Introduction
A key performance indicator limiting the potential of aluminum alloy sheet in automotive body panels is dent resistance. Dent resistance is a function of many coupled influences such as panel stiffness, curvature, support conditions, and strength. In addition, the effects of prior work, that is, thickness reductions and work hardening during panel stamping must be considered. Two types of dent resistance are considered, static and dynamic. The difference being the nature of the applied load, static loading is typified by a hand pushing slowly on a hood, while dynamic loading is driven by inertia and contact forces generated during an impact. This work involves prediction of dent resistance for aluminum panels using the finite element method, and validation of these predictions using experimental testing.
Forming Models
Forming strain predictions from a finite element model are required to accurately predict dent resistance for a given panel.
Structural Models
Real automotive panels have stiffening supports which affect panel dent resistance and therefore must be considered.
Mesh Refinement & Stress/Strain Remapping
The FE models used in industry lack sufficient local refinement for denting analysis. A software tool that refines these models and creates a new FE denting model has been created to minimize the amount of pre-processing.
Experimental Testing
Both static and dynamic dent testing was performed using a 5-axis test bed.
Validation of Numerical Results
For static denting both residual dent depth and stiffness response were compared.
For dynamic denting the residual displacement was compared.
Full-Scale Hood Models
The work on the medium scale model was used as a foundation for full-scale models of production automotive hoods.
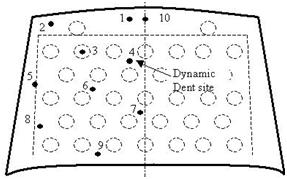
Schematic of dynamic dent sites (Dashed circles represent teacup sites and dashed lines indicate internal supports)
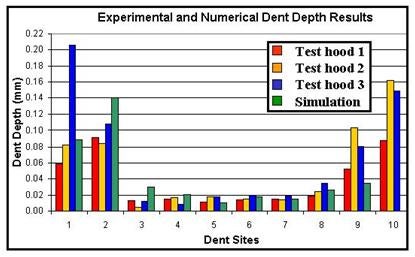
Dynamic Dent Depth Comparisons
Mesh Refinement & Stress/Strain Remapping
The FE models used in industry lack sufficient local refinement for denting analysis. A software tool that refines these models and creates a new FE denting model has been created to minimize the amount of pre-processing work.
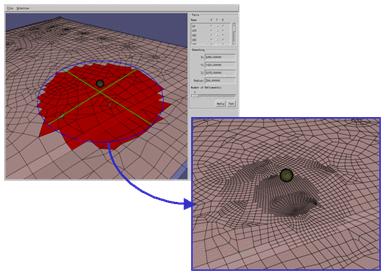
Mesh Refinement Software Interface (200mm refinement radius, 4 levels of refinement)