Introduction
Currently, the need to improve automobile efficiency through weight reduction is apparent and one method in which this can be realized is through the use of hydroforming to manufacture conventional automobile structural components. A schematic of a pre-bent and hydroformed tube is shown below.
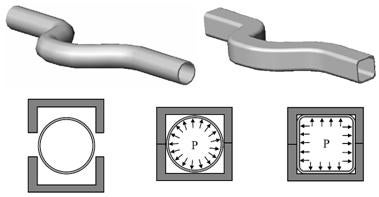
Typical hydroforming process schematic
Typically, automobile structural components are manufactured using the stamping and welding processes, but by hydroforming a continuously bent steel tube, the following advantages can be realized:
- weight reduction (improved fuel efficiency)
- improved strength and stiffness due to continuous sections
- part consolidation and reduced scrap
- better dimensional accuracy
- reduced cost due to a reduction in labour
- equipment and energy consumption
Inherently, weight reduction is an advantage that hydroformed components possess over stamped and welded parts. This advantage can be further exploited through the use of high-strength steels (HSS), advanced high-strength steels (AHSS) and aluminum. The inherently lower ductility/formability of these materials limits their expansion during hydroforming due to premature fracture (burst), therefore techniques such as end-feeding and pre-bending optimization are required to manufacture a functional part.
The focus of the hydroforming program at the University of Waterloo is on 3.0” O.D. tubes. The types of parts that have been hydroformed include straight and pre-bent tubes. Both “high pressure” and “low pressure” hydroforming experiments are conducted at the University of Waterloo. The following geometries and the type of hydroforming process (high or low pressure) have been produced:
- Straight Tube (high and low pressure)
- 90° Pre-Bent Tubes bend radii of R/D 2.0 and 2.5 (high pressure)
- S-Rails with bend radii of R/D 1.5, 2.0 and 2.5 (high and low pressure)
- Tailor Welded Straight Tubes and Tailor Welded S-Rails
![(a) Straight tube hydroforming [DP600] (b) Pre-bent tube hydroforming [DP600] (c) S-Rail [AA5754]](/waterloo-forming-crash-lab/sites/default/files/uploads/images/prebent.jpg)
(a) Straight tube hydroforming [DP600] (b) Pre-bent tube hydroforming [DP600] (c) S-Rail [AA5754]
The tube alloys that have been tested at the University of Waterloo include:
- Dual Phase Steel (DP600, DP800)
- High Strength Low Alloy Steel (HSLA350)
- Drawing Quality Steel (DDQ, DQAK)
- Interstitial-Free Steel (IF)
- Aluminum (EN-AW5018, AA5754)
Experimental: Tube Bending
An Eagle Precision Technologies EPT-100 hydraulic mandrel-rotary draw tube bender at the University of Waterloo is used to conduct all of the bending experiments for this work as shown in the figure below. This industrial grade tube bender was retrofit with a closed-loop servo-hydraulic controls system that is run with a PC-based control and data acquisition system. A mix of MTS 406 and MTS FlexTest servo-hydraulic controllers are used. A custom in-house LabVIEW program is used to control the instrumented tube bender.
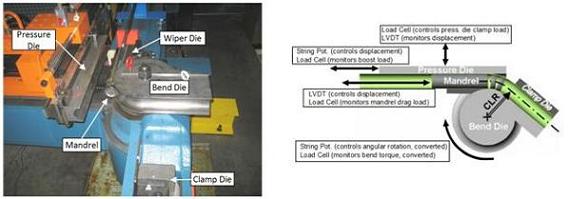
Instrumented mandrel-rotary draw tube bender at the University of Waterloo
The goal of the pre-bending work is to improve the formability of the tubes in the subsequent hydroforming operation. Improved formability can be achieved by the reduction of thinning during pre-bending, which delays the onset of fracture (burst) during hydroforming. The three main process parameters that are investigated in the pre-bending operation are (1) lubrication condition (2) bend severity and most significantly (3) the application of bending boost. The below figure shows the reduction of thinning for increased bending boost levels.
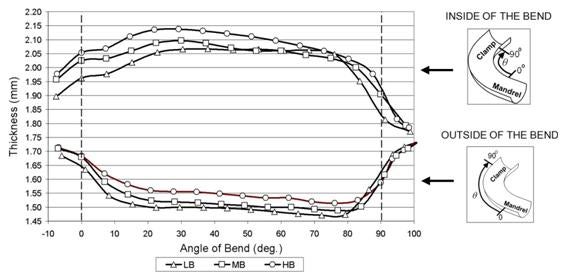
Thickness distribution of an IF steel tube due to low (LB), medium (MB) and high (HB) boost conditions
Experimental: Hydroforming
Hydroforming experiments are performed at the University of Waterloo, using the 1,000Ton (2 million lbf) Macrodyne press shown below. To generate the internal pressure required for hydroforming, a high pressure intensifier is used to boost the internal water pressure to a maximum pressure of 414MPa (60ksi). For high pressure hydroforming experiments, hydraulic end-feed (EF) actuators are used to seal the tube and apply an axial EF load during hydroforming. The actuators each have a capacity of 1,112kN (250kip). For low pressure hydroforming experiments, end-plugs are used. A polymeric o-ring is used to created the seal between the inside diameter of the tube and the EF ram/end-plug. The leading edge of the o-ring expands radially upon application of pressure from the inside of the tube. A teflon ring is used as a back up seal by expanding radially when compressed by the o-ring.
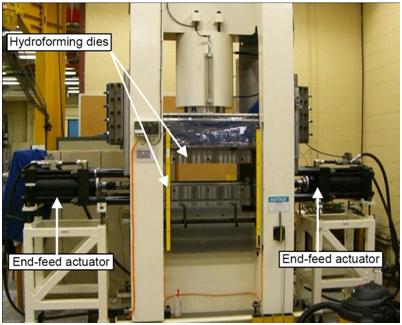
1,000 Ton hydroforming press at the University of Waterloo
Finite Element Modeling
Finite Element Modeling (FEM) codes are able to accurately simulate complex real-world problems such as metal forming. The computational power and speed of computers available today has increased to such an extent that these codes are now able to generate models quickly and accurately to aid in the design and development of industrial manufacturing processes, such as tube bending and hydroforming. After these models have been experimentally validated, they become extremely useful tools that allow the effect of many different factors to be explored without the need for expensive experimental testing.
The dynamic FEM code LS-DYNA is used to model the complex pre-bending and subsequent hydroforming process as shown by the FE models below. Of great importance, is the validity of these models, which is determined by comparing the predicted results to the experiments. Replicating the experimental boundary conditions is crucial to the success of the models. The instrumentation on the tube bender and hydroforming apparatus measures the boundary conditions (loads and displacements) which are used for validation purposes.
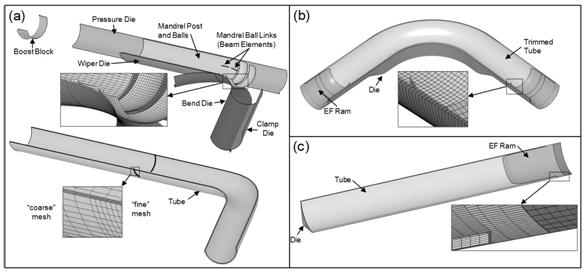
FE mesh of (a) pre-bending (b) pre-bent hydroforming with end-feed (c) straight tube hydroforming FE models
The predicted (FE) and measured (exp.) thickness/strain distributions after pre-bending and hydroforming are often compared for model validation. In the figure below, the thickness and strain distributions of a hydroformed DP600 straight tube show excellent agreement between the models and experiments, which provides confidence in the FE models.
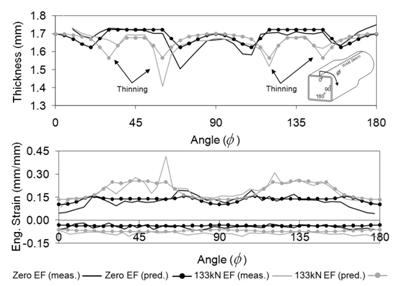
Predicted and measured thickness/strain distributions for straight tube hydroforming of DP600 with zero and 133kN end-feed loads (just prior to burst)
The main goal of hydroforming advanced high strength steels and aluminum tubes is to increase the formability during the process by applying an end-feed load which delays the onset of fracture (burst). Below, the predicted and measured effect of end-feed load on corner-fill expansion (measure of formability) is shown for both straight and pre-bent DP600 tubes. The accuracy of the models is good and considerable increases of formability are shown.
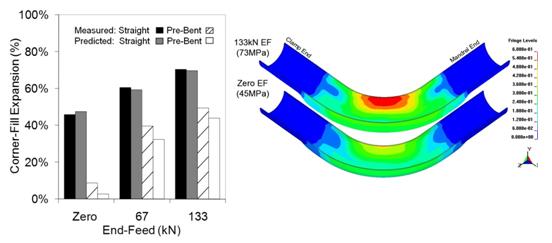
Predicted and measured corner-fill expansion (formability indicator) for straight and pre-bent DP600 tubes with various levels of end-feed load (just prior to burst). Contours of effective plastic strain for the pre-bent hydroformed tubes at zero and 133kN end-feed loads.
As a result of the pre-bending and hydroforming work conducted at the University of Waterloo, the Extended Stress-Based Failure Criterion (XSFLC) was developed to predict the onset fracture in hydroforming. Free-expansion burst tests are used to calibrate the criterion which has the ability to accurately predict necking (failure) pressure, corner-fill expansion and fracture location as shown below for DP600 straight tubes at various levels of end-feed.
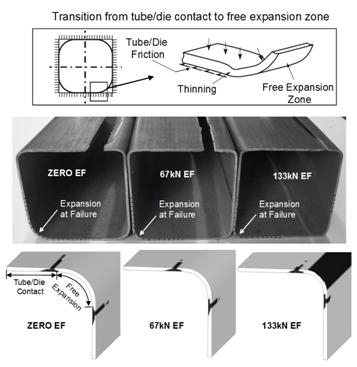
Predicted (XSFLC) failure locations and corner expansions due to various levels of end-feed load for DP600 straight tubes