4.1 Designated Substances
The Ontario Occupational Health and Safety Act defines a designated substance as being a biological, chemical or physical agent or combination thereof prescribed as a designated substance to which the exposure of a worker is prohibited, restricted, limited, or controlled. If it is ascertained that the actual or intended use or production of a designated substance in a workplace (including even small quantities in a research laboratory) is likely to endanger the health of a worker (researcher or other occupants of the laboratory), the Ministry of Labour will require implementation of engineering controls at the workplace and possibly medical surveillance of the researchers involved.
As of January, 2018, the following are designated substances in Ontario:
- Acrylonitrile
- Arsenic (including elemental arsenic and inorganic compounds of arsenic, excepting arsine, and including organic compounds of arsenic only where both inorganic and organic compounds of arsenic are present)
- Asbestos (including the following fibrous silicates: actinolite, amosite, anthophyllite, chrysolite, crocidolite or tremolite)
- Asbestos on construction (repair or removal of asbestos used in building construction)
- Benzene
- Chemical and biological agents named in O.Reg. 654/86 (see p. 9)
- Coke oven emissions
- Ethylene oxide
- Isocyanates (toluene diisocyanate; methylene bisphenyl isocyanate; hexamethylene; 1,6-diisocyanate; isophorone diisocyanate)
- Lead (including elemental lead, and inorganic or organic compounds of lead)
- Mercury (including elemental mercury, and inorganic or organic compounds or mercury)
- Silica (crystalline silica in respirable form)
- Vinyl chloride
Supervisors and research workers in laboratories where a designated substance is stored, handled or used shall take the necessary precautions (hygiene practices and facilities; work methods; engineering controls) to ensure that the time-weighted average exposure of a worker to a designated substance does not exceed the limits prescribed by the regulation pertaining to that substance.
The following procedures are to be followed when handling a designated substance or any chemical which has a high potential hazard rating:
- The substance shall be exposed to air only when it is used in a properly operated fume hood (see section 5.5)
- Appropriately impermeable gloves should be worn
- Hygiene and work practices should prevent any bodily contact with the substance.
4.2 Chemical Handling and Storage
Chemicals can be hazardous unless properly handled. Serious skin and eye irritations and damage to clothing can result from needless spills and sprays. Toxic materials can cause severe illness, even death; all chemicals, especially new compounds, the toxicity of which has not yet been determined, should be assumed to be highly toxic until demonstrated otherwise. Flammable gases, liquids and solids can cause fires and develop into explosive mixtures.
Never transport chemical reagents on stairways where a slip or trip could result in serious exposure. Use elevators only with proper secondary containment, (e.g. rubber bucket or lab cart).
Before working with any chemical, it is essential to know its properties. The properties of known reaction products, intermediates or even possible reaction products should be ascertained before work begins (see section 3.1). In exploratory research work, only very small quantities of chemicals should be employed. Larger amounts may be used after the initial work has been successfully completed and the reaction rates and the properties of the reaction products have been established.
Hazardous chemicals include, in addition to flammable materials, those substances that are toxic, corrosive or reactive. It must be recognized that a material, which by itself is comparatively harmless, can become very hazardous under conditions of use and under conditions to which it may be subjected accidentally--as in fires.
- Pour acids into water slowly while agitating. Never pour water into acid.
- Hydrofluoric Acid (HF) has special risks and requires extra safety precautions and procedures. Consult the Safety Office HF Standard before working with HF.
- Stoppers should be held out of contact with anything but air while pouring from a bottle and chemicals should be flushed off a bottle before returning it to a rack. Chemicals should be transferred or added while holding the receiver over a sink. Never return unused chemicals to stock bottles.
- To reduce the risk of accidental breakage by service personnel, do not store glass bottles of chemicals on floor
UW General Chemical Storage Recommendations:
- Chemicals should NEVER be alphabetized unless they are segregated by hazard class first.
- In general, high hazard chemicals should be in separate cabinets, and organic and inorganic materials should be segregated from one another. The storage scheme presented in Table 8 can be used to maximize space in the laboratory:
Table 8: Chemical Storage
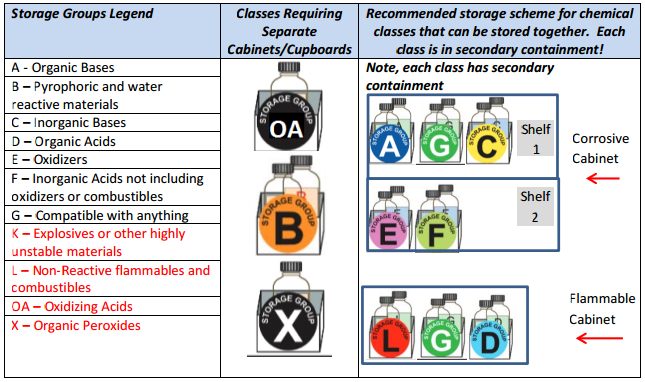
Liquid Chemical Classes:
Groups A, C, D (A - Organic Bases, C – Inorganic Bases, D – Organic Acids)
- Organic and inorganic bases can be kept in the same cabinet on the same shelf. Inorganic acids should be separated from all bases. Ideally this means a different cabinet, but if this is not possible, on a different shelf with secondary containment. Organic acids should be stored away from inorganic acids, and all bases - ideally in the flammable cabinet.
- Organic bases contain nitrogen, or an amino group. Some examples include - Diethylamine, Piperidine, Triethanolamine, Benzylamine, and Benzyltrimethylammonium hydroxide.
- Inorganic bases normally contain a hydroxide group and accept hydrogen ions from other substances. Their general action is the corrosion of metals and destruction of living tissue. Examples include: Sodium hydroxide, Ammonium hydroxide, Lithium hydroxide, Cesium hydroxide.
Group B – Pyrophoric and water reactive materials:
- Pyrophoric and water reactive materials are those that can ignite spontaneously or react violently with air, moisture in air, oxygen, or water. Some examples of these compounds include – Sodium borohydride, Benzoyl chloride, Zinc dust, Alkyl lithium solutions such as Methyl lithium in tetrahydrofuran, Methanesulfonyl chloride, Lithium, and Aluminum hydride. These must be stored in their own cabinet.
Group E – Oxidizers including Inorganic peroxides:
- This class of chemical is highly reactive and gives off oxygen and other oxidizing substances. Oxidizers can intensify combustion during a fire, widen the flammable range of a flammable gas or liquid, and can lower the flashpoint or ignition temperature of combustible materials. Inorganic peroxides are generally stable but may form organic peroxides on contact with organic compounds.
Groups F, and OA (F – Inorganic Acids, OA – Oxidizing Acids):
- Organic and inorganic acids should not be kept in the same cabinet, but should be stored on different shelves. Inorganic acids should be stored on different shelves then inorganic bases, and both should have secondary containment.
- Acids should not be stored near cyanide or sulfide containing chemicals to prevent formation of hydrogen cyanide or hydrogen sulfide gases.
- Acids should not be stored near metal piping that supplies natural gas or water.
- Inorganic acids, organic acids, and oxidizing acids should be segregated from one another.
- Nitric acid, perchloric acid, and sulfuric acids are oxidizing acids that should be stored in their own secondary containment and in their own designated cabinets/cupboards with secondary containment – meaning Nalgene trays or equivalent. They are Group OA.
Group L - Flammable Liquids:
- Flammable liquids must be stored away from oxidizers AND oxidizing acids (nitric, chromic, sulphuric, etc…) - generally they are kept in their own flammable cabinet.
- Non-flammable solvents may be stored in flammable cabinets.
- Flammable cabinets shall be grounded and vented. If venting is not possible the vent port should be sealed.
- Refrigerators used for storage of flammable compounds shall be certified for such use and designated as explosion proof.
Group K – Explosives or Other Highly Unstable Materials:
- Some examples of these materials include – Picric Acid Dry (<10% H2O), Nitroguanidine, Tetrazole, Urea nitrate.
Group X – Incompatible with ALL Other Storage Groups:
- Some examples of this group of chemicals include -Picric Acid Moist (10% – 40% H2O), Phosphorus, Benzyl Azide, Organic Peroxides, and Sodium hydrogen sulfide.
Solid chemicals:
- Flammable solids and oxidizing salts should be segregated onto separate shelving. Examples of oxidizing solids include: bromates, chlorates, chlorites, chromates, dichromates, hypochlorites, iodates, nitrates, nitrites, perchlorates, peroxides, permanganates, picrates.
- Water reactive or pyrophoric materials should be placed in their own cabinet.
4.2.1 Inventory Control
The person in charge of a laboratory should compile an inventory list, including purchase and expiry dates, of all chemicals in the laboratory. As an absolute minimum, the chemical stocks should then be reviewed and expired or deteriorated chemicals must be discarded in accordance with disposal regulations (see section 4.4 and Appendix 2). The inventory list should be uploaded and regularly maintained on erPortal, UW's online chemical inventory system. Additional information about erPortal can be found on the University of Waterloo Safety Office website.
4.2.2 Labelling
All containers of chemicals, including temporary containers, must have legible labels attached to them identifying both the contents and the type of hazard presented by the contents.
4.2.3 Safety Data Sheets
The Safety Data Sheet, or SDS, contains important information about the controlled product you are using and is one of the three core elements of the WHMIS program at UW. The SDS when used to supplement the information found on WHMIS labels and in conjunction with an effective education plan will give you the knowledge you need to work safely and confidently with any hazardous material.
SDS Availability
Every WHMIS controlled product in your work/study area must have an associated SDS readily available. The SDS must be able to be accessed by all UW personnel that work with, or near the controlled product. An SDS may be kept in either a hard (i.e., paper) or soft (i.e., electronic) format.
Hard copies must at all times be;
- Visible, and
- Accessible.
Soft copies must be accessible through a computer to employees/students in the area where the controlled products are stored or used. Ready access means;
- Having a user ID and password, if the computer is security enabled;
- Knowing the server and file path to find the information;
- If applicable, knowing how to use the SDS management software, and
- Having privileges and knowing how to print a hardcopy.
Whether the SDS is a hard or soft copy it must not be older than 3 years.
Maintain your SDS collection as follows:
Laboratories/Shops/Studios
- Hard copies must be maintained for:
- Any controlled products that are kept out in the open or on a bench-top, and
- Controlled products that are present in:
- a pipe;
- a piping system including valves;
- a process vessel; or
- a reaction vessel
- Soft copies may be maintained for all remaining controlled products
Controlled product storage areas
- Hard copies must be maintained for storage areas with 10 or fewer controlled products
- Soft copies may be maintained for storage areas with over 10 controlled products
Controlled product dispensing areas
- Hard copies must be maintained for all controlled products dispensed in the area
Safety data sheets come in one of two forms:
- 9 heading – meets minimum requirements under Canada regulations
- 16 heading – more comprehensive international format that is replacing the 9 format
4.2.4 Containers
Containers must be compatible with their contents, inspected regularly, and disposed of, if damaged or deteriorated. Chemicals should be dated when purchased, and again when the container is opened. Non-original containers must also be dated. Containers should be kept securely closed, with chemicals requiring venting being stored only in a proper pressure-venting container. Flammable and combustible liquids must be stored in and dispensed from approved containers. Containers for storage of chemicals should be chosen with care and using guidelines in the university Safety policy. Please consult the University of Waterloo Safety Office’s website for procedures on how to store chemicals correctly.
4.2.5 Chemical Compatibility and Safe Handling
Below is a chart adapted from the CRC Laboratory Handbook which groups various chemicals into 23 groups with examples and incompatible chemical groups. This chart is by no means complete but it will aid in making decisions about storage. For more complete information please refer to the SDS for the specific chemical.
Table 9: Incompatible Chemicals
Group |
Name |
Example |
Incompatible Groups |
Group 1 |
Inorganic Acids |
Hydrochloric acid, Hydrofluoric acid, Hydrogen chloride, Hydrogen fluoride, Nitric acid, Sulfuric acid, Phosphoric acid |
2, 3, 4, 5, 6, 7, 8, 10, 13, 14, 16, 17, 18, 19, 21, 22, 23 |
Group 2 |
Organic Acids |
Acetic acid, Butyric acid, Formic acid, Propionic acid |
1, 3, 4, 7, 14, 16, 17, 18, 19, 22 |
Group 3 |
Caustics |
Sodium hydroxide, Ammonium hydroxide solution |
1, 2, 6, 7, 8, 13, 14, 15, 16, 17, 18, 20, 23 |
Group 4 |
Amines & Alkanolamines |
Aminoethylethanolamine, Aniline, Diethanolamine, Diethylamine, Dimethylamine, Ethylenediamine, 2-Methyl-5-ethylpyridine, Monoethanolamine, Pyridine, Triethanolamine, Triethylamine, Triethylenetetramine |
1, 2, 5, 7, 8, 13, 14, 15, 16, 17, 18, 23 |
Group 5 |
Halogenated Compounds |
Allyl chloride, Carbon tetrachloride , Chlorobenzene, Chloroform, Methylene chloride, Monochlorodifluoromethane, 1,2,4-Trichlorobenzene, 1,1,1-Trichloroethane, Trichloroethylene, Trichlorofluoromethane |
1, 3, 4, 11, 14, 17 |
Group 6 |
Alcohols, Glycols, Glycol Ether |
1,4-Butanediol, Butanol (iso, n, sec, tert), Diethylene, glycol, Ethyl alcohol, Ethyl butanol, Ethylene glycol, Furfuryl alcohol, Isoamyl alcohol, Methyl alcohol, Methylamyl alcohol, Propylene glycol |
1, 7, 14, 16, 20, 23 |
Group 7 |
Aldehydes & Acetaldehydes |
Acrolein, Butyraldehyde, Crotonaldehyde, Formaldehyde, Furfural, Paraformaldehyde, Propionaldehyde |
1, 2, 3, 4, 6, 8, 15, 16, 17, 19, 20, 23 |
Group 8 |
Ketones |
Acetone Acetophenone Diisobutyl ketone Methyl ethyl ketone |
1, 3, 4, 7, 19, 20 |
Group 9 |
Saturated Hydrocarbons |
Butane, Cyclohexane, Ethane, Heptane, Paraffins, Paraffin wax, Pentane, Petroleum ether |
20 |
Group 10 |
Aromatic Hydrocarbons |
Benzene, Cumene, Ethyl benzene, Naphtha, Naphthalene, Toluene, Xylene |
1, 20 |
Group 11 |
Olefins |
Butylene, 1-Decene, 1-Dodecene, Ethylene, Turpentine |
1, 5, 20 |
Group 12 |
Petroleum Oils |
Asphalt, Gasolines, Mineral Oil |
20 |
Group 13 |
Esters |
Amyl acetate, Butyl acetates, Castor oil, Dimethyl sulphate, Ethyl acetate |
1, 3, 4, 19, 20 |
Group 14 |
Monomers & Polymerizable Esters |
Acrylic acid, Acrylonitrile, Butadiene, Acrylates |
1, 2, 3, 4, 5, 6, 15, 16, 19, 20, 21, 23 |
Group 15 |
Phenols |
Carbolic acid, Cresote, Cresols Phenol |
3, 4, 7, 14, 16, 19, 20 |
Group 16 |
Alkylene Oxides |
Ethylene oxide, Propylene oxide |
1, 2, 3, 4, 6, 7, 14, 15, 17, 18, 19, 23 |
Group 17 |
Cyanohydrins |
Acetone cyanohydrin, Ethylene cyanohydrin |
1, 2, 3, 4, 5, 7, 16, 19, 23 |
Group 18 |
Nitriles |
Acetonitrile, Adiponitrile |
1, 2, 3, 4, 16, 23 |
Group 19 |
Ammonia |
Ammonia gas, Ammonium Hydroxide |
1, 2, 7, 8, 13, 14, 15, 16, 17, 20, 23 |
Group 20 |
Halogens |
Chlorine, Fluorine |
3, 6, 7, 8, 9, 10, 11, 12, 13, 14, 15, 19, 21, 22 |
Group 21 |
Ethers |
Diethyl Ether, THF |
1, 14, 20 |
Group 22 |
Phosphorus |
Phosphorus, Elemental |
1, 2, 3, 20 |
Group 23 |
Acid Anhydrides |
Acetic anhydride, Propionic anhydride |
1, 3, 4, 6, 7, 14, 16, 17, 18, 19 |
4.2.5.1 Flammable and Combustible Liquids
Part IV of the Ontario Fire Code governs quantities of flammable liquids that are handled or stored in Laboratories.
Maximum Quantities:
The maximum container size allowed in laboratories is 5 L.
Section 4.12.3.1(1) of the Ontario Fire code states "The container size used for the storage of flammable or combustible liquids in a laboratory shall be not more than 5 L capacity"
Table 10: Classification of Flammable Liquids
Description |
Class |
Boiling Point (°C) |
Flash Point (°C) |
Flammable |
IA |
<37.8 |
<22.8 |
Flammable |
IB |
>37.8 |
<22.8 |
Flammable |
IC |
--- |
>22.8 and <37.8 |
Combustible |
II |
--- |
>37.8 and <60 |
Combustible |
IIIA |
--- |
>60 and <93.3 |
Combustible |
IIIB |
--- |
>93.3 |
Dispensing Solvents
Part IV of the Ontario Fire Code restricts dispensing flammable or combustible liquids from containers of more than 5 L capacity. Dispensing flammable or combustible liquids from containers of 5 L capacity or less is permissible in laboratories at UW provided the dispensing is performed in an approved chemical (fume) hood. Chemistry Stores (ESC 109) is the only location on campus that has been designed and approved to dispense flammable or combustible liquids from containers with a capacity greater than 5 L.
Flammable/combustible Liquids in the Open Lab
A maximum of 300 L of combustible (class II and III) and flammable liquids (class I), of which no more than 50 L can be flammable (class I), can be outside of a flammable liquid storage cabinet at any one time.
Flammable Liquid Storage Cabinets
A maximum of 500 L of combustible (class II and III) and flammable liquids (class I), of which no more than 250 L can be flammable (class I), can be stored in an approved flammable liquid storage cabinet. Each lab is permitted a maximum of 3 flammable liquid storage cabinets.
For more information about flammable storage cabinets see the University of Waterloo Safety Office website.
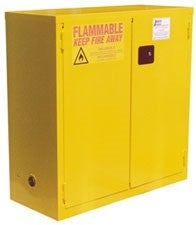
Figure 3: Flammables Storage
Location of work when working with flammable or combustible liquids
All work, research, investigations, etc. involving flammable or combustible liquids must be carried out in an approved chemical (fume) hood when;
- Their use releases flammable vapours which could be potentially explosive,
- Liquids are heated to a temperature greater than their flash point, or
- Unstable liquids are used.
Refrigerated storage
Where refrigerators are required to keep flammable liquids (class I) at a controlled temperature the refrigerator must:
- Be approved by the Electrical Safety Authority,
- Be identified as containing flammable liquids, and
- Have all containers within the refrigerator tightly closed.
4.2.5.2 Toxic and Carcinogenic Chemicals
Refer to section 4.2.3 Safety Data Sheets
4.2.5.3 Explosive Chemicals
Chemicals such as propargyl bromide, azides, picric acid, and concentrated hydrogen peroxide are potential explosives and must be restricted within the laboratory to those amounts needed for one week’s work. It is imperative that all substances having an explosion hazard potential be carefully dated and monitored, and kept away from heat, light, and sources of ignition or physical damage. Many ethers form dangerously explosive peroxides upon prolonged exposure to the atmosphere. Though detection of peroxides can be easily achieved by dipping a starch iodide paper strip into the solvent being tested (the strip turning purple indicates that peroxides are present), disposal is preferred when the expiry date has passed. Soluble azides, when in contact with heavy metals, can produce heat- and shock-sensitive insoluble azide explosives. These should always be handled with care, and diluted heavily with water before disposal. Picric acid containers with less than 10 percent water content are shock sensitive high explosives, and must not be opened or moved, but reported immediately to the Safety Office for proper disposal. Also see perchloric acid (section 4.2.5.5). Table 9 lists some chemicals that present explosion hazards.
Table 11: Some Potentially Explosive Chemicals
(Ref.: York University Science Health and Safety Manual)
Compounds Which Can Form Explosive Peroxides During Storage:
divinyl acetylene isopropyl ether potassium metal |
sodium amide vinylidene chloride |
Compounds Which Can Produce Explosive Peroxide Conditions Upon Concentration:
Acetal Cyclohexane Diacetylene Dicyclopentadiene diethylene glycol dimethyl ether (diglyme) dimethyl ether |
dioxamethylene glycol dimethyl ether (glyme) methyl acetylene tetrahydrofuran tetrahydronapthalene (tertalin) vinyl ethers |
Compounds Which Can Initiate Explosive Polymerization upon Peroxide Formation:
acrylic acid acrylonitrile butadiene chloroprene chlorotrifluoroethylene methyl methacrylate styrene |
tetrafluoroethylene vinyl acetate vinyl acetylene vinyl chloride vinylidene chloride vinylpyridine |
Compounds Which May Readily Detonate or Decompose or React Explosively at Normal Room Temperatures and Pressures. (Also includes compounds which are sensitive to mechanical or localized thermal shock.)
acetyl peroxide (25% solution in dimethyl phathalate) ammonium perchlorate 3-bromopropane (propargyl bromide) tert-butyl hydroperoxide tert-butyl perbenzoate tert-butyl peroxyacetate (75% solution in benzene) tert-butyl peroxypivalate (75% solution in mineral spirits) 1-chloro-2,4-dinitrobenezene cumene hydroperoxide diacetyl peroxide dibenzoyl peroxide |
tert-dibutyl peroxide diethyl peroxide diisopropyl peroxydicarbonate o-dinitrobenzene ethyl methyl ketone peroxide ethyl nitrite nitroglycerine nitromethane 2-nitro-p-toluidine peroxyacetic acid (diluted with 60% acetic acid solution) picric acid trinitrotoluene trinitrobenzene |
4.2.5.4 Oxidizing Agents
Oxidizing agents such as peroxides, nitrates, nitrites, bromates, chromates, chlorates, dichromates, perchlorates, and permanganates should be restricted within the laboratory to single small-sized containers, and stored in cabinet of non-combustible material.
4.2.5.5 Corrosive Chemicals and Perchloric Acid
Corrosives such as acids and alkalis should be restricted within the laboratory to single, small-sized containers, and stored segregated from each other and from other chemicals on corrosion resistant materials. Containers of corrosives must be set into appropriate trays or buckets when being moved or stored in case of leakage or spillage. Perchloric acid is extremely strong, and will produce severe burns when in contact with the skin, eyes and respiratory tract. Proper protective equipment and procedures along with required specialized equipment such as a Perchloric Acid Fume Hood must be used when handling perchloric acid. All users of perchloric acid must ensure that equipment and procedures are adequate prior to use, including prepared emergency procedures. Bottles of perchloric acid, such as commercial 70%, must be inspected monthly and disposed of if any discoloration is noted. Individual preparations of anhydrous perchloric acid, which may be unstable even at room temperature, and may spontaneously explode, must not be stored, but disposed of at the end of each day. Mixtures of anhydrous perchloric acid with organic substances constitute a severe fire and explosion hazard.
4.2.5.6 Water-Sensitive Chemicals
Quantities of potassium, sodium metals and metal hydrides, which are water sensitive, should be restricted to single, small-sized containers, and stored in fire resistant, cool, dry areas designed to prevent accidental contact with water and other incompatible chemicals.
4.2.5.7 Compressed Gases
Compressed gas cylinders can be extremely hazardous when misused or abused. Certain precautions must be observed when storing, handling, and using compressed gas cylinders in order to keep the hazards to a minimum. The uncontrolled release of a compressed gas can result in serious consequences, not only because of possible toxicity and flammability, but also because a high pressure cylinder can become a lethal missile if the cylinder valve is broken off.
Storage:
- Store cylinders in an upright position (valve end up), on a level fireproof floor.
- Fasten cylinders securely at all times.
- Keep storage area well ventilated and dry.
- Ensure no flammable substances such as oil and volatile liquids are stored in the same area.
- Separate oxygen cylinders from cylinders containing flammable gases or other combustible materials by 6m, or by a 1.5m high fire-resistant wall with a rating of at least 30 minutes.
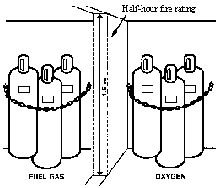
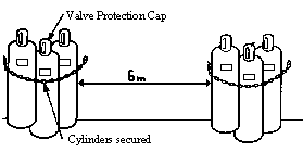
Figure 4: Cylinder Storage
- Store out of direct sunlight and away from other sources of heat as cylinder temperatures must not exceed 125°F.
- Separate empty and full cylinders. Clearly mark the empties "MT and date" with chalk, regulator removed and valve cap replaced.
- No smoking in the storage room or near any compressed gas.
- Remove all sources of ignition from the storage room.
- Propane tanks greater than 5 lbs. In size must be stored out of doors.
Laboratory Storage:
- Storage of cylinders in the laboratory should be restricted to those cylinders that are connected and in use.
- As soon as possible remove empty, not in use, or unnecessary cylinders from the laboratory or to storage.
- Toxic gases should be placed in ventilated storage
Compressed Gas Cylinder Storage
Flammable or Oxidizing Gas |
Liquefied Flammable Gas |
Gases with a Health Hazard Rating of 3 or 4 (LC 50 < 3000 PPM) (stored in ventilated cabinet) |
|
Number of large Cylinders per 500 ft2 |
3 |
2 |
3 |
Procedure for cylinder replacement in Laboratory:
- Mark the bottle empty (MT) with a felt tip pen on the yellow label and ensure there is at least twenty (20) psig (pounds per square inch gauge) remaining or the equivalent pressure that the equipment uses to prevent reverse flow of gas causing contamination. DO NOT REMOVE THE LABEL.
- Fully close the cylinder valve, wait for a minute to let all the gas out of the regulator, completely “back-off” the Pressure Adjust (PA) valve
- With the proper wrench, remove the regulator from the cylinder
- Cap the cylinder
- Place cylinder on a gas cart and move it to another chained location.
- Order a replacement using the online order form.
Note: Do not remove safety cap until cylinder is fixed into cylinder holders in the laboratory.
Handling:
- Cylinders should be transported carefully in accordance with procedure listed above
- Numbers, marks, and paint colours on cylinders identify them and must not be removed or changed. Tags attached to the cap are not a satisfactory method of identification.
- Keep the metal cap securely in place to protect the valve whenever the cylinder is not connected for use.
- Protect cylinders from damage.
- Because of their shape, smooth surface, and weight, cylinders must not be carried by hand. Cylinders are to be moved only with cylinder carts in which the cylinder is securely held by a chain.
- When cylinders must be handled by a crane or derrick, carry them in a cradle or on a suitable platform and take extreme care that they are not dropped or bumped. Do not use slings.
- If necessary, cylinders may be rolled on their bottom edge while in a nearly vertical position, but never dragged.
- Keep valve caps in place when cylinders are transported, moved, or not connected for use.
- Do not use cylinders for rollers, supports, or any purpose other than to contain gas.
- Avoid dropping cylinders or allowing them to strike violently against other cylinders.
- Handle empty cylinders as carefully as full ones; residual pressures can be dangerous.
- Do not tamper with safety devices in valves or on cylinders.
- Never refill a cylinder. This calls for specialized equipment and techniques.
- Never mix gasses in a cylinder. The next person who draws from it may unknowingly cause an explosion. If an outlet valve becomes clogged with ice or frozen, thaw with warm (not boiling) water (if gas is not water reactive), applied only to the valve. Do not use a flame.
Use and Operation:
- Use cylinders, particularly those containing liquefied gas, in an upright position and secure them firmly with chains or clamps.
- Reduce the pressure of a compressed gas through a manufacturer’s specified regulator attached to the cylinder valve.
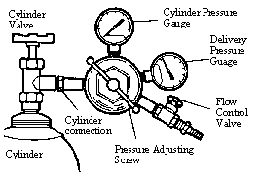
Figure 5: Gas Cylinder Regulator
- Ensure the threads on a regulator or union correspond with those on the cylinder valve outlet. Do not force mismatched connections.
- Use regulators and pressure gauges only with gases for which they are designed and intended. Do not use adapters or modify connectors.
- Use regulators and pressure gauges only with gases for which they are designed and intended. Do not use adapters or modify connectors to circumvent this rule.
- Open cylinder valves slowly with valve outlet directed away from all personnel.
- DO NOT EMPTY A CYLINDER COMPLETELY. This will prevent a flash-back and a possible explosive mixture.
- Never use oil or grease on valves or attachments for oxygen cylinders and never handle oxygen cylinders and apparatus with oily hands, gloves, or clothing.
- Test cylinders for leaks each time you use them. Use soapy water, approved leak - test solution or detection equipment to check for leaks, never use flame. (Figure 6)
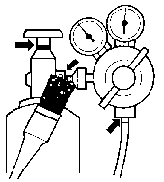
Figure 6: Regulator Leak Check
- If leaks occur in cylinders of noxious or combustible gases, close the valve and remove the cylinder outdoors or place in fume hood and notify the Safety Office.
- Purge oxygen and acetylene lines before lighting.
- When bleeding off flammable gases, use a ground wire on cylinder valves.
- Do not use recessed top of the tank cylinders for the storage of tools or other equipment.
- Never direct compressed air or other gases toward the body.
- Exercise care to avoid injury to hands or feet. The use of safety shoes and heavy gloves is highly recommended.
- Do not use force to open or close cylinder valves; if there is a problem, notify the Safety Office.
- Use the cylinder valve for turning the gas off, not the regulator valve.
- Close the main cylinder valve as soon as it is no longer necessary to have it open.
- Before you remove the regulator make sure that the cylinder valve is closed.
- Place a trap between the regulator valve and the reactor vessel to prevent contamination when carrying out chemical reactions using pressurized gas.
- Turn off the cylinder valve and then the regulator, when your work is finished. The pressure gauges should be brought back to zero.
Hoses and Connections
- Do not use unnecessarily long hoses. If a long hose must be used, make sure it is free from kinks, and away from high traffic areas.
- Examine hoses periodically for leaks. (Figure 7)
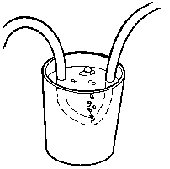
Figure 7: Hose Leak Check
- Repair leaks properly and promptly.
- Store hoses in a cool place, and protect from hot objects, and sparks.
- Do not use a single hose having more than one gas passage.
4.2.5.8 Mercury (also see section 4.3.2)
Use caution in working with mercury (Hg). The equilibrium concentration of Hg vapour over liquid mercury at room temperature is about 20 times the threshold toxic limit.
Metallic mercury and mercury compounds can be absorbed into the body by inhalation, ingestion, or contact with the skin, but breathing the vapour is the most common cause of mercury poisoning. Mercury is a very subtle poison, the effects of which are cumulative and not readily reversible. Short exposures to high levels of mercury can cause acute poisoning. The lethal oral dose is 1.0 to 2.0 g. Additionally, mercury and its compounds are skin irritants; a solution of as little as one part of salts in 4000 parts of water can be very irritating to the unbroken skin and has been reported to be capable of causing sensitization dermatitis.
Note that Hg is a designated substance:
“Individuals working with designated substances are required to comply with the “Designated Substances Regulations (O. Reg 490)”. If you work or plan to work with these materials, an assessment of the exposure or likelihood of exposure to a designated substance in the workplace must be conducted. Contact the Safety Office (ext. 33587) to request assistance in working with any designated substance.”
Bulk storage of elemental mercury should be under a layer of water and in tightly covered, thick-walled glass or preferably high-density polyethylene bottles. It is a good idea to store these bottles in secondary containers. Transfers of mercury from one bottle to another should be carried out in a hood, over a tray or pan to confine any spills.
In pouring mercury, in addition to always using funnels, one should place a basin, tray, or large beaker underneath the vessel or tube into which the mercury is being poured. This does not guarantee spill immunity, but it may at lease reduce the clean-up problem greatly. If mercury gets into the cracks of a wood or tile floor or into the pores of a concrete floor, the contamination may become so great the floor must be replaced or sealed before the lab can be safely used again; this may occur with a relatively small spill that is not properly cleaned up, but which on impact with the floor becomes dispersed that the resulting large surface area and sufficiently high vapour pressure of mercury can result in poisoning. To prevent such inconvenience, metallic mercury should be handled over impervious (stainless steel or plastic) surfaces with rims but no crevices. To prevent volatilization, the surface should not be excessively warm, i.e., not above normal room temperature (15 to 20°C).
Unsealed instruments or equipment containing elemental mercury: manometers, mercury diffusion pumps, vacuum pumps, etc.:
Manometers are used in many labs, but because of the very small surface area of mercury exposed to the atmosphere they do not pose a significant problem. Nevertheless, it is a good policy to cap the open end(s) of a manometer when it is not in use. A potentially more hazardous condition may exist with a mercury diffusion pump or where a manometer is used to continuously monitor the negative pressure produced in an evacuated chamber by a vacuum pump that is in continuous operation and that exhausts within the lab. If it is not practical to place the pump in a fume hood or run exhaust tubing to a fume hood, etc, then a feasible method of minimizing or eliminating mercury vapour release into the lab involves introducing into the system a tube or vessel containing a packing agent, which can be used as a scavenger for mercury vapour, such as activated charcoal, or Resisorb or copper turnings; copper forms an amalgam with the mercury vapour in the exhausting air or gas prior to its release into the lab environment. Because mercury is a substance with no warning properties (colourless, odourless, tasteless, etc.) the pump exhaust should be monitored regularly by exhaust air sampling; obviously this need not be done when exhausting into a fume hood or similar device.
Mercury Thermometers
Mercury thermometers are no longer allowed on campus as people tend to place them in ovens and/or break them. This could lead to possible exposure, especially if the mercury gets heated. This increases the level of vapour and level of exposure. Replace with an alcohol thermometer or a thermocouple
4.2.5.9 Cryogenic Gases
Cryogenic liquids (argon, nitrogen, helium, hydrogen and oxygen) and certain other liquefied gases are at extremely low temperatures (-60/C to -266/C). Very small amounts of these liquids produce large amounts of gas. Consult the product's SDS for specific guidelines regarding health and safety information, personal protective equipment and emergency recommendations.
Safety precautions that must be taken with compressed gases also apply to cryogenic liquids (see compressed gas standard). There are, however, additional precautions necessary when dealing with cryogenic materials.
Contact with cryogenic materials can rapidly freeze and destroy skin tissues. If exposed:
- Contact a physician immediately.
- Remove all clothing that may restrict circulation to the frozen area.
- Flush affected area with warm, not hot, water. Water temperature should be between 40/C- 46/C. Do not use dry heat.
- Do not rub frozen body parts, before or after warming.
- Keep patient warm and resting.
- Cover thawed body part with dry sterile gauze and large, bulky protective clothing.
- Do not allow patient to drink alcohol or smoke.
Common materials such as carbon steel, plastic, and rubber may become brittle or fracture after contact with cryogenic liquids.
Storage
Cryogenic liquid containers are specially designed to reduce heat loss. This design consists of an inner container and an outer casing, which are separated by a vacuum and special insulation. This construction makes cryogenic containers more fragile than other compressed gas cylinders. For this reason cryogenic containers must be handled with extreme care:
- Use dollies for moving cryogenic containers. Avoid rolling containers by holding the neck as it is the main support for the inner portion of the container.
- Keep containers clean. Avoid contaminating them with materials which may create hazardous conditions upon contact with the cryogenic fluid or gas.
- Report all leaking or improperly set relief valves, as well as safety valves with broken seals or with any frost, ice formation, or excessive corrosion to the supplier.
- Remove the container to a remote location and contact the supplier if plugs of ice or foreign material develop in container vents or opening. Do not attempt to remove the plug.
- Vent containers with an approved safety device which permits excess gas to escape.
- Label containers clearly.
- Avoid heating or welding containers which contain a cryogen.
- Do not store oxygen with any other gases except gaseous nitrogen or gaseous carbon dioxide.
- Do not store liquid nitrogen with helium, hydrogen or oxygen.
Personal Protective Equipment
- Use protective gloves when any material that comes in contact with cold liquids and their vapours is being handled. Gloves should be loose fitting, so that they can be removed quickly if liquids are spilled into them.
- Wear safety glasses, if spraying or splashing is likely a face shield should be worn.
- Cuffless trousers should cover the top of and remain outside of boots or work shoes.
General Safety Precautions
- Use and store cryogenic materials only in well ventilated areas. Cryogenic gases are capable of displacing air necessary for respiration and causing asphyxiation.
- Never allow any unprotected part of the body to touch uninsulated pipes or vessels that contain cryogenic fluids.
- Avoid wearing clothing or jewellery (watches, rings, etc.) which may trap a cryogenic fluid close to the skin.
- Use tongs to withdraw objects immersed in a cryogenic liquid.
- Perform operations slowly to minimize boiling and splashing when charging a warm condenser or when inserting objects into a cryogenic liquid.
- Remove all combustible materials from the area, especially oil or gases when handling liquid oxygen. NO SMOKING signs should be posted.
- Change and air all clothing that has been splashed with liquid oxygen immediately. Material may absorb pure oxygen and become highly flammable.
4.2.5.10 Nano-Materials
Risk Assessment
University safety policy states that for experiments involving nanomaterials, a risk assessment must be completed.
Table 12: Nano-Materials Risk Assessment Guide
Risk Level 1 |
Form |
Bonded or fixed nanomaterial |
Material (examples) |
Nanotube polymers |
|
Ventilation Controls |
General Laboratory Ventilation |
|
PPE |
Nitrile gloves |
|
Spills |
Laboratory Personnel |
|
Risk Level 2 |
Form |
Suspended in liquid (low toxicity) with no aerosol generation |
Material (examples) |
Silver or Gold Nanotubes or nanoparticles |
|
Ventilation Controls |
Fume hood or Class II, Type A2 BioSafety Cabinet non ducted |
|
PPE |
Nitrile gloves |
|
Spills |
UW Spill Team (Spills outside containment) |
|
Risk Level 3 |
Form |
Dry dispersible |
Material (examples) |
Quantum dots |
|
Ventilation Controls |
Fume hood with HEPA Filter or Class II, Type B2 BioSafety Cabinet thimble ducted or Glove box |
|
PPE |
Nitrile gloves |
|
Spills |
UW Spill Team (Spills outside containment) |
Storage
- Tightly sealed container
- Over packed with sealed bag
- Label Nanomaterial with description (ie Nanomaterial contains nano-silver material)
Labeling Work Area
Label work enclosures (Fume hoods, BSC’s and Glove boxes) “Warning Nano Hazard”
Ventilated Enclosures
Fume Hood
- The fume hood must meet the minimum design criteria outlined in CSA Z316.5-94. and meet or exceed performance standards specified by ANSI/ASHRAE 110-1995 .
- Fume Hood equipped with Certified HEPA filter that can be changed bag in-bag out
- Suitable for work with volatile chemicals(solvents) or radioactive work
BioSafety Cabinets
Class II, Type A2 Cabinet
- Exhaust air ducted back into laboratory or out of laboratory by thimble connection
- Face velocity of 100 ft/min
- HEPA filter is changeable using BAG In and Bag Out
- Ducts in hoods under negative pressure, if they leak the material will stay in the duct work.
- Not suitable for work with volatile chemicals or radioactive work
Class II, Type B2 Cabinet
- Exhaust air ducted out of laboratory by thimble connection
- Face velocity of 100 ft/min
- HEPA filter is changeable using BAG In and Bag Out
- Ducts in hoods under negative pressure, if they leak the material will stay in the duct work.
- Suitable for work with volatile chemicals(solvents) or radioactive work
Alternate Enclosures
There a numerous manufactures of ventilated enclosures that have been designed for using nano materials.
The following criteria must be met.
- Certified HEPA filter that can be changed bag in-bag out
- Face velocity of 60-70 ft/min
- If volatile chemicals are used exhaust air must be ducted via thimble connection.
4.2.6 Peroxidizable Organic Chemicals
Organic peroxides are carbon-based chemicals that contain the characteristic peroxide O-O bond many organic peroxides are shock, heat, or friction sensitive. The inadvertent production or concentration of organic peroxides has been the cause of many well-documented accidents.
The procedures outlined below are designed to prevent or limit the formation of organic peroxides.
4.2.6.1 Moieties that may form Peroxides
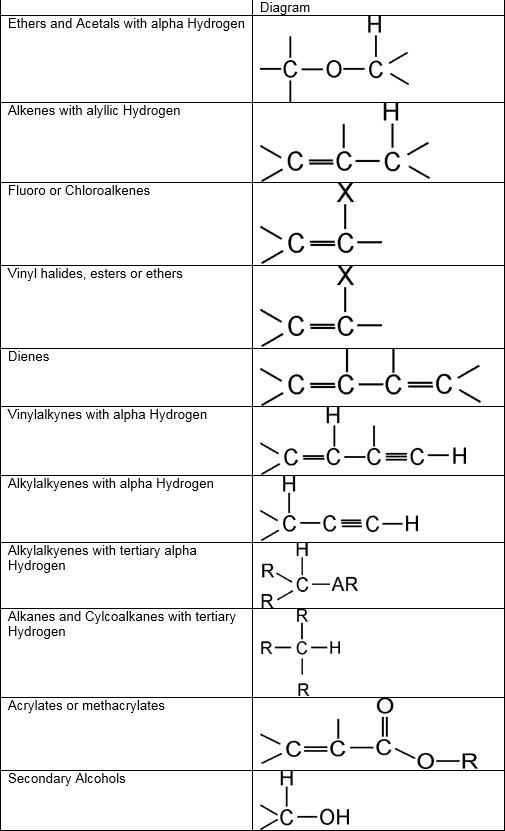
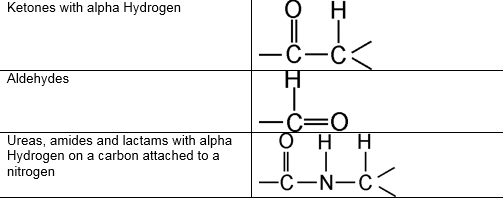
4.2.6.2 Classes of Peroxides Formers
Class A |
Class B |
Class C |
Chemicals that form explosive levels of peroxides without concentration |
Chemicals that form explosive levels of peroxides on concentration |
Chemicals that may autopolymerize as result of peroxide accumulation |
3 months |
12 months |
Uninhibited chemicals 24 hours Inhibited chemicals 12 months |
Butadienea Chloroprenea Divinylacetylene Isopropyl ether Tetrafluoroethylenea Vinylidene chloride |
Acetal Acetaldehyde Benzyl alcohol 2-Butanol Cumene Cyclohexanol 2-Cyclohexen-1-ol Cyclohexene Decahydronaphthalene Diacetylene Dicyclopentadiene Diethyl ether Diethylene glycol dimethyl Ether Dioxanes Ethylene glycol dimethyl Ether 4-Heptanol 2-Hexanol Isopropyl alcohol Methylacetylene 3-Methyl-1-butanol Methylcyclopentane Methyl isobutyl ketone 4-Methyl-2-pentanol 2-Pentanol 4-Penten-1-ol 1-Phenylethanol 2-Phenylethanol Tetrahydrofuran Tetrahydronaphthalene Vinyl ethers Other secondary alcohols |
Acrylic acidb Acrylonitrileb Butadienec Chloroprenec Chlorotrifluoroethylene Methyl methacrylateb Styrene Tetrafluoroethylenec Vinyl acetate Vinylacetylene Vinylchloride Vinylpyridine Vinyladiene chloride |
Notes:
- When stored as a liquid monomer.
- Although these chemicals form peroxides, no explosion involving these monomers has been reported.
- When stored in liquid form, these chemicals form explosive levels of peroxides without concentration. They may also be stored as a gas in a cylinder. When stored as a gas, these chemicals may auto polymerize as a result of peroxide accumulation.
4.2.6.3 Maximum Levels of Peroxides
100 ppm is the maximum allowable concentration of peroxides in peroxide forming organic chemicals. Note that there could be elevated concentrations of peroxides on the threads of screw cap bottles as a result of evaporation.
4.2.6.4 Inhibitors
Inhibitors can greatly increase the safe storage life of peroxide forming organic chemicals. These compounds are depleted over time and must be replenished periodically.
4.2.6.5 Storage
Peroxidizable chemicals must be dated when received. If the material is kept longer than the recommended storage time the material will be tested for peroxides and the test date and results attached to the container. If the peroxide content exceeds 100 ppm the material will be disposed of or the peroxides neutralized.
4.2.6.6 Handling
Procedures which result in evaporation of peroxide formers or extensive exposure to air or oxygen should be avoided. Distillation of any peroxide former should not be attempted unless the material has been tested for the presence of peroxide. Uninhibited Class C chemicals should not be distilled.
4.3 Chemical Spills
4.3.1 General
Prior to work with hazardous materials:
- Determine spill procedures from SDS for all chemicals.
- All UW employees and students handling hazardous materials are required to be trained in spill procedures.
- Obtain proper spill kits and clean up equipment. Available from Chemistry Stores ESC 109.
For a small spill that poses no immediate threat to health:
- Notify occupants in the immediate area of the spill
- Use spill kits to absorb and contain according to spill procedure.
- Place material in a secure and ventilated area
- Contact Safety Office at Ext. 36268 for disposal instructions.
For large spills or spills that pose an immediate threat to health:
- Remove sources of ignition if possible.
- Evacuate immediate area.
- Activate wall-mounted fire alarm pull station located at exits.
- Call UW POLICE x22222
Additional Precautions for Flammable Liquids
- Immediately remove all sources of ignition from the area.
- Identify location of nearest fire extinguisher(s)
- Use non-sparking tools (e.g., bronze) during clean up.
4.3.1.1 Chemical Neutralization of Acids and Bases
Effective chemical neutralization depends on the chemistry of the particular spill substance and requires an exact identification of the spill. Neutralization can also create heat causing boiling and spattering of the spill substance. Never attempt neutralization unless results are certain.
Neutralization Procedures
- Be sure that the neutralizing agent is suitable for use on the spill substance.
- When using neutralization kit, follow directions exactly.
- Add the neutralizing chemical cautiously and in relatively small amounts to minimize the creation of heat.
- Apply the neutralizer from the perimeter inward and thoroughly mix the neutralizing agent with the spilled substance until the spill has been completely neutralized. The neutralizing agent in some pre-packaged kits will change colour to indicate complete neutralization.
- Once the spill has been completely neutralized, the substance can be disposed of in accordance with approved procedures.
Strong acids: use a weak base, e.g. soda ash (sodium carbonate)
Strong caustic: use a weak acid, e.g. acetic
Oxidizing agent: use a mild reducing agent
Reducing agent: use a mild oxidizing agent
The exact neutralizer to be used on a particular spill should be identified in advance as part of the Research Project Health and Safety Assessment (see section 3.1).
4.3.1.2 Absorbents for Solvents or Acids and Bases
Sorbents (such as clay, vermiculite, or amorphous silica) are available in the form of loose or bulk material or in the form of pre-packaged pillows or pads. They have the advantage of multi-purpose use, as they can be applied to different types of liquid spills-acids, caustics, liquids, or flammable solvents. The sorbent material used must be non-reactive with the spill substance. Use of an absorbent does not eliminate or neutralize the potential hazard of the spilled substance.
Absorption Procedures
- Apply the sorbent carefully from the outer edge to the centre to avoid spreading the spill.
- Avoid touching or stepping into the spill or saturated sorbent.
- Avoid inhaling any vapours.
- Label and dispose of contaminated sorbent in accordance with the approved procedure applicable to the hazardous substance.
After neutralizing or absorbing the spill substance, clean the contaminated area thoroughly with a non-flammable detergent and water, and mop it dry.
4.3.2 Mercury (also see section 4.2.5.8)
Spilled mercury must be immediately and thoroughly cleaned up. Pools and droplets of metallic mercury can be pushed together and then collected, preferably by suction using an aspirator bulb or a vacuum in which the mercury is collected under water. Alternatively, mercury spill clean-up kits are commercially available. If mercury is suspected of remaining behind, the area may be further decontaminated by creating a chemical reaction with zinc metal producing an amylogen. NOTE: sulfur powder is used to indicate the presence of mercury only. It is not a decontamination agent.
Immediately after a spill and during clean up, the area must be closed to unauthorized persons and No Admittance signs posted. Since mercury can cling to clothing and other items, it is imperative that anyone involved in clean up and decontamination activities wear disposable gloves and shoe covers. Disposable mercury vapour respirators must be worn by those involved in the clean-up of large spills. When the clean-up is complete, the gloves, shoe covers, and respirator (if needed) must be disposed of and hands, arms and face thoroughly washed several times.
- Domestic vacuum cleaners must not be used since they will only disperse mercury aerosols and increase contamination.
- Sweeping must be avoided because it creates dust and breaks the mercury into even smaller particles that can vaporize more quickly.
- Similarly, compressed air must not be used to blow mercury off equipment or clothes, because it can disperse the mercury throughout the work area.
Waste Mercury Disposal
Significant quantities of metallic mercury from spills or broken thermometers or other equipment and contaminated mercury from laboratory activities should be collected in thick-walled, high-density polyethylene bottles for reclamation. See ChE Safety Officer - Charles Dal Castel (E6-3102).
Rags, sponges, shoe covers, and such used in clean-up activities, and broken thermometers containing small amounts of residual mercury should be placed in a sealed plastic bag, labelled, and disposed of in a safe manner (see section 4.4.1 below).
4.3.3 Nano-Material Spill Procedure
Risk Level 2 and 3 (Inside containment)
- Use PPE appropriate for risk level
- Notify occupants of laboratory.
- Use absorbent material with an appropriate solvent to wet wipe the areas or HEPA filtered vacuum.
- Place all cleaning materials, disposable PPE and waste in plastic bag.
- Seal and wipe exterior
- Place bag in secondary bag
- Seal secondary bag and wipe exterior
- Label Nanomaterial waste with description for disposal (e.g. Nanomaterial contains nano-silver material)
Spills Procedures Risk Level 2 and 3 (Outside containment)
- Evacuate occupants of laboratory, close laboratory door and secure area.
- Contact UWaterloo Police at Ext. 22222.
- Provide the following information
- Location of Spill
- Material
- Quantity
- Assessment of risk
- Remain with uWaterloo Police until spill team arrives.
4.4 Chemical and Biological Waste Disposal
4.4.1 Chemical Wastes
A centralized chemical waste disposal system is available at the University of Waterloo, using the facilities of the Department of Chemistry (Chemistry Storeroom, ESC 122, x35755. Except for certain substances (see exceptions listed in Appendix 2), waste or outdated chemicals in appropriate containers which are clearly labelled in accordance with specified requirements (see below) may be brought to the Chemistry Storeroom (ESC 122) for storage and subsequent pick-up by the contractor handling waste chemical removal. However, any waste which must be kept under refrigeration or in a fume hood for safety reasons cannot be stored in ESC 122. The Chemistry storekeeper should be notified of the location of such a stored waste, which will be picked up at its local storage site on the day of the next pickup by the contractor.
Chemical waste drop-off for the ChE department occurs as follows:
- DWE- Tuesdays from 1:00 to 1:20 in DWE-1521 (heavy lab)
- E6 – Tuesdays from 2:00 to 2:20pm in E6-1022
Packaging Instructions
Do not mix waste. Use a separate container for each waste.
- All material must be placed in an appropriate container (container material will not be degraded by contents).
- The following containers are available without charge from the Environmental Safety Facility (ESF):
|
![]() |
Bio waste Containers |
![]() |
- Container must be sealed (leaking containers will not be accepted) and placed in secondary containment during transport.
- Containers must be clean on the exterior and are to be labelled with the UW waste label (available from ESF) and contents listed.
- Liquid containers should be only 80% full.
- Store waste bottle in a secure area (not on floor).
- Unknown substances will be accepted (an account number is required for classification of unknown).
Waste |
Description |
Examples |
|
Solvents |
|||
Non Halogenated Solvents |
|
|
|
Halogenated Solvents |
|
|
|
Sample Vials |
|||
1 |
Halogenated |
|
|
2 |
Non-Halogenated |
|
|
3 |
Aqueous |
|
|
4 |
Solid |
|
|
Aqueous Waste |
|||
1 |
Water contaminated with Non halogenated Solvents |
|
|
2 |
Water contaminated with halogenated Solvents |
|
|
3 |
Heavy metals |
|
|
4 |
Inorganic Salts |
|
|
5 |
Cyanides |
|
|
6 |
Organic material |
|
|
Oxidizers |
|
||
Acids |
|||
1 |
Mineral Acids |
|
|
2 |
Organic Acids |
|
|
Bases |
|
||
Metals |
|
||
Organic |
|
||
Air Reactive |
|
|
|
Water Reactive |
|
|
|
Paints |
|||
1 |
Latex paints |
|
|
2 |
Oil Based or alkyd paints |
|
|
3 |
Paint solvents |
|
|
Monomers |
|
|
|
Organic Peroxides |
|
||
Silica |
|
|
|
Solid Waste |
|||
1 |
Contaminated with organic compounds |
|
|
2 |
Contaminated with inorganic compounds |
|
|
Labelling
All containers of waste chemical must be labelled with the following information:
1. Mandatory information
1.1 Scientific name(s) of chemical(s). A trade name is not acceptable.
1.2 Amount (approximate).
1.3 Department of origin.
1.4 Name of professor and student or other researcher.
2. Desired information
2.1 When chemical identity is known, list the Group Code (see Appendix 2).
2.2 Unknowns: label as unknown, but include any information on its probable contents.
Figure 4 (see p. 37) shows a pre-printed adhesive label, available at Chemical Eng. Stores.
4.4.2 Biological Wastes
Bio-Waste
1 |
Medical |
|
|
2 |
Sharps |
|
|
3 |
Animal Frozen |
|
|
4 |
Animal Preserved |
|
All liquid or solid wastes that contain or may contain biological material (organisms, plasmids, enzymes, etc.) must be autoclaved before disposal. Such wastes include:
- sample residues and spent inoculum
- Petri dish or test tube cultures on agar
- residual biomass in fermenters or shake flasks
- filtrates and supernatants (microporous-filtered liquids are not 100% organism-free)
All microorganisms for disposal are to be treated as if they were potential pathogens.
Figure 8: Chemical Waste Disposal Label
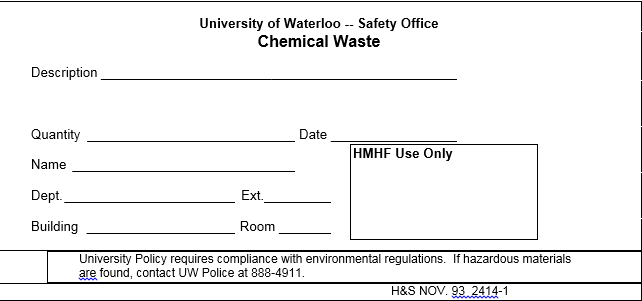
For recombinant organisms, you must use time-temperature exposure conditions known by prior testing to effectively sterilize the organisms. The safety of recombinant DNA materials for disposal must be verified a priori by quantitative testing of standard disposal samples (type of biological material; liquid volume; container type).
The design of apparatus and systems and the proposed operating, sampling, containment, and disposal procedures for all experiments involving pathogenic or recombinant organisms must be approved in advance of the project start by the UW Biological Safety Officer (see p. iii)
4.4.3 Nano-Material Wastes
- Place waste in plastic bag.
- Seal and wipe exterior.
- Place bag in secondary bag.
- Seal and wipe exterior.
- Label Nano-material waste with description for disposal (ie Nano-material contains nano-silver material) (see 4.4.1)
- Take to the Environmental Safety Facility for disposal or arrange a pickup.
4.5 Disposition of Chemical or Biological Inventories and Wastes upon Termination of Project Work
When a researcher completes his or her work on a particular research project, and before leaving the Department, he or she is responsible for the following:
- Collection, correct identification, required labelling (see section 4.4.1) of all project-related chemical wastes and forwarding of same for disposal.
- Deactivation of all project-related biological wastes or residues by validated procedures (see section 4.4.2)
- Full identification (i.e., labelling, including the control information described in section 4.2.1) of and use of safe storage containers and conditions for all chemical and biological agents to be retained for future use on the project.
- Each research apparatus or instrument is left in a safe working condition; otherwise it should be tagged DO NOT USE, stating the defects.
The research supervisor should ensure that the above requirements have been met. If the researcher has not fulfilled these requirements, the supervisor assumes personal responsibility for ensuring that these requirements are satisfied at once.