Introduction
Sheet metal aluminum alloys are prime candidates for use in the automotive industry because of their good strength and stiffness-to-weight ratios. Aluminum sheet alloys only typically posses moderate formability at room temperature, limiting their design applications. Warm forming of these alloys can significantly improve their formability and this is the main focus of the warm forming research at the University of Waterloo. A large component of this work is on the development of finite element constitutive models that are able to capture the anisotropic behaviour of these metals at elevated temperatures and strain rates. The research described below is focused on the warm forming of both age-hardenable and non-age-hardenable sheet aluminum alloys and the general characterization of the effect of temperature on these metals.
Structural Alloys
Warm forming experiments on age-hardenable 6xxx and 7xxx sheet aluminum alloys are conducted to characterize the material’s formability, drawability, constitutive response at elevated temperatures and strain rates and as-processed energy absorption characteristics.
A schematic of the warm forming apparatus at the University of Waterloo is shown below for the Nakazima limiting dome height (LDH) configuration. LDH testing is performed on a triple acting servo-hydraulic press with heater cartridges (PID) embedded within the tooling for isothermal and non-isothermal conditions. Different punch configurations can be utilized.
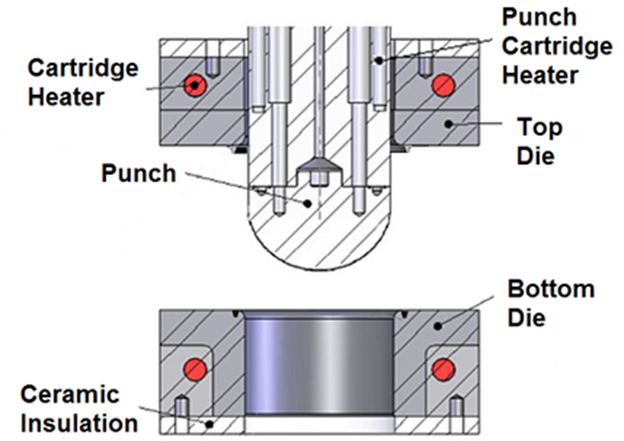
A schematic and photograph of the warm limiting dome height apparatus
![]() |
![]() |
![]() |
![]() |
Formability
Material formability is characterized through LDH testing under different proportional loading conditions, temperatures and strain rates to develop a forming limit diagram (FLD) of a given material. In-situ 3d stereoscopic digital image correlation (DIC) techniques are utilized to capture the full field strain and dome topology evolution over the duration of each LDH test.
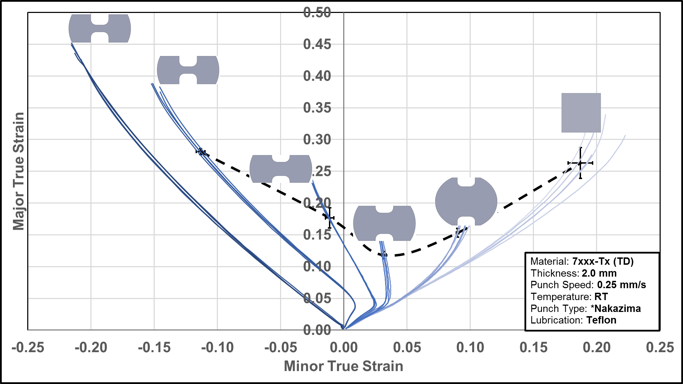
Different LDH geometries yield different loading conditions
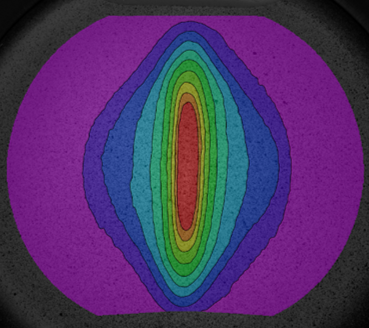
Major Strain distribution in a 200°C plane strain specimen prior to failure
Friction is controlled to the best of our abilities using different lubrication techniques. Shown below are the effects of reducing friction on the failure of a plane-strain dome specimen. Note the absence of a double-neck and failure closer to the dome apex.
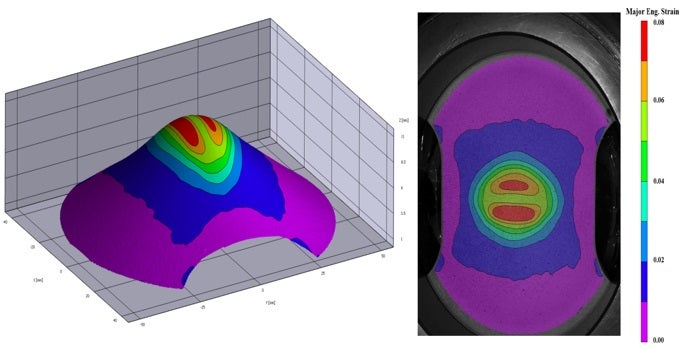
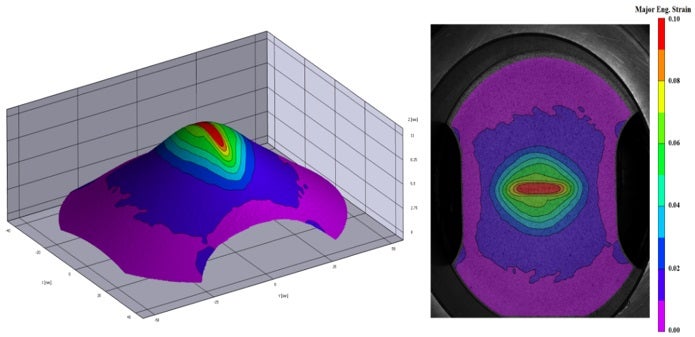
Poor lubrication versus good lubrication
Using the strain and deformation results captured through DIC analysis of each LDH test, different formability analysis techniques are implemented to assess the onset of localization within the material. Common techniques utilized at the university of Waterloo include the ISO12004-2:2008 standard and a curvature approach which captures the onset of localization balanced on a tolerance in the change in local sheet curvature during LDH testing. An example of the curvature approach is shown below.
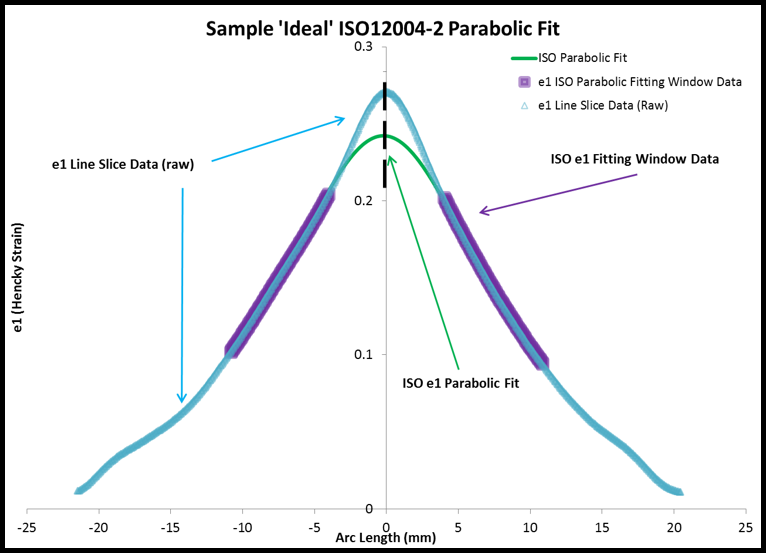
Curvature evolution in a 5182-O temper alloy
The curvature approach used at the University of Waterloo looks for local changes in sheet curvature as a measure of the onset and evolution of necking in a limiting dome height test. An example of the curvature approach is shown below for a 5182-O temper sheet alloy at room temperature and 200°C. Note that the curvature of the alloy at 200°C increases much more gradually as a function of the local strain compared to the room temperature results. The corresponding strain distributions further illustrate these observations.
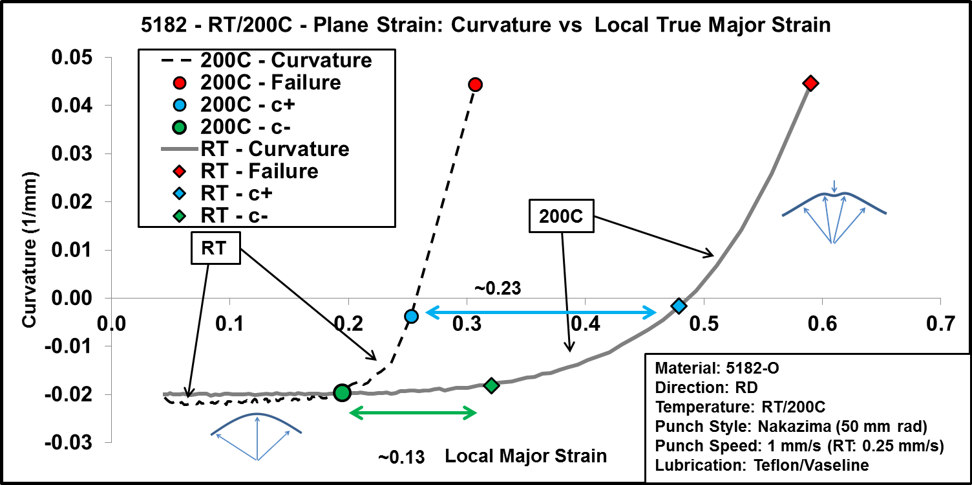
Curvature evolution in a 5182-O temper alloy
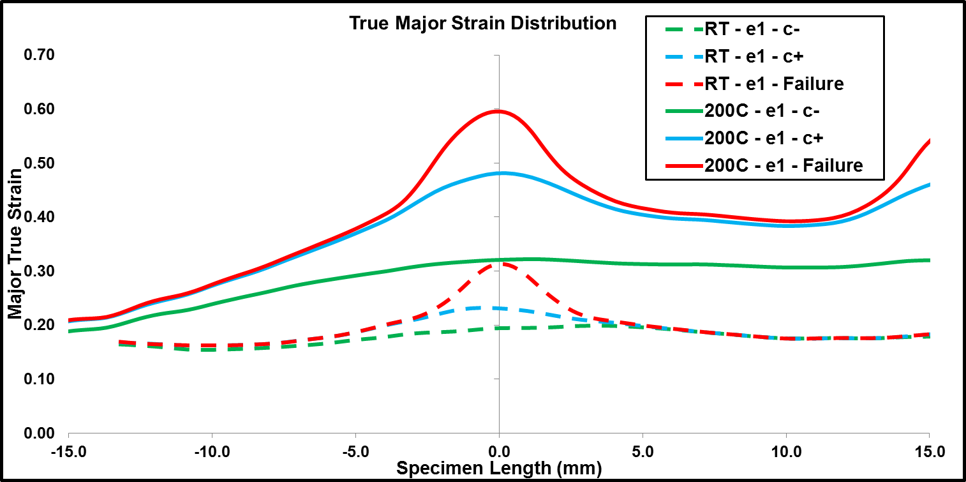
Major strain distribution in a 5182-O temper alloy at different levels of deformation at RT/200C
With a sufficient number of repeats over different temperatures and proportional loading conditions, a forming limit diagram can be generated. Shown below is an FLD for the sheet aluminum alloy 6013-T6 using the previously discussed curvature approach.
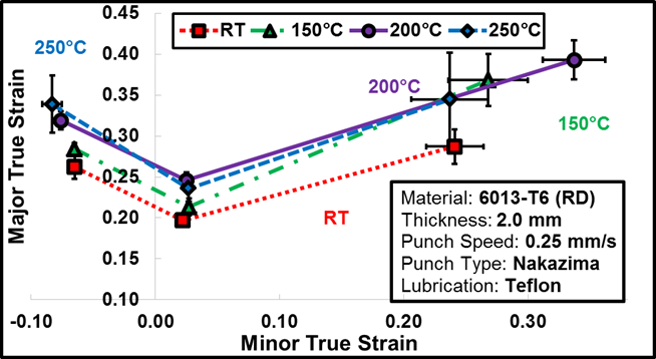
Temperature dependent FLD of 6013-T6
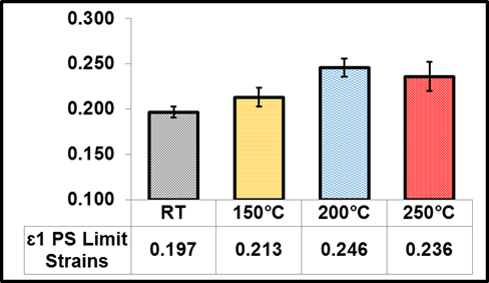
6013-T6 Plane Strain forming limit strains vs temperature
Drawability
Deep-drawability testing is conducted at the University of Waterloo to understand the impact of temperature on the drawability of these structural aluminum alloys. Shown below, it can be observed that at room-temperature, the 7075-T6 alloy cannot be drawn; however at elevated temperatures under non-isothermal conditions, excellent drawability is observed.
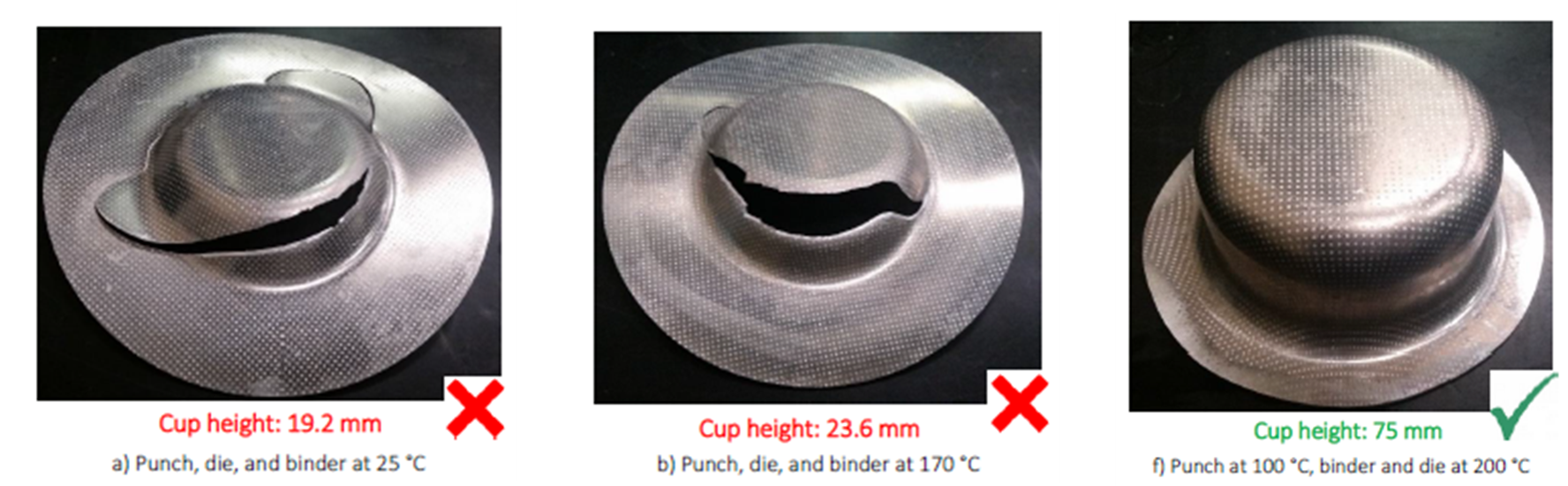
Examples of 7075-T6 deep-drawn cups under different thermal conditions
When friction is correctly minimized, elevated temperature drawability tests of structural alloys serve as excellent candidates for observing the influence of anisotropy on material drawability. Shown below are three different sheet aluminum alloys, and their respective earing responses. These observations illustrate the need for proper testing to capture the elevated temperature constitutive response of these alloys.
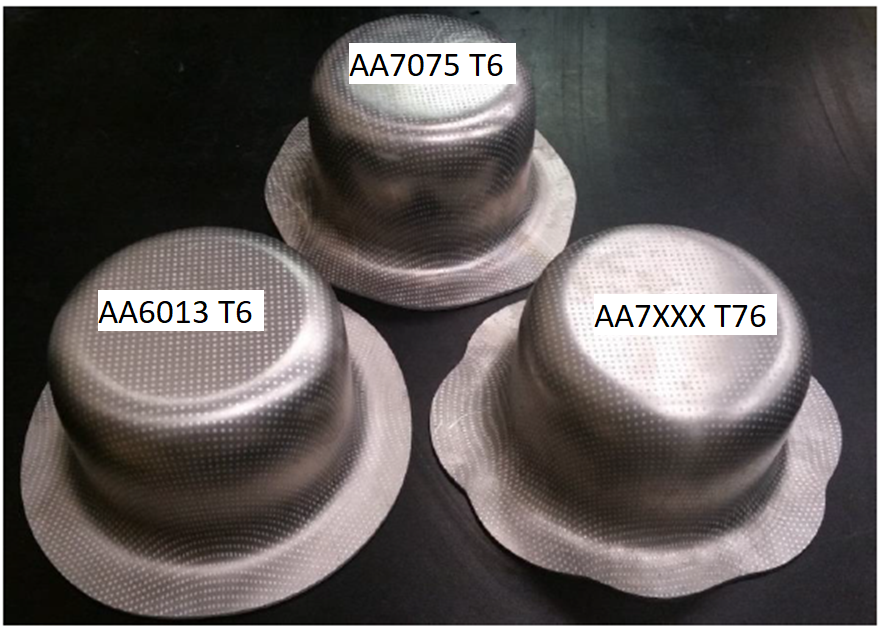
Influence of anisotropy on the earing behaviour of three different sheet aluminum alloys during elevated temperature drawability testing
Constitutive Response
The elevated temperature constitutive behavior of sheet aluminum alloys is captured using through elevated temperature tensile testing at different rates and directions. At elevated temperatures, some sheet aluminum alloys may ‘neck’ under tensile conditions at low strains, so a local area reduction technique is implemented to capture the true stress-strain response of the alloy. This is achieved using 3d stereoscopic DIC measurements of tensile specimens. Elevated temperature tensile testing is performed using a Gleeble apparatus and a MTS apparatus with a thermal chamber and optical grade glass for strain observations. An example of the local area reduction technique is shown below.
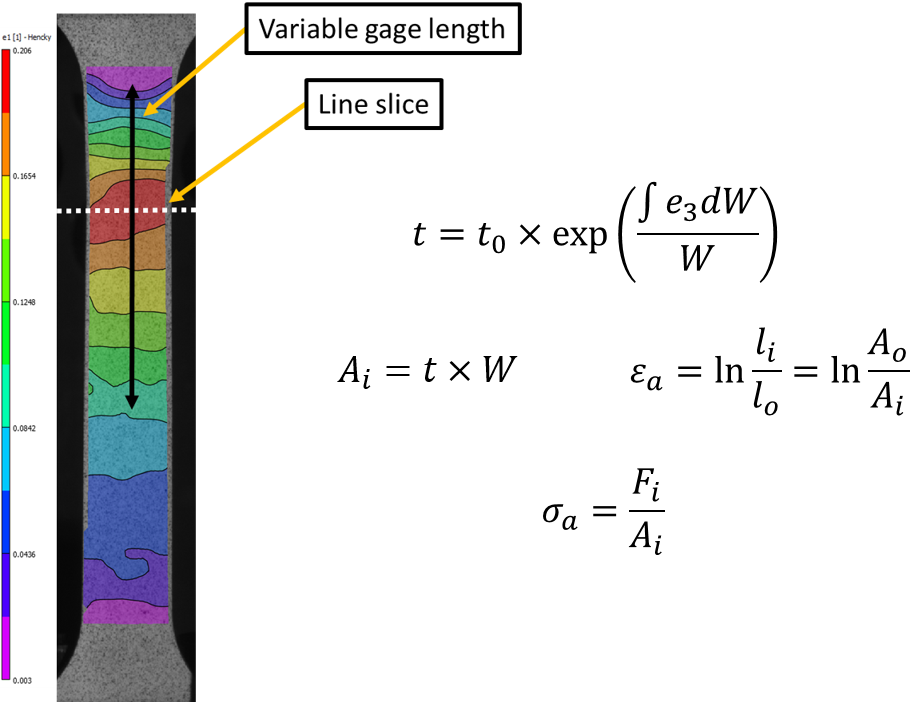
Left: Local area reduction technique. Right: Influence of gage length on the true-stress true-strain response of the alloy compared to the local area reduction technique.
The strain rate sensitivity and young’s modulus as a function of temperature is also captured using 3d stereoscopic DIC techniques.
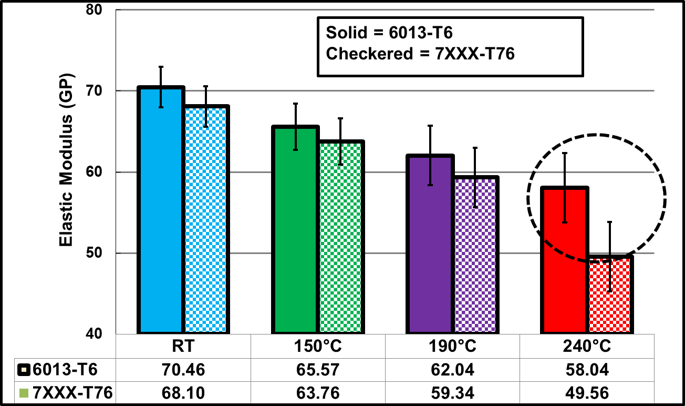
Temperature dependent elastic modulus
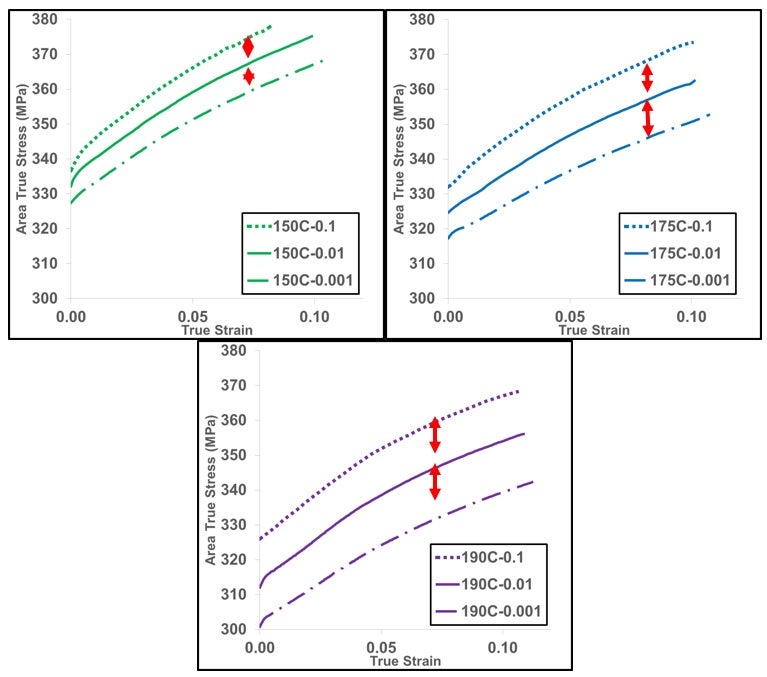
Strain-rate sensitivity and hardening response of a 6013-T6 alloy as a function of temperature
The influence of anisotropy at temperature is explored through the implementation of different yield surfaces in a deep-draw simulation using R-values and stress-ratios obtained through tensile testing in different directions. Generally speaking, the anisotropy of the structural alloys presented in this work were not found to vary significantly as a function of temperature, up to approximately 250°C.
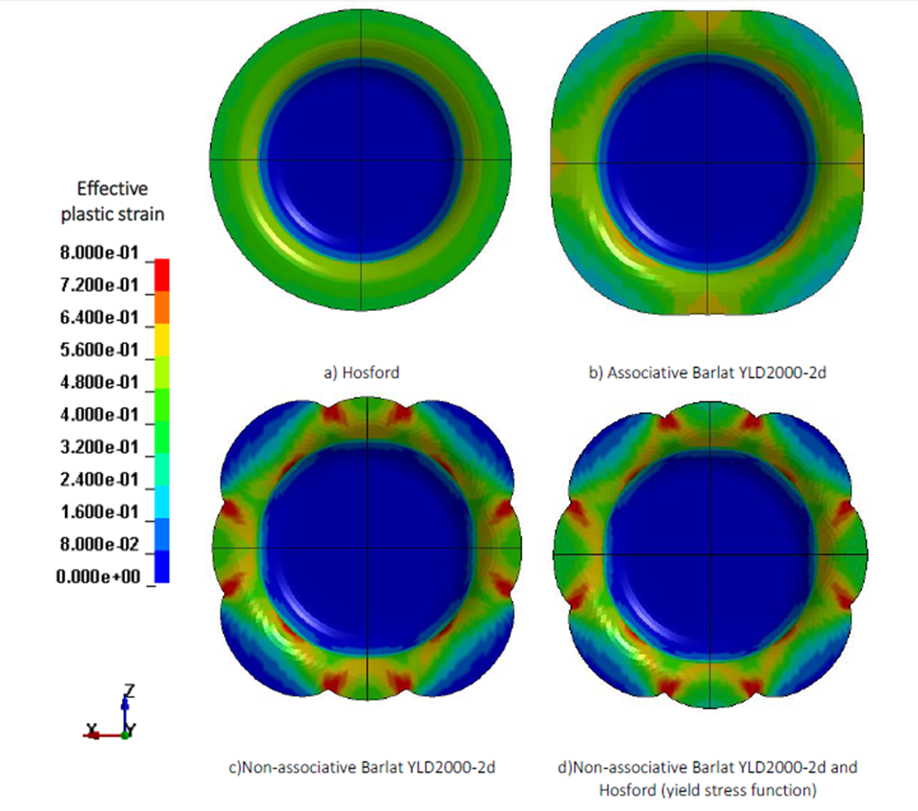
For highly anisotropic sheet alloys, only advanced yield surfaces can sufficiently capture anisotropy of the sheet material.
Modelling
Limiting dome height, deep-draw and rail forming FEM models are developed and validated against their corresponding experimental tests using the constitutive behaviour observed through coupon level testing.
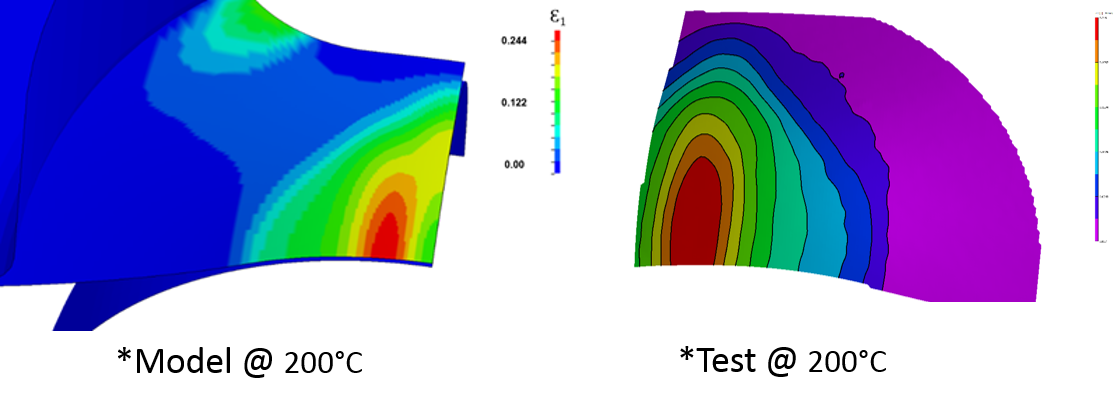
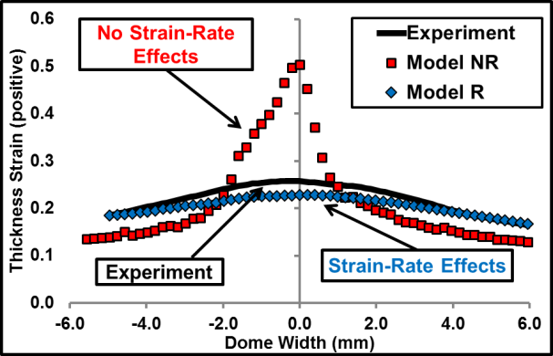

6013-T6 Plane Strain Dome Comparison: Experiments and Model at 200°C
7xxx series elevated temperature deep-draw simulation (top view)
7xxx series elevated temperature deep-draw simulation (oblique view)