electrochemical power source technologies: batteries, super capacitors and fuel cells. They are becoming increasingly important in electrochemical synthesis technologies such as electrolysis, photolysis, CO2 electro-reduction and production of value added chemicals.
Nano-materials contribute to the enhancement of the catalytic properties of the electrodes, dramatically improve interconnectivity of porous matrixes and revolutionize mass-transport characteristics on micro- and meso-scale. Their main role is in enabling the display of phases of greater catalytic activity, stabilizing “unusual” surface moieties that are not displayed in quantities in bulk phases and in facilitating transport phenomena and through this increasing of volumetric (and in some cases, gravimetric) power density, provide for higher energy density and facilitate increased rate of drain. Detailed understanding of these processes allows even broader exploration of nano-materials for energy conversion and storage. Structural properties of these materials are making possible new design solutions and provoke a new stage in power source systems engineering. All these will bring substantial benefit if manufacturing of such materials could meet the demand in volume, performance and reproducibility.
UNM has developed the Sacrificial Support Method (SSM) as a main approach for templated synthesis of hierarchically structured electrocatalysts materials. In this method the catalysts precursors are being absorbed on, impregnated within or mechanically mixed with the support (usually mono-dispersed or meso-structured structured silica), thermally processed (pyrolyzed) and then the silica support is removed by etching (in KOH or HF) to live the open frame structure of a “self-supported” material that consists of the catalysts only (see Fig. 1).
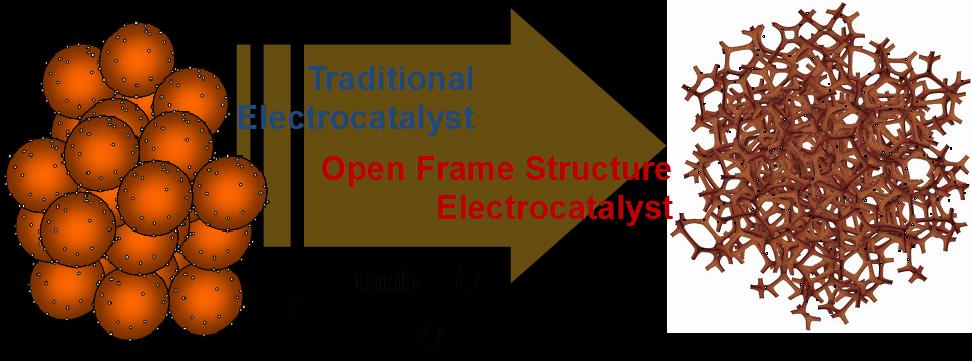
Fig. 1: Schematic of a “open-frame” structured electrocatalyst in contrast with the traditional decorated powder material design.
This presentation brings examples from two materials synthesis platforms: aerosol processing in a format of spray pyrolysis1,2 and colloidal approach based on sol-gel templating of micro- emulsions.3,4 Both approaches have been used at UNM over the last decade to design electrocatalyst powders with varied chemical structure and desired morphology for fuel cell and related applications. The spray-based process results in formation of unique spherical, micron-sized aggregates consisting of sub-micron electrocatalyst particles where the nanometer sized active phases are highly dispersed. Examples include platinum group metals (PGM) and metal alloys; metal oxides, composite and non-noble or graphene metal electrocatalysts. Microemulsion-derived materials have three levels of morphology control: nanopores derived from micellar structure of the surfactant used, mesopores templated on the microemulsion droplets and macrostrucuted particles resulting from sheer mixing. We have developed these two approaches to produce not only traditional electrocatalysts (PGM and their allows supported as decorative phase on carbon blacks) but also a whole new set of reactive oxide and conductive oxide materials that serve as co-catalysts or non-carbonaceous supports. 5,6
Synthesis of non-platinum electrocatalysts based on transition metals and N-containing carbonaceous materials obtained by both methods will be discussed as well. 7-12 Such hierarchical structures are advantageous in enhancement of the fuel cell performance since they correspond to the different levels of transport in the corrugated electrode matrixes. Fig. 2 illustrates the SSM when it is applied to synthesis on Non-PGM catalysts.

Fig. 2: Sacrificial Support Method for templated synthesis of Non-PGM electrocatalyst of Transition Metal-Nitrogen-Carbon class.
A wide variety of materials can be made by these methods in which not only the composition but also the microstructure can be varied. It is the combination of these attributes - control over microstructure at a number of different length scales and composition, simultaneously - that is extremely important to the performance of the electrocatalyst materials in a fuel cells. This paper will bring examples of successful practical applications of our materials in automotive technologies using both Polymer Electrolyte (PEMFC) and Alkaline Membrane (AMFC) Fuel Cells with gaseous and liquid fuels. 13-14
Bio-Sketch: Plamen Atanassov graduated from the University of Sofia specializing in Chemical Physics and Theoretical Chemistry. He joined the Bulgarian Academy of Sciences and become a Member of Technical Staff of its Central Laboratory of Electrochemical Power Sources (now the Institute for Electrochemistry & Power Systems). His initial work included materials solutions for metal-air batteries. He was a visiting scientist at the Frumkin’s Institute of Electrochemistry, Moscow, Russia studying bio-electrochemistry of enzymes and received a PhD in Physical Chemistry/Electrochemistry. Dr. Atanassov moved to the United States in 1992 and later became a research faculty with the University of New Mexico. During the 90s he was involved in development of a several electrochemical biosensor technologies for biomedical, environmental, food safety and defense applications. In 1999 Plamen Atanassov joined Superior MicroPowders LLC (acquired later by Cabot Corp.) were he was a project leader in fuel cell electrocatalysts development that resulted in introduction of spray pyrolysis for catalyst synthesis on industrial scale. He returned to the University of New Mexico in 2000 as faculty member of the Chemical & Nuclear Engineering Department. In 2007 Dr. Atanassov founded the UNM Center for Emerging Energy Technologies. From January 2012 to December 2013 Dr. Atanassov was the Associate Dean for Research of the UNM School of Engineering. Currently Dr. Atanassov is a Distinguished Professor of Chemical & Biological Engineering and leads the UNM Center for Micro-Engineered Materials (CMEM). His research programs are focused on development of novel electrocatalysts: non-platinum electrocatalyst for fuel cells, nano-structured catalysts for oxidation of complex fuels, new materials and technologies for energy conversion and storage. Dr. Atanassov bio-electrocatalysis programs range from enzyme electrochemistry, enzymatic and microbial fuel cells, and systems for biological and bio-inspired energy harvesting. His research is funded by NSF, DOD, DOE and industrial partners, among those Daihatsu Motor Co, Ballard Power Systems, AFCC, SFD Research Corp. and others.